As an inventory professional, you likely already know how crucial raw materials are for smooth business operations. Poor raw material management can trigger specific issues like production delays, profit loss from shortages, or increased storage costs due to excess stock.
Raw material inventory refers specifically to the company’s stored materials that have not yet entered the production cycle. These can include any basic supplies or components still waiting to be turned into finished goods.
But even if you understand the basic definition, do you still wonder exactly why mastering raw material inventory management matters for your company, or how to effectively apply these concepts? Keep reading this article to gain valuable insights and practical knowledge!
Key Takeaways
|
Table of Content
Content Lists
What is Raw Material Inventory?
Raw material inventory refers to the assessed value of a company’s fundamental components used in the production and manufacturing of its goods. These materials, often termed as “pre-production inventory,” are stocked and ready for use.
Businesses typically classify raw materials as a current asset on financial statements like the balance sheet, given their role in contributing to a manufacturer’s total product inventory.
Raw materials are further divided into two categories:
- Direct materials: These are materials that become an integral part of the final product. For instance, in the production of blankets, the fabric or textile used in crafting the blanket would be considered a direct material.
- Indirect materials: These materials are used during production but cannot be easily quantified as part of the final product. For example, in the manufacturing of clocks and watches, the oil applied to lubricate gears would be classified as an indirect material.
Methods to Manage Raw Materials Inventory
Having covered the definition of raw materials inventory, we will now explore the common techniques used to manage it efficiently. Below are several widely adopted methods:
1. Just-in-Time (JIT)
The JIT method focuses on minimizing stored raw materials by ordering only what is needed for production. This ensures that materials arrive precisely when required, reducing storage costs and preventing excess inventory.
While this approach helps eliminate waste, it demands strong coordination with suppliers to prevent delivery delays.
2. Economic Order Quantity (EOQ)
EOQ is a strategy for determining the ideal order quantity to minimize overall inventory costs, including storage, ordering, and stock shortage expenses.
Businesses apply a mathematical formula to balance ordering frequency with storage costs, ensuring an optimal inventory management approach.
3. ABC Analysis
This method classifies raw materials based on their value and usage. Typically, materials are divided into three categories:
- A: High-value, low-volume items
- B: Medium-value, medium-volume items
- C: Low-value, high-volume items
With this approach, businesses prioritize stricter control over Category A items to prevent shortages and manage costs efficiently, while allocating resources appropriately across all inventory groups.
4. First-In, First-Out (FIFO)
FIFO ensures that the oldest raw materials in storage (first-in) are used first in production (first-out). This method is especially beneficial for perishable materials, such as food and pharmaceuticals, to prevent spoilage and expiration.
5. Material Requirements Planning (MRP)
MRP is a computerized system that determines raw material needs based on production schedules.
By factoring in existing orders, production timelines, and delivery schedules, MRP ensures the availability of necessary materials in the right quantities and at the right time. Hence, shortages, dead stock, and overstocking can be prevented more readily.
How to Calculate Raw Material Inventory
There are different ways to calculate raw material inventory, depending on the goal—whether it’s determining the total inventory value or analyzing how quickly raw materials are used. Below are two common methods:
1. Calculating the Value of Raw Material Inventory
To find out how much your raw materials are worth at the end of a specific period, use this formula:
Raw Material Inventory Value = Initial Inventory + Purchases During the Period – Ending Inventory
Here’s what each term means:
- Initial Inventory: The amount of raw materials available at the start of the period.
- Purchases During the Period: The total raw materials bought during that time.
- Ending Inventory: The remaining raw materials at the end of the period.
This formula helps businesses determine the total value of materials still available for production.
2. Calculating the Inventory Turnover Ratio
To measure how efficiently raw materials are used in production, calculate the inventory turnover ratio with this formula:
Inventory Turnover Ratio = Cost of Raw Materials Used ÷ Average Raw Material Inventory
- A higher ratio means raw materials are being used quickly, which indicates efficient production but could lead to shortages if not managed properly.
- A lower ratio suggests that materials are sitting in storage for too long, which may increase storage costs and reduce efficiency.
