It’s peak season, and orders are flying in. Your warehouse team moves fast, but there’s a problem. Your system says 500 units of a product are in stock, but only 490 are on the shelves. Worse, 10 units are damaged and can’t be sold. That means you actually have 480 ready to ship, not 500. These issues may arise because of an ineffective inventory audit.
Instead of disappointing 20 customers and scrambling for last-minute fixes, regular inventory audits help prevent these issues. These checks ensure that recorded stock matches actual inventory and that everything in storage is fit for sale—avoiding costly errors and operational setbacks.
As a business owner in Malaysia, inventory management isn’t just about keeping count—it’s about ensuring smooth operations and maximizing profits. In this guide, you’ll learn key audit strategies and smart technologies to keep your business running efficiently. Let’s dive in!
Key Takeaways
|
Table of Content
Content Lists
What is an Inventory Audit?
Inventory audits involve counting and assessing a business’s physical goods, then comparing that data to its records. It’s similar to an inventory count, but instead of just tracking quantities, you also check for damage, spoilage, or mistakes.
As a result, the company gets a more accurate view of what’s actually sellable.
Moreover, the audits are useful to identify the immediate causes of inventory shrinkage and keep stock levels in check. Furthermore, purchasing software helps plan inventory costs and manage orders more efficiently, leading to better control over operations and finances.
Benefits of Inventory Audit
Even though audit procedures take time, they’re essential for keeping records accurate. They help you:
- Spot discrepancies: Your stock should match your records. If there’s a gap, it could point to inventory shrinkage. Finding the issue gives you a chance to address whatever’s causing it.
- Plan for future purchases: A thorough inventory audit helps you prepare for upcoming orders. By tracking sales and revenue, you get a better idea of how much you’ll need to spend to restock.
- Keep stock levels balanced: Ordering the right amount of inventory reduces storage costs and prevents stockouts. Accurate counts help you avoid buying too much or too little.
- Fix workflow issues: Missing inventory often signals process inefficiencies, whether it’s lost items in transit or problems with warehouse management. Catching these shortages helps you identify and resolve those issues.
Inventory Audit Procedures
Inventory audits involve several methods to ensure stock accuracy and uncover any discrepancies in records. Below are nine key procedures that help businesses maintain better control over their inventory.
1. Physical Inventory Count
Physical inventory method involves manually counting stock and comparing it with inventory records. Any discrepancies, including missing or damaged items, should be flagged.
While this can be time-consuming for large inventories, businesses with minimal stock find it more manageable. Barcode scanners help speed up the process and improve accuracy by instantly updating inventory data.
2. ABC Analysis
This technique categorizes inventory into different groups based on profitability and importance to the business. For example:
- “A” products are the most valuable or essential to operations. For an outdoor goods store, these might include bestsellers like tents and lanterns.
- “B” products have moderate value—less critical than “A” items but still important. Camping chairs, for example, may not be top sellers but are expected by customers.
- “C” products have the lowest value and profit margins, such as premade camping meals or niche accessories.
Grouping inventory this way helps prioritize resources, focusing audits and stock management on the most impactful items.
3. Analytical Procedures
This approach compares inventory data over time to assess trends and system efficiency. By analyzing factors like inventory turnover, return rates, and gross margins, businesses can better predict future demand and adjust stock levels accordingly.
4. Finished Goods Inventory
Finished goods are ready-to-sell products, excluding damaged or incomplete items like unassembled kits.
Their value helps estimate future revenue. To calculate it, start with the previous inventory value, add the cost of newly purchased or produced goods, and subtract the cost of goods sold.
5. Overhead Analysis
Inventory management isn’t just about the products—it also includes indirect costs like rent, utilities, and administrative expenses.
An overhead analysis reviews these costs to help with budgeting and pricing, ensuring your prices reflect the true cost of production while remaining competitive.
6. Freight Cost Analysis
This method evaluates the total expenses of transporting goods, including hidden costs like border fees or carrier surcharges.
Reviewing recent shipping data, such as costs, routes, and shipment volumes, can reveal ways to cut expenses. Strategies like consolidating smaller shipments or scheduling deliveries during off-peak times can help reduce costs and improve efficiency.
7. Cutoff Analysis
A cutoff analysis involves temporarily pausing certain activities, such as shipping and receiving, to conduct a precise inventory count.
Since the process can take anywhere from a few hours to several days, scheduling it at a convenient time prevents errors like missed items or duplicate counts caused by stock movement.
