Have you ever scrutinized your inventory and pondered how much capital is immobilized in unsold stock? This prevalent issue often escapes attention until it significantly impacts a company’s financial health.
Implementing lean inventory management presents challenges, including resistance to change, inadequate data accuracy, and technological limitations. These obstacles can hinder the successful adoption of lean practices within an organization.
A study on manufacturing firms in Northern Malaysia found that lean practices, including efficient inventory management, improve environmental performance by reducing waste and resource use. This proves that inventory strategies reduce costs and promote sustainability, making them vital for long-term efficiency.
Continue reading this comprehensive guide to learn more about lean inventory management and discover software solutions to streamline your operations.
Table of Content
Content Lists
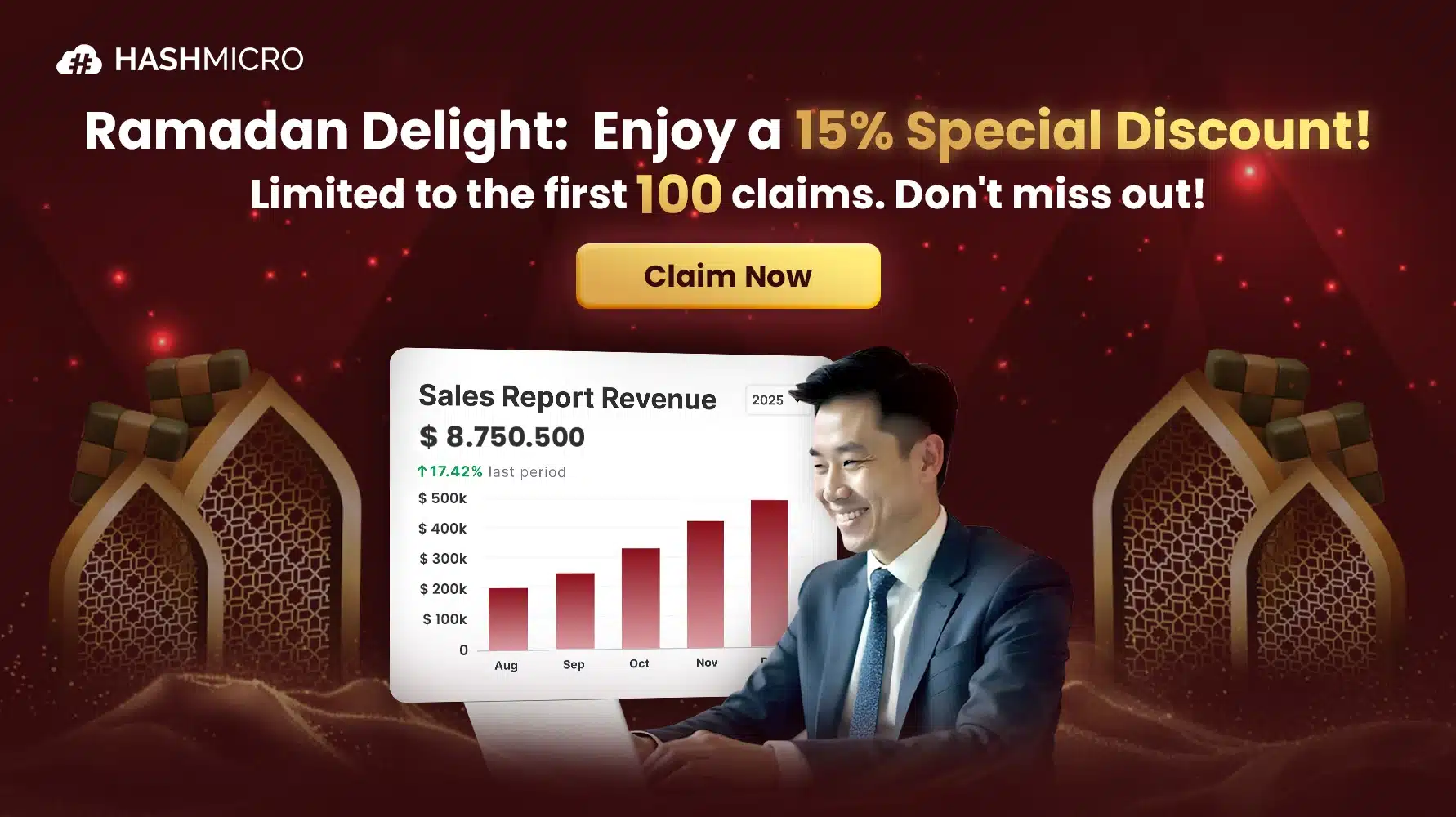
Key Takeaways
|
What is Lean Inventory Management?
