Managing construction equipment goes beyond simply owning the right tools and machines. From heavy construction equipment to everyday construction tools and equipment, success in the construction industry depends on how well these assets are maintained, tracked, and utilized.
With the global construction equipment market valued at over USD 207 billion in 2023 and projected to grow at a CAGR of 8.4% until 2030, this sector is expanding rapidly. For contractors and project managers, the challenge is no longer just about acquiring equipment—it’s about managing it effectively to avoid downtime, control expenses, and ensure project safety.
In this article, we’ll explore proven strategies for managing everything from site equipment to heavy-duty equipment and how modern tools like construction management software and construction estimating solutions are changing the game for businesses looking to stay competitive.
Key Takeaways
|
Table of Content
Content Lists
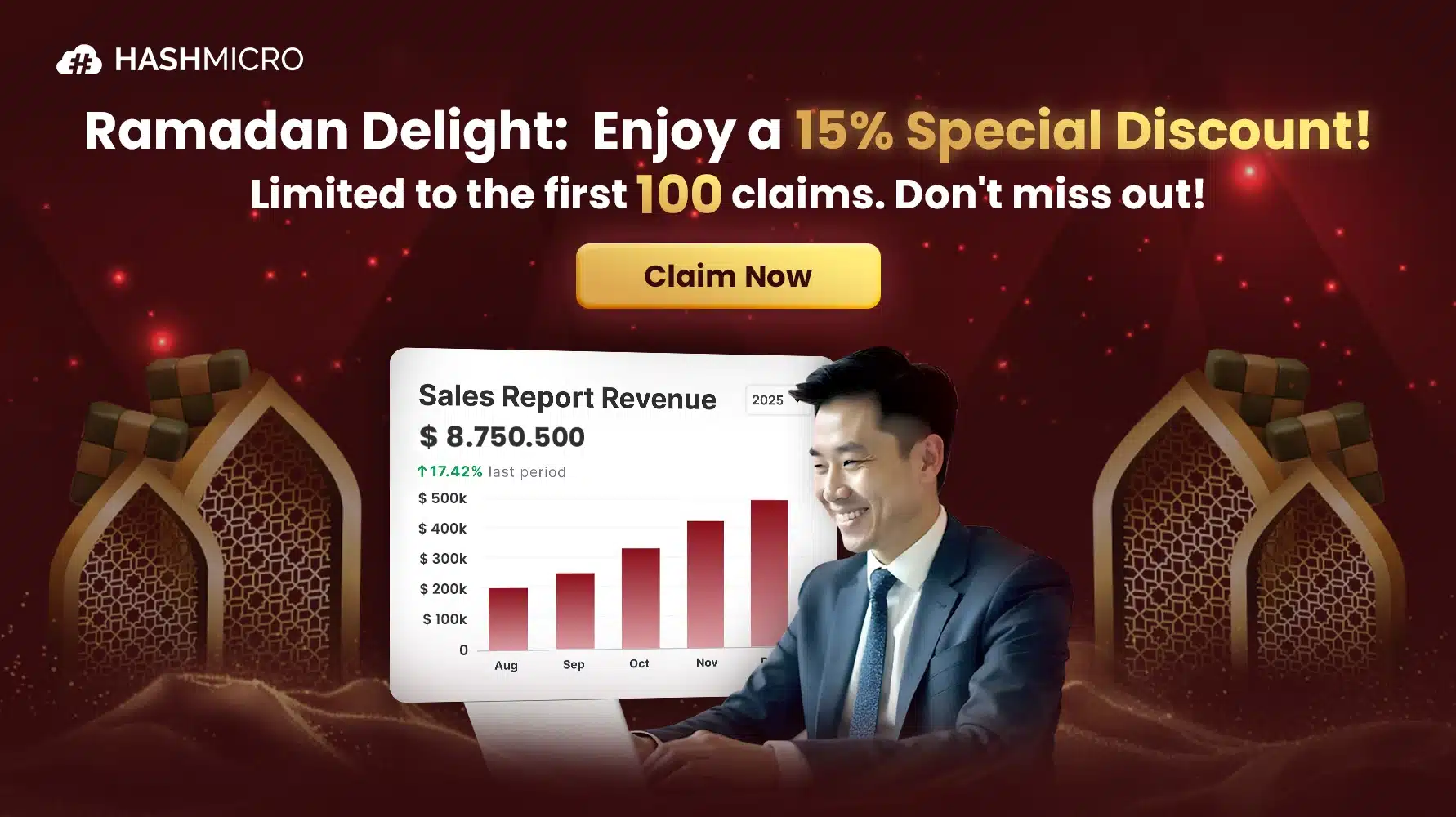
Why Good Construction Equipment Management Matters
In construction, delays, cost overruns, and safety risks often stem from poor equipment management. Whether you’re dealing with heavy construction equipment or smaller site equipment, ensuring everything is in top condition and properly allocated can make or break a project.
