Malaysia’s manufacturing output rose 3.7% this January, but growth means nothing if your BOMs can’t keep up. As more orders come in and production lines get busier, even a small oversight in your bill of materials (BOM) can lead to costly delays or stock shortages.
Your BOM is more than just a checklist. It’s the foundation of your entire production process. From sourcing materials to scheduling assembly, a well-structured BOM keeps everything aligned and moving efficiently.
But as operations grow more complex, relying on manual updates or spreadsheets just doesn’t cut it anymore.
In this article, we’ll break down what a BOM really is, why it’s critical to your manufacturing success, and how modern solutions, like HashMicro’s Manufacturing Software, can make managing it faster, easier, and far more accurate.
Key Takeaways
|
Table of Content
Content Lists
What is the Bill of Materials?
A bill of materials (BOM) is a structured list of all the materials, subassemblies, components, and parts, along with their respective quantities, required to manufacture a product. It’s also referred to as a production recipe, assembly list, or component list.
Beyond listing parts and quantities, a BOM typically includes specifications and quality standards for each item. This level of detail helps ensure that the final product meets desired performance and quality benchmarks.
BOMs are widely used across industries such as manufacturing, construction, engineering, and even software development. No matter the sector, creating a BOM is often the first step in initiating a reliable and efficient production process.
Benefits of Bill of Materials
A bill of materials (BOM) helps improve production accuracy and keeps the manufacturing process running smoothly by serving as a clear, step-by-step guide.
With a well-organized BOM, companies can:
- Plan and buy materials on time while keeping track of what’s running low.
- Stay on top of costs, monitor inventory, and deal with delays or urgent needs quickly.
- Manage timelines and budgets without losing control of the production flow.
- Keep proper records, cut down on waste, and quickly swap out parts that aren’t working.
- Spot weaknesses in the supply chain—especially in digital systems—to keep operations safer.
By covering all these bases, the BOM helps teams run a more reliable, cost-efficient, and secure production process.
Types of Bill of Materials
There are three main types of bill of materials:
- Manufacturing BOM (MBOM): Lists all parts, subassemblies, and materials needed to manufacture and ship a finished product. It includes components that require processing before assembly and shows how parts relate to one another.
- Engineering BOM (EBOM): Outlines the product’s design from the engineering team’s perspective. Usually created using CAD or electronic design tools, the EBOM includes technical drawings and functional layouts. Multiple versions may exist as the product goes through revisions.
- Sales BOM (SBOM): Describes a product and its components before assembly, mainly for sales purposes. Both the finished item and its individual parts are listed separately in the sales order. The product is treated as a sales item rather than inventory.
Types of BOM Displays
Explosion and implosion are two common ways to present the structure of a bill of materials (BOM):
- Explosion starts from the finished product and breaks it down into its individual components. It follows a top-down format, beginning with the end result and then detailing how each part fits into the overall assembly. The deeper you go, the more detailed the breakdown becomes.
- Implosion takes the opposite approach. It begins by outlining the main components and how they come together, gradually building up to show the final product at the end.
Why Excel Isn’t Built for Bill of Materials Management
Using a spreadsheet might feel like the obvious way to manage your bill of materials (BOM). But once your product or operations grow, Excel starts showing its limits. Here’s why relying on it can slow you down:
- Prone to Errors: Manual updates, copy-paste slips, and complicated formulas can easily lead to costly mistakes. One wrong value can affect your entire production—and you may not catch it until it’s too late.
- Struggles with Product Variants: Managing multiple product versions in Excel is a headache. Each variant often needs its own BOM, which quickly turns your spreadsheet into a cluttered mess that’s hard to update and harder to trust.
- Complicated Cost and Quantity Tracking: Simple calculations are fine. But when you start dealing with multi-level BOMs, tracking costs and quantities across several layers becomes a nightmare. One missed formula, and your margins could take a hit.
- Multi-Level BOMs Are a Pain: Indenting, sorting, updating shared parts; Excel can do it, but not well. Move one item the wrong way and your entire hierarchy can break. If a single part appears in five places, updating it once doesn’t mean it updates everywhere.
