Maximizing productivity while maintaining quality and efficiency is a common challenge for many businesses. OEE, or Overall Equipment Effectiveness, helps measure how well equipment is performing practically and clearly.
It gives managers and decision-makers a better view of where time and output are lost and where improvements can be made. As the evolution of overall equipment effectiveness continues to shape modern operations understanding this concept is key to making smarter and more confident business decisions.
This guide will walk you through the basics of OEE, why it’s important and how it can bring real value to your operations.
Key Takeaways
|
Table of Content
Content Lists
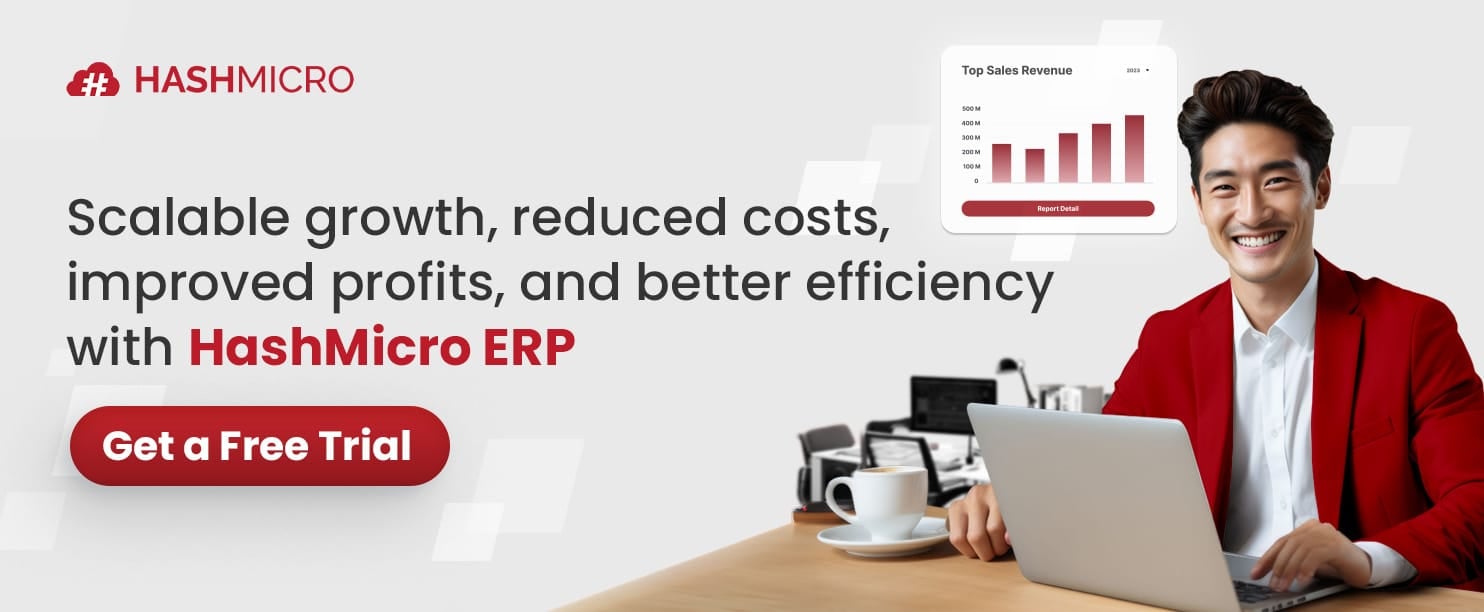
What is OEE?
OEE or Overall Equipment Effectiveness is a key metric in maintenance that helps measure how well equipment supports production. It considers three main factors availability, performance and quality to give a clear view of equipment efficiency throughout the manufacturing process.
Availability shows whether the machine is ready and running when needed. Performance refers to how much output the machine delivers compared to its maximum capacity. Quality reflects the percentage of products that meet expected standards.
By tracking these elements, businesses can pinpoint strengths and identify areas for improvement. When integrated with ERP manufacturing software, OEE data becomes even more powerful. It offers real-time insights, centralized reporting, and better decision-making across production teams.
