Unexpected equipment failures can lead to costly downtime, reduced efficiency, and frustrated teams. For businesses that rely on seamless operations, a well-structured preventive maintenance strategy is essential.
Rather than waiting for machines or systems to break down, preventive maintenance focuses on regular inspections, servicing, and repairs to keep assets in peak condition. Without it, companies risk frequent disruptions, higher repair costs, and lost productivity.
How can businesses implement an effective preventive maintenance plan? What are the key types and benefits? This guide breaks it all down helping you optimize asset allocation and operational efficiency.
Keep reading to discover how the right preventive maintenance approach supported by smart automation solutions can transform the way your company manages its assets.
Key Takeaways
|
Table of Content
Content Lists
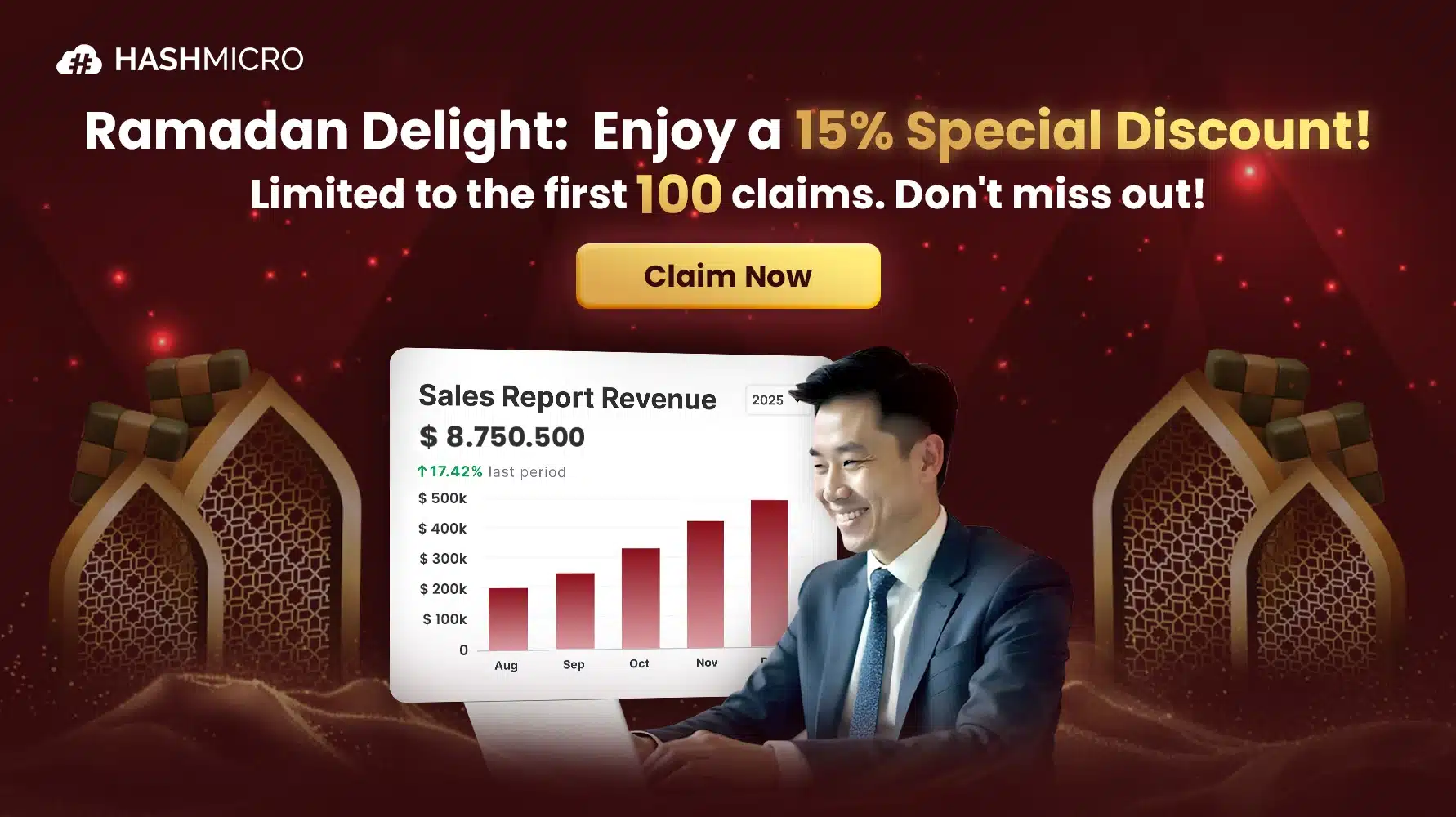
What is Preventive Maintenance?
