How much stock should you really keep? Too little leads to stock-outs, which means lost sales. Too much ties up cash in storage, increases costs, and risks products becoming obsolete before they sell. Striking the balance in inventory levels is surely complicated, don’t you think?
Without proper management, businesses either scramble to restock or struggle with excess inventory that takes up space and drives up costs. So, to optimize your inventory management, you need more than just tracking stock. But what else do you possibly need?
This guide will answer your questions. We will break down everything you need to know, from essential formulas to best practices, so you can take full control of your inventory and avoid costly mistakes.
Key Takeaways
|
Table of Content
Content Lists
What are Inventory Levels?
Inventory level refers to the quantity of goods available in a company’s warehouse or storage facility at any given moment. It encompasses various types of inventory, including raw materials, semi-finished goods, and finished products ready for sale, which all need to be kept in optimal conditions.
For example, if inventory levels are too low, there won’t be enough stock to meet incoming demand. During such instances, missed sales opportunities and lost revenue can occur, especially if the products aren’t available for backorders.
On the other hand, maintaining excessive inventory requires a significant upfront investment. The longer these goods remain in storage, the higher the carrying costs. By the time they are eventually sold, profit margins may have decreased already.
Different Types of Inventory Levels
Inventory levels within the supply chain help determine the optimal amount of stock a company should maintain. There are four key inventory levels: minimum, maximum, danger, and average stock levels.
1. Minimum Inventory Level
Minimum inventory levels represent the lowest quantity a company should maintain for each Stock Keeping Unit (SKU). Falling below this level increases the risk of the stock being empty, thus preventing the company from meeting customer demand.
To prevent this, businesses must ensure minimum stock levels are maintained. Insufficient stock may also lead to longer lead times.
2. Maximum Inventory Level
Maximum inventory levels indicate the highest quantity a business should hold at any time. Exceeding this level results in unnecessary overhead costs.
To determine maximum stock levels, companies must analyze sales trends, seasonal fluctuations, and inventory expenses. Before issuing a purchase order (PO), businesses should calculate the maximum inventory required.
3. Danger Inventory Level
The danger inventory level indicates that stock for a specific item is critically low. When inventory reaches this point, immediate restocking is necessary to prevent supply shortages and production disruptions.
Companies often need to source products from suppliers who can deliver quickly, but this urgency can lead to higher procurement costs compared to standard pricing.
4. Average Inventory Level
An average inventory level represents the optimal stock quantity a company should maintain. This ensures customer demand is met while keeping inventory costs low, improving cash flow, and maximizing profit margins.
For instance, if a business sells 150 units monthly, they should maintain an average stock of 150 items, so that the expenses aren’t too much.
What are Minimum and Maximum Inventory Levels?
To determine the ideal inventory level, the following metrics are essential:
- Minimal stock levels: This refers to the lowest number of products required to fulfill all orders. If inventory runs out, safety stock—extra goods reserved for emergencies—serves as a backup to prevent stockouts.
- Maximum stock levels: This represents the highest quantity of inventory that can be stored without incurring excessive warehousing costs. Surpassing this limit may lead to overstock, potentially causing storage space shortages.
It is essential to differentiate optimal inventory levels from the average inventory level, which estimates the quantity of stock available in a facility over a given period.
Factors to Determine the Optimal Inventory Level
When setting target inventory levels for your business, key factors to consider include:
- Product handling times: More inventory requires additional time and resources for movement and management.
- Lead Time: Warehouse management teams must monitor supplier lead times—the period between placing a stock order and receiving the goods.
- Stock Turnover: Effective inventory organization relies on tracking turnover rates for each SKU. Demand analysis techniques, such as ABC analysis, help classify SKUs and optimize stock placement to improve efficiency.
- Sales channel expansion: Entering new markets or platforms complicates inventory management and requires careful stock level adjustments.
- Market trends: Research, such as from McKinsey’s survey, indicates that businesses now maintain higher overall stock levels to balance resilience with cost control.
As inventory optimization remains a priority for many businesses, finding the right balance between stock availability and cost efficiency is crucial.
How to Calculate Inventory Levels
Knowing how to calculate inventory levels helps businesses avoid stock shortages and excess storage costs. Below is a breakdown of three key formulas to determine the right stock levels for your needs.
1. Calculating Minimum Inventory Levels
To determine the minimum inventory level, use the following formula:
Minimum inventory level = reorder point – (normal consumption × normal delivery time).
