Imagine launching a new product only to face complaints, returns, and a damaged reputation all because of overlooked quality issues. No company can afford to let that happen. Quality control isn’t just a routine checkpoint. It’s critical to maintaining customer trust, reducing costs, and ensuring business longevity.
By implementing effective QC practices, businesses can minimize errors, improve efficiency, and consistently deliver high-quality products or services. But what does it take to build a quality control system that truly works?
Keep reading to explore its impact and the best strategies for ensuring excellence in your operations.
Key Takeaways
|
Table of Content
Content Lists
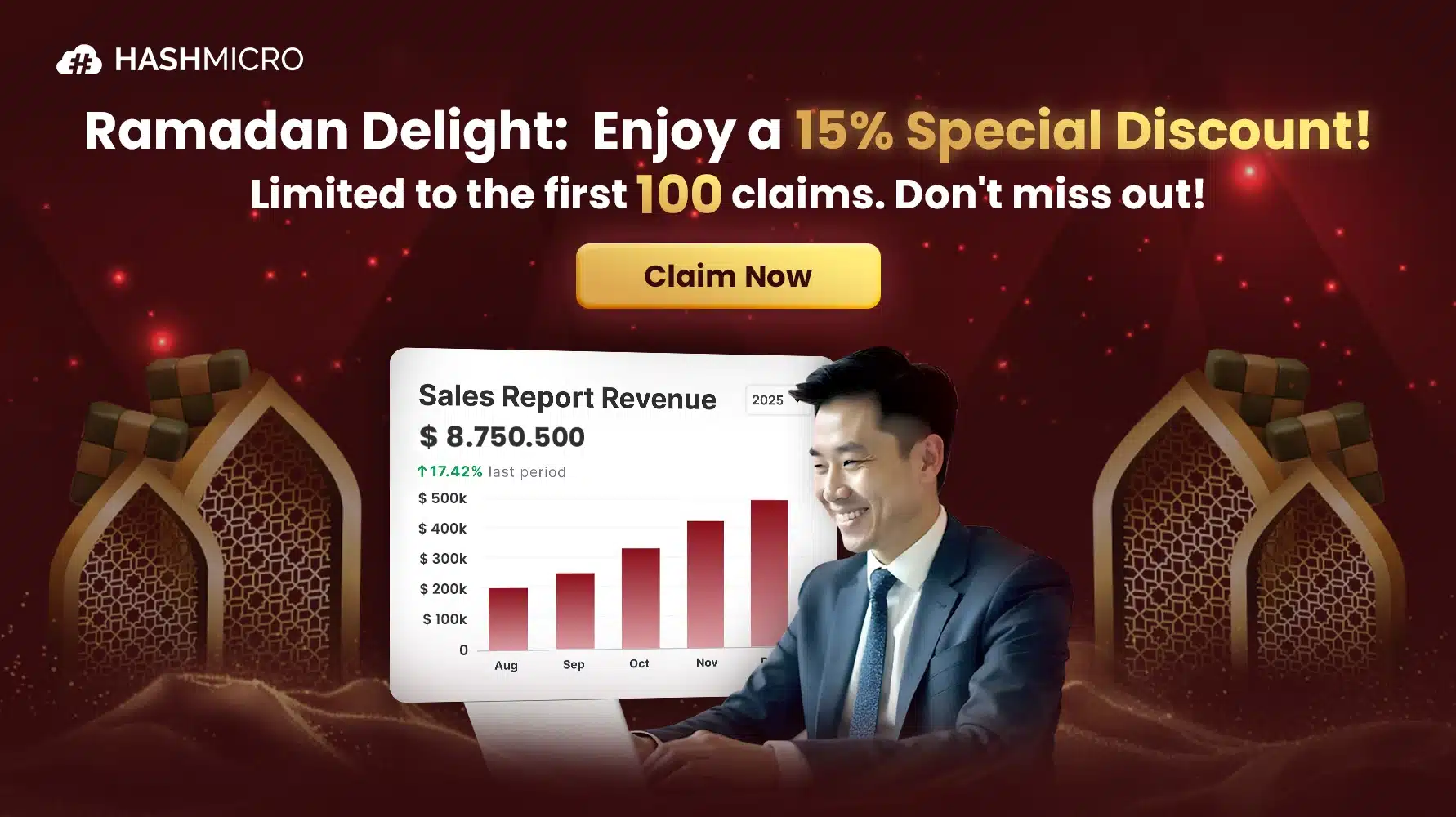
What is Quality Control (QC)?
