Have you ever experienced an order-picking mistake, like receiving the wrong product instead of what you ordered? It’s a frustrating experience for customers and a costly error for businesses. Each mistake forces the store to handle product exchanges, process refunds, and adjust inventory levels.
A reliable order-picking process can prevent these mistakes and ensure customers always receive the right products. With accurate and efficient picking methods, businesses can avoid unnecessary errors and maintain a seamless fulfillment process.
This article delves into the importance of order picking and offers a practical guide to optimizing it for improved accuracy and a better customer experience. Read on to get to know this concept more!
Key Takeaways
|
Table of Content
Content Lists
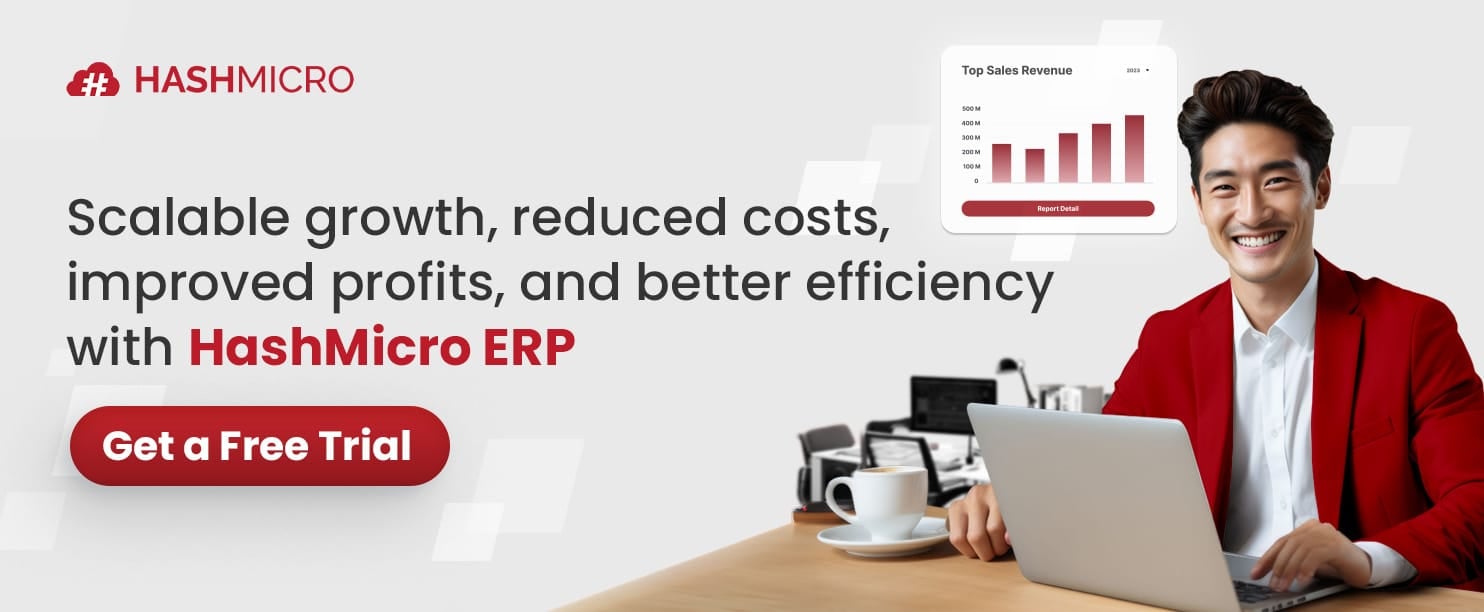
What is Order Picking?
Order picking is the process of retrieving items specified in a customer’s order from their designated storage locations within a warehouse. It’s the first step in getting an order ready, and it needs to be accurate so packing, shipping, and delivery go smoothly. A good system ensures the right items are picked every time.
For example, imagine shopping at Lotus’s in Malaysia. You go around different aisles to find everything on your list because the items aren’t all in one spot. That’s similar to what a warehouse picker does: collecting products from different locations to complete an order.