8. Reconcile Inventory Discrepancies
Compare physical stock counts with recorded inventory figures. If numbers don’t match, identify the cause—such as miscounts, theft, or damaged goods—and update records accordingly to maintain accuracy.
9. Verify Invoices Against Shipping Logs
Cross-check invoices with shipping records to confirm that every dispatched item has been properly billed and documented. Address any missing or mismatched entries to prevent financial and inventory errors.
How to Conduct Inventory Audit
You can handle an audit internally or bring in a professional auditor for a more specialized approach. Either way, following a structured process helps maintain accuracy. Here are five key steps to follow:
1. Plan and Prepare
Set up the workspace so all necessary information is easily accessible. Define the audit’s objectives and select the right procedures to match them. For example, if the goal is to conduct a physical inventory count, ensure there’s a plan in place for scheduling, tools, and staff coordination.
For businesses handling bulk stock, adopting wholesale inventory software can best-streamline audits and prevent costly errors.
2. Carry Out the Audit
Once the type of audit is decided, begin the process. This might involve reviewing financial records to assess overhead costs, analyzing purchase and sales data to evaluate finished goods, or physically counting stock in warehouses.
Make sure the team understands the audit procedures to avoid unnecessary delays or mistakes. Choose a time that minimizes disruptions to daily operations, and follow the outlined steps carefully.
3. Review and Compare Findings
Examine the audit data and check whether it aligns with expectations. Depending on the audit type, this could involve verifying product quantities, comparing actual shipping costs with estimates, or assessing whether the right items have been prioritized for restocking.
4. Pinpoint and Resolve Discrepancies
Look for inconsistencies or unexpected trends in the data. You might discover higher-than-expected overhead costs or missing inventory in a specific warehouse.
Identifying these gaps allows you to develop targeted solutions, such as refining stock management practices in locations where losses occur.
5. Enhance Future Audits
Inventory management isn’t a one-time task—it requires continuous improvement. After completing an audit, assess any challenges in the process and find ways to make future audits more efficient.
Challenges in Inventory Audit
Managing inventory manually comes with serious risks, especially when relying on spreadsheets. Errors in stock adjustments, calculations, and shipping records can create discrepancies that disrupt inventory accuracy and financial reporting.
Key challenges include:
- Frequent Data Entry Errors – Mistakes in recording stock levels, pricing, or order quantities can lead to miscounted inventory and incorrect financial statements.
- Lack of Real-Time Visibility – Manual tracking fails to provide instant updates, causing delays in stock monitoring and mismatches between recorded and actual inventory.
- Stock Mismanagement – Over-ordering leads to excess inventory and storage costs, while under-ordering results in stockouts and lost sales opportunities.
- Time-Consuming and Labor-Intensive – Employees spend hours updating records and reconciling discrepancies, diverting time from higher-value tasks.
To overcome these challenges, many businesses are adopting automated inventory systems. These systems range in features, capabilities, and ultimately, pricing. If you want to know how much an inventory system would cost, click on our banner below and get your customized quote.
