Managing finished goods inventory is essential for ensuring seamless business operations and driving profitability, particularly in Malaysia’s fast-paced and diverse economic landscape. As companies scale, effective inventory management becomes even more critical for meeting customer expectations while minimizing costs.
One of the primary challenges in managing inventory is ensuring accuracy and integration across various departments, such as production, sales, and logistics. Without efficient systems, businesses risk issues like overstocking, stockouts, and delivery delays, all of which can negatively affect their bottom line.
A case study from a Malaysia herbal medicine company highlighted how improved inventory planning significantly reduced costs by optimizing stock levels and minimizing storage expenses. These improvements not only enhanced operational efficiency but also bolstered the company’s ability to adapt to market demand fluctuations.
For businesses looking to refine their production planning and inventory tracking, advanced solutions like inventory management software can make a transformative difference. With the right tools, Malaysian companies can optimize their processes, reduce waste, and achieve sustainable growth.
Key Takeaways
|
Table of Content
Content Lists
What is the Finished Goods Inventory?
Finished goods inventory refers to the stock of products that are fully manufactured and ready for sale to customers without requiring further processing. These goods represent the final stage of the production cycle and are stored until purchased or shipped to customers.
For example, in the Malaysian retail industry, finished goods may include ready-to-sell clothing, electronics, or packaged food. However, items in earlier production stages, such as raw materials (fabric, semiconductors, or ingredients), are not classified as finished goods until they are fully assembled and ready for distribution.
To effectively manage this type of inventory, businesses must track goods from the moment they are manufactured to their eventual sale. Employing a finished goods inventory formula and integrating advanced inventory management system can help maintain optimal stock levels, preventing overproduction or shortages while improving overall business efficiency.
Why Finished Goods Inventory Matters?
A comprehensive understanding of finished goods inventory is essential for maintaining operational efficiency and financial accuracy. By leveraging the finished goods formula, Malaysian companies can better track stock, manage production cycles, and maintain a balanced flow of goods from raw materials to finished products.
This understanding allows businesses to improve resource management, minimize waste, and avoid stockouts. Effective order processing also plays a vital role in ensuring the smooth transition of finished goods from production to customer delivery. Below are several reasons why efficient management of finished goods inventory is critical for companies in Malaysia:
1. Enhances financial planning
Accurately tracking finished goods inventory costs contributes to more reliable financial planning by ensuring precise data for balance sheets and income statements. Malaysian businesses can use this data to optimize cash flow, reduce financial risks, and allocate budgets effectively for future operations.
2. Maintains accurate asset records
In Malaysia’s competitive business environment, accurate accounting of current assets, including finished goods, is essential. The finished goods formula helps businesses track production progress and inventory, reducing costly errors and ensuring compliance with financial regulations.
3. Minimizes material waste
Efficient finished goods management prevents overproduction, reducing the likelihood of waste due to product obsolescence or spoilage. By maintaining optimal stock levels through restaurant inventory software or any kind can also lower storage costs, contributing to sustainable and cost-effective operations.
4. Streamlines inventory processes
Using advanced tools for inventory management enables Malaysian businesses to enhance visibility into production costs and identify areas for improvement. Whether automating processes or refining manual workflows, optimized inventory processes can significantly reduce bottlenecks and improve supply chain efficiency.
5. Reduces the risk of stockouts
A well-maintained inventory system ensures businesses can meet customer demands without delays. Accurate forecasting and stock level adjustments allow companies to maintain a balanced inventory, ensuring customer satisfaction and avoiding lost sales opportunities.
Steps in the Lifecycle of Finished Goods
Before a product is categorized as a finished good, it undergoes several critical stages in the production cycle. Understanding these stages is vital for Malaysian businesses to streamline inventory management and ensure cost efficiency.
- Raw materials: The journey of finished goods begins with raw materials. In industries such as manufacturing or food production, these include items like wood, plastic, or raw ingredients. Maintaining adequate raw material inventory ensures smooth production without interruptions.