Example of Calculating Raw Material Inventory for a Malaysian Business
Let’s apply these formulas to Gardenia Bakeries (Malaysia) Sdn. Bhd., one of the largest bread and bakery product manufacturers in Malaysia. The company relies on raw materials like flour, yeast, sugar, and butter to produce its bread and baked goods.
1. Calculating the Value of Raw Material Inventory
Suppose Gardenia wants to determine the total value of raw materials at the end of the month. Here’s the data:
- Initial Inventory (Raw materials at the start of the month): RM 2 million
- Purchases During the Period (New raw materials bought): RM 5 million
- Ending Inventory (Remaining raw materials at the end of the month): RM 1.5 million
Applying the formula:
Raw Material Inventory Value = Initial Inventory + Purchases – Ending Inventory
= RM 2 million + RM 5 million – RM 1.5 million
= RM 5.5 million
This means that at the end of the month, Gardenia’s total raw material usage is worth RM 5.5 million.
2. Calculating the Inventory Turnover Ratio
Now, let’s find out how efficiently Gardenia uses its raw materials.
- Cost of Raw Materials Used (Total materials consumed in production): RM 5.5 million
- Average Raw Material Inventory (Initial Inventory + Ending Inventory ÷ 2):
(RM 2 million + RM 1.5 million) ÷ 2 = RM 1.75 million
Applying the formula:
Inventory Turnover Ratio = Cost of Raw Materials Used ÷ Average Raw Material Inventory
= RM 5.5 million ÷ RM 1.75 million
= 3.14
What does this mean?
Gardenia’s inventory turnover ratio of 3.14 means that the company uses up and replaces its raw materials about 3 times within a month.
- A turnover ratio above 3 is generally a good sign, showing that materials are moving quickly and not sitting in storage for too long.
- If the ratio were too high (e.g., above 6), it might indicate a risk of stock shortages, which could disrupt production.
- If the ratio were too low (e.g., below 2), it could mean excess inventory, leading to higher storage costs and potential waste.
By analyzing these numbers, Gardenia can make better purchasing decisions, reduce waste, and maintain an efficient supply chain to keep its bread production running smoothly.
Tips to Manage Raw Material Inventory
Here are some effective ways to manage raw material inventory efficiently:
1. Automate Inventory Tracking and Management
In manufacturing and production, automating inventory management software can significantly improve efficiency. Using specialized software or digital systems helps businesses track and organize raw material data, forecast inventory needs, and estimate production costs.
However, do you wonder how much an inventory management system costs? Why don’t you click on the pricing scheme below to get your customized quote?
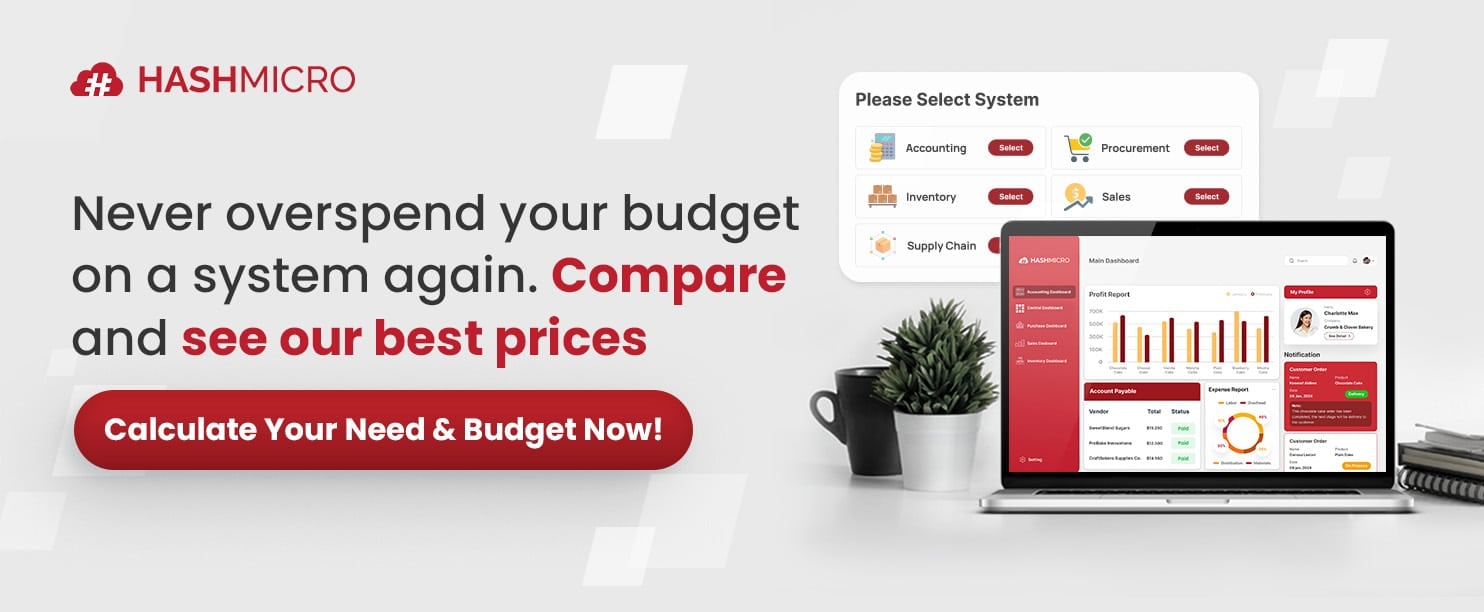
2. Identify and Address Overstock or Understock Issues