Lean inventory management eliminates waste and inefficiencies by maintaining only the necessary stock at every production stage. By applying Just-in-Time (JIT) and inventory aging analysis, businesses can optimize stock levels, reduce carrying costs, and prevent overproduction.
More than just minimizing excess inventory, this approach enhances inventory flow management by identifying bottlenecks and implementing FIFO method to reduce spoilage and obsolescence. Lean techniques like Kaizen, Kanban, and Six Sigma ensure continuous supply chain improvements, making businesses more agile and responsive to demand changes.
Lean inventory replaces demand forecasting with production based on actual customer needs. This reduces storage costs and maximizes inventory value by eliminating waste in labor, materials, and time through continuous improvement strategies.
Businesses implementing inventory principles experience lower costs, better product quality, and higher customer satisfaction. Whether in retail, manufacturing, or healthcare, lean strategies drive efficiency, streamline operations, and enhance long-term profitability through optimized cloud inventory management software.
5 Key Principles of Lean Inventory Management
Implementing lean inventory practices requires a structured approach to eliminating waste, optimizing efficiency, and maintaining inventory flow management. Below are the five core principles of inventory management and their contribution to a more agile and efficient process.
1. Value: Delivering what customers need
Understanding lean inventory meaning starts with defining value from the customer’s perspective. Businesses should determine what products customers truly need and ensure their inventory aligns with actual demand.
This principle reduces overstocking and prevents businesses from holding excess or obsolete inventory, allowing for an optimized inventory system that enhances operational efficiency. For example, an efficient inventory management strategy ensures that high-demand products are always available, minimizing delays and improving customer satisfaction.
2. Value stream: Optimizing the inventory lifecycle
Mapping the value stream involves analyzing every step in the inventory process, from sourcing raw materials to delivering the final product. This principle helps businesses identify inefficiencies and remove non-essential steps slowing inventory movement.
By improving inventory flow management, companies can streamline operations, reduce storage costs, and eliminate waste, ultimately enhancing supply chain responsiveness. A lean inventory example is adopting automation tools that provide real-time tracking, ensuring smoother inventory transitions and reducing lead times.
3. Flow: Ensuring seamless inventory movement
The flow principle ensures that inventory moves smoothly through each stage of the supply chain without unnecessary bottlenecks. An efficient lean inventory strategy requires businesses to manage stock levels dynamically, reducing downtime and ensuring a steady production cycle.
Utilizing inventory flow management techniques like demand forecasting and MRP (Materials Requirements Planning) helps businesses determine what is needed, how much is required, and when stock should be replenished. By maintaining a continuous flow, companies can improve efficiency, reduce excess inventory, and prevent costly production delays.
4. Pull: Stocking only what is needed
The pull principle ensures that inventory is replenished only when actual demand exists rather than relying on inventory forecasting. This core concept in inventory management helps businesses minimize overproduction and holding costs.
By using a pull-based inventory flow management system like Just-in-Time (JIT), companies can avoid waste and ensure they only stock items that customers actively purchase. For example, a retail business applying lean inventory would replenish stock based on real-time sales data rather than assumptions, reducing dead stock and improving cash flow.
5. Perfection: Continuous improvement for optimal performance
Striving for perfection means continuously improving inventory processes to eliminate inefficiencies and enhance overall performance. Businesses should regularly analyze their lean inventory strategies, applying methodologies like Six Sigma and Total Quality Management (TQM) to refine their optimized inventory system.
Regular ABC analysis and demand forecasting helps businesses adjust stock levels proactively, preventing costly inventory mismanagement. By constantly optimizing workflows, companies can achieve greater flexibility, reduce costs, and maximize the long-term benefits of inventory.
By following these five lean inventory management principles, businesses can transform their inventory processes into a highly responsive and cost-effective system. Whether in manufacturing, retail, or logistics, adopting a lean inventory example that aligns with customer demand ensures greater efficiency, reduced waste, and improved profitability.