Even though it sounds simple, order picking is expensive. It’s one of the most costly warehouse tasks, making up the largest part of operating expenses. A report from H. Milton Stewart School of Industrial and Systems Engineering at Georgia Tech shows it can take up to 63% of a warehouse’s total budget.
Types of Order Picking
There are three main picking systems: piece picking, case picking, and pallet picking. Each system works with five processes: single order picking, batch picking, zone picking, pick-and-pass, and wave picking. Let’s break the order picking methods down:
Picking Systems
- Piece Picking: This involves picking items one by one from the warehouse. It’s commonly used for orders with many SKUs but a small quantity per item.
- Pallet Picking: Pallet picking involves retrieving entire pallets, which are wooden platforms holding products. Depending on size, a pallet may contain one large item or several smaller ones.
- Case Picking: Similar to pallet picking, but here only part of a pallet is picked. This method is used for orders with a variety of SKUs but fewer items per SKU.
Picking Processes
- Single Order Picking: In this process, the picker handles one order at a time and takes it to the packing station. It’s ideal for smaller warehouses with low traffic and works with piece, case, or pallet picking.
- Batch Picking: Pickers handle multiple orders at once, collecting items for several orders in one trip to the packing station. This is useful for high-order volumes with a small number of items per order and is mostly used with piece picking.
- Zone Picking: Warehouses are divided into zones, and each picker is responsible for one zone. Pickers handle all orders from their assigned area, making it suitable for high-volume orders with a large number of items. It works with all three picking systems.
- Pick-and-Pass: This is a variation of zone picking. Orders are passed from one zone to another until all items are picked. It’s compatible with all three picking systems.
- Wave Picking: Pickers from different zones simultaneously collect items for an order and send them to a consolidation area. Once all items are consolidated, the order is sent to packing. Wave picking is ideal for warehouses needing fast shipping for high-volume orders and works with all three systems.
Automated Picking Systems
Traditionally, pickers relied on a paper picklist, which is simply a list of items needed to fulfill an order. Nowadays, warehouses use automated picking systems that act as picklists, guide pickers to product locations using the best route, verify if the correct items are picked, and more.
Here are some commonly used automated picking systems:
1. Pick-to-Light
This system uses barcode scanners and LED lights set up on racks and shelves. The picker scans the barcode on a shipping carton, which temporarily holds items for one order. Scanning activates the LED lights for the products in that order, guiding the picker to their locations. This system reduces both picking time and labor costs.
2. Voice Picking
Pickers wear headsets connected to an order management system, receiving voice instructions on where to find items. This method boosts both productivity and accuracy.
3. Mobile Scanner Picking
All items in the warehouse are labeled with unique barcodes. Pickers use mobile scanners that display the order picklist and the location of each item. If the wrong barcode is scanned, the device alerts the picker, ensuring a high level of accuracy.
No matter the method used, order picking is about selecting the correct products from a warehouse for a customer’s order. Since warehouses vary in size, order volume, and infrastructure, the best picking method depends on the specific needs of each operation.
Moreover, all of these systems can be used either independently or integrated into one cohesive system with a warehouse management system (WMS).
However, those who run a warehouse must have realized that they might need the WMS to ease their burdens beyond just integrating the tools. Hence, we’ve provided a list of the best warehouse management system for your perusal and further considerations.
Advantages of Order Picking
Using an effective order-picking method can significantly improve how your warehouse clustering runs and delivers results. From faster delivery to higher customer satisfaction, the benefits are both practical and impactful. Below are seven benefits of order picking for your warehouse:
- Faster Delivery Times: With optimized methods like batch picking or pick-to-light systems, workers spend less time locating items, which speeds up fulfillment and supports faster delivery, such as same-day or next-day services.
- Fewer Customer Returns: Ensuring orders are picked accurately reduces mistakes, such as shipping the wrong items or quantities. Over time, the system will be running smoothly without much more nudgings.
- Lower Labor Costs: Efficient systems, such as voice picking, enable workers to process multiple orders in a single trip. As a result, businesses can reduce overtime hours and limit the need for temporary staff during peak seasons.
- Better Use of Warehouse Space: Strategies like zone picking help reduce bottlenecks in narrow aisles and optimize layouts for smoother movement. Workers can navigate the space more effectively while keeping items accessible and organized.