Overstocking means having more raw materials than needed, while slow-moving inventory leads to shortages that can disrupt production. If a company struggles with inventory control, it can take steps to resolve the issue, such as:
- Reviewing sales forecasts for accuracy
- Setting clear reorder points for safety stock
- Communicating with suppliers about potential delays
- Analyzing seasonal trends to anticipate demand shifts
3. Prioritize High-Quality Raw Materials
Using superior-quality raw materials can improve production efficiency, reduce costs, and enhance customer satisfaction. Low-quality materials may cause manufacturing issues, such as defects or inconsistencies, leading to delays and increased waste.
While high-quality materials may have a higher upfront cost, they often result in fewer production problems, better product reliability, and long-term cost savings.
Make Raw Material Inventory Management Effective with HashMicro’s System
Managing raw material inventory can be complex, but HashMicro’s inventory management system makes it easier than ever. As one of the top solutions in Malaysia, HashMicro helps businesses sort their stocks and boost efficient inventory and warehouse management.
One standout advantage? No user limitations! Multiple team members can oversee inventory at the same time. It also connects effortlessly with accounting, HRIS, warehouse storage, and more. Plus, as your business expands, the system can scale, so no need to change the system!
Sounds like the perfect solution for your business? Here’s what HashMicro’s inventory system has to offer:
- RFID Warehouse Rack Stock In-Out Automation: The system uses RFID technology to automatically detect and record stock movements as items enter and exit warehouse racks.
- Run Rate Reordering Rules: The system analyzes sales history and market trend data to accurately forecast product demand and automatically triggers reordering when stock reaches predetermined levels.
- Stock Reservations & Reporting: The system allows users to reserve specific quantities of items in advance and generates detailed inventory reports to track item availability.
- Consignment Management: The system tracks consignment inventory by automatically updating stock levels, recording sales transactions, and calculating consignor payments.
Conclusion
Raw material inventory is essential for smooth production, preventing shortages, and minimizing excess stock. Managing it well keeps costs low and operations efficient.
With HashMicro Inventory System, businesses get real-time tracking, automation, and seamless integration for effortless inventory control. No more stock issues; just smarter, faster management.
Why struggle with manual tracking when HashMicro simplifies everything for you? Gain real-time inventory insights, automated reordering, and complete transparency across your supply chain.
Upgrade today with the free demo and take control of your inventory like never before!