For instance, imagine you run a bookstore. Your reorder point for a popular novel is 500 copies, with a typical delivery time of 4 weeks. The normal sales rate for the book is 80 copies per week.
Minimum inventory level = 500 copies – (80 copies per week × 4 weeks) = 180 copies
In this case, the minimum inventory level would be 180 copies.
2. Calculating Maximum Inventory Levels
To determine the maximum inventory level, apply this formula:
Maximum inventory level = reorder point + reorder quantity – (minimum consumption × minimum lead time).
Using the bookstore example, your reorder point remains at 500 copies, and you typically reorder 1,200 copies at a time. The minimum sales rate is 60 copies per week, and the shortest lead time is 4 weeks.
Maximum inventory level = 500 copies + 1,200 copies – (60 copies × 4 weeks) = 1,460 copies
In this scenario, the maximum inventory level would be 1,460 copies.
3. Calculating Optimal Inventory Levels
Optimal inventory levels fall between the minimum and maximum stock thresholds. Determining this number is essential for maintaining the right balance of inventory. However, calculating optimal levels involves more than just using a formula or an inventory list.
It requires real-time inventory tracking and demand forecasts based on expected business growth. Since market conditions and demand fluctuate constantly, pinpointing the exact optimal stock level can be challenging.
While some businesses rely on spreadsheets for these calculations, this method is often time-consuming and prone to errors. A more efficient and accurate approach is to use inventory management software or an operations optimization tool.
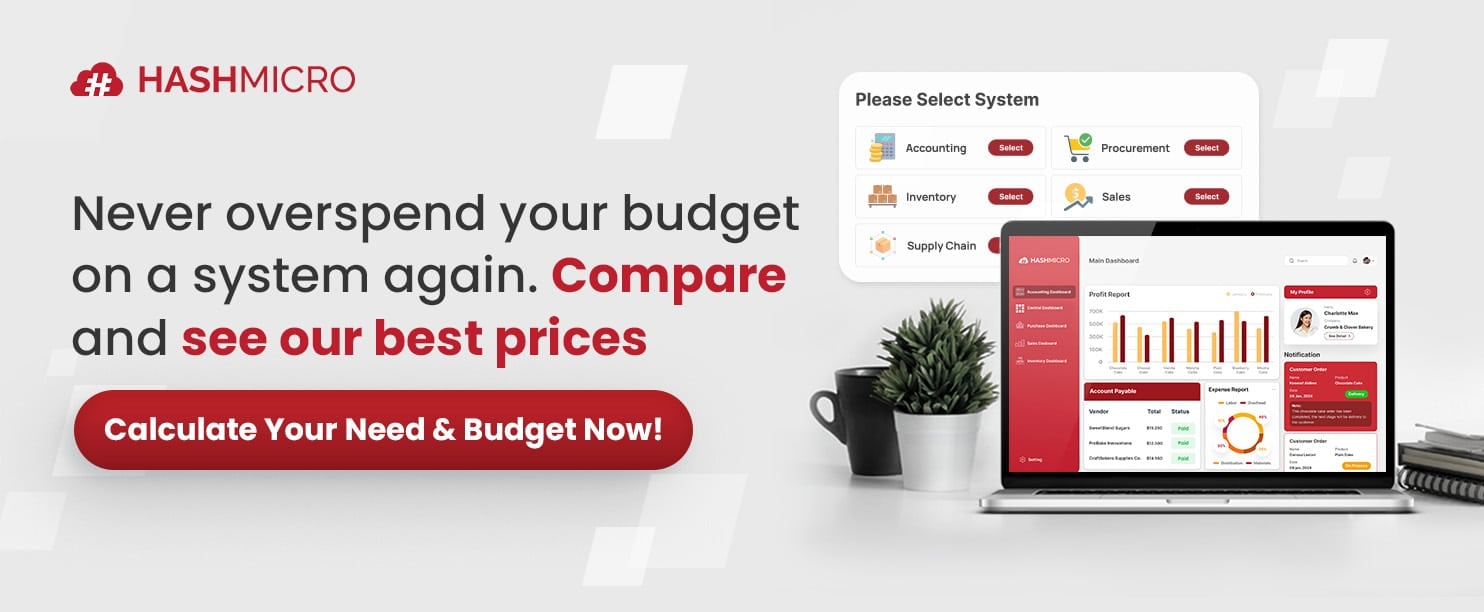
Best Practices to Optimize Inventory Levels
Here are some best practices that help businesses maintain optimal inventory levels in the supply chain:
1. Prioritize Inventory Organization
Certain products require more oversight due to high demand. To address this, inventory management methods categorize and rank items based on importance. Several techniques, such as ABC analysis or HML analysis, assist in this process.