What is the OEE Formula?
To truly understand how OEE works in practice, it’s essential to examine how it’s calculated.
By breaking it down into clear and measurable components, you can gain deeper insights into where efficiency is gained or lost within your operations. The OEE formula is:
If you’re unsure how to apply this formula in real operations, no need to worry. Here’s a simple example of how the OEE formula works in a manufacturing setting.
A manufacturing company produces bicycles in the Philippines. It wants to know the OEE of their production process using the following data:
- Good count: 380 units
- Ideal cycle time: 1 minute per unit
- Planned production time: 8 hours (480 minutes)
The calculation is as follows:
In other words, the production process is running at 79.17% efficiency, giving a clear picture of how well operations are performing at the moment.
Key Components of the OEE Framework for Businesses
The key elements of OEE are closely tied to the factors that make up the OEE formula such as:
- Good count: The number of units that meet quality standards, excluding defective or reworked items. This is crucial for assessing the overall production quality.
- Ideal cycle time: The minimum time required to produce one unit when everything is functioning optimally.
- Planned production time: The total scheduled production time, excluding any planned downtime such as maintenance.
- Fully productive time: The actual time when equipment operates at its peak, producing quality units without interruptions.
What does OEE Mean for Maintenance?
Overall equipment effectiveness is a valuable tool for maintenance teams. It helps identify problems, minimize downtime, and ensures machines operate at their best. Here’s how OEE influences maintenance:
Aspect |
Explanation |
Benefits for Maintenance |
Availability | Measures downtime and operating time. | Pinpoints when and why downtime occurs, aiding in preventive measures. |
Performance | Compares actual speed to ideal speed. | Helps identify issues affecting machine speed, guiding maintenance actions. |
Quality | Assesses defect rates in production. | Reveals quality-related problems that maintenance can address. |
Data-Driven Decisions | Uses OEE data to plan maintenance. | Improves scheduling and reduces unplanned repairs. |
Benefits of Conducting OEE
Implementing overall equipment effectiveness within manufacturing software offers several important benefits, such as:
- Identifying inefficiencies: OEE reveals hidden issues like downtime, slow production, and defects, enabling focused improvements.
- Increasing productivity: OEE helps enhance output without needing additional resources by maximizing equipment efficiency.
- Improving quality: It monitors defects to reduce waste, ensuring more high-quality products are produced.
- Optimizing maintenance: Provides valuable insights for proactive maintenance, preventing major breakdowns and extending the lifespan of equipment.
- Supporting better decisions: Delivers real-time data that empowers managers to make informed, quick decisions for ongoing improvement.
Challenges for Improving Overall Equipment Effectiveness
Improving OEE can be difficult due to several factors:
- Unplanned downtime: Unexpected equipment failures can disrupt production, making it challenging to maintain optimal OEE. Identifying and fixing the root causes of these breakdowns can be complicated.
- Variable production speeds: Fluctuations, often caused by operator errors or equipment wear, can prevent machines from running at their ideal pace.
- Quality challenges: Achieving consistent high-quality output is tough, particularly when defects result from poor raw materials or outdated processes. Reducing defects requires ongoing monitoring and adjustments.
- Data tracking: Gathering accurate OEE data in real-time can be tricky without the proper tools, often leading to incomplete or incorrect information that hinders effective decision-making.
- Resistance to change: Employees may be hesitant to adopt new processes or technologies meant to improve OEE, making it difficult to implement changes smoothly.
