Material Requirements Planning (MRP) adalah pendekatan logis yang digunakan untuk menentukan jumlah bagian, komponen, dan material yang diperlukan untuk menghasilkan sebuah produk akhir. Dengan MRP, Anda dapat menyusun jadwal waktu yang terperinci kapan setiap komponen, material, dan bagian harus dipesan atau diproduksi. Dengan demikian, MRP membantu memastikan tersedianya semua bahan yang diperlukan untuk produksi.
Sementara itu, Master Production Schedule (MPS) adalah rencana produksi yang mempertimbangkan tenggat waktu untuk produksi sejumlah produk jadi. Dengan menggunakan MPS, Anda dapat menentukan kapan dan berapa banyak harus dipesan untuk setiap komponen produk. Sebagai contoh, perusahaan garmen dapat menggunakan MPS untuk merencanakan kebutuhan kain berdasarkan permintaan baju yang diterima dari pelanggan.
Perbedaan mendasar antara MRP dan MPS membuat keduanya memiliki peran yang berbeda dalam perencanaan produksi. MRP lebih fokus pada perencanaan kebutuhan material, sedangkan MPS lebih fokus pada penjadwalan produksi dan koordinasi operasi manufaktur.
Dalam artikel ini, Anda akan mempelajari lebih lanjut tentang MPS dan MRP, serta bagaimana keduanya saling berhubungan dalam perencanaan produksi.
Daftar Isi:
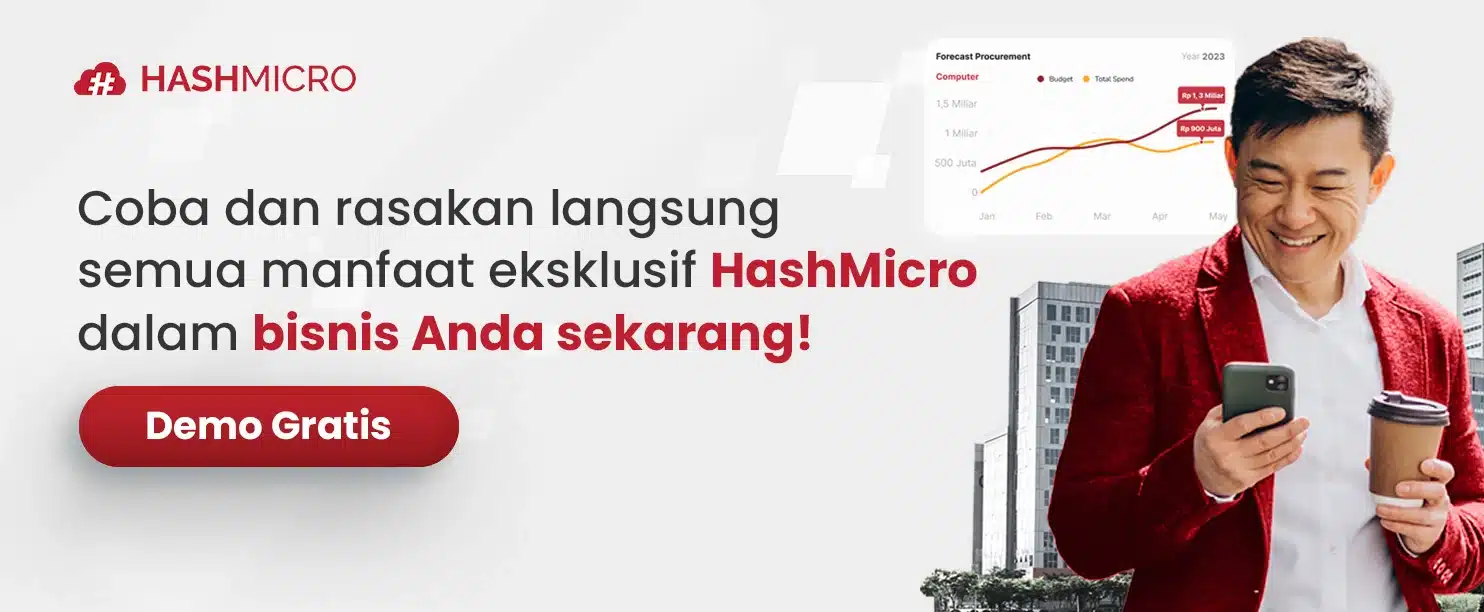
Apa Itu MPS (Master Production Schedule)?
MPS (Master Production Schedule) adalah rencana produksi yang memainkan peran kunci dalam proses manufaktur. Rencana produksi ini menggambarkan hubungan antara jumlah dan waktu penyediaan yang diinginkan untuk setiap jenis produk akhir.
MPS digunakan untuk menentukan jadwal produksi untuk setiap barang yang akan diproduksi. Pada contoh kasus di industri garmen, MPS digunakan untuk membuat jadwal produksi berdasarkan permintaan baju yang muncul dari pelanggan. Dengan menggunakan MPS, perusahaan dapat menentukan kapan dan berapa banyak kain yang diperlukan untuk memenuhi permintaan tersebut.