So, what’s the bottom line? Spreadsheets weren’t designed for the complexity of modern manufacturing. With a dedicated BOM system, your team spends less time fixing errors and more time getting products out the door.
Clearly, since Excel has its limits, you need to explore for a better option. A modern manufacturing software system is one of them, because it can simplify BOMs and so much more. Explore how it can work for your team; try the no-cost demo below.
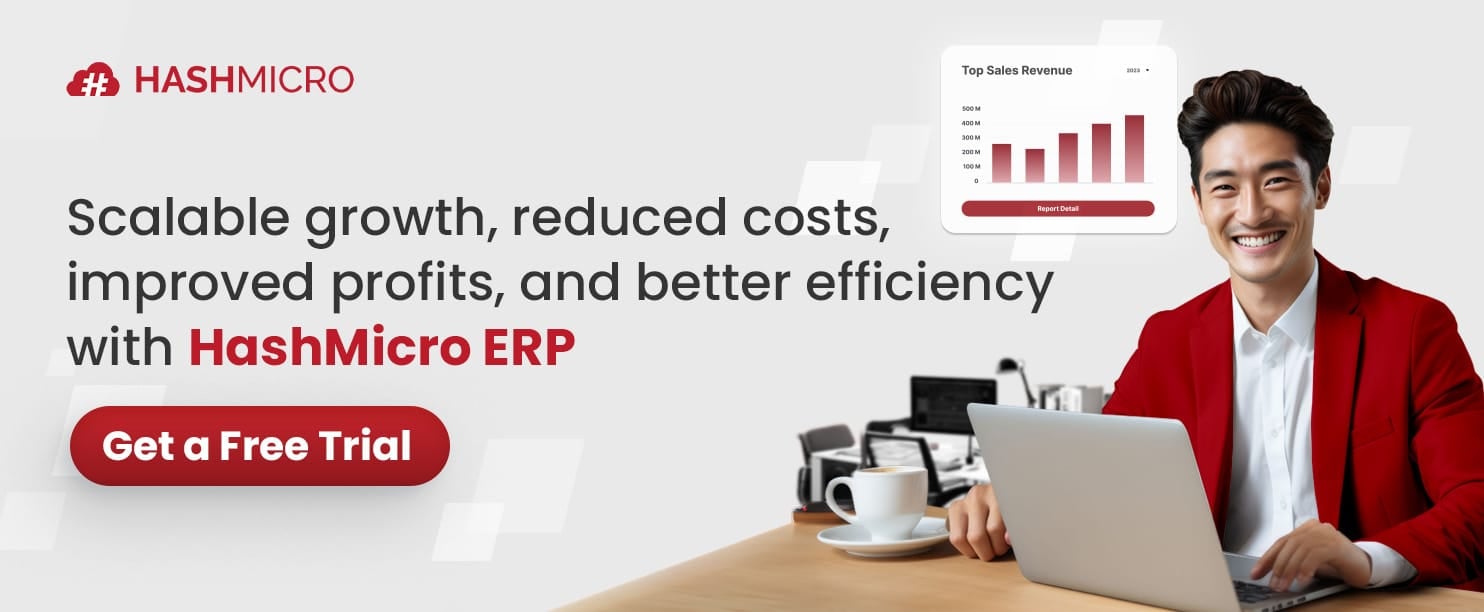
Structures of Bill of Materials
A bill of materials (BOM) is usually arranged in a hierarchy, starting with the finished product at the top. It includes details like product codes, part descriptions, quantities, costs, and specifications. The two most common formats are single-level and multilevel BOMs.
1. Single-Level BOM
This is the simplest format, listing all assemblies or components needed to build a product, along with their required quantities. It’s easy to create and manage but lacks depth—it doesn’t show how components relate to subassemblies.
So, if something breaks, it’s hard to trace the issue back to a specific part.
2. Multilevel BOM
More complex but far more detailed, a multilevel BOM maps out every component, subassembly, and their relationships. It provides a complete view of how a product is built—from top-level assemblies down to the smallest part—making it ideal for managing complex products and production workflows.