Effective management of construction tools and equipment extends the life of your assets, minimizes unplanned downtime, and improves safety for workers. It also supports better budget planning and construction estimating, giving project managers a clear view of operational costs.
With the help of tools like construction management software, companies gain full visibility over their equipment, from real-time usage data to maintenance records—enabling smoother, safer, and more profitable projects.
8 Tips to Manage Construction Equipment Effectively
Whether it’s heavy-duty equipment or everyday construction tools, managing assets properly ensures projects stay on time and within budget. These tips will help you streamline operations, reduce equipment-related risks, and get the most value from your investment.
1. Use a Centralized Equipment Management System
A centralized platform, like construction management software, helps keep track of your entire fleet. It allows teams to update data in real time and ensures everyone has access to the latest information on location, condition, and usage.
Key benefits:
- Real-time tracking of all equipment
- Accurate inventory and maintenance records
- Integration with construction estimating and project planning tools
2. Centralize Equipment Requests and Cost Allocation
Managing multiple projects means juggling equipment across various sites. Centralizing requests and usage logs prevents double-booking and ensures optimal allocation based on priority and availability.
Why it matters:
- Improves scheduling accuracy and project coordination
- Helps control equipment-related expenses
- Enhances visibility into costs across different job sites
3. Set Clear Usage Protocols and Provide Operator Training
Improper handling of construction equipment not only leads to faster wear and tear but also increases the risk of accidents. Establishing clear protocols and training ensures your team uses construction safety equipment and machinery responsibly.
What to do:
- Define safe usage guidelines for each type of construction tool or equipment
- Limit access to trained personnel only
- Assign responsibility to operators to improve accountability
4. Schedule Regular Inspections and Preventive Maintenance
Routine checks and scheduled maintenance are key to avoiding unexpected breakdowns. With an asset tracking system or construction management software, you can log inspections and automate service schedules for better control.
Benefits include:
- Early detection of wear, damage, or misuse
- Longer lifespan for heavy-duty equipment
- Better planning and fewer project interruptions
5. Optimize Equipment Utilization and Track ROI
Don’t let valuable construction equipment sit idle. By monitoring usage and calculating return on investment (ROI), you can determine which assets are driving value and which ones are draining your budget.
How to do it:
- Match site equipment to project needs to avoid overstocking or underuse
- Use data to inform purchasing or rental decisions
- Track which assets contribute most to productivity and cost-efficiency
6. Leverage Telematics and IoT for Real-Time Monitoring
Smart construction management software can integrate with IoT sensors to provide real-time insights into equipment performance, usage patterns, and even location.
Advantages:
- Track heavy construction equipment in real time across job sites
- Predict maintenance needs before issues escalate
- Reduce downtime with data-backed decisions
7. Foster Strong Communication and Collaboration
Clear communication between field teams and office staff helps avoid misunderstandings about equipment status, availability, or repairs. Use digital tools to streamline updates and keep everyone aligned.
Best practices:
- Implement mobile apps for real-time reporting and updates
- Use shared dashboards for transparency on equipment status
- Encourage collaborative issue tracking and resolution
8. Conduct Regular Audits and Performance Assessments
Routine audits help evaluate how well your construction tools and equipment are being used and maintained. These reviews also ensure compliance with safety standards and support cost control.
