In today’s competitive business landscape, managing inventory efficiently is critical for managers striving to optimize operations and reduce costs. Implementing Just-in-Time (JIT) inventory management offers a solution by aligning inventory levels closely with actual demand, thereby minimizing waste and enhancing profitability.
However, the transition to a JIT system presents several challenges that managers must address to ensure success. These include establishing reliable supplier relationships, accurately forecasting demand, and maintaining flexibility to adapt to unforeseen disruptions in the supply chain.
For instance, a global dress distributor successfully integrated AI-powered inventory management, resulting in a 40% reduction in overstock. This case highlights the potential benefits of adopting advanced technologies to enhance JIT implementation.
To explore how JIT inventory management can transform your business and discover software solutions that facilitate its adoption, continue reading this comprehensive guide.
Table of Content
Content Lists
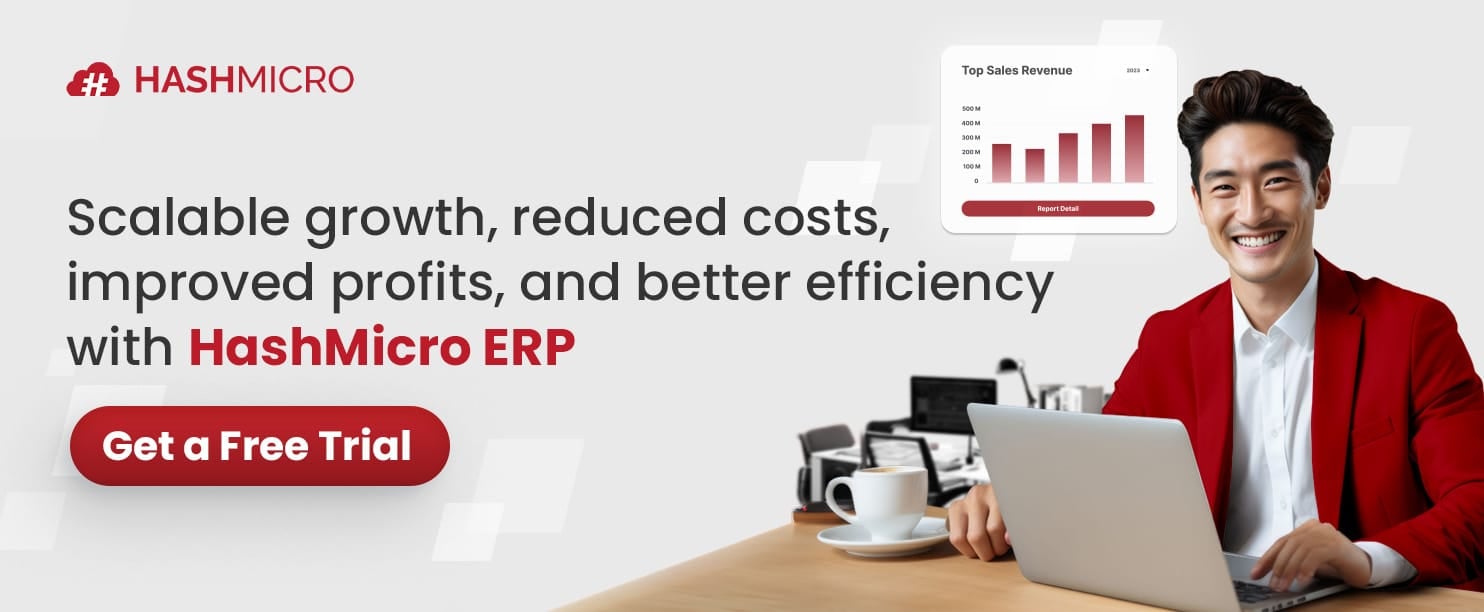
Key Takeaways
|
What is Just-in-Time (JIT) Inventory Management?