7 Types of Waste in Lean Inventory
Waste is one of the biggest obstacles to efficient inventory management, leading to unnecessary costs, delays, and inefficiencies. In inventory management, businesses strive to eliminate waste to improve productivity, reduce expenses, and enhance overall performance.
Below are the seven types of waste that commonly impact inventory systems, along with strategies to mitigate them:
1. Overproduction: Producing more than necessary
Overproduction occurs when businesses manufacture products or components that are not immediately needed, leading to excess inventory. This results in increased storage costs, inefficient resource use, and, in some cases, dead stock that never gets sold.
A core lean inventory example is Just-in-Time (JIT) production, where items are only produced based on real-time demand. By implementing demand forecasting and planning, businesses can align production with customer needs, reducing unnecessary stock buildup.
2. Waiting: Downtime that slows inventory flow
Waiting waste occurs when inventory sits idle due to production delays, supply chain bottlenecks, or inefficient order processing. This ties up valuable capital and increases lead times, negatively impacting inventory flow management.
Businesses can minimize this waste by automating inventory tracking, improving supplier coordination, and streamlining order fulfillment processes. An optimized inventory system ensures that stock moves seamlessly from one stage to the next, preventing unnecessary delays.
3. Excess Inventory: Holding more stock than needed
Storing excess inventory leads to high carrying costs, increased risk of obsolescence, and reduced liquidity. When businesses hold too much stock, they tie up funds that could be used elsewhere, impacting cash flow and financial stability.
A well-executed lean inventory strategy focuses on efficient inventory management, ensuring that businesses only maintain necessary stock levels. Using inventory optimization tools, companies can track demand patterns and prevent overstocking.
4. Transportation: Unnecessary product movement
Unnecessary movement of goods within a warehouse or between locations adds no real value and increases costs. This can lead to higher fuel expenses, damaged goods, and inefficiencies in the inventory flow management process.
Implementing warehouse layout optimization, automated picking systems, and direct shipping methods can significantly reduce transportation waste. Cross-docking, where products are moved directly from inbound shipments to outbound deliveries, minimizes handling and is a prime lean inventory example.
5. Overprocessing: Performing unnecessary work
Overprocessing waste happens when businesses add extra steps, materials, or labor that do not improve product quality or value. Examples include excessive packaging, redundant data entry, or inefficient quality control processes.
Companies can enhance efficient inventory management by standardizing workflows and eliminating non-essential tasks. Lean methodologies like Six Sigma help identify unnecessary processes and streamline operations for better productivity.
6. Motion: Inefficient movements that reduce productivity
Wasted motion occurs when employees or machines perform unnecessary actions, such as searching for misplaced inventory or frequently adjusting equipment. This reduces efficiency and increases wear and tear on machinery, leading to higher maintenance costs.
Businesses can address this by implementing clear warehouse organization systems, ergonomic workstations, and automated picking technology. An optimized inventory system ensures that inventory locations are structured for quick and easy access.
7. Defects: Errors that lead to rework and losses
Defective products result in costly rework, lost sales, and potential damage to a company’s reputation. Poor quality control can lead to customer dissatisfaction and increased waste in both materials and labor.
Lean inventory practices focus on proactive quality management, ensuring defects are minimized through continuous process improvement. A key benefit of lean inventory is reducing product failures by incorporating regular inspections, supplier quality checks, and data-driven decision-making.
5S Framework
The 5S framework is a structured approach to workplace organization that enhances efficient inventory management by eliminating waste and improving productivity. Businesses can streamline operations and maintain an optimized inventory system by following five essential steps—sort, straighten, shine, standardize, and sustain.
- Sort: The first step in lean inventory management is sorting through all items in a workspace and removing anything unnecessary. This helps businesses reduce clutter, improve accessibility, and prevent overstocking, ensuring that only essential materials are available when needed.
- Straighten: Effectively organizing work areas allows employees to locate tools, materials, and inventory quickly, reducing wasted time and motion. A well-structured inventory flow management system ensures a seamless workflow, improving productivity and minimizing operational bottlenecks.
- Shine: Regular cleaning of work areas prevents safety hazards and keeps inventory processes running smoothly without disruption. This step enhances efficient inventory management, as a well-maintained environment reduces the risk of misplaced items and production delays.