For instance, ABC analysis follows this hierarchy:
- A: High-sales products requiring frequent reviews and regular reorders.
- B: Moderate-value products that need monthly reorders.
- C: Low-value products that require minimal reordering.
2. Define Reorder Points
Reorder points depend on sales velocity and restocking lead time. Setting these points prevents stockouts by ensuring timely replenishment. The most effective approach involves analyzing customer demand and supplier lead times.
3. Utilize Inventory Management Software
Inventory management software synchronizes SKUs, orders, and stock levels in real time. It also simplifies oversight across centralized inventory, fulfillment centers, and multiple sales channels.
For industries like retail, there are solutions that cater specifically to their requirements, such as retail inventory software. Make sure that you choose the right system for your business.
4. Conduct Regular Inventory Audits
To prevent stock from reaching dangerous levels, businesses must carry out inventory audits and make a comprehensive inventory report. Modern inventory software automates this process, enabling spot checks, cycle counts, and full annual assessments.
5. Implement Kitting and Bundling
Through kitting, individual products are packaged and sold as a single unit, increasing the average order value. This method offers a cost-effective solution for reducing shipping expenses and minimizing deadstock.
6. Leverage Hedge Inventories
Hedge inventory protects businesses from supply chain disruptions, such as strikes or material shortages. This strategy relies on forecasts and speculation, which may not always be accurate. However, it provides a safeguard when unexpected challenges arise.
7. Ensure Quick Response Capabilities
A rapid response approach benefits businesses with high turnover and low profit margins. When checkout data is promptly accessible to suppliers, they can adjust inventory levels efficiently, shorten lead times, and improve forecasting accuracy.
Simplify Inventory Level Management with HashMicro
HashMicro Inventory Management Software delivers a powerful and precise solution for managing inventory levels across businesses of all sizes. This cloud-based system caters to various industries, including wholesale, retail, food and beverage, construction, manufacturing, and more.
For those interested in exploring its capabilities, HashMicro offers a free demo with zero commitment; no subscription required, and access is available anytime.
Beyond inventory control, HashMicro connects with other business applications to create a powerful, all-in-one system. It’s very useful, isn’t it? Here are HashMicro’s features that can help with managing inventory levels:
- Stock Forecasting: Predicts inventory needs and automates reordering based on stock consumption trends.
- Stock Optimizer: Balances stock across branches to prevent overstocking and stockouts.
- Inventory Reports – Tracks stock levels, movements, aging, turnover, and fast vs. slow-moving items for better decision-making.
- Expiry Tracking – Monitors product expiration dates with automated notifications to reduce waste.
- Putaway Strategy – Organizes stock placement based on product type, category, or warehouse capacity to improve space utilization.
Conclusion
Keeping the right inventory levels is key to avoiding stockouts, cutting unnecessary costs, and keeping operations smooth. With a solid strategy, businesses can maintain the perfect balance between demand and supply without wasting resources.
With HashMicro Inventory Management Software, businesses can stay ahead with smart forecasting and automated reordering. Real-time tracking and in-depth reports provide clear insights, so you can prevent under- or overstock, as well as adjust reordering quickly.
Why rely on guesswork when you can have accuracy and control? HashMicro’s all-in-one system simplifies inventory management and keeps your business running smoothly.
Try the free demo today and see how this system makes managing stocks and warehouses more effective!