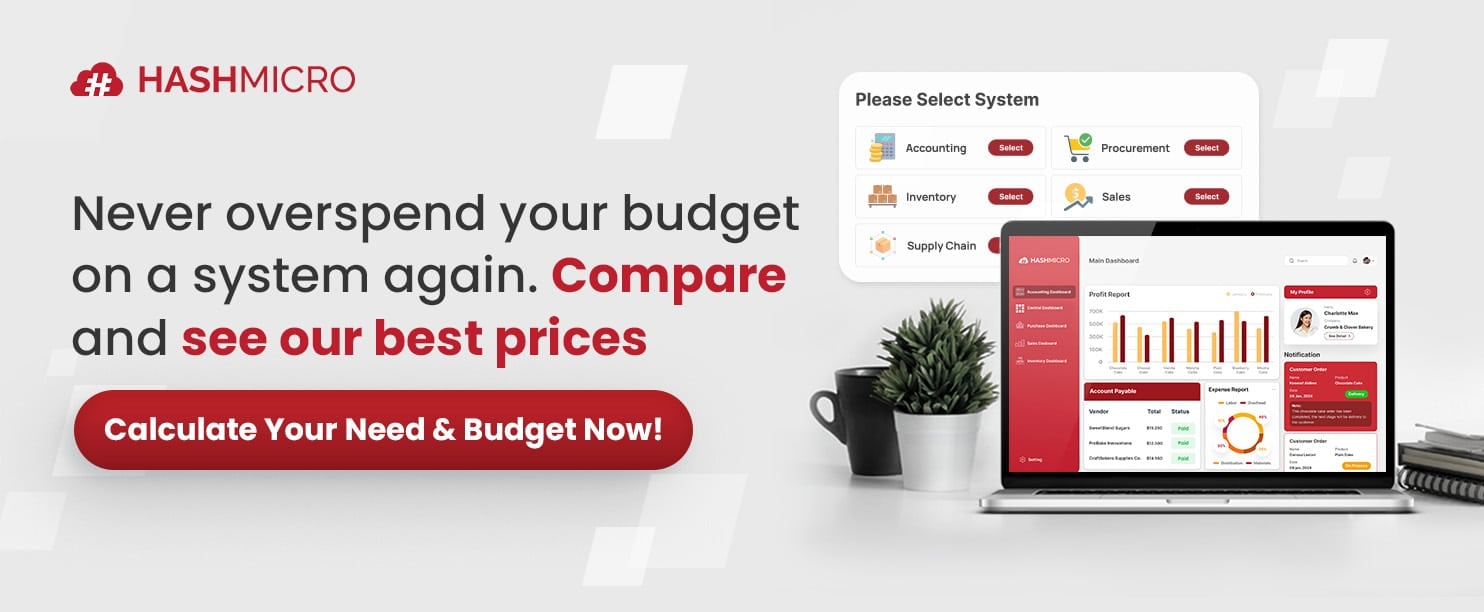
Best Practices for Effective Inventory Audits
Following effective audit strategies helps simplify the process and provides valuable data to improve operations. Here are some key practices to consider:
- Establish a Regular Audit Schedule – Conducting audits on a monthly, quarterly, or annual basis keeps inventory data consistent. Recognizing patterns over time makes it easier to detect discrepancies early.
- Train Employees on Audit Procedures – A well-trained team performs audits more efficiently and with fewer mistakes. Regular training ensures staff understands proper processes and minimizes human errors.
- Use Technology to Simplify Audits – Tools like barcode scanners and inventory management software help automate data collection, reducing errors and improving accuracy.
- Break Audits into Manageable Sections – Instead of auditing everything at once, divide the warehouse into smaller zones and check one section at a time. This prevents staff from feeling overwhelmed and keeps the process organized.
To overcome these challenges, many businesses, including those moving in the FMCG sections are adopting automated solutions like retail inventory software to improve stock accuracy and reduce manual errors.
Simplify Your Inventory Audits with HashMicro Inventory Software
Struggling with inventory audits? Wasting hours on manual counts, missed discrepancies, and stock inaccuracies? HashMicro Inventory Software transforms the way businesses handle inventory—faster, smarter, and mistake-free.
With real-time tracking and automation, you get precise stock data at your fingertips, so you can audit without the usual headaches. Not only that, your entire inventory and warehouses, be it single or multiple-branch, can be managed easily, as the software can give real-time updates.
What else can HashMicro do? Let’s take a look at the features:
- RFID & 3D Warehouse Mapping: No more guessing where stock is located. Advanced RFID tracking and 3D warehouse visualization give you an instant, real-time view of every item’s exact location and quantity.
- Smart OCR for Instant Data Capture: Say goodbye to manual entry errors! With Optical Character Recognition (OCR), your system automatically records incoming goods, updating inventory without the hassle.
- AI-Powered Stock Forecasting: Running out of stock or overordering? Predict demand with precision using run rate reordering, ensuring you always have the right amount of inventory—never too much, never too little.
- Built-in Quality Control: Avoid losses from defective stock. Automated quality checks ensure only the best products hit the shelves, so that your company only sells top-tier products.
- Barcode & QR Code Integration: Speed through audits with seamless barcode and QR code scanning, eliminating human errors and making stock tracking effortless.
Conclusion
Inventory audits involve carefully counting physical stock, finding discrepancies, and maintaining accuracy to optimize business profitability. Effective audits help businesses reduce costs, minimize errors, improve stock management, and streamline operational efficiency.
Ready to ditch tedious manual counts and messy spreadsheets for smarter, faster inventory management? HashMicro Inventory Software brings real-time accuracy to your fingertips, effortlessly simplifying audits and boosting your company’s profits.
With powerful features like RFID tracking, OCR scanning, and smart forecasting, HashMicro makes inventory headaches history.
It’s your turn; try the free demo and see just how easy inventory management can really be!
