Optimizing your fulfillment warehouse is essential for maintaining a competitive edge in today’s fast-paced business environment. By improving distribution efficiency and reducing shipping costs, businesses can enhance customer satisfaction and scale operations effectively.
One of the most effective ways to achieve this is by leveraging a fulfillment warehouse. This specialized facility helps businesses manage inventory, process orders, and ensure timely deliveries with minimal operational hassle.
Whether you run an ecommerce fulfillment warehouse or seek warehouse fulfillment services, integrating a professional fulfillment solution into your supply chain can streamline operations and allow you to focus on business growth.
This article explores how a fulfillment warehouse optimizes logistics, improves efficiency, and supports business scalability. Read on to discover how investing in a third-party logistics service can enhance your fulfillment strategy.
Key Takeaways
|
Table of Content
Content Lists
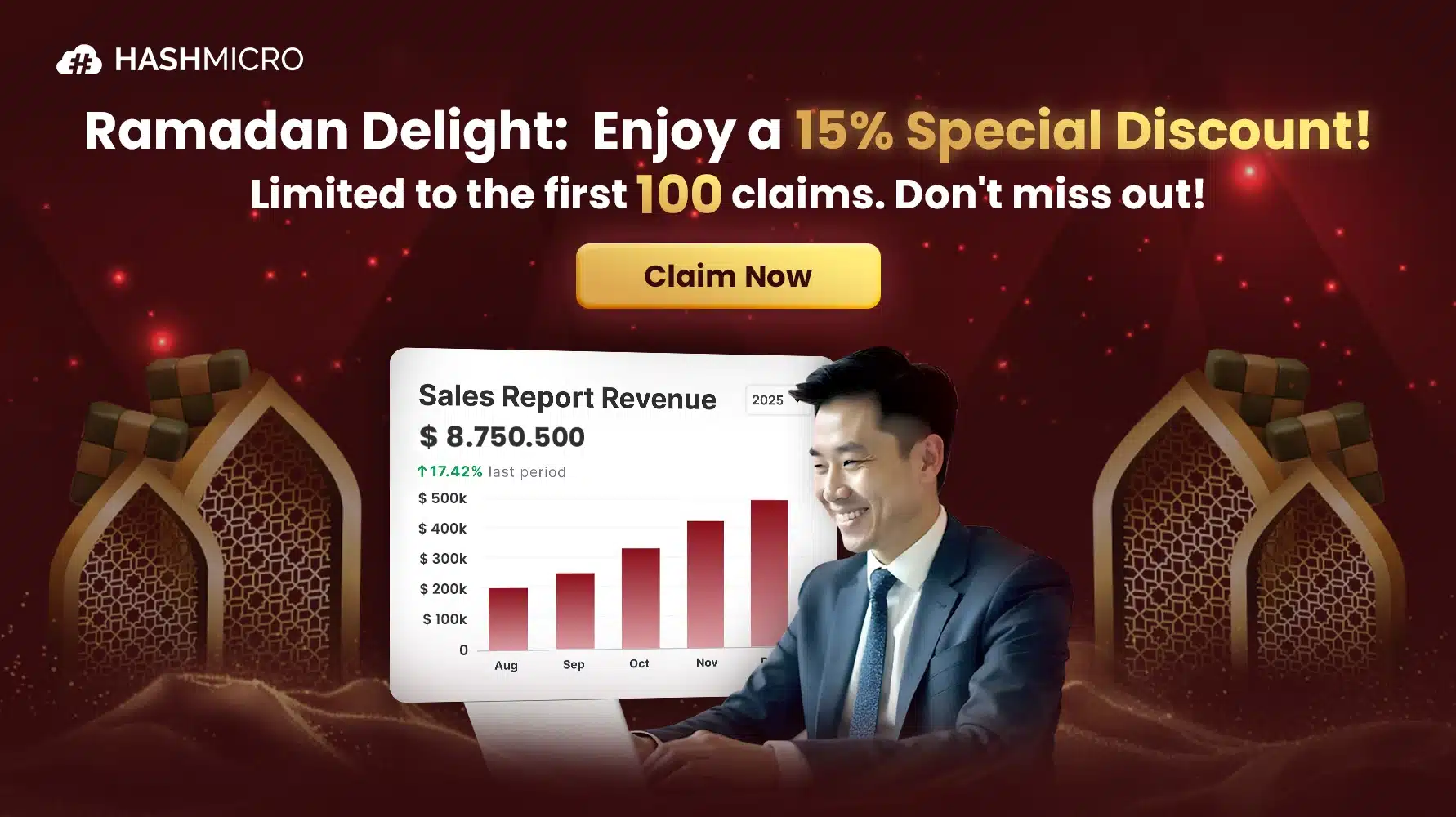
The Critical Role of a Fulfillment Warehouse in Ecommerce Success
A well-optimized fulfillment warehouse is essential for ecommerce businesses looking to streamline logistics and improve order fulfillment. It ensures efficient inventory management, accurate order processing, and timely deliveries—key factors in meeting customer expectations and driving repeat purchases.