Audit essentials:
- Inspect equipment condition and usage logs
- Review compliance with construction safety equipment regulations
- Identify inefficiencies and adjust strategies as needed
How to Choose the Right Construction Equipment
Choosing the right construction equipment is just as important as managing it. Each project comes with its own set of challenges, and selecting the right tools ensures that work gets done safely, efficiently, and within budget. Here’s how to make the right choice:
- Assess Project Needs: Start by identifying the scope and scale of your project. Will you need heavy construction equipment or smaller site equipment? Referencing past project data can help you decide.
- Evaluate Job Site Conditions: Terrain, space, and weather can all affect which construction tools and equipment are suitable. Some sites may require compact machines, while others demand high-powered machinery.
- Set a Realistic Budget: Keep your financial plan aligned with your equipment needs. This step is crucial in accurate construction estimating, helping you avoid overspending while still getting the job done.
- Choose Reliable Suppliers: Source from vendors who can deliver on time and offer support when needed. Consider local availability and after-sales services.
- Review Warranties and Contracts: Before finalizing, check warranty terms and equipment agreements to ensure long-term value and protection.
- Smart equipment selection upfront can save time, reduce risks, and improve your bottom line throughout the project lifecycle.
When to Retire and Replace Construction Equipment
Even the best-maintained construction equipment has a limit. Knowing when to repair, retire, or replace a machine is essential to keep operations smooth and costs under control. Key factors to consider:
- Age and Usage: Compare actual usage against the manufacturer-recommended lifespan. Heavy-use equipment may wear out faster than expected.
- Rising Repair Costs: If maintenance is frequent and expensive, it may cost more to fix than to invest in new, more efficient equipment.
- Technology Advancements: Older tools may still work but lack the precision or automation features of newer construction tools and equipment. Upgrading can improve productivity.
- Shifting Project Needs: As project scopes change, some site equipment may no longer be relevant. It’s better to phase out unused tools to free up resources.
- Compliance and Safety: Outdated machines may not meet modern construction safety equipment standards, putting your team and business at risk.
Evaluating these signs regularly ensures your fleet stays efficient, safe, and aligned with your project goals.
Manage Construction Effectively with Construction Equipment Management Software
Managing multiple pieces of construction equipment across various sites can get overwhelming fast. With the right construction management software, you can track everything in one place—reducing delays, avoiding hidden costs, and keeping your operations on schedule.
HashMicro’s Construction Management Software simplifies equipment oversight with these key features:
- Preventive Maintenance Scheduling: Automatically schedule and track maintenance to extend the lifespan of your heavy-duty equipment and avoid unexpected breakdowns.
- Asset GPS Tracking: Know the real-time location of all your tools and machinery—especially useful for large sites or mobile teams.
- Comprehensive Cost Reporting: Monitor maintenance and operational expenses for smarter construction estimating and budget planning.
- Maintenance Budget Tracking: Keep repair costs in check by allocating and monitoring budgets for each asset.
- QR Code Scanning for Requests: Staff can easily report equipment issues using QR codes, enabling quick responses and reducing downtime.
By using HashMicro’s software, you gain full control over your construction tools and equipment, helping you operate more efficiently and make smarter decisions across your projects.
Conclusion
Proper construction equipment management is more than just maintenance—it’s about maximizing productivity, cutting unnecessary costs, and keeping your projects on track. From selecting the right tools to using data for smarter decisions, the right strategies can transform how your business operates.
With tools like HashMicro’s Construction Management Software, you can streamline equipment tracking, automate maintenance, and gain full visibility over your assets. It’s a smarter, more efficient way to manage everything from site equipment to heavy-duty machinery so your team can focus on what matters most: building success.
Try a free demo today and see how HashMicro can help you manage your construction operations with confidence.
FAQ about Construction Equipment
-
What are equipments in construction??
Construction equipment refers to machines and tools used to build, repair, or maintain structures—ranging from excavators and cranes to drills and safety gear.
-
What is the most common construction equipment??
Excavators are among the most common, used for digging, lifting, and demolition on nearly all job sites.
-
What is DEF in construction equipment??
DEF (Diesel Exhaust Fluid) is a liquid used in diesel-powered equipment to reduce harmful emissions and meet environmental regulations.
-
What machinery is needed for construction??
Essential machinery includes excavators, bulldozers, loaders, cranes, and concrete mixers—depending on the project’s scope.