Quality Control (QC) is a crucial process businesses use to ensure that their products and services meet specific standards. It involves the systematic monitoring and evaluation of various stages of production, from raw materials to finished goods to identify and correct defects or inconsistencies.
QC helps maintain consistency, reliability, and customer satisfaction by detecting issues early and preventing faulty products from reaching the market.
It is the backbone of a company’s commitment to delivering high-quality outputs and maintaining a competitive edge in the industry.
Difference between Quality Control and Quality Assurance
Quality Control (QC) and Quality Assurance (QA) play vital roles in upholding high standards, but they serve distinct functions within a business.
Recognizing the differences between these two processes allows organizations to develop more effective strategies for maintaining product quality. Below is an overview of how QC and QA differ in approach and purpose.
Aspect |
Quality Control (QC) |
Quality Assurance (QA) |
Definition |
QC focuses on identifying defects in finished products. |
QA focuses on preventing defects by improving processes. |
Objective |
Ensure the product meets quality standards and specifications. |
Ensure that the production process itself is efficient and capable of producing quality products. |
Approach |
Reactive – Identifying and correcting issues after they occur. |
Proactive – Implementing processes and guidelines to prevent issues before they happen. |
Scope |
Focuses on the final product or output. |
Focuses on the entire production process and system. |
Methods |
Inspection, testing, and sampling of the product. |
Audits, reviews, and process evaluations. |
Timing |
It happens after the product is produced. |
Occurs during the development or production process. |
Responsibility |
Often performed by dedicated QC inspectors or teams. |
Often involves everyone in the organization, particularly process managers. |
The Importance of Quality Control for Companies
Quality control is a critical process that ensures a company’s products or services consistently adhere to established standards and meet customer expectations. By identifying and addressing issues early in the production cycle, businesses can minimize defects, reduce costly errors, and enhance operational efficiency.
Additionally, a well-implemented quality control system strengthens customer confidence by ensuring the reliability and consistency of delivered products.
In a highly competitive market, maintaining rigorous standards safeguards a company’s reputation, provides a strategic advantage, and fosters long-term success.
Quality Control Methods and Strategies
Several approaches can be used to ensure quality control in manufacturing:
1. Just-in-Time (JIT)
Just-in-Time (JIT) is a production strategy that minimizes inventory waste by ensuring materials and components arrive precisely when needed in the manufacturing process. By implementing JIT inventory management, businesses can enhance efficiency, reduce costs, and prevent excess stock while streamlining operations.
With HashMicro’s Smart Inventory System, JIT becomes even more effective. Enjoy real-time stock tracking, automated procurement, and seamless supply chain integration to keep operations smooth and cost-efficient.
2. Workstation quality
Workstation quality focuses on maintaining high standards at every stage of production by organizing tools, equipment, and materials for optimal workflow. Ensuring that each workstation meets specific quality requirements helps reduce defects, improve consistency, and boost overall productivity.
Well-trained employees play a crucial role in monitoring product quality before it advances to the next stage.
3. Statistical Quality Control (SQC)
Statistical Quality Control (SQC) applies data-driven methods to monitor and maintain product quality throughout manufacturing. By analyzing production samples, SQC helps identify variations that could lead to defects, allowing companies to take preventive action.
Techniques such as control charts, process capability analysis, and regression analysis are commonly used to ensure consistent quality. Integrating manufacturing inventory software with SQC can further enhance efficiency by tracking raw materials.
4. Inspection
Inspection is a fundamental quality control process that involves checking products or materials at different production stages to ensure they meet established quality standards.
This can be done visually or with specialized tools to detect defects, inconsistencies, or deviations from specifications. Inspections may occur during raw material intake, production, or final product evaluation.
5. Total Quality Management (TQM)
Total Quality Management (TQM) is a holistic approach aimed at improving product and service quality across an entire organization.
It emphasizes continuous improvement, employee involvement at all levels, and a commitment to enhancing processes, reducing waste, and increasing customer satisfaction.