- Standardize: Creating standardized procedures ensures consistency in task performance, reducing confusion and errors in inventory handling. Businesses develop an optimized inventory system that fosters accuracy and efficiency across all departments by setting clear operational guidelines.
- Sustain: Sustaining the 5S framework means regularly evaluating and improving processes to maintain long-term efficiency. Companies that integrate lean inventory principles into their daily operations benefit from ongoing enhancements in productivity, cost savings, and overall performance.
Lean Inventory Management Attributes
Implementing a lean inventory system requires a strategic approach focusing on efficiency, waste reduction, and collaboration. By integrating these six essential attributes, businesses can enhance inventory flow management, reduce costs, and improve overall operational performance.
Below are the key characteristics that define inventory management and contribute to a highly optimized inventory system:
- Demand planning: Effective lean inventory management relies on accurate demand forecasting to ensure stock levels align with customer needs. By analyzing historical data, market trends, and upcoming events, businesses can maintain enough inventory to fulfill demand without overstocking.
- Cross-enterprise collaboration: A successful lean inventory example involves seamless collaboration across departments, integrating real-time data from ERP, CRM, and sales systems. This ensures all teams can access the latest inventory insights, allowing for better coordination and responsiveness to market changes.
- Cost and waste reduction: The benefit of lean inventory is its ability to minimize waste while maintaining high customer service standards. Companies achieve this by optimizing stock levels, reducing excess materials, and streamlining operations to eliminate unnecessary costs without affecting product quality.
- Process standardization: Standardizing workflows helps businesses improve efficient inventory management by reducing errors, increasing consistency, and simplifying training procedures. A well-defined inventory process enhances repeatability and creates opportunities for automation, ensuring a smoother operation.
- Industry standardization: While internal standardization improves efficiency, companies must align with industry norms to maintain competitiveness. For instance, an automotive company may use standard tire sizes but customize rim designs to differentiate its products while maintaining optimized inventory system processes.
- Cultural change: A strong lean inventory extends beyond operations—it fosters a culture of continuous improvement where employees take ownership of processes. Businesses that empower their teams to contribute to lean initiatives see higher engagement, improved efficiency, and long-term sustainability.
By adopting these lean inventory attributes, businesses can create a more optimized inventory system that reduces waste, enhances efficiency, and ensures long-term profitability. When implemented correctly, lean inventory management drives operational excellence while keeping businesses agile and customer-focused.
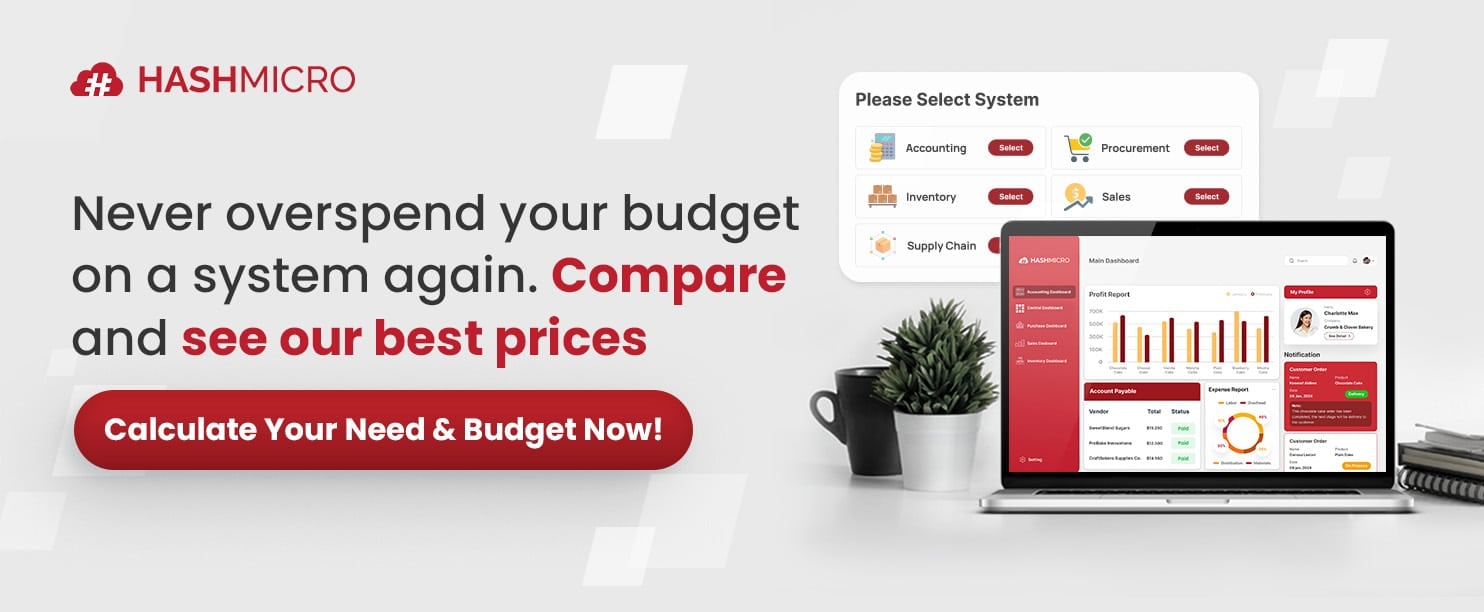
Benefits of Lean Inventory Management
Implementing lean inventory management helps businesses reduce costs, enhance efficiency, and improve overall operational performance. By eliminating waste and optimizing inventory flow management, companies can create a streamlined and optimized inventory system that maximizes profitability.