- Improved Inventory Accuracy: Order picking often acts as a secondary inventory check. With tools like mobile scanners and barcodes, businesses can update stock records in real time, reducing mismatches and preventing costly stockouts.
- Fewer Workplace Injuries: Integrating trolleys, conveyor belts, and automated tools significantly reduces physical strain on workers. Lower strain decreases the risk of repetitive injuries and creates a safer environment.
- Reduced Stockouts: Accurate picking processes help warehouses spot inventory gaps early. Reordering stock before it runs out ensures consistent availability and avoids missed sales opportunities.
How to Choose an Order Picking System
The efficiency of your business operations can heavily depend on the order-picking method used in your warehouse. Your chosen strategy also helps maintain a safe and organized workspace for your employees.
Moreover, using the right order-picking technique can enhance customer satisfaction and overall experience, which is key to retaining loyal customers. When selecting an order-picking process, consider factors such as:
- The working hours of your pickers: Consider when your pickers will work, as this affects how you manage shifts and productivity, especially during peak hours.
- Employee safety: Ensure your chosen method minimizes risks, like heavy lifting or repetitive strain, to protect workers and reduce accidents.
- The size of your workforce: Choose a strategy that matches your team size—smaller teams may need simpler methods, while larger teams can handle complex systems.
- The types of products you sell: If your products vary in size or fragility, select a method that accommodates these differences without risking damage.
- Product sizes and typical order quantities: For large or bulk items, pallet picking might work best, while smaller, diverse orders may require piece picking.
- How frequently customers place orders: If you handle high-frequency orders, prioritize faster techniques like batch picking or automated systems to meet demand efficiently.
It’s important to establish clear goals when choosing an effective order-picking strategy for your business.
Optimize Your Order Picking System with HashMicro’s WMS
Every successful warehouse thrives on accuracy and efficiency, especially when it comes to order picking. Delays, errors, and disorganized workflows often disrupt the process, leading to dissatisfied customers and increased costs.
With HashMicro’s WMS, your warehouse can achieve this seamlessly. The system optimizes your picking processes by guiding pickers with real-time inventory data, automated picking routes, and tools like mobile scanners.
Whether you’re dealing with bulk pallet picking or smaller, SKU-heavy orders, HashMicro’s WMS adapts to your needs by offering these features:
- Picking, Packing, Delivery Management: Tracks and organizes the workflow for order picking, packing, and delivery coordination. Assigns tasks to workers, logs item statuses, and ensures every step of the process is completed in sequence.
- Integrated with Barcode, QR, and RFID: Allows pickers to scan product codes using barcode readers, QR scanners, or RFID devices. Identifies products quickly by matching scanned data with warehouse records.
- Mobile Apps with Mobile QR/Barcode Scanner with Ad Hoc Transfers: Enables workers to scan product codes directly from a mobile app and execute immediate stock transfers. Displays real-time picking tasks and confirms item selection on the go.
- Mobile Apps that Work Hybrid (Online & Offline): Operates seamlessly in both online and offline modes, allowing users to continue scanning and updating tasks without connectivity interruptions. Syncs data automatically once the connection is restored.
- Putaway Strategy Based on Product, Product Categories, or Warehouse Capacity: Assigns storage locations for products based on category, size, or available warehouse capacity. Ensures that items are placed systematically for quick access.
- Stock Optimizer : Analyzes stock levels across multiple locations and suggests transfers to ensure appropriate distribution of inventory. Tracks and updates stock movement logs after execution.
- In-Depth Reports: Compiles and organizes data on inventory trends, including the age of stock, movement frequency, current levels, and stock transfers. Categorizes information into detailed reports for easy review.
Conclusion
Order picking is the process of retrieving items from storage to fulfill customer orders accurately and efficiently. It is a crucial step in ensuring smooth fulfillment and easier management of a business’s warehouses.
To take your order-picking process to the next level, HashMicro’s WMS offers a seamless and reliable solution. With advanced features, the system simplifies even the most complex workflows. These capabilities make it easier to handle large order volumes while maintaining accuracy and efficiency.