Implementasi MPS memungkinkan perusahaan mengatur produksi secara efisien, mengoptimalkan penggunaan sumber daya, dan mengurangi risiko overstock atau understock. Dengan memiliki gambaran yang jelas tentang apa yang perlu diproduksi, perusahaan dapat menghindari kelebihan persediaan yang tidak efisien.
Secara keseluruhan, MPS berperan sebagai panduan untuk mengatur jadwal produksi sehingga dapat mengikuti permintaan pasar, menghindari kekurangan persediaan, dan meningkatkan efisiensi produksi.
- Perusahaan otomotif menggunakan MPS untuk mengatur produksi kendaraan dan menyusun jadwal pemasok komponen-komponen mobil.
- Perusahaan elektronik menggunakan MPS untuk mengatur produksi berbagai produk elektronik seperti smartphone, televisi, atau laptop.
- Perusahaan makanan dan minuman menggunakan MPS untuk mengatur produksi makanan dan minuman dalam jumlah yang tepat untuk memenuhi permintaan pasar.
Apa Itu MRP (Material Requirements Planning)?
Material Requirements Planning (MRP) adalah sistem informasi berbasis komputer yang digunakan dalam perencanaan produksi. MRP bertujuan untuk mempermudah penjadwalan produksi induk menjadi tahapan kebutuhan sub-assy, komponen, dan bahan baku yang diperlukan. Dengan menggunakan MRP, Anda dapat mengendalikan tingkat persediaan, menentukan prioritas item, merencanakan kapasitas produksi, dan mengidentifikasi jumlah dan waktu material yang dibutuhkan.
MRP sangat penting dalam operasi manufaktur karena membantu perusahaan untuk mengatur dan mengelola persediaan mereka secara efisien. Dengan memiliki informasi yang tepat tentang kebutuhan material, perusahaan dapat menghindari kekurangan persediaan atau penumpukan yang berlebihan.
Perbedaan utama antara MRP I dan MRP II terletak pada tingkat rincian dan cakupan perencanaannya. MRP I didesain untuk mengelola persediaan dan perencanaan kebutuhan material, sementara MRP II melibatkan perencanaan sumber daya dan keuangan yang lebih komprehensif.
MRP adalah salah satu alat yang sangat penting dalam proses manufaktur. Dengan menggunakan MRP, perusahaan dapat mengoptimalkan produksi mereka, mengurangi biaya persediaan, dan meningkatkan efisiensi operasional. Dengan demikian, MRP mendukung operasi manufaktur dengan menyediakan informasi yang diperlukan untuk mengelola material dan persediaan dengan cara yang paling efisien.
Perencanaan Permintaan dan Hubungannya dengan MRP dan MPS
Perencanaan permintaan adalah aspek penting dalam pengelolaan produksi untuk memastikan ketersediaan material yang diperlukan dan menjadwalkan produksi dengan efisien. Dalam perencanaan tersebut, ada dua jenis permintaan yang perlu diperhatikan: permintaan tergantung dan permintaan independen.
Permintaan tergantung adalah permintaan yang bergantung pada permintaan level yang lebih tinggi. Sebagai contoh, permintaan kain adalah permintaan dependen pada permintaan baju. Dalam hal ini, MRP (Material Requirements Planning) memiliki peran penting dalam perencanaan kebutuhan material. MRP mengidentifikasi jumlah dan waktu material yang dibutuhkan berdasarkan jadwal produksi untuk memastikan persediaan yang mencukupi.
Di sisi lain, permintaan independen adalah permintaan yang tidak bergantung pada permintaan level yang lebih tinggi atau permintaan lainnya. Permintaan independen bisa berasal dari pelanggan, pasar yang bersifat acak, atau promosi penjualan. Dalam hal ini, MPS (Master Production Schedule) berperan dalam menjadwalkan produksi berdasarkan permintaan independen tersebut.
Dalam perencanaan produksi, MRP dan MPS memiliki peran yang berbeda. MRP lebih fokus pada perencanaan kebutuhan material dan pengaturan tingkat persediaan yang efisien. Sedangkan MPS lebih fokus pada jadwal produksi dan mengkoordinasikan operasi manufaktur secara keseluruhan. Keduanya saling terkait dan bekerja sama untuk mencapai efisiensi dan ketersediaan material yang optimal.
Secara keseluruhan, MRP dan MPS memiliki peran yang sangat penting dalam perencanaan produksi. MRP bertanggung jawab untuk mengelola kebutuhan material, sementara MPS merencanakan jadwal produksi untuk memastikan kelancaran operasi manufaktur. Dengan memahami perbedaan antara permintaan tergantung dan independen, serta bagaimana MRP dan MPS mengatasi aspek-aspek ini secara berbeda, perusahaan dapat mengoptimalkan perencanaan produksi mereka dan mencapai tingkat efisiensi yang lebih baik.