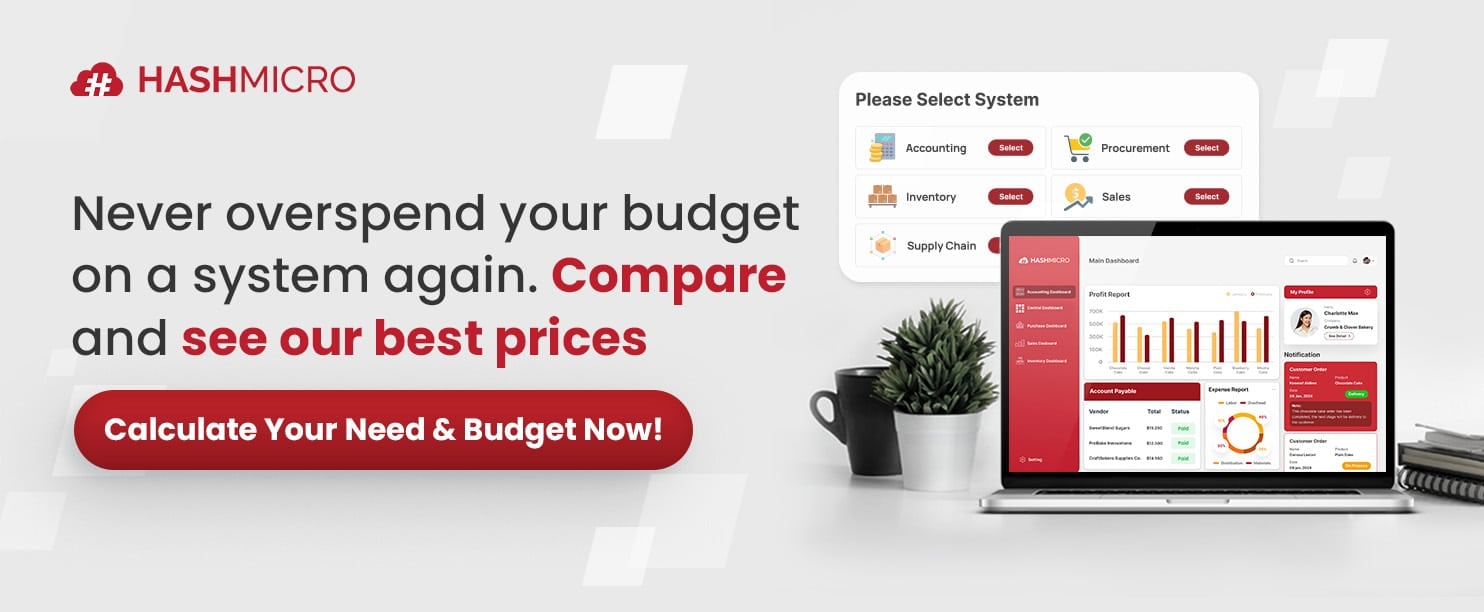
How to Improve OEE
To improve Overall Equipment Effectiveness (OEE), it’s essential to focus on key areas that directly impact equipment performance and production efficiency. Here are some actionable steps you can take to enhance overall effectiveness:
- Minimize downtime: Perform routine maintenance and promptly resolve issues to reduce unplanned production interruptions.
- Optimize production speeds: Regularly assess and adjust machine speeds to maintain optimal cycle times without compromising product quality.
- Enhance quality control: Implement robust quality control measures to detect defects early and minimize the need for rework or waste.
- Standardize procedures: Establish consistent operating procedures to ensure stable performance and eliminate production variability.
- Utilize OEE tracking tools: Invest in advanced, real-time software solutions to continuously monitor OEE, enabling swift identification and resolution of issues.
Boost Your Overall Equipment Effectiveness with HashMicro Software
Using an OEE tracking tool is crucial for improving manufacturing processes. But which software can effectively handle OEE and other manufacturing tasks? HashMicro could be the ideal solution for you.
HashMicro is a reliable software provider that has been operating since 2015. With impressive achievements, HashMicro offers high-quality software with numerous benefits, including a free demo, no extra cost for additional users, and customizable options.
The OEE calculation could happen by the use of these features:
- Manufacturing requisition planning: A tool that helps create detailed production plans and ensures that the necessary raw materials and resources are available for the production process.
- Quality control: A system designed to verify that stored, processed, and delivered products meet the required quality standards.
- Manufacturing production scheduling: A feature that enables businesses to organize production timelines based on demand forecasts derived from historical data.
- Finished goods production simulation: A feature that simulates the number of products that can be produced based on the materials available in the Bill of Materials (BoM).