HashMicro’s WMS empowers businesses with tools for better organization and decision-making. From automated stock management to detailed reporting, the system helps you stay in control and ahead of your competitors.
Ready to see how HashMicro’s WMS can transform your warehouse? Try the free demo today and experience the difference!
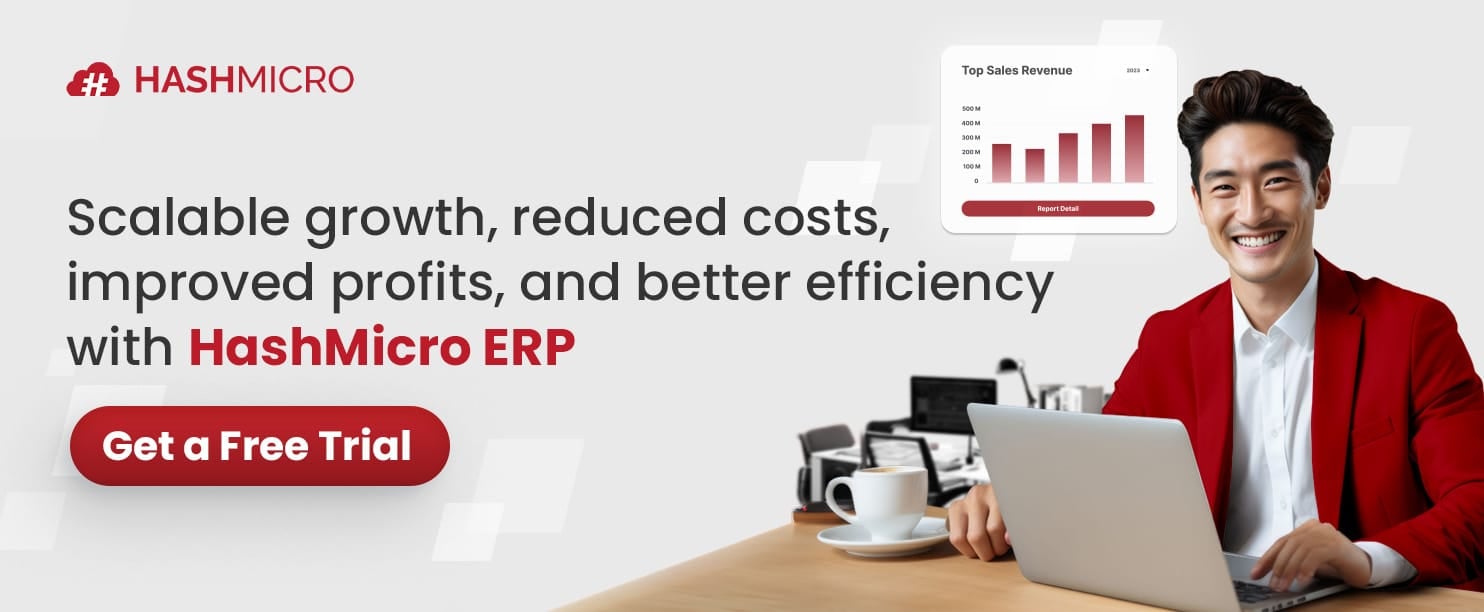
FAQ on Order Picking
-
What is the most efficient order picking method?
The efficiency of an order picking method depends on various factors, including order volume, product types, and warehouse layout. Common methods include single-order picking, batch picking, zone picking, and wave picking, each suitable for different operational needs.
-
How can technology improve order picking accuracy?
Implementing technologies such as Warehouse Management Systems (WMS), barcode scanning, and automated picking tools can significantly enhance accuracy by reducing human errors and providing real-time inventory data.
-
How does order picking impact customer satisfaction?
Accurate and timely order picking ensures that customers receive the correct products promptly, directly influencing their satisfaction and likelihood of repeat business. Efficient order picking processes are essential for meeting customer expectations.
-
What are the common challenges in order picking?
Challenges include incorrect orders, inefficient organization, worker fatigue, ergonomic issues, and difficulties during peak demand or labor shortages. Addressing these challenges is crucial for maintaining efficiency and accuracy.