Just-in-Time (JIT) inventory management is a strategic approach that helps businesses optimize stock levels by receiving materials only when needed for production or sales. This method ensures companies maintain minimum inventory while meeting demand, reducing storage costs, and eliminating inefficiencies such as overstocking or unnecessary capital investment in idle goods.
By aligning JIT inventory systems with real-time customer demand and supply chain optimization, businesses can enhance operational efficiency and prevent wastage. This strategy requires close collaboration with reliable suppliers to ensure raw materials arrive precisely when production begins, avoiding costly delays while maintaining a seamless JIT supply chain.
The just-in-time inventory system is widely used in manufacturing, retail, and food services to improve productivity while reducing unnecessary stockpiling. With an accurate demand forecasting approach, businesses can leverage just-in-time inventory management to remain agile, lower expenses, and focus on growth rather than inventory holding concerns.
The Evolution and History of Just-in-Time Inventory
The concept of JIT inventory management emerged in post-World War II Japan as a strategic response to resource scarcity. Spearheaded by Taiichi Ohno at Toyota, the just-in-time inventory system was designed to eliminate waste, improve efficiency, and ensure that materials arrived precisely when needed for production.
By the 1970s and 1980s, businesses in the United States began adopting just-in-time inventory management, expanding its use beyond the automotive sector into various industries. This shift led to the evolution of JIT supply chain optimization, integrating lean manufacturing principles and advanced data analytics to enhance production efficiency.
Today, just-in-time inventory is widely used in manufacturing, retail, healthcare, and other industries that require streamlined operations and cost-effective inventory control. With the rise of automation and cloud-based solutions, businesses continue to refine JIT inventory systems, making supply chains more responsive, agile, and competitive in global markets.
Why Use JIT Inventory Management?
Many businesses adopt JIT inventory management as a cost-effective strategy to minimize stock investment while maximizing efficiency. By reducing the need for excessive storage, companies can optimize cash flow, lower operational costs, and focus on strategic growth rather than managing excess inventory.
A well-executed just-in-time inventory system enhances business agility by improving supply chain responsiveness and reducing waste. With JIT supply chain optimization, businesses can maintain lean operations, ensuring products are available exactly when needed while preventing overproduction and inventory obsolescence.
Successful just-in-time inventory management relies on real-time data and ERP systems to track stock turnover, shipments, and purchasing trends. By leveraging digital tools, businesses can streamline operations, improve workforce efficiency, and empower teams to make data-driven decisions for better profitability.
Benefits of JIT Inventory Management
Implementing JIT inventory management offers businesses numerous advantages, from cost savings to improved operational efficiency. By optimizing stock levels and streamlining supply chain processes, companies can reduce waste, enhance productivity, and maximize return on investment.
Below are the key benefits of adopting a just-in-time inventory system in modern business operations:
- Eliminates Excess Inventory & Waste – Businesses only stock what’s needed, preventing overordering, reducing material waste, and supporting a lean supply chain.
- Prevents Obsolete and Dead Stock – Maintaining low inventory levels ensures stock moves quickly, avoiding financial losses from expired or outdated products.
- Reduces Defective Product Loss – Lower production volumes make identifying and fixing defects easier, minimizing waste and improving product quality.
- Enhances Supply Chain Responsiveness – Frequent, smaller deliveries ensure raw materials arrive quickly, reducing storage needs and optimizing working capital.
- Improves Supplier Collaboration & Delivery Reliability – Close supplier relationships ensure timely deliveries and minimize risks of production delays.
- Boosts Operational Productivity – JIT reduces unnecessary stock handling, prevents bottlenecks, and accelerates order fulfillment, leading to faster turnaround times.
- Optimizes Resource Allocation – With less stock to manage, businesses can reallocate workforce efforts, lower warehousing costs, and improve overall efficiency.
By leveraging JIT inventory management, businesses can transform their supply chain operations, enhance efficiency, and achieve significant cost savings. Investing in ERP solutions further strengthens just-in-time inventory processes by ensuring real-time coordination between suppliers, warehouses, and production lines.