Preventive maintenance is a systematic approach to maintaining equipment, machinery, and assets through scheduled inspections. Unlike reactive maintenance which addresses issues only after a breakdown occurs, preventive maintenance focuses on detecting and resolving potential problems before they lead to costly failures.
This strategy helps businesses minimize unplanned downtime, extend the lifespan of critical assets, and improve overall operational efficiency.
By implementing a well structured maintenance strategy, companies can optimize asset allocation, reduce repair costs, and ensure consistent performance across their operations.
10 Key Types of Preventive Maintenance Every Business Should Know
Implementing an effective preventive maintenance strategy requires understanding the different approaches available. Each type serves a specific purpose, helping businesses maintain equipment reliability, reduce downtime, and optimize asset allocation.
Below are ten key types that can help your organization improve operational efficiency:
- Periodic maintenance: Conducted at predetermined intervals, regardless of the equipment’s current condition. For example, a manufacturing facility may carry out monthly inspections on all machinery using a structured preventive maintenance checklist.
- Predictive maintenance: Relies on real-time data and monitoring tools to anticipate potential equipment failures. For instance, sensors can be used to track vibration levels in motors, allowing businesses to address issues before they escalate.
- Perspective maintenance: Focuses on analyzing how equipment deteriorates over time, enabling companies to adjust maintenance strategies based on specific wear patterns and prolong asset lifespan.
- Usage based maintenance: Scheduled based on actual equipment operation, such as the number of running hours or production cycles.
- Risk based maintenance: Prioritizes maintenance efforts based on the likelihood and consequences of equipment failure. High-risk machinery with significant operational impact receives greater attention and more frequent servicing.
- Time based maintenance: Performed at fixed intervals, regardless of equipment condition. A common example is servicing HVAC systems every six months to ensure optimal performance.
- Condition based maintenance: Carried out when specific indicators, such as temperature fluctuations or pressure changes, signal potential wear. For instance, oil changes are performed when viscosity levels drop below the recommended threshold.
- Meter based maintenance: Scheduled according to usage metrics like mileage, energy consumption, or operating hours. For example, a fleet vehicle may undergo servicing after reaching 50,000 miles.
- Calendar based maintenance: Follows a predetermined schedule, such as annual servicing of heating systems before the onset of winter to ensure efficiency.
- Failure finding maintenance: Aims to detect hidden failures in protective systems, such as fire alarms, ensuring they function properly when required for safety compliance.
The Difference Between Predictive and Preventive Maintenance
Understanding the differences between preventive and predictive maintenance: a guide to making the right choice for your business.
Aspect | Preventive Maintenance | Predictive Maintenance |
Approach | Scheduled maintenance at regular intervals. | Maintenance based on real-time data and equipment condition. |
Trigger | Time-based or usage-based intervals. | Condition of equipment, monitored by sensors or data. |
Cost | Lower initial cost, but can lead to unnecessary tasks. | Higher initial cost due to monitoring tools, but more efficient in the long run. |
Downtime | Prevents downtime but may still result in unnecessary stops. | Minimizes downtime by addressing issues only when needed. |
Resource utilization | This can result in over-maintenance or under-maintenance. | Ensures optimal use of resources based on actual conditions. |
Data dependency | Minimal reliance on data. | Heavily reliant on real-time data and advanced analytics. |
Efficiency | Preventive but may lead to unnecessary repairs. | Highly efficient, addressing only imminent failures. |
Both preventive and predictive maintenance have benefits, but preventive maintenance stands out by addressing potential issues before they arise, ensuring seamless operations. Integrating these strategies with asset management software can further enhance equipment reliability and maximize resource efficiency.
To explore how these systems can simplify maintenance processes and reduce costs, take the first step by reviewing the pricing options for asset management software below.