- Work in Progress (WIP): Work in progress refers to partially completed products that are still in production. For instance, a car assembly plant in Malaysia might classify a vehicle awaiting engine installation as WIP. Tracking WIP is essential for assessing production efficiency and ensuring timely completion.
- Finished goods: Once all production stages are complete, the item becomes a finished good, ready for sale or distribution. For Malaysian exporters, for instance, finished goods might include fully assembled electronics or packaged agricultural products destined for overseas markets.
Streamlining each production stage is essential for efficient inventory management and accurate cost forecasting. Looking to simplify these processes? Discover a tailored software solution to optimize your finished goods management—click the banner below for an instant price estimate.
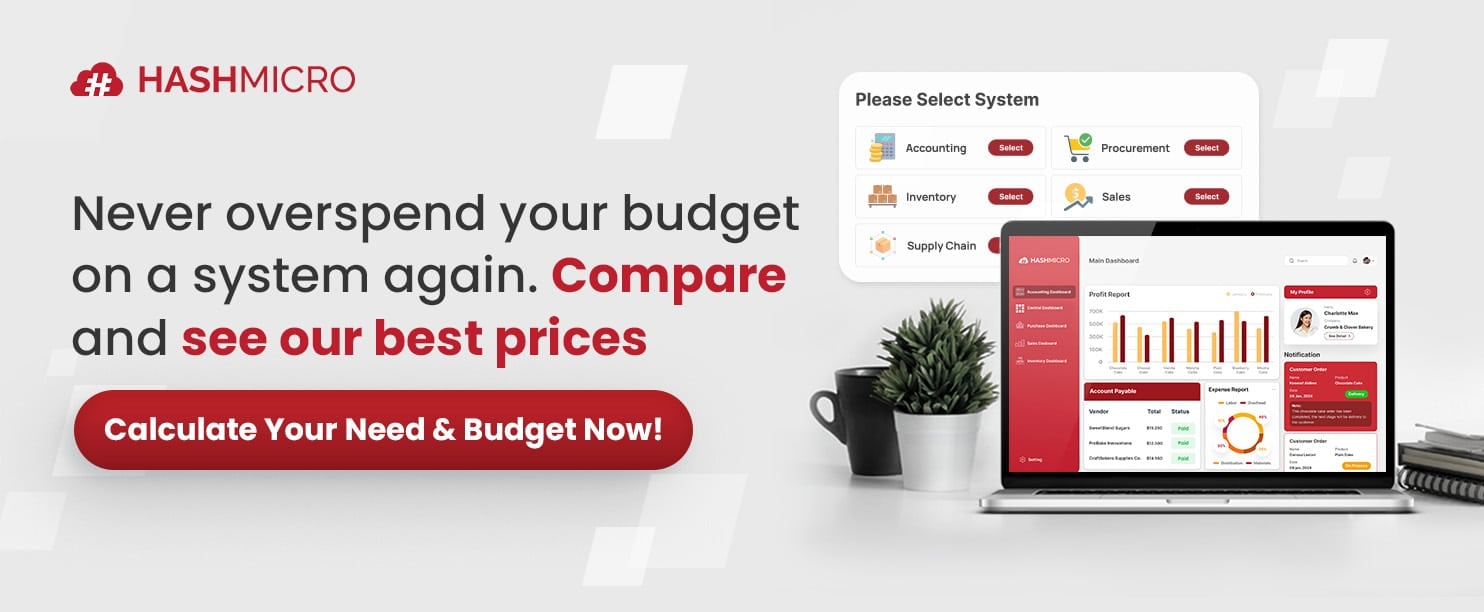
How to Calculate Finished Goods Inventory
Calculating finished goods inventory is essential for understanding the financial value of stock at the end of a fiscal period. The formula commonly used is as follows:
Finished Goods Inventory Formula: Beginning Inventory + Cost of Goods Manufactured (COGM) – Cost of Goods Sold (COGS) = Ending Finished Goods Inventory
For example, a Malaysian furniture manufacturer starts the quarter with RM100,000 in finished goods inventory. It produces RM90,000 worth of new products (COGM) and sells RM70,000 worth of goods (COGS). Using the formula: RM100,000 + RM90,000 – RM70,000 = RM120,000
This calculation helps businesses assess whether their stock levels align with sales performance and operational needs. It also provides valuable insights for pricing strategies and financial reporting.