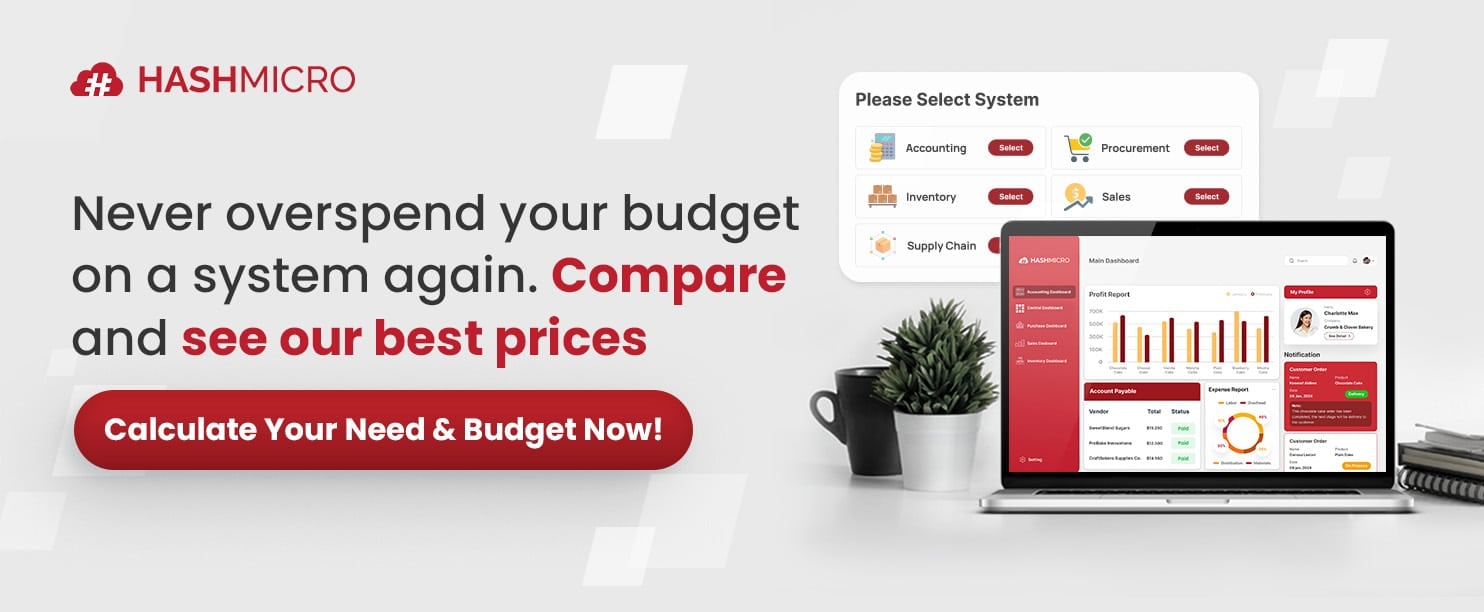
How Does Just-in-Time Inventory Work?
JIT inventory management ensures that stock arrives exactly when needed for production or sales, reducing unnecessary storage and improving cash flow. This just-in-time inventory system helps businesses minimize excess stock while maintaining efficiency and responsiveness to market demands.
A key component of JIT inventory management is aligning procurement with production schedules to avoid overstocking or shortages. By implementing JIT supply chain optimization, businesses can collaborate with reliable suppliers for timely deliveries, reducing risks like inventory waste and supply chain disruptions.
With just-in-time inventory, companies optimize their resources by eliminating inefficiencies in manufacturing and warehousing. This approach enables businesses to focus on productivity and cost savings, ensuring they meet customer demand without holding excessive stock.
Businesses can automate demand tracking and streamline procurement processes by leveraging digital solutions such as cloud-based inventory software. A well-executed JIT inventory system enhances operational agility, allowing companies to reduce waste, lower costs, and maintain a competitive edge.