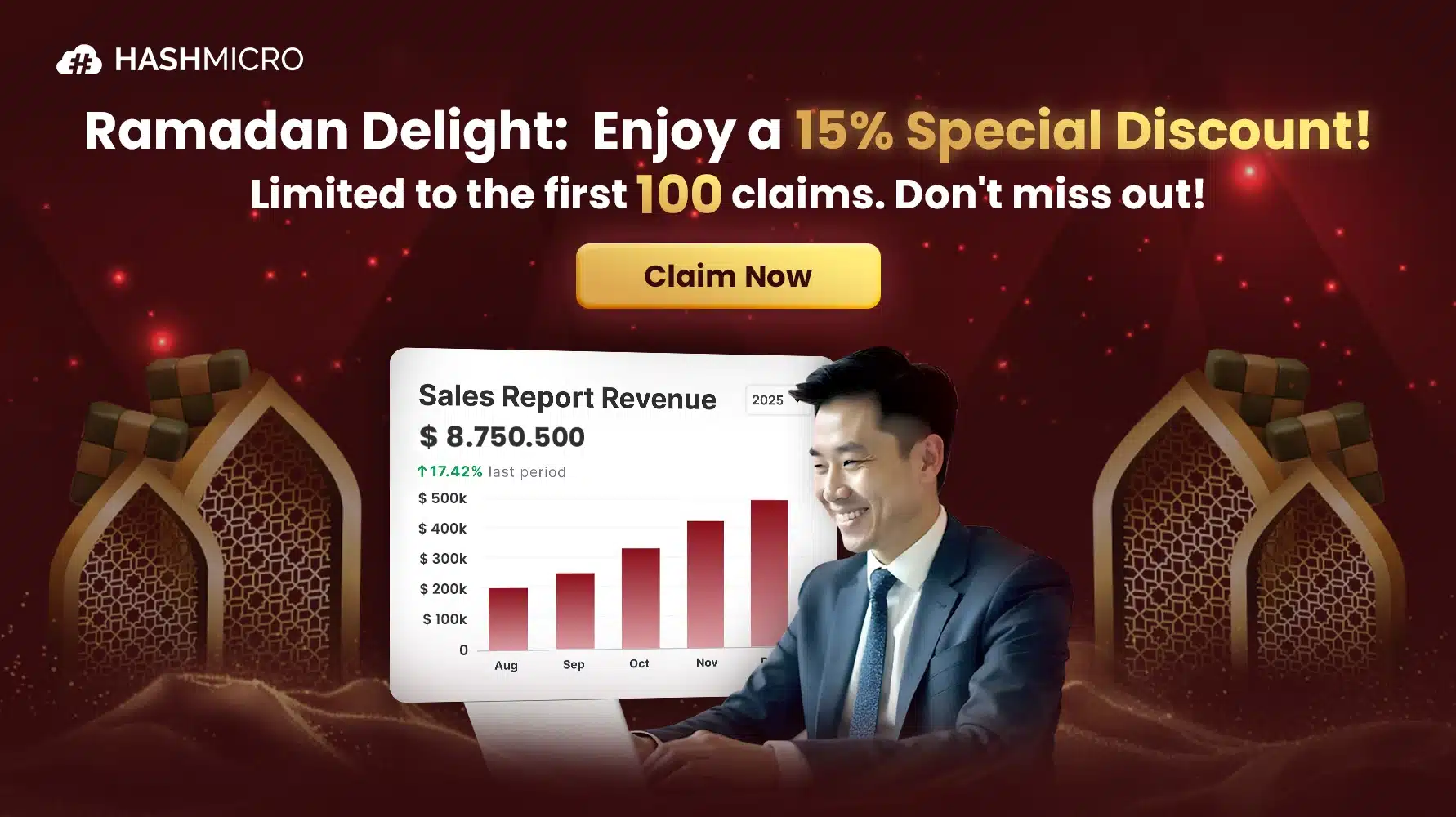
Frequently Asked Questions on Raw Material Inventory
-
How does raw material inventory affect a company’s cash flow?
Buying too many raw materials can tie up money that could be used for other business needs. Managing inventory well ensures there’s enough cash for daily operations.
-
What is the role of raw material inventory in supply chain management?
Raw materials are the first step in making products, so they affect production speed and delivery times. Keeping the right amount ensures smooth operations.
-
What are the risks of holding too much raw material inventory?
Storing too many raw materials takes up space, increases costs, and some materials might expire or become outdated. Keeping only what’s needed helps avoid waste.
-
How can technology improve raw material inventory management?
Using tools like barcode scanners or automated tracking helps businesses know what they have in stock. This reduces mistakes and makes inventory control easier.