By utilizing warehouse fulfillment services, businesses can reduce shipping delays and enhance operational efficiency. A structured fulfillment process, from inventory tracking to packing and shipping, minimizes errors and optimizes delivery speed, strengthening brand reputation in a competitive market.
Additionally, integrating automation and smart inventory systems boosts accuracy and reduces costs. Investing in a reliable third-party logistics service allows businesses to scale efficiently while focusing on growth and customer satisfaction.
When to Upgrade to a Professional Fulfillment Warehouse
As your business grows, managing inventory, processing orders, and ensuring on-time deliveries becomes more complex. What once worked for a small operation may no longer be efficient as order volumes increase. If you’re struggling to keep up, it may be time to upgrade to a professional fulfillment warehouse.
Frequent shipping delays, stock discrepancies, and errors in order fulfillment are clear signs that your current system is falling short. A warehouse fulfillment service offers advanced inventory tracking, optimized storage, and faster processing, helping businesses maintain accuracy and keep customers satisfied.
Expanding into new markets also presents logistical challenges. A strategically located ecommerce fulfillment warehouse can reduce shipping costs and improve delivery speed, making it easier to serve customers across different regions without logistical headaches.
If scaling your operations has become overwhelming, upgrading to a professional fulfillment warehouse provides the efficiency and flexibility needed for long-term growth. Partnering with the right fulfillment provider allows you to focus on business expansion while ensuring a seamless supply chain.
Optimizing Fulfillment Warehouse Layout
A well-structured fulfillment warehouse layout plays a crucial role in maximizing operational efficiency, reducing errors, and speeding up order fulfillment. By strategically organizing your warehouse, businesses can streamline workflows, improve inventory accessibility, and minimize handling time.
1. Smart Inventory Organization
Proper inventory categorization and labeling ensure that products are easy to locate and pick. Using a logical storage system, such as ABC classification (grouping items by sales frequency), minimizes search time and increases order fulfillment speed.
2. Optimized Flow Pathways
An efficient warehouse layout should reduce unnecessary movement. Organizing picking stations, packing areas, and shipping zones in a seamless flow helps workers navigate the space efficiently, leading to faster order processing.
3. Leveraging Technology and Automation
Implementing barcode scanning, conveyor belts, and robotic picking systems significantly enhances accuracy and reduces manual errors. Automation in warehouse layout boosts productivity while cutting down operational costs.
Understanding the Impact of On-Demand Fulfillment Warehousing
On-demand warehousing is transforming logistics by offering flexible, scalable storage solutions. Unlike traditional warehousing, which requires long-term leases, on-demand warehousing allows businesses to adjust storage capacity based on demand, improving efficiency and cost management.
1. Cost-Effective Storage Solutions
Instead of committing to fixed warehouse space, businesses can use on-demand warehousing services to pay only for what they use, reducing unnecessary expenses and increasing financial flexibility.
2. Seamless Seasonal & Market Expansion
During peak seasons or business expansions, companies can scale storage up or down without long-term contracts, ensuring they always have the right amount of space when needed.
3. Faster Order Fulfillment & Delivery
With access to multiple fulfillment warehouse locations, businesses can store products closer to customers, reducing shipping time and costs while enhancing customer satisfaction.
4. Optimized Inventory & Risk Management
By leveraging real-time inventory tracking, businesses can avoid overstocking or stock shortages, ensuring they always maintain optimal stock levels for smooth operations.
Integrating Eco-Friendly Practices into Fulfillment Warehouse Operations
Sustainability is becoming a priority for businesses looking to reduce costs and minimize their environmental impact. Simple changes, like switching to LED lighting and optimizing heating and cooling systems, can significantly cut energy consumption. Using electric delivery vehicles and route optimization also helps lower fuel costs and reduce carbon emissions.
Reducing waste is another key step. Businesses can replace single-use plastics with biodegradable or recyclable packaging to create a more sustainable shipping process. Setting up recycling stations for materials like cardboard and plastic ensures warehouses contribute to waste reduction efforts while keeping operations efficient.
Adopting green logistics strategies not only benefits the environment but also boosts brand reputation. Customers are increasingly drawn to businesses that prioritize eco-friendly practices, making sustainability a smart move for both the planet and long-term business growth.
Choosing a Warehouse Management System (WMS) for Your Fulfillment Warehouse
A Warehouse Management System (WMS) is essential for keeping a fulfillment warehouse running smoothly. It helps businesses track inventory in real-time, reduce errors, and speed up order processing. Choosing the right WMS requires careful consideration to ensure it aligns with your business operations, growth plans, and budget.
1. Key Features for Efficiency
A good WMS should offer real-time inventory tracking so you always know what’s in stock. Features like barcode scanning and order processing automation help speed up fulfillment while minimizing errors. Some systems also provide demand forecasting to help businesses plan inventory based on sales trends, preventing stock shortages or excess inventory.