Contoh Penerapan MRP dan MPS dalam Industri
Terdapat banyak contoh penerapan MRP dan MPS dalam industri. Misalnya, perusahaan manufaktur ABC menggunakan MRP untuk mengendalikan tingkat persediaan dan menentukan jumlah komponen dan bahan baku yang dibutuhkan. Dengan menggunakan MRP, perusahaan dapat mengoptimalkan pengaturan persediaan dan menghindari kekurangan atau kelebihan material yang berpotensi merugikan efisiensi produksi.
Sementara itu, perusahaan manufaktur XYZ menggunakan MPS untuk merencanakan jadwal produksi produk akhir. Dengan MPS, perusahaan dapat mengatur urutan produksi dengan efisien sehingga dapat memastikan produk akhir disediakan tepat waktu sesuai dengan permintaan pelanggan. Hal ini membantu perusahaan menghindari keterlambatan pengiriman dan meningkatkan kepuasan pelanggan.
Analisis kasus dan pengalaman nyata menunjukkan bahwa kedua sistem, MRP dan MPS, secara signifikan berkontribusi terhadap efisiensi produksi. MRP membantu mengoptimalkan pengelolaan persediaan dan memastikan ketersediaan material yang diperlukan, sedangkan MPS membantu merencanakan jadwal produksi dengan tepat. Dengan menerapkan kedua sistem ini, perusahaan dapat meningkatkan produktivitas dan keuntungan mereka.
Kesimpulan
Dalam memilih strategi yang tepat, pengusaha dan manajer produksi disarankan untuk mempertimbangkan kebutuhan operasional mereka. Jika perusahaan memiliki tantangan dalam mengatur persediaan material, MRP dapat menjadi pilihan yang baik. Di sisi lain, jika perusahaan berfokus pada jadwal produksi dan pengiriman tepat waktu, MPS dapat menjadi pilihan yang lebih tepat.
Namun, pengelolaan persediaan material dan pengaturan jadwal produksi dapat semakin efektif dengan software ERP. HashMicro merupakan software ERP yang mampu mengintegrasikan fungsi MRS dan MPS di satu dasbor. Dengan begitu, Anda dapat meningkatkan efisiensi perencanaan produksi, mengurangi biaya operasional, dan mampu memenuhi kebutuhan konsumen tepat waktu.
Coba demo gratis sekarang dan rasakan manfaatnya!
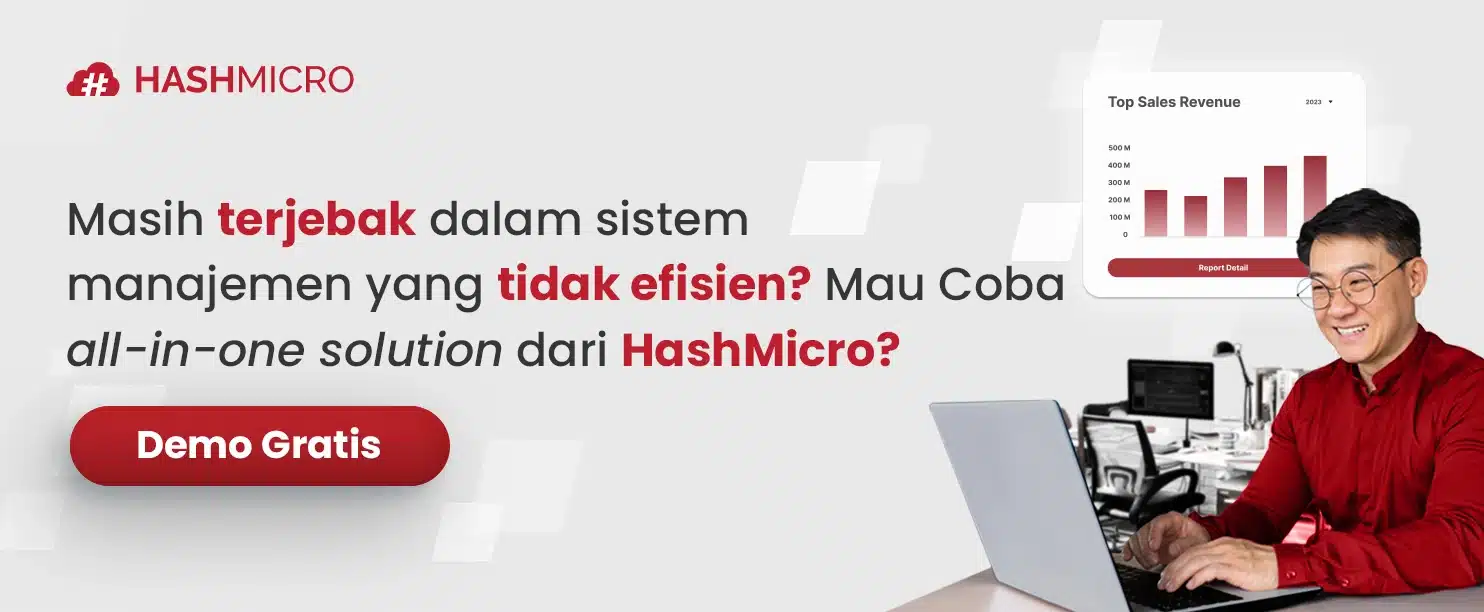