Managing Finished Goods Inventory with HashMicro’s Advanced Systems
For Malaysian businesses aiming to streamline operations, adopting advanced inventory management systems is key to overcoming challenges associated with finished goods. HashMicro’s Inventory Management Software offers comprehensive tools to optimize stock management and ensure seamless operations. Below are some key features that can transform inventory processes:
- RFID Warehouse Automation: HashMicro integrates RFID technology into its inventory system, automating stock movement tracking. This feature is particularly beneficial for industries in Malaysia with high inventory turnover, ensuring accurate, real-time visibility of finished goods without manual intervention.
- Stock Forecasting: By analyzing sales trends and seasonal data, HashMicro’s stock forecasting feature ensures businesses can anticipate demand fluctuations. This capability is critical for Malaysian industries such as retail and F&B, where demand often varies based on festivals or consumer preferences.
- Quality Control Management: Ensuring product quality is crucial, especially for businesses dealing with exports or regulated sectors. The software’s quality control feature enforces standards by verifying that each product meets predefined criteria before being classified as finished goods.
- First Expiry First Out (FEFO) System: For Malaysian businesses managing perishable goods, such as those in the halal food industry, the FEFO system ensures older stock is sold first, reducing waste and adhering to compliance standards.
- Stock Aging Reports: This feature identifies slow-moving inventory, helping businesses adjust stock levels and avoid unnecessary storage costs. It also enables data-driven decisions for promotions or stock clearance sales.
- Barcode and QR Code Integration: With integrated barcode and QR code scanning, Malaysian businesses can speed up inventory updates while reducing manual errors. This feature supports efficient warehouse operations and enhances overall productivity.
Benefits of Inventory Management Software for Malaysian Businesses
Implementing inventory management software has become a crucial step for businesses in Malaysia to stay competitive in a dynamic market. By automating inventory processes and providing real-time data, these systems allow companies to manage their stock efficiently while minimizing errors and costs. Here are some key advantages that Malaysian businesses can reap from adopting inventory management software:
- Improved Efficiency: Automating manual processes saves time and reduces the likelihood of human errors.
- Cost Reduction: Optimizing stock levels minimizes storage costs and prevents overproduction.
- Real-Time Insights: Access to live inventory data allows for quicker decision-making and improved responsiveness to market demands.
- Regulatory Compliance: Features like FEFO and quality control help businesses meet Malaysian industry standards and regulations.
- Scalability: The system grows with your business, adapting to increased inventory needs or expanded product lines.
By implementing HashMicro’s inventory management system, Malaysian businesses can not only improve operational efficiency but also gain a competitive edge in the market.
Conclusion
Efficient management of finished goods inventory is crucial for ensuring smooth business operations and maintaining customer satisfaction. By optimizing inventory tracking and adopting advanced tools, Malaysian companies can minimize costs, reduce waste, and improve overall productivity.
HashMicro’s Inventory Management System provides a reliable solution tailored to the unique needs of Malaysian businesses. Its robust features, from RFID automation to stock forecasting, ensure accurate inventory management while supporting regulatory compliance.
Ready to transform your inventory processes? Schedule a free demo today and experience firsthand how HashMicro’s system can enhance your finished goods management and drive your business forward.