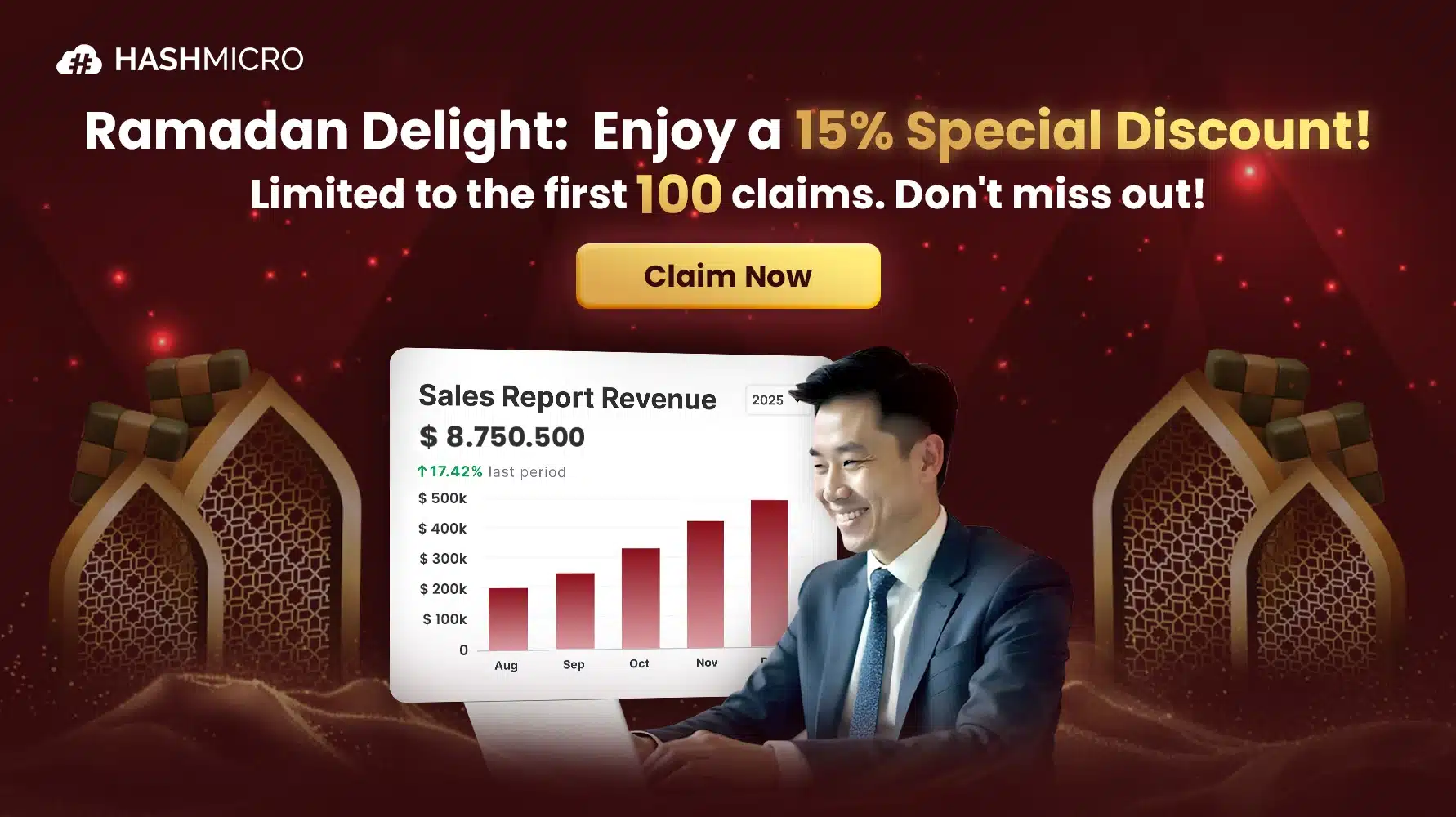
Frequently Asked Questions on Inventory Levels
-
How do seasonal trends affect inventory levels?
Seasonal trends can significantly impact inventory levels, as demand for certain products fluctuates during specific times of the year. Businesses must anticipate these changes and adjust their stock accordingly to meet customer needs without overstocking.
-
What is the Economic Order Quantity (EOQ) model, and how does it relate to inventory levels?
The EOQ model helps determine the optimal order quantity that minimizes total inventory costs, including ordering and holding expenses. By calculating EOQ, businesses can maintain appropriate inventory levels and reduce unnecessary costs.
-
What role does technology play in managing inventory levels?
Technological solutions, such as inventory management software and automation, enable real-time tracking, accurate demand forecasting, and efficient stock control, leading to optimized inventory levels and improved operational efficiency.
-
How does lead time variability influence inventory levels?
Variations in lead time—the period between placing and receiving an order—can cause stock shortages or surpluses. To mitigate this, businesses often maintain safety stock to buffer against unpredictable lead times.