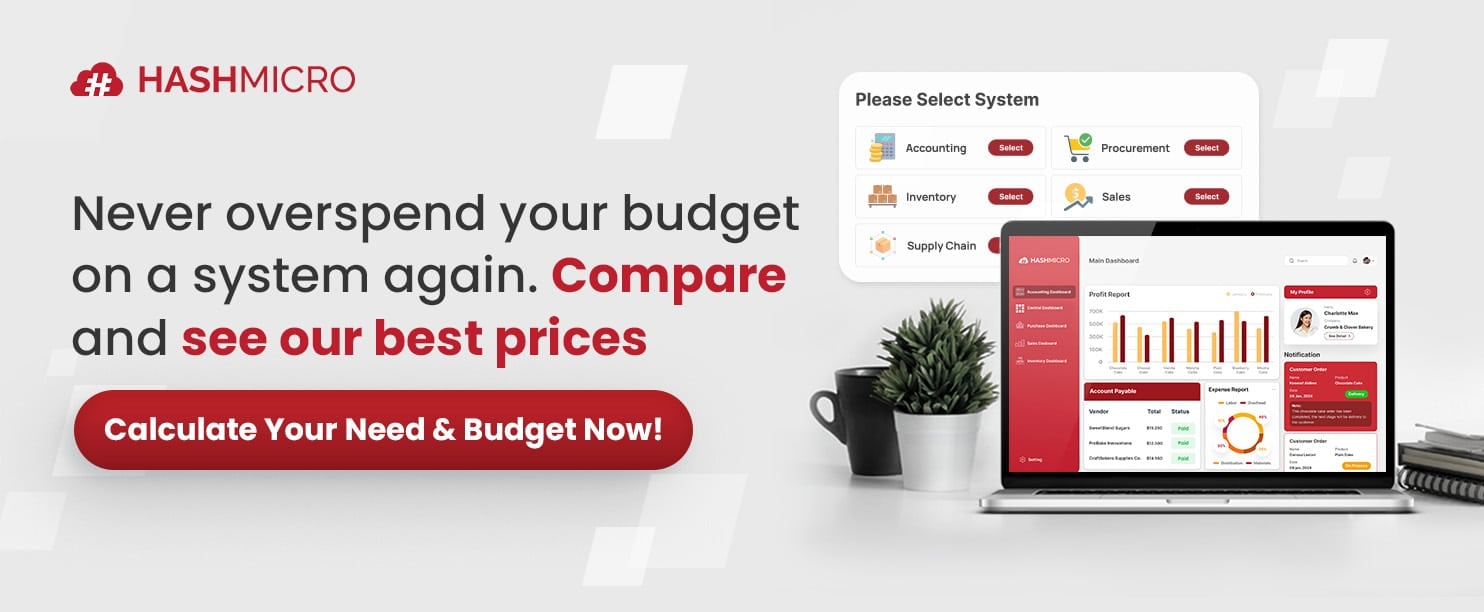
How Can Quality Control be Enhanced in Manufacturing?
Enhancing manufacturing processes is essential to ensuring consistent product standards, boosting customer satisfaction, and improving operational efficiency.
Below are some effective strategies to strengthen quality standards in manufacturing.
1. Auditing processes
Auditing in manufacturing involves systematically reviewing production methods and operational performance to ensure compliance with quality standards. Regular audits help identify inefficiencies, improve workflows, and optimize resource usage.
By conducting audits, manufacturers can minimize errors, enhance consistency, and align processes with industry best practices.
2. Collecting data
Data collection is key in quality control. It provides insights into production efficiency, defect rates, and equipment performance. By analyzing this data, manufacturers can detect trends, address issues, and make informed decisions.
Using monitoring tools and manufacturing software enables proactive quality management, ensuring continuous improvements in production.
Simplify Quality Control in Manufacturing with HashMicro Software
Ensuring quality control in manufacturing can be a complex task, but with the right tools, the process becomes more efficient and precise.
HashMicro’s manufacturing software is designed to streamline operations, enhance accuracy, and maintain consistent product quality. Here’s how HashMicro simplifies quality control:
- Automated quality checks: HashMicro automates routine inspections, reducing human error and maintaining consistent quality standards. With real-time monitoring and reporting, manufacturers can quickly detect and resolve issues.
- Data driven insights: Advanced analytics provide valuable insights from collected data, helping manufacturers identify trends, optimize workflows, and make well-informed decisions.
- Seamless workflow integration: The software integrates smoothly with other production systems, ensuring a unified workflow. This reduces redundancy, improves team coordination, and enhances overall efficiency.
- Customizable reporting: HashMicro enables manufacturers to generate detailed reports tailored to specific needs. These reports offer a comprehensive view of key metrics, helping businesses track.
With HashMicro’s ERP manufacturing software, businesses can enhance quality control, improve productivity, and achieve greater operational efficiency.
Conclusion
Recognizing the importance of quality control is crucial for companies striving to maintain consistent product standards, enhance customer satisfaction, and stay competitive.
Effectively implementing quality control measures can streamline operations, lower costs, and build stronger client trust. However, managing these processes efficiently requires the right technology.
HashMicro’s advanced manufacturing software offers a complete solution for optimizing. With automation, real-time monitoring, and enhanced accuracy, businesses can ensure continuous improvement throughout production.