Below are the key advantages of adopting a lean inventory approach.
1. Maximized profits
One of the greatest benefits of lean inventory is its ability to lower storage costs and minimize losses from obsolescence, spoilage, and dead stock. By only stocking what is necessary, businesses free up capital that can be reinvested into growth and innovation.
Additionally, reducing stock-outs ensures businesses consistently meet customer demands, preventing lost sales opportunities. A well-implemented lean inventory example increases profit margins by balancing supply and demand efficiently.
2. Waste reduction
A lean inventory meaning extends beyond stock reduction—it focuses on eliminating wasted motion, overproduction, and excess handling of materials. By moving inventory only in response to customer orders, businesses reduce unnecessary transportation and minimize product damage.
This also decreases the risk of workplace injuries caused by excessive stock movement. Implementing efficient inventory management ensures that resources are utilized effectively, reducing operational waste.
3. Increased product quality
A lean inventory system prioritizes quality by decreasing defects, rework, and returns, leading to a more reliable product line. With standardized processes and real-time quality control, businesses can identify and correct defects early in production.
This leads to lower return costs and increased customer satisfaction due to consistent product excellence. High-quality inventory strengthens brand reputation, fostering customer loyalty and repeat purchases.
4. Shorter lead times
Reducing production and inventory bottlenecks ensures that products reach customers faster, improving the buying experience. A lean inventory approach allows businesses to respond quickly to shifts in market demand, avoiding overproduction or stock shortages.
Shorter lead times give companies a competitive edge by improving service levels and reducing unnecessary delays. An optimized inventory system helps businesses stay agile in dynamic markets.
5. Stock turnover
A high stock turnover rate prevents products from sitting idle for extended periods, reducing the risk of obsolescence or spoilage. Inventory flow management strategies ensure that products are replenished based on demand, keeping stock levels lean and efficient.
Faster turnover frees up warehouse space, lowers carrying costs, and reduces the risk of outdated inventory. A strong lean inventory example is real-time inventory tracking to maintain an ideal balance of supply and demand.
6. Eco-friendly and sustainable business practices
Businesses that adopt lean inventory management eliminate unnecessary waste, contributing to a more sustainable and environmentally friendly supply chain. Reducing overproduction, minimizing waste, and streamlining logistics help lower carbon footprints and resource consumption.
Many companies implement digital inventory systems to go paperless, reducing excess documentation and improving efficiency. Sustainable inventory practices also align with consumer preferences, boosting brand reputation among eco-conscious customers.
7. Boosts employee morale
Employees thrive in a well-structured environment where workflows are clear and responsibilities are well-defined. Lean inventory management encourages teamwork, continuous improvement, and engagement by empowering employees to contribute to efficiency improvements.
Clear, standardized processes reduce frustration caused by disorganization and inefficiencies, increasing job satisfaction. A strong lean inventory fosters a work culture that values productivity, innovation, and long-term success.
Limitations of Lean Inventory Management
While lean inventory management offers numerous benefits, it also comes with certain challenges that businesses must consider. Implementing a lean inventory example requires significant effort, and some industries may find its limitations outweigh the benefit of inventory.
