Procurement is a crucial aspect of construction, accounting for 40 to 70 percent of a company’s total spending. Efficient procurement ensures smooth project execution, cost control, and quality assurance. However, many construction projects face delays, budget overruns, and supply chain disruptions, with 70% of Malaysian projects failing to meet time, cost, and quality goals. The role of procurement in construction is pivotal in managing these challenges effectively.
A well-structured construction procurement process helps businesses manage resources effectively, minimize risks, and maintain project timelines. By adopting the right procurement strategies, companies can enhance coordination, reduce inefficiencies, and improve overall project performance, overcoming the challenges in construction procurement.
What is Construction Procurement?
Construction procurement refers to the process of acquiring materials, equipment, and services essential for completing a construction project. This involves planning, supplier selection, contract negotiation, purchasing, and logistics management to ensure that all project requirements are met efficiently. To define procurement, it is the process of sourcing goods and services needed for business operations, often involving strategic planning and vendor management.
The process typically begins with identifying project needs and creating a procurement plan that outlines budgets, timelines, and specifications. Traditional procurement methods, such as bidding or direct negotiation, are used to assess vendors and secure the best quality and pricing while ensuring compliance with industry standards. Once agreements are finalized, contracts are managed to ensure all deliverables are provided as specified.
Effective procurement management helps control costs, coordinate resources, and mitigate risks, ensuring projects stay on schedule and within budget. Companies that optimize their procurement strategies can enhance supply chain efficiency and prevent costly delays.
Key Takeaways
|
Table of Content
Content Lists
Advantages of an Effective Construction Procurement Process
A well-executed construction procurement process offers numerous benefits that directly impact project efficiency, cost management, and quality assurance. By streamlining procurement operations, construction companies can minimize risks and improve overall project outcomes.
1. Cost Control and Budget Management:
An efficient procurement strategy ensures businesses acquire materials and services at competitive prices through bidding and negotiations. This approach helps prevent cost overruns, optimize spending, and maximize project profitability.
2. Timely Project Completion:
Delays in procurement can lead to disruptions in construction schedules. A structured procurement process ensures that materials, services, and contractors are available when needed, keeping projects on track and minimizing downtime.
3. Quality Assurance:
By selecting reliable vendors and contractors, businesses can maintain high-quality construction standards. Strict procurement guidelines help prevent defects, reduce rework, and meet client and regulatory expectations.
4. Improved Communication and Coordination:
A clear procurement workflow ensures seamless coordination between project managers, suppliers, and contractors. Effective communication minimizes misunderstandings, leading to smoother execution and fewer project disruptions.
Who Oversees Procurement in Construction Supply Chain Management?
In construction, procurement managers play a key role in overseeing the acquisition of materials, equipment, and services. Their responsibilities include strategic planning, supplier selection, contract negotiations, and ensuring timely deliveries to keep projects on schedule and within budget.
The role of a procurement manager varies depending on company size and project scope, but generally includes:
1. Developing a Strategic Procurement Plan:
Procurement managers create detailed procurement plans that outline budget allocations, supplier selection strategies, and contingency measures. By anticipating potential risks such as supply chain disruptions, they ensure projects remain on track.
2. Reviewing Contracts, RFPs, and Bidding Processes:
Handling requests for proposals (RFPs), bidding processes, and supplier evaluations is a crucial task. Procurement managers assess vendor capabilities, negotiate pricing, and ensure contracts align with project specifications and compliance requirements.
3. Overseeing Resources and Timelines:
Procurement managers work closely with project teams to schedule material deliveries and workforce allocation. By leveraging digital procurement tools, they can monitor real-time progress, identify bottlenecks, and make adjustments to avoid delays.
Continuous tracking and monitoring of procurement activities allow managers to optimize costs, mitigate risks, and ensure seamless execution throughout the project lifecycle.
Types of Procurement Methods in Construction
Selecting the right procurement method is essential for ensuring project efficiency, cost-effectiveness, and quality control. Different methods offer distinct advantages based on project complexity, budget constraints, and timelines.
1. Single-Source Procurement:
This method involves sourcing materials, equipment, or services from one trusted supplier without considering alternatives. It helps maintain consistent quality and reliable delivery, but over-reliance on a single vendor can pose risks if supply disruptions occur.