How to Create a Bill of Materials
A bill of materials isn’t just a list. It’s a critical document that helps your team manage production, procurement, and costing with accuracy. Whether you’re producing in Penang, Johor, or Klang Valley, here’s how to create a BOM that works for your operations:
1. Part Name & Part Number
Give each material, ingredient, or component a clear and unique name. Assigning a part number (nombor komponen) or SKU makes tracking and reordering easier.
You can use:
- Intelligent part numbers like PCB-MY101-V1, where PCB stands for Printed Circuit Board, MY refers to Malaysia, 101 is the model number, and V1 is the version.
- Or nonintelligent numbers, such as 000984756234, which serve only as unique identifiers.
2. Part Phase
This indicates where a part is in its lifecycle—design phase, released, or under revision. Tracking part status helps ensure that only approved components are used during production.
3. Levels & Structure
BOMs are often multi-layered. Each level (tahap) shows where a component sits in the assembly structure. Clear levels help teams understand how everything fits together and support better planning.
4. Procurement Type
Define how each item is sourced using standard codes:
- P for purchased parts (dibeli)
- M for modified parts (ubah suai)
- C for custom-made parts (ditempah khas)
5. Quantity & Units of Measure
List the quantity of each material needed and the unit of measurement (unit ukuran)—such as pieces, litres, meters, or kilograms. This avoids miscommunication between departments or with suppliers.
6. Product Colour
If your product comes in different colours, include this detail in the BOM. It prevents mistakes during assembly and ensures the right variant reaches your customer.
7. Description & Notes
Provide a short, clear description for each item. You can also add notes for technical details, handling instructions, or anything the production team should be aware of.
8. Stock Cost (Kos Stok)
Record the cost per unit based on the required quantity. This helps track material expenses in Ringgit (MYR) and gives your finance team accurate data for budgeting and pricing.
Want to skip the manual work and reduce costly errors? A smart manufacturing system can automate BOM creation, manage multi-level assemblies, and keep all your data updated in real-time.
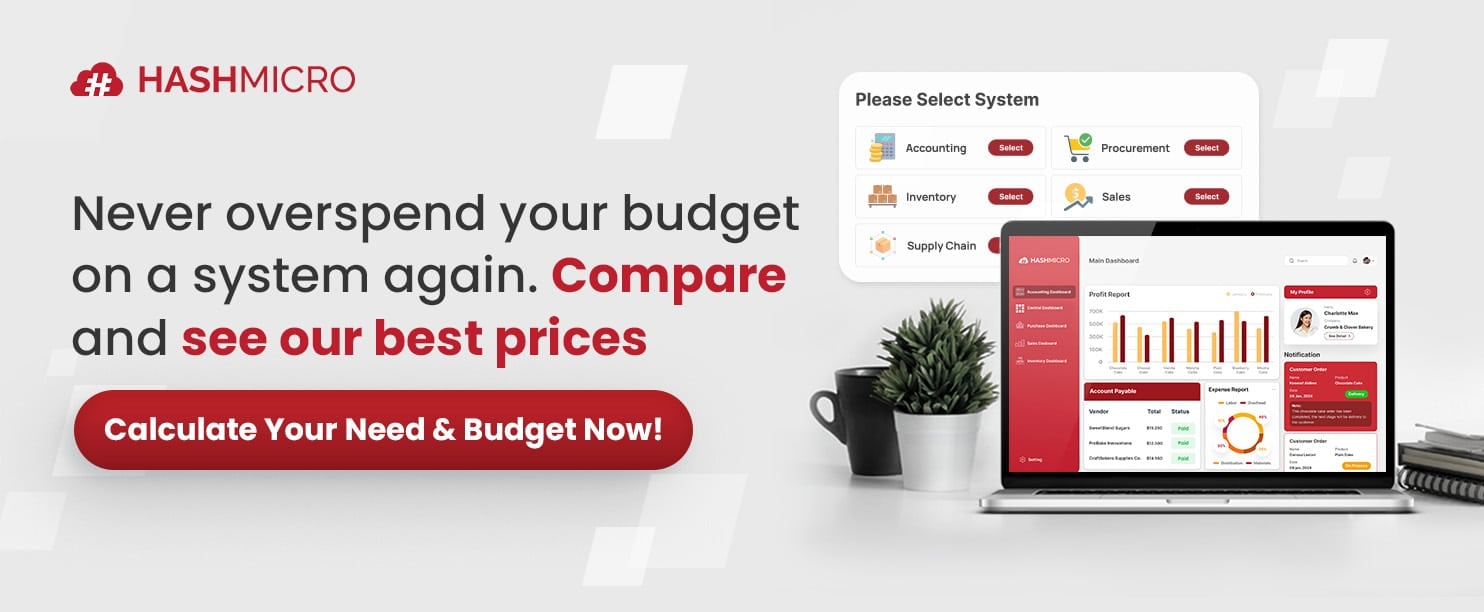
How to Manage Bill of Materials More Efficiently
A bill of materials (BOM) isn’t a one-and-done document—it evolves as your product does. To keep it effective and relevant, here are some smart practices you can follow:
- Keep It Up to Date: Design tweaks, material changes, or cost shifts? Update your BOM regularly to reflect what’s happening on the ground. Staying current helps avoid errors and keeps production running smoothly.
- Automate When You Can: Manually managing BOMs gets tricky fast—especially in fast-moving environments. Using manufacturing software or an ERP system helps you track changes in real time and keeps everything in sync automatically.