Below are some key challenges companies face when adopting a lean inventory approach.
1. It’s time- and resource-intensive
Building an optimized inventory system with lean principles requires a considerable investment in training, technology, and process optimization. Businesses must allocate time and financial resources to implement automation tools, train employees, and restructure supply chain workflows.
2. Lack of customization
Since lean inventory meaning revolves around standardized processes and efficiency, it can limit a company’s ability to offer customized or highly specialized products. Industries that thrive on personalization, such as luxury goods or bespoke manufacturing, may struggle to implement strict lean principles without sacrificing product differentiation.
3. Team onboarding and cultural shifts
Successful lean inventory management requires full commitment from employees, managers, and executives to ensure a smooth transition. Resistance to change can be challenging, as employees may be accustomed to traditional inventory methods.
Effective leadership, ongoing training, and clear communication are essential to foster a culture of continuous improvement and make lean inventory a long-term success.
How to Implement Lean Inventory in Your Business
Bringing lean inventory principles into your business doesn’t have to be complicated, but it does require commitment and the right strategies. By building strong supplier relationships and leveraging modern inventory flow management tools, businesses can create an optimized inventory system that minimizes waste and maximizes efficiency.
-
Build strong supplier relationships
Establishing reliable partnerships with suppliers is essential for maintaining a lean inventory. For example, it ensures materials arrive quickly without unnecessary stockpiling. Open communication and mutual trust enable businesses to align supply with demand efficiently, reducing excess inventory while maintaining a smooth production flow.
-
Use inventory management software
Implementing efficient inventory management software allows businesses to track stock levels in real time, automate reordering, and improve demand forecasting. With features like FEFO (First Expired, First Out) and automated stock synchronization, companies can minimize waste and prevent stock shortages, leading to an optimized inventory system that enhances operational efficiency.
Challenges of Lean Inventory Management
While lean inventory management offers numerous advantages, it also comes with challenges that businesses must address to ensure success. By understanding these obstacles and applying the right strategies, companies can create an optimized inventory system that enhances efficiency and profitability.
- Resistance to change: Shifting from traditional inventory methods to a lean inventory approach can be met with resistance from employees accustomed to established processes. Proper training, clear communication, and demonstrating the benefits of lean inventory can help employees embrace the new system and improve overall adoption.
- Lack of data: A successful lean inventory system relies on precise data related to stock levels, sales patterns, and customer demand. Without access to reliable insights, businesses risk mismanaging inventory, leading to overstocking or shortages, which disrupt inventory flow management and impact profitability.
- Technology gaps: For example, outdated or insufficient technology can prevent businesses from fully optimizing their lean inventory. Investing in modern, efficient inventory management software provides real-time tracking, automated reordering, and data-driven decision-making, ensuring a more effective and responsive inventory system.
Despite these challenges, businesses that successfully implement lean inventory strategies experience significant improvements in cost reduction, efficiency, and customer satisfaction. By leveraging the right tools and training, companies can overcome these obstacles and build a sustainable, optimized inventory system that drives long-term success.
How HashMicro’s Software Can Simplify Lean Inventory Management
Managing inventory manually often results in inefficiencies, excess stock, and wasted resources. HashMicro’s Inventory Software empowers businesses to implement lean inventory practices, ensuring accurate stock control, minimizing waste, and improving operational efficiency.
Experience the power of HashMicro’s Inventory Software with a free demo. Discover how our advanced system helps businesses optimize stock control, prevent overstocking, and ensure a lean inventory, that aligns with real-time demand.
Why Choose HashMicro? Our optimized inventory system automates critical inventory processes, such as real-time stock tracking, multi-location inventory control, and smart reordering, ensuring greater accuracy and cost efficiency. Seamlessly integrating with procurement, warehouse, and accounting modules provides a lean inventory, enhancing overall business performance.
Key Features of HashMicro’s Inventory Software for Lean Inventory Management:
- Stock Forecasting: By analyzing historical sales data and market trends, stock forecasting accurately predicts future demand. This prevents overstocking and stock shortages, ensuring efficient inventory management and a balanced supply chain.
- Run Rate Reordering Rules: Automating reorder points based on sales velocity and consumption patterns ensures timely stock replenishment. This minimizes manual intervention, reduces carrying costs, and prevents overstocking and stockouts.