2. Multiple-Source Procurement:
Companies often rely on multiple suppliers to reduce risks such as shortages, delays, or price fluctuations. By doing so, they increase flexibility and enhance supply chain resilience. However, this approach requires effective coordination to ensure quality consistency across all suppliers.
3. Two-Stage Tendering:
This method allows early collaboration between clients and contractors. The first stage involves preliminary bidding, where contractors submit initial proposals. The second stage refines project details before finalizing contracts. This approach reduces risks and improves project planning.
4. Selective Tendering:
In selective tendering, only pre-qualified contractors are invited to submit bids. This ensures that bidders meet financial, technical, and quality standards, reducing risks associated with hiring inexperienced vendors.
5. Open Tendering:
A widely used method where any contractor or supplier can bid for a project. Open tendering promotes transparency and competition, making it ideal for public sector projects. However, evaluating multiple bids can be time-consuming.
6. Negotiated Contracting:
Clients directly negotiate contracts with a preferred contractor. This method fosters faster decision-making and strong collaboration but requires high levels of trust and transparency to ensure fairness.
Choosing the right procurement method depends on project requirements, budget constraints, and risk tolerance, ensuring the most efficient approach for successful project execution.
9 Essential Steps for Managing Building Materials Procurement
A well-structured construction procurement process ensures projects run efficiently, stay within budget and meet quality standards. Below are nine essential steps to guide procurement managers in optimizing their workflow.
1. Develop Detailed Specifications:
The design team prepares comprehensive project specifications, including material types, quality standards, and regulatory compliance. These details act as a blueprint for suppliers and contractors, reducing errors and miscommunication.
2. Prepare Estimates and Submit Bids:
Contractors analyze the project scope and submit detailed cost estimates covering materials, labor, and equipment. Using construction accounting software can streamline budgeting and improve cost tracking.
3. Finalize Agreement Terms:
Both parties establish clear contractual terms, payment schedules, and responsibilities to prevent disputes. Additionally, compliance checks ensure the contract aligns with legal and regulatory requirements.
4. Solicit Bids from Suppliers:
Procurement managers request pricing and proposals from suppliers and subcontractors. Factors such as cost, reliability, and delivery timelines are evaluated before finalizing supplier agreements.
5. Organize the Procurement Schedule:
A procurement schedule outlines when materials and services are needed, ensuring that deliveries align with the project timeline. As a result, supply chain bottlenecks and delays can be minimized.
6. Review Contractor Submittals:
Contractors submit material samples, specifications, and plans for approval. The design team verifies compliance with project standards before granting final approval.
7. Complete Purchases with Suppliers:
Once approvals are secured, procurement managers confirm purchase orders and delivery timelines with suppliers, ensuring the availability of required materials.
8. Manage Material Delivery to the Site
Timely deliveries are crucial for maintaining construction progress. Procurement teams monitor logistics and inventory tracking to ensure materials arrive on time and meet quality standards.
9. Conduct Final Inspections:
Before project handover, a quality inspection ensures that materials and construction meet contractual requirements. Any defects or discrepancies are addressed before final approval.
Conclusion
An effective building project procurement strategy is essential for ensuring projects are completed on time, within budget, and to the highest quality standards. By following a structured procurement process—from cost estimation and supplier selection to contract management and final inspections—businesses can minimize risks, improve coordination, and enhance operational efficiency. Implementing a Procurement Management System streamlines this process, automating key tasks, improving vendor management, and providing real-time insights to ensure timely project completion and cost control.
To further streamline procurement operations, adopting construction procurement software can automate critical processes, optimize vendor management, and provide real-time insights into procurement activities. HashMicro’s Procurement Software offers a comprehensive solution designed specifically for the construction industry, helping businesses gain better control over purchasing, budgeting, and supplier performance.
Explore how HashMicro can transform your procurement process—request a free demo today and experience a smarter way to manage construction procurement.