- Organize It Clearly: Structure your BOM with a clear hierarchy. When everyone can see how parts connect—from main assemblies to the tiniest screws—it’s easier to plan, build, and troubleshoot.
- Use the Right Units: Avoid confusion by clearly stating units of measurement for every item—like pieces, meters, or kilograms. When everyone speaks the same “language,” planning becomes easier and errors drop.
- Add the Details That Matter: Include specs, instructions, and quality standards right in the BOM. The more context you give, the easier it is for teams to make informed decisions and avoid missteps.
- Include Supplier Info: Listing out suppliers for each part speeds up sourcing and gives your procurement team a head start when parts run low or changes are needed.
- Control Who Edits What: To avoid messy mistakes, define who can make changes to the BOM—and keep a record of all updates. With proper access control, you protect data accuracy and keep everything on track.
Speed Up Production with Automated BOM Tracking from HashMicro
Managing a complex production process comes with its fair share of challenges, especially when you’re dealing with multi-level BOMs, fluctuating stock levels, and supplier coordination. Manual tracking just isn’t enough anymore.
If you’re a manufacturer facing these issues, automating your BOM management can be a game-changer. That’s where HashMicro’s Manufacturing Software steps in.
With full support for both single-level and multilevel BOMs, the system adapts to whatever you’re producing—whether it’s a simple product or one that involves several layers of assemblies and subcomponents.
And because it connects directly with your inventory and accounting modules, you can generate accurate COGM reports without switching platforms.
Here’s how HashMicro helps simplify your entire production flow:
- Secret Recipe / BOM: Build and secure detailed formulas or product recipes, with access control to keep sensitive data protected.
- Manufacturing Requisition Planning: Know exactly what materials you need before you need them, so production never gets held up.
- Finished Goods Production Simulation: Forecast your output based on current stock and BOM data. Get alerted if anything’s missing.
- Production Scheduling: Turn BOM details into clear, efficient production plans to meet demand without wasting resources.
- Quality Control: Ensure only approved, high-quality materials are used, keeping your final product consistent and BOM records reliable.
In short, HashMicro turns BOM management from a manual burden into a fully integrated, effortless part of your workflow.
Conclusion
A bill of materials is a structured guide that lists everything needed to assemble a product efficiently. It helps manufacturers improve accuracy, control costs, and maintain a smooth, well-organized production process.
If you’re tired of manual updates and spreadsheet errors, it’s time to switch to smarter BOM management. HashMicro’s Manufacturing Software handles everything from cost tracking to production planning: fast, accurate, and fully connected.