- Gantt Chart management: A tool that aids in production planning by scheduling machine and labor capacity and helping identify any potential scheduling conflicts.
By incorporating tools like PPIC production planning software and optimizing manufacturing warehouse operations, companies can enhance visibility, reduce bottlenecks, and improve overall production efficiency.
Conclusion
Enhancing Overall Equipment Effectiveness (OEE) in manufacturing is crucial for improving efficiency and driving growth. While OEE brings benefits like higher productivity and improved quality, challenges such as unplanned downtime and production inconsistencies can still occur.
HashMicro’s manufacturing software helps address these issues through real-time monitoring, automated maintenance, and quality control.
Interested in learning how it can optimize your operations? Book a free demo today to explore its full capabilities.
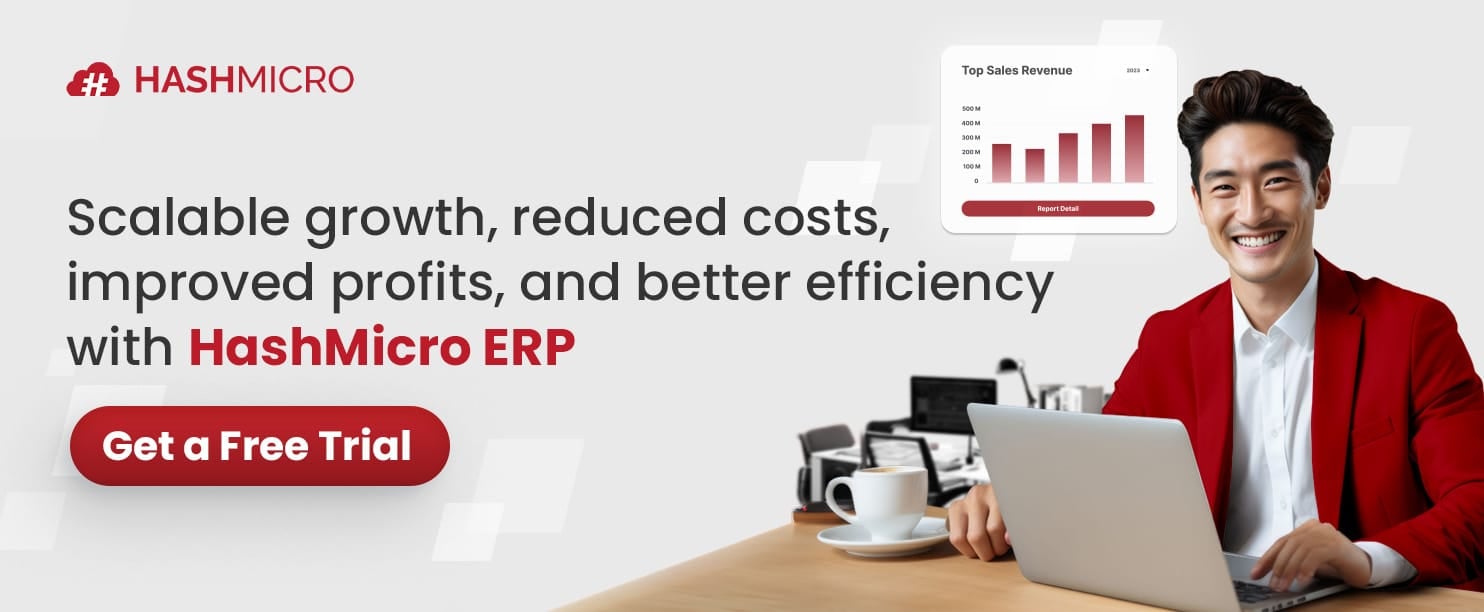
FAQ OEE
-
What is the formula for total asset usage?
How to calculate your asset utilization. The most basic asset utilization metric takes the total losses in hours and subtracts those losses from the total number of hours in a year (8,760). The maximum possible asset utilization for each asset is 8,760 hours in a year period.
-
Why is OEE important?
OEE provides a comprehensive view of how Maintenance and Production are impacting production line performance, enabling them to work together to increase capacity and improve asset performance and plant profitability.