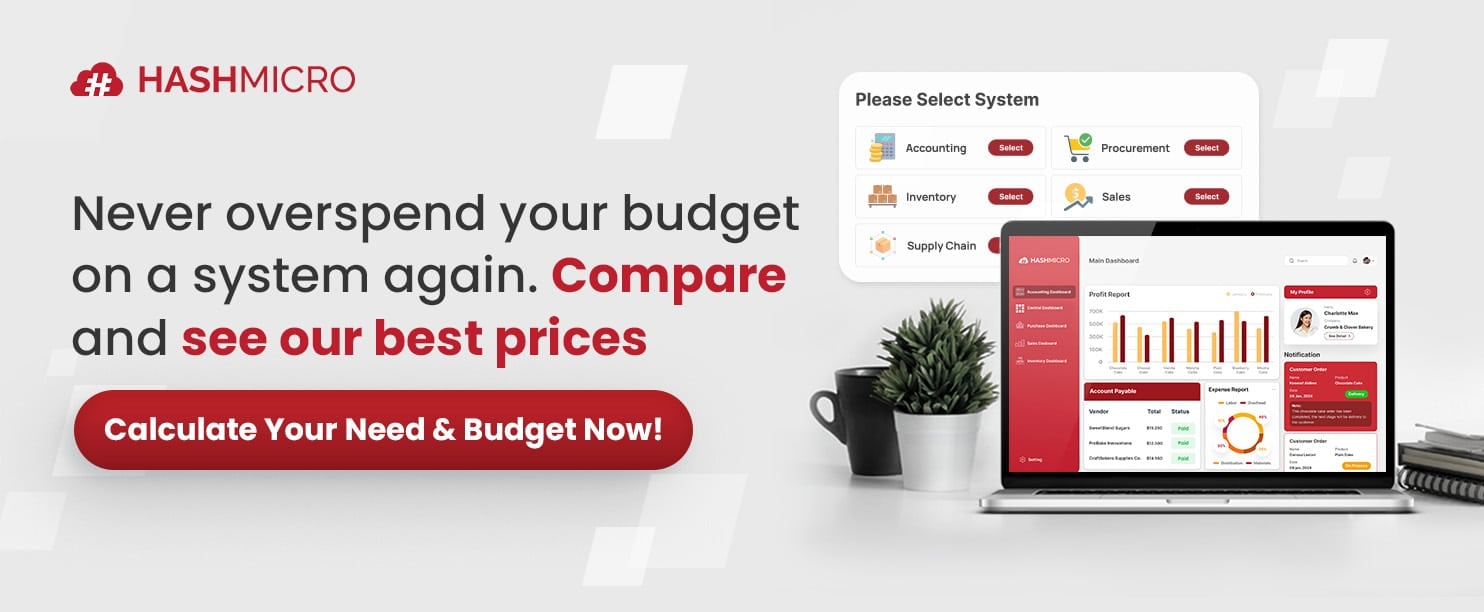
Pros and Cons of Implementing Preventive Maintenance
Before adopting strategy, it is essential to understand both its advantages and limitations. While this approach helps reduce unexpected failures and optimize asset management, it also requires proper planning and resources.
Implementing EAM software can streamline this process by improving maintenance scheduling and resource allocation. The table below outlines the key pros and cons of incorporating preventive maintenance into your business.
Pros | Cons |
Reduces unexpected equipment failures. | Requires regular scheduling and planning. |
Extends the lifespan of assets. | Can lead to unnecessary maintenance if not properly managed. |
Improves operational efficiency. | May increase short-term costs due to frequent servicing. |
Enhances workplace safety by preventing accidents. | Demands skilled personnel and the right tools. |
Lowers long-term repair and replacement costs. | It can be challenging to implement without asset management software. |
Transform Your Complex Maintenance Into Automatic Asset Management from HashMicro
Managing maintenance for multiple assets can be complex, especially in industries that rely on heavy equipment and infrastructure.
The integrated HashMicro Construction Asset Management Software simplifies this process by automating maintenance tasks, keeping assets in top condition, and reducing downtime and costs.
With real time tracking and predictive features, businesses can transition from manual maintenance to a fully automated and more efficient system.
- Automated maintenance scheduling: Plan and execute preventive maintenance effortlessly to extend asset lifespan.
- Real time asset monitoring: Track asset performance and detect potential issues before they lead to failures.
- Predictive maintenance integration: Utilize data-driven insights to optimize maintenance schedules and reduce unexpected breakdowns.
- Comprehensive asset tracking: Maintain complete visibility over construction equipment, tools, and materials.
Conclusion
Preventive maintenance helps extend equipment lifespan, reduce downtime, and enhance operational efficiency. By addressing potential issues before they escalate, businesses can prevent costly repairs while improving safety and overall performance.
To streamline this process, consider automating your preventive maintenance with HashMicro’s asset management software. This advanced solution enables seamless scheduling, real-time monitoring, and detailed reporting, allowing you to manage assets more effectively.
Try a free demo today and discover how it can optimize your maintenance strategy.