With HashMicro, you get more than a tool. Instead, you get peace of mind in every production run. Book your free demo today and experience a simpler, smarter way to manage your manufacturing operations!
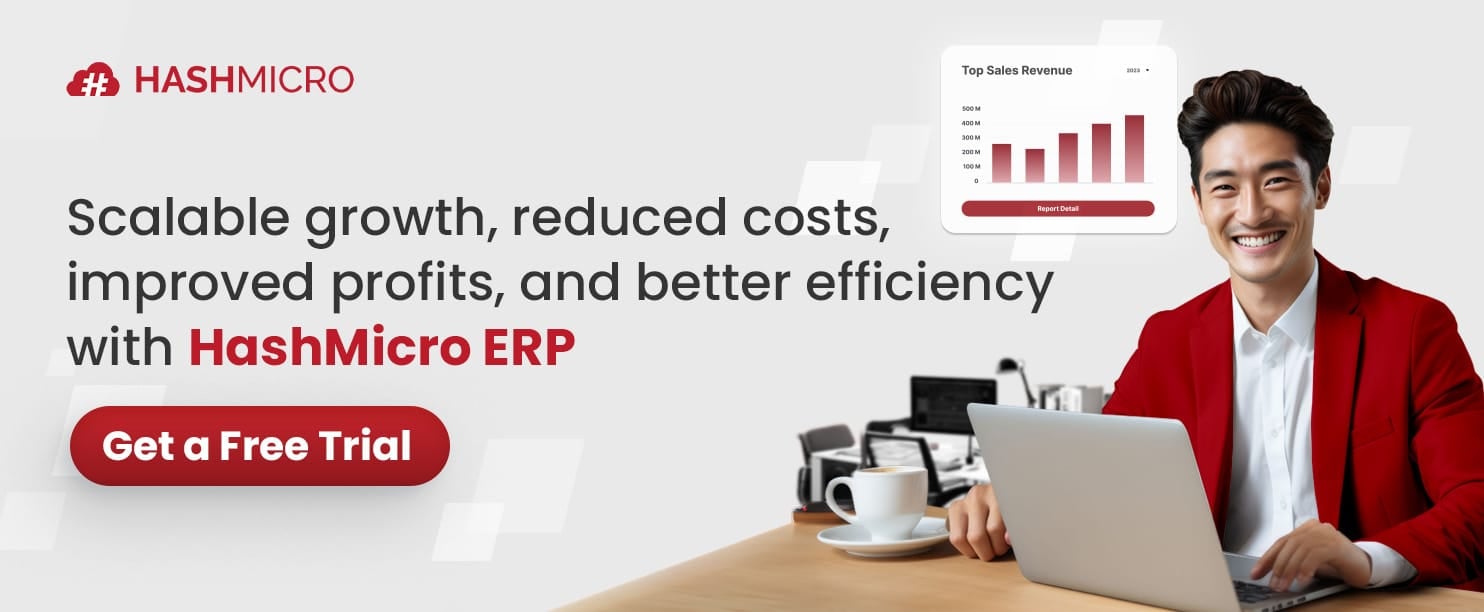
FAQ on Bill of Materials
-
What is the difference between a BOM and routing in manufacturing?
A BOM specifies the materials and components required to produce a product, essentially detailing “what” is needed. In contrast, routing outlines the sequence of operations or steps involved in the manufacturing process, describing “how” the product is made.
-
How does a BOM affect inventory management?
An accurate BOM is crucial for effective inventory management as it helps in demand forecasting, procurement planning, and resource allocation. It ensures that the right components are available at the right time, minimizing excess inventory and reducing the risk of stockouts.
-
How should BOM changes be handled during production?
Managing BOM changes during production requires a structured approach, including a clear revision policy, version control, and communication with all stakeholders. Utilizing BOM management software can facilitate tracking changes, ensuring that updates are implemented smoothly without disrupting the production process.
-
What is a phantom BOM?
A phantom BOM represents a subassembly that is used in the manufacturing process but is not stocked as a separate item. It simplifies the production process by allowing the components of the phantom assembly to be picked and assembled as part of the parent item, without creating a separate production order for the subassembly.