Additionally, a WMS with automated alerts can notify warehouse managers of low stock levels, delayed shipments, or unexpected demand spikes. This ensures quick decision-making and reduces the risk of disruptions in the supply chain.
Choosing a system that supports batch picking or wave picking can also increase efficiency by allowing multiple orders to be processed at once, reducing labor costs and improving order fulfillment speed.
2. Scalability & System Compatibility
As your business grows, so should your WMS. A scalable system can handle higher order volumes, multiple warehouse locations, and increased product variety. It’s also crucial that the WMS integrates smoothly with your ecommerce platforms, ERP systems, and shipping providers, ensuring a seamless flow of data across different departments.
An adaptable WMS should also support multi-channel fulfillment, enabling businesses to process orders from different sales channels—such as websites, marketplaces, and retail stores—without delays or errors.
The ability to customize workflows and automate repetitive tasks helps businesses stay efficient even during peak seasons or rapid growth. A flexible system ensures warehouses can scale their operations without sacrificing speed or accuracy.
3. Ease of Use & Accessibility
A WMS should be intuitive and easy to use so warehouse staff can operate it without extensive training. Cloud-based systems provide remote access, allowing business owners and managers to monitor warehouse operations in real-time from anywhere, making management more flexible.
A well-designed interface with drag-and-drop features, visual dashboards, and mobile compatibility can improve productivity by making it easier to manage warehouse tasks.
Mobile access allows employees to scan items, update inventory, and receive shipment notifications directly from handheld devices. This ensures real-time updates and fewer processing delays, making operations smoother and more efficient.
Leveraging Technology to Enhance Fulfillment Warehouse Productivity
The adoption of technology in warehouse operations has significantly improved efficiency, accuracy, and cost management.
Automation has become a game-changer, allowing warehouses to streamline order fulfillment with automated storage and retrieval systems (AS/RS), conveyor belts, and robotic picking solutions. By minimizing manual tasks and reducing human errors, these systems ensure faster order processing, improved accuracy, and quicker shipping times, ultimately enhancing customer satisfaction.
In addition to automation, Artificial Intelligence (AI) is transforming inventory management system by providing data-driven insights into sales trends, stock levels, and demand forecasting.
AI-powered systems help businesses optimize stock replenishment, preventing both overstocking and stock shortages. Automated reordering ensures inventory is maintained efficiently, reducing the risk of stockouts and minimizing unnecessary holding costs.
Another crucial innovation is real-time tracking and IoT (Internet of Things) integration, which provides warehouses with greater visibility and control over inventory movement. Technologies such as RFID (Radio Frequency Identification) and smart sensors allow for real-time stock monitoring and improving order accuracy.
Conclusion
A fulfillment warehouse is essential for businesses looking to streamline logistics, optimize order fulfillment, and enhance customer satisfaction. By integrating efficient warehouse layouts, automation, and scalable solutions, businesses can ensure that inventory management and shipping processes run smoothly while keeping operational costs under control.
If you’re looking to optimize your fulfillment warehouse operations and enhance inventory management, HashMicro’s Warehouse Management Software can help. With features like automated inventory tracking, real-time stock visibility, and seamless order fulfillment, our solution ensures that your warehouse operates with maximum efficiency while reducing errors and costs.
Want to see how a smart warehouse management system can transform your logistics? Request a free demo today and experience the power of automation in streamlining your fulfillment operations.
FAQ about Fulfillment Warehouse
-
What is a fulfillment warehouse, and how does it work ?
A fulfillment warehouse is a facility that stores, processes, and ships orders on behalf of businesses. It manages inventory storage, order picking, packing, and shipping, ensuring that products reach customers efficiently. Many fulfillment warehouses also use automation and warehouse management systems (WMS) to streamline operations and improve accuracy.
-
How can a fulfillment warehouse improve order accuracy and delivery speed ?
A fulfillment warehouse enhances order accuracy by using barcode scanning, automated sorting, and inventory tracking systems to ensure the right products are packed and shipped. Additionally, strategically located warehouses help reduce shipping times by storing inventory closer to customers, leading to faster deliveries and improved customer satisfaction.
-
When should a business upgrade to a professional fulfillment warehouse ?
Businesses should consider upgrading when they experience increasing order volumes, frequent shipping delays, stock discrepancies, or difficulty managing inventory. A professional fulfillment warehouse offers real-time tracking, optimized storage, and automated order processing, allowing businesses to scale efficiently while maintaining accuracy.
-
How does a Warehouse Management System (WMS) enhance fulfillment operations ?
Businesses should consider upgrading when they experience increasing order volumes, frequent shipping delays, stock discrepancies, or difficulty managing inventory. A professional fulfillment warehouse offers real-time tracking, optimized storage, and automated order processing, allowing businesses to scale efficiently while maintaining accuracy.