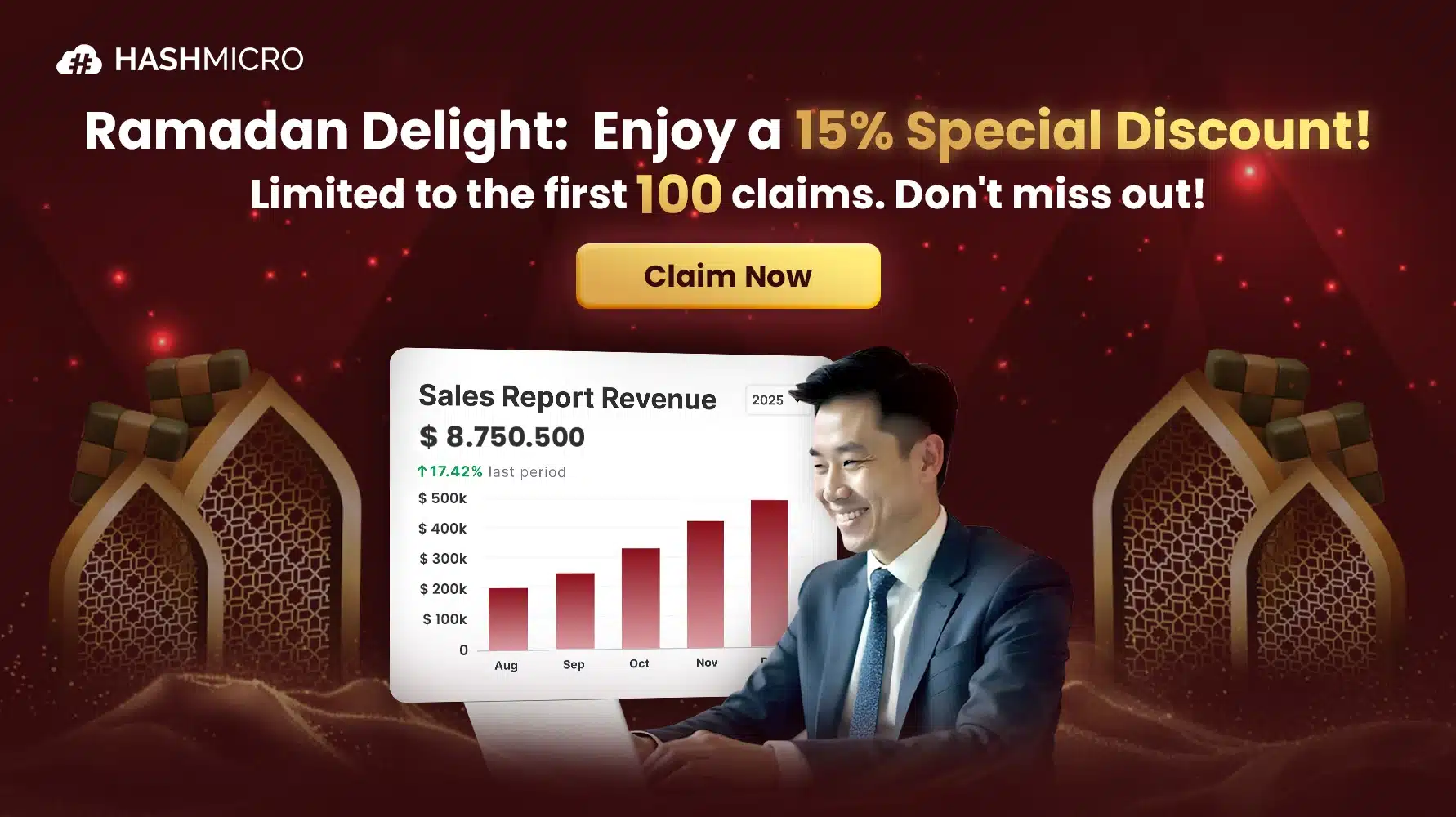
FAQ Preventive Maintenance
-
What is preventive maintenance or PMS?
Preventive Maintenance Schedule (PMS) refers to a systematic approach to maintaining and servicing a vehicle regularly to prevent potential issues and prolong its lifespan.
-
How to calculate PM compliance?
To calculate PM compliance, first start by dividing the total number of completed preventive maintenance work orders by the total number of scheduled work orders within a defined period. Then, multiply the result by 100.
-
What is KPI in maintenance?
Maintenance key performance indicators (KPIs) evaluate factors critical to an organization’s success. They are used to measure performance against goals related to machine failures, repair times, maintenance backlogs, and costs