Discover how HashMicro can enhance your business strategies with advanced automation and seamless integration. Schedule a free demo today and experience improved efficiency, accuracy, and productivity
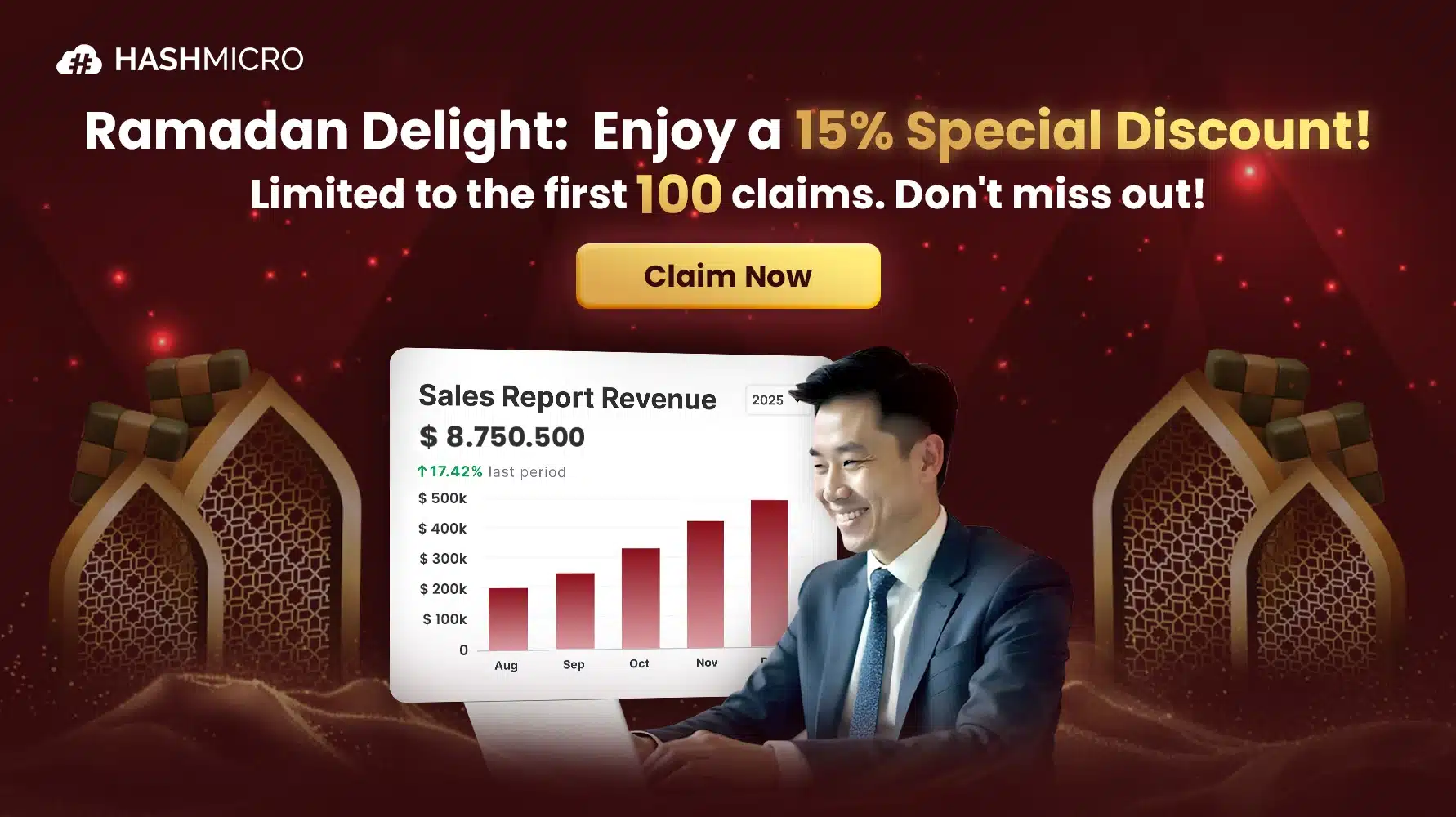
FAQ Quality Control
-
What are the 4 types of quality control?
The four types of quality control are process control, control charts, acceptance sampling, and product. While a control chart helps study changing processes over time, process control and product help monitor and adjust products as per the standards.
-
What is the QA QC plan?
Starting a quality assurance and quality control (QAQC) program on your new construction project is essential to ensuring that you deliver a successful project that conforms to the project design, meets customer requirements and complies with local building codes.
-
What is the QC process?
The QC process involves identifying standards for quality, regularly reviewing products to ensure they meet those benchmarks and removing any products that don’t meet quality expectations.