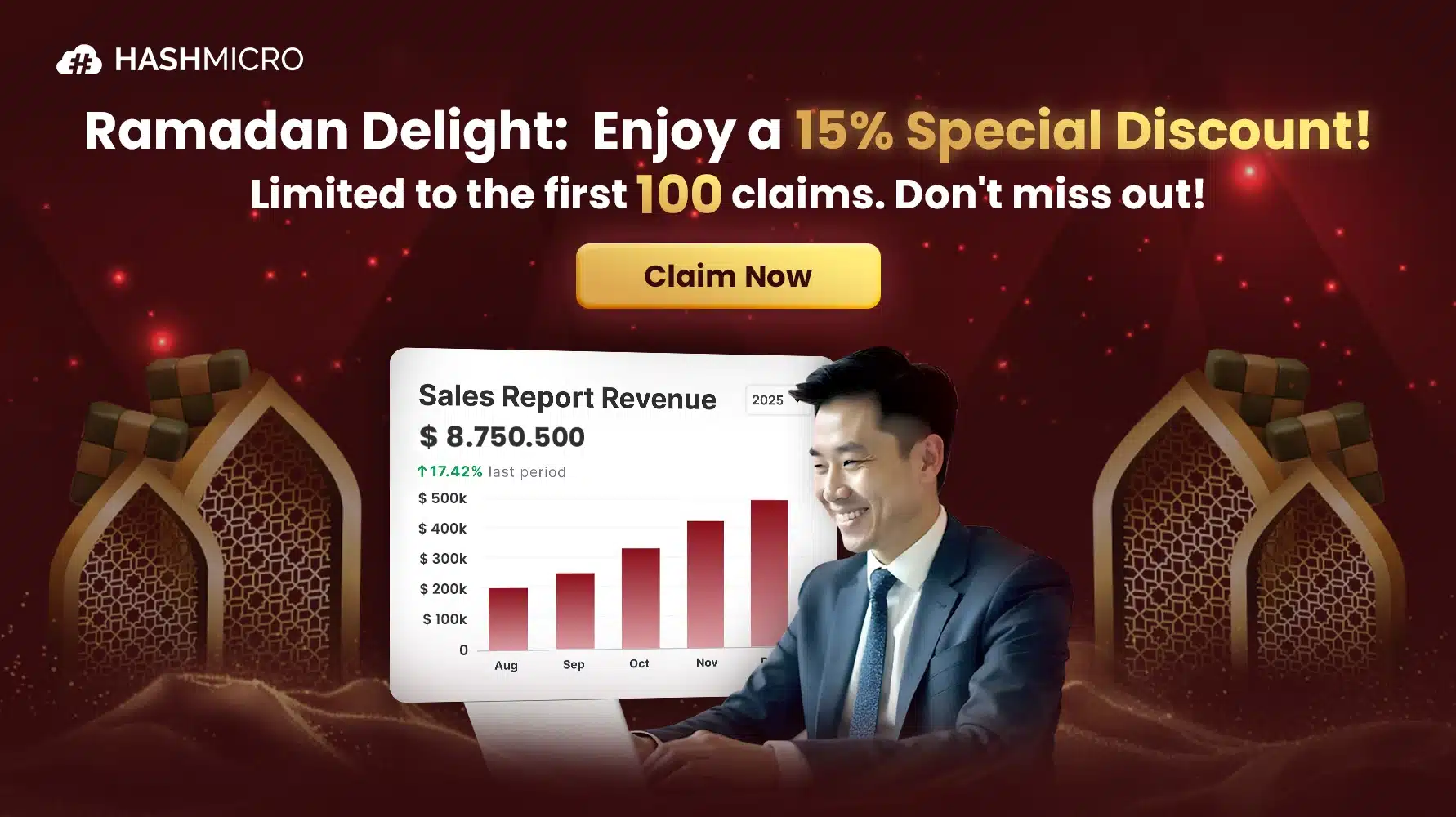
FAQ about Construction Procurement
-
What is construction procurement?
Construction procurement is the process of acquiring materials, equipment, and services needed to complete a construction project.
-
What are the 7 stages of procurement?
The seven stages are identification of needs, supplier selection, contract negotiation, purchase order creation, delivery and inspection, invoice processing, and payment.
-
What are the three types of procurement?
The three main types are direct procurement (materials and goods for production), indirect procurement (business operations support), and services procurement (outsourced labor and expertise).
-
What is a procurement process?
The procurement process involves planning, selecting vendors, negotiating contracts, purchasing, tracking deliveries, and managing payments to ensure smooth project execution.