Pros and Cons of JIT Inventory Management
Adopting JIT inventory management provides businesses with multiple advantages, from cost savings to enhanced operational efficiency. However, this strategy also presents challenges that require careful planning and strong supplier relationships.
Below are the key pros and cons of just-in-time inventory management to help businesses determine if this system is the right fit.
Pros of JIT Inventory Management
- Reduced inventory costs: By aligning stock levels with real demand, JIT inventory management reduces the capital tied up in unsold goods. This frees up cash flow, allowing businesses to invest in other areas like innovation and market expansion.
- Enhanced efficiency and productivity: With a just-in-time inventory system, businesses eliminate unnecessary storage and handling processes, leading to streamlined workflows. This efficiency boost minimizes waste, optimizes production schedules, and enhances productivity.
- Improved quality control: A responsive JIT inventory example includes immediate defect identification, allowing businesses to address quality issues early. This results in fewer defective products, higher customer satisfaction, and stronger brand reputation.
- Higher inventory turnover rates: A well-implemented just-in-time inventory approach ensures that products move quickly from suppliers to customers. This prevents dead stock, improves sales cycles, and reduces the risk of obsolete inventory.
- Lower storage and space requirements: With minimal stock on hand, businesses reduce warehouse costs and optimize available space for more critical functions. JIT supply chain optimization further enhances space utilization by ensuring frequent but controlled stock replenishment.
- Faster adaptation to market changes: Companies using just-in-time inventory management can quickly adjust production levels in response to demand fluctuations. This flexibility allows businesses to remain competitive, especially in industries with fast-changing consumer preferences.
Cons of JIT Inventory Management
- Supply chain disruption risks: JIT inventory systems depend on precise supplier deliveries, making businesses vulnerable to disruptions. Delays caused by supplier issues, transportation failures, or global supply chain crises can halt production and lead to financial losses.
- High dependence on suppliers: Strong supplier relationships are crucial for JIT inventory management, but reliance on external vendors can be risky. Businesses may struggle to maintain operations if a supplier fails to meet delivery schedules or quality standards.
- Forecasting challenges: Since just-in-time inventory requires accurate demand forecasting, miscalculations can lead to stock shortages or overreliance on emergency procurement. Businesses must invest in data-driven forecasting tools to minimize these risks.
- Increased pressure on workforce: Implementing a JIT inventory system demands strict coordination between teams, requiring well-trained staff and efficient communication. Any misalignment in production, procurement, or logistics can disrupt the supply chain.
- Vulnerability to price fluctuations: Since businesses order inventory as needed, they may be affected by sudden price increases in raw materials. Unlike bulk purchasing, JIT inventory management does not allow companies to lock in lower prices for long-term savings.
- High implementation costs: Transitioning to just-in-time inventory management involves significant investment in training, supplier integration, and advanced JIT supply chain optimization technologies. Businesses must be prepared for an initial learning curve and operational adjustments.
While JIT inventory management offers cost savings, efficiency, and flexibility, it requires strong supply chain coordination and reliable forecasting. Companies that effectively manage these challenges can benefit from streamlined operations, reduced waste, and improved profitability.
Industries That Benefit from JIT Inventory Systems
JIT inventory management is widely used across industries that require cost-efficient operations, reduced storage needs, and better responsiveness to demand fluctuations. Businesses adopt just-in-time inventory systems from manufacturing to retail to optimize their supply chains and improve cash flow.
- Automotive industry: The JIT inventory system originated in the automotive sector, where manufacturers need to reduce storage costs and enhance production efficiency. Car companies worldwide still rely on just-in-time inventory to ensure parts arrive precisely when needed, reducing excess stock and optimizing manufacturing capacity.
- Retail and big box stores: Retail businesses, especially large chains like supermarkets and department stores, use JIT inventory management to stock goods based on demand forecasts. Seasonal products such as holiday decorations or fashion trends arrive just in time to maximize sales while preventing overstock.