- FEFO – First Expiry First Out: Implementing FEFO ensures that products with the earliest expiration dates are used or sold first. This reduces waste, maintains product quality, and enhances lean inventory efficiency.
- Stock Aging Report: Monitoring stock aging helps identify slow-moving or obsolete inventory that needs to be cleared or optimized. This improves inventory turnover, reduces excess storage costs, and prevents financial losses from unsellable stock.
- Fast-moving and Slow-Moving Stocks Analysis: Categorizing products based on their sales velocity allows businesses to prioritize high-demand items and reduce slow-moving stock. This optimizes warehouse space, streamlines procurement, and improves cash flow.
- Stock Optimizer per Warehouse: Distributing inventory efficiently across multiple warehouses based on demand and location ensures optimal stock allocation. This reduces unnecessary transfers, minimizes transportation costs, and enhances overall inventory flow management.
- Replenishment Product with Multiple Action: Automating replenishment through purchase orders, warehouse transfers, or production scheduling ensures optimal stock levels. This eliminates stock shortages, prevents over-ordering, and improves operational efficiency.
- Integrated with Barcode & QR Code: Barcode and QR code scanning streamline stock tracking and reduce manual errors in inventory updates. This enhances accuracy, speeds up warehouse operations, and improves supply chain transparency.
- Lot & Serial Number Management: Assigning unique lot and serial numbers to inventory items enables full traceability throughout the supply chain. This ensures regulatory compliance, simplifies recall management, and enhances inventory accuracy.
- Stock Take and Inventory Adjustment Management: Automating stock takes and adjustments ensures real-time inventory accuracy with minimal effort. This reduces discrepancies, enhances data reliability, and supports a well-maintained optimized inventory system.
These features enable businesses to reduce stock waste, improve supply chain efficiency, and create a lean inventory example that supports business growth. With HashMicro’s Inventory Software, companies can achieve optimized inventory system processes, enhance stock control, and drive sustainable efficiency.
Conclusion
Lean inventory management is a strategic approach that helps businesses minimize waste, optimize stock levels, and improve efficiency. By implementing lean inventory principles, companies can cut unnecessary costs, enhance supply chain agility, and maintain a competitive edge in a dynamic market.
HashMicro’s Inventory Management Software provides the automation and intelligence needed to execute lean inventory management seamlessly. With features like real-time stock tracking, smart reordering, and inventory optimization, businesses can easily reduce excess inventory, prevent stockouts, and improve operational performance.
Ready to experience the benefits of lean inventory? Try HashMicro’s Inventory Management Software with a free demo and see how you can streamline your operations, eliminate inefficiencies, and drive sustainable growth today!
FAQ About Lean Inventory
-
How can a lean inventory strategy help your business reduce waste and improve efficiency?
A lean inventory strategy reduces waste by ensuring businesses stock only what is needed, minimizing excess and storage costs. By implementing Just-in-Time (JIT) and automation, companies can optimize stock levels and prevent overproduction.
This approach enhances inventory flow management, streamlining operations and improving supply chain efficiency. As a result, businesses experience lower costs, better resource utilization, and increased profitability while maintaining seamless operations.
-
How to do Lean inventory?
1. Ensure Accurate Inventory Tracking – Utilize an ERP system or digital tools to maintain real-time inventory visibility and precise stock records.
2. Build Strong Supplier Relationships – Collaborate closely with suppliers to enhance efficiency, ensure timely deliveries, and align inventory needs.
3. Maintain a Safety Stock – Keep a buffer inventory to prevent shortages and disruptions in case of unexpected demand or supply chain delays.
4. Adopt Cycle Counting – Regularly audit inventory in small, scheduled counts to maintain accuracy and reduce discrepancies without major disruptions.
-
What are the 4 P’s of lean?
1. Philosophy – Focus on long-term success by prioritizing efficiency, waste reduction, and continuous improvement.
2. Process – Implement streamlined workflows to enhance productivity and eliminate unnecessary steps in production.
3. People & Partners – Build strong relationships with employees and suppliers to ensure smooth collaboration and operational efficiency.
4. Problem-Solving – Encourage a culture of continuous improvement by identifying issues, analyzing root causes, and implementing effective solutions.