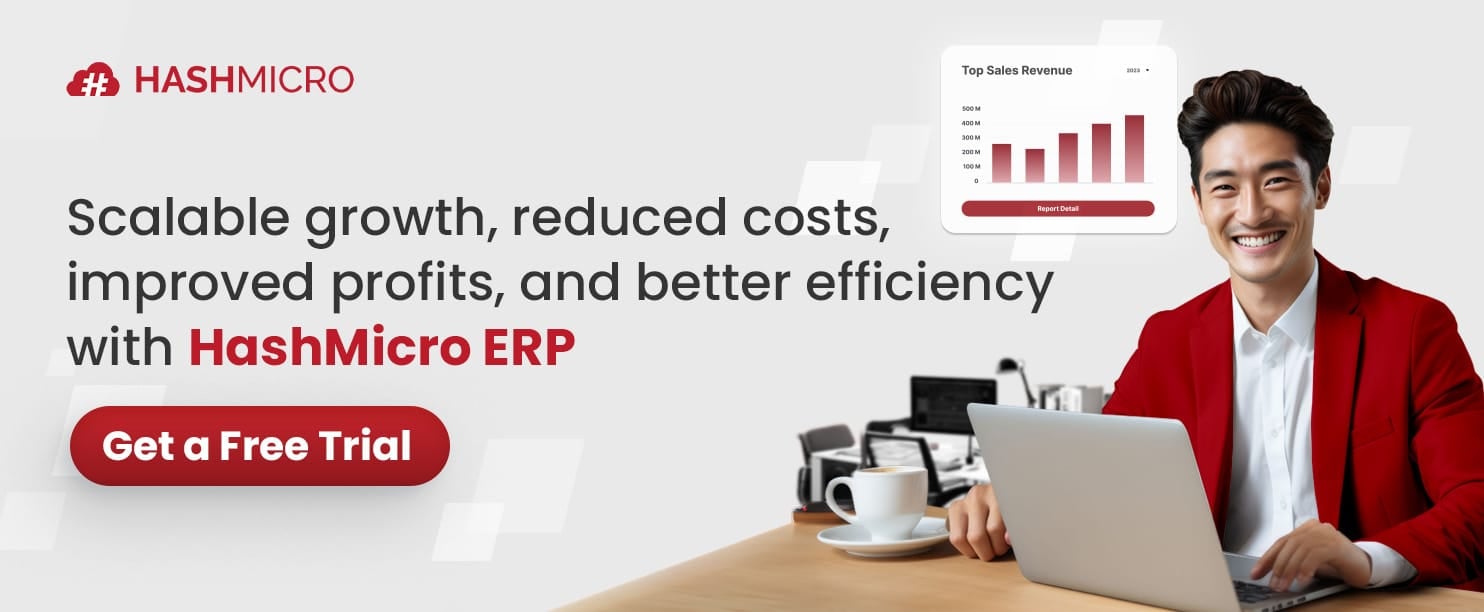
FAQs on Finished Goods Inventory
-
How do you record finished goods inventory?
Finished goods inventory is recorded by tracking the cost of manufacturing, which includes raw materials, direct labor, and overhead costs. This total is then categorized as “finished goods” in your inventory management system or accounting software once the products are complete and ready for sale.
-
How do you find finished goods in inventory?
You can determine finished goods inventory by using the formula: Beginning Finished Goods Inventory + Cost of Goods Manufactured – Cost of Goods Sold = Ending Finished Goods Inventory. This calculation ensures accurate tracking of stock ready for sale, helping businesses manage inventory levels effectively.
-
What is the best example of a finished goods inventory?
A clear example of finished goods inventory is packaged beverages in a bottling plant. These are ready for distribution and sale, having completed all production stages, including bottling, labeling, and packaging.
-
What are examples of finished goods?
Examples of finished goods include electronics like smartphones, ready-to-wear clothing, and packaged food products. These items are fully assembled, meet quality standards, and are ready for sale to end customers.