- Manufacturing and aerospace: Manufacturers leverage just-in-time inventory to improve production flow, minimize waste, and accelerate delivery times. Aerospace companies benefit significantly from JIT supply chain optimization by reducing costly delays and managing space constraints efficiently.
- Healthcare and pharmaceuticals: Hospitals and healthcare providers use JIT inventory systems to maintain essential medical supplies without overstocking costly or perishable items. This approach helps control expenses, ensure product freshness, and improve inventory accuracy in critical healthcare operations.
- Food and beverage industry: Fast-food chains and restaurants apply just-in-time inventory management to order fresh ingredients only when needed, minimizing spoilage and waste. This strategy allows food businesses to maintain quality, reduce excess stock, and streamline their supply chain.
- Publishing and on-demand printing: The publishing industry benefits from just-in-time inventory through on-demand printing, where books are produced only when an order is placed. This reduces unnecessary printing, storage, and returns, making it a cost-effective solution for independent publishers and print-on-demand businesses.
From automotive manufacturing to healthcare and retail, JIT inventory management enables businesses to operate efficiently while reducing waste and costs. By adopting a just-in-time inventory system, companies can enhance flexibility, improve supply chain responsiveness, and remain competitive in fast-paced industries.
Critical Considerations Before Adopting JIT Inventory
Before transitioning to JIT inventory management, businesses must evaluate their operational readiness, supply chain resilience, and ability to adapt to a lean inventory system. Below are key questions to assess whether your company is prepared for a just-in-time inventory system:
- Can my products be manufactured or supplied quickly enough? A successful JIT inventory system requires fast production cycles and reliable suppliers who can deliver materials on demand. If your supply chain cannot meet short turnaround times, stock shortages may disrupt operations.
- Is my demand forecasting accurate? Just-in-time inventory management relies on precise demand predictions to avoid overstocking or shortages. Investing in data-driven forecasting tools ensures supply levels align with market demand.
- Is my supply chain flexible enough to handle disruptions? Unpredictable factors like supplier delays or natural disasters can impact JIT inventory operations. Businesses must have contingency plans and alternative suppliers to maintain stability during disruptions.
- Are my suppliers reliable and consistent? Since just-in-time inventory minimizes stock levels, businesses must work with suppliers that guarantee timely and accurate deliveries. Establishing strong partnerships and long-term agreements helps reduce supply chain risks.
- Is my workforce trained and ready for JIT? Implementing JIT supply chain optimization requires a skilled and adaptable workforce. Employees should be trained in lean inventory processes and cross-functional roles to maintain efficiency.
- Do I have the right technology to support JIT? Advanced inventory management software is essential for tracking stock levels, automating orders, and managing supplier coordination. Investing in digital tools enhances just-in-time inventory management efficiency and accuracy.
Evaluating these factors will help businesses determine whether JIT inventory management is a suitable strategy for their operations. With the right preparation, just-in-time inventory systems can optimize resources, reduce costs, and improve supply chain agility.
How HashMicro’s Inventory Management Software Enhances JIT Management Efficiency
HashMicro offers a robust inventory management software designed to optimize Just-in-Time (JIT) inventory management, ensuring businesses maintain lean inventory levels while meeting demand efficiently. With automated tracking, real-time updates, and seamless supply chain integration, companies can enhance JIT supply chain optimization and reduce operational costs.
Experience the efficiency of HashMicro’s JIT inventory system, where automation eliminates excess stock, enhances visibility, and ensures real-time updates to prevent shortages. Try a free demo today and see how seamless JIT inventory management can optimize your supply chain and boost profitability!
Why Choose HashMicro? Unlike traditional inventory systems, HashMicro’s software is designed to support JIT inventory principles, ensuring that businesses order and receive stock precisely when needed. The system helps companies to eliminate overstocking, streamline procurement, and enhance production efficiency.
Below are some of the key features of HashMicro’s inventory management software for JIT inventory management:
- RFID warehouse rack stock automation: The system utilizes RFID technology to automatically track stock movement in and out of warehouse racks, ensuring real-time updates. This minimizes manual tracking errors, improves inventory accuracy, and enhances operational efficiency.