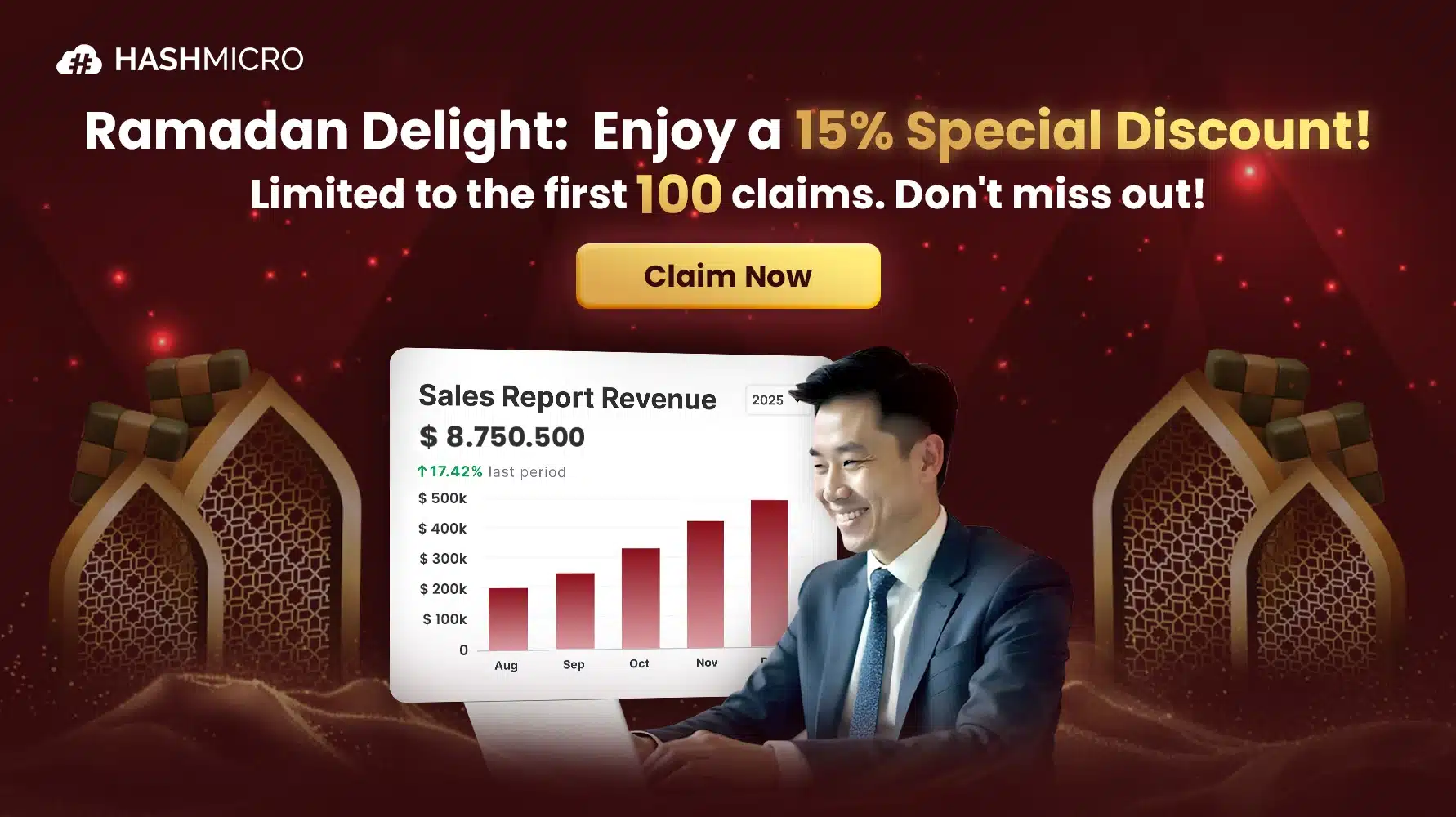
Frequently Asked Questions on Inventory Audit
-
What is cycle counting, and how does it differ from traditional physical inventory counts?
Instead of shutting down operations for a full stock check, cycle counting lets businesses audit inventory in small sections over time. This method reduces disruptions, catches errors sooner, and keeps stock levels accurate year-round.
-
Why is stock-taking important for businesses?
Stock-taking isn’t just about counting products—it’s about ensuring your records match reality. By physically verifying stock, businesses spot discrepancies, prevent losses, and keep operations running smoothly.
-
How does technology make inventory audits easier?
Barcode scanners, AI-driven forecasting, and real-time inventory software eliminate guesswork, reduce human errors, and speed up audits. With the right tools, businesses gain better control over stock without manual hassle.
-
What are the most common inventory audit methods?
Businesses use physical inventory counts, ABC analysis (categorizing items by value), and analytical procedures that compare sales trends over time