- Fast-moving and slow-moving stock analysis: The system analyzes stock movement patterns to identify which items sell quickly and which remain in storage longer. This helps businesses optimize stock levels, reduce overstocking, and prevent unnecessary inventory holding costs.
- Stock forecasting & run rate reordering rules: The system predicts future stock needs using historical sales data and sets automatic reordering thresholds. This ensures balanced inventory levels, prevents shortages, and maintains seamless business operations.
- Stock reservations & reporting: The system allows businesses to reserve inventory in advance while generating detailed stock and inventory reports. This ensures stock availability when needed, streamlining workflows and preventing operational disruptions.
- Quality control management: Integrated quality control processes inspect and verify stock before it becomes available for sale or use. This ensures that only high-quality products remain in inventory, reducing defects and enhancing customer satisfaction.
- Product expiry & warranty tracking with reminders: The system tracks product expiration dates and warranty periods, sending automated alerts before they lapse. This prevents financial losses from expired or outdated inventory and ensures compliance with quality standards.
- Consignment stock management: Businesses can monitor supplier-provided inventory in real time by automating consignment stock tracking. This guarantees accurate stock levels, timely replenishment, and improved supplier coordination.
- Stock take and inventory adjustment management: The system automates stock-taking and inventory adjustments by regularly updating stock records. This reduces discrepancies, improves stock accuracy, and streamlines inventory audits.
- Integrated barcode & QR code support: Barcode and QR code scanning automate stock entry and retrieval, enabling quick and error-free inventory management. This minimizes human errors, accelerates stock processing, and improves overall accuracy.
- Material request management: The system automates requests by tracking demand and ensuring timely stock availability. This prevents delays, optimizes resource allocation, and enhances supply chain efficiency.
With JIT inventory management software, businesses can optimize operations, improve cash flow, and enhance customer satisfaction. HashMicro’s JIT inventory system helps companies reduce waste, maintain lean stock levels, and operate with greater efficiency in today’s competitive market.
Conclusion
Just-in-Time (JIT) inventory management enables businesses to minimize excess stock, reduce costs, and improve efficiency by ensuring materials arrive exactly when needed. With inventory management software, companies can automate stock tracking, enhance demand forecasting, and maintain a responsive supply chain.
As a leading solution, HashMicro’s Inventory Management Software embeds JIT capabilities to help businesses optimize inventory control and enhance overall efficiency. It’s a comprehensive feature enables companies to streamline supply chain operations while minimizing excess inventory.
Take the next step towards smarter inventory management by exploring HashMicro’s JIT-powered solutions. Request a free demo today and discover how automation and precision-driven inventory control can transform your business operations.
FAQ About JIT Inventory
-
What is the difference between JIT and EOQ?
The Just-in-Time (JIT) inventory system focuses on minimizing stock levels by ordering only what is needed, precisely when required, reducing holding costs. In contrast, the Economic Order Quantity (EOQ) model determines the optimal order quantity that minimizes total inventory costs, including ordering and holding expenses.
A key difference lies in demand levels—JIT is more cost-effective for low-demand items, as it prevents excess inventory, while EOQ is preferable for high-demand products, as bulk purchasing reduces per-unit costs. Businesses must assess their supply chain needs and operational efficiency to determine which model best suits their inventory strategy.
-
What is the basic idea of a JIT inventory system?
JIT operates on the principle of producing goods only when they are required, rather than manufacturing in advance and storing excess inventory. This approach helps businesses lower inventory costs, enhance cash flow, and maximize warehouse space utilization.
-
What are the four types of inventory management systems?
The four primary inventory management methods include Just-in-Time (JIT), Materials Requirement Planning (MRP), Economic Order Quantity (EOQ), and Days Sales of Inventory (DSI). Each approach is suited to specific business needs, with effectiveness varying depending on the industry and operational model.