Are you facing high logistics costs and inefficient inventory management? Or are slow distribution and delivery delays affecting your business performance? These challenges can lead to higher expenses and reduced efficiency in your supply chain.
Warehouse clustering solves your needs by allowing businesses to streamline distribution, reduce costs, and improve efficiency through strategically grouping warehouses. A proper warehouse management system (WMS) optimizes inventory tracking, speeds up order fulfillment, and maximizes productivity.
Discover how warehouse clustering can transform your logistics strategy. Read on to explore its benefits and how it can drive better supply chain performance for your business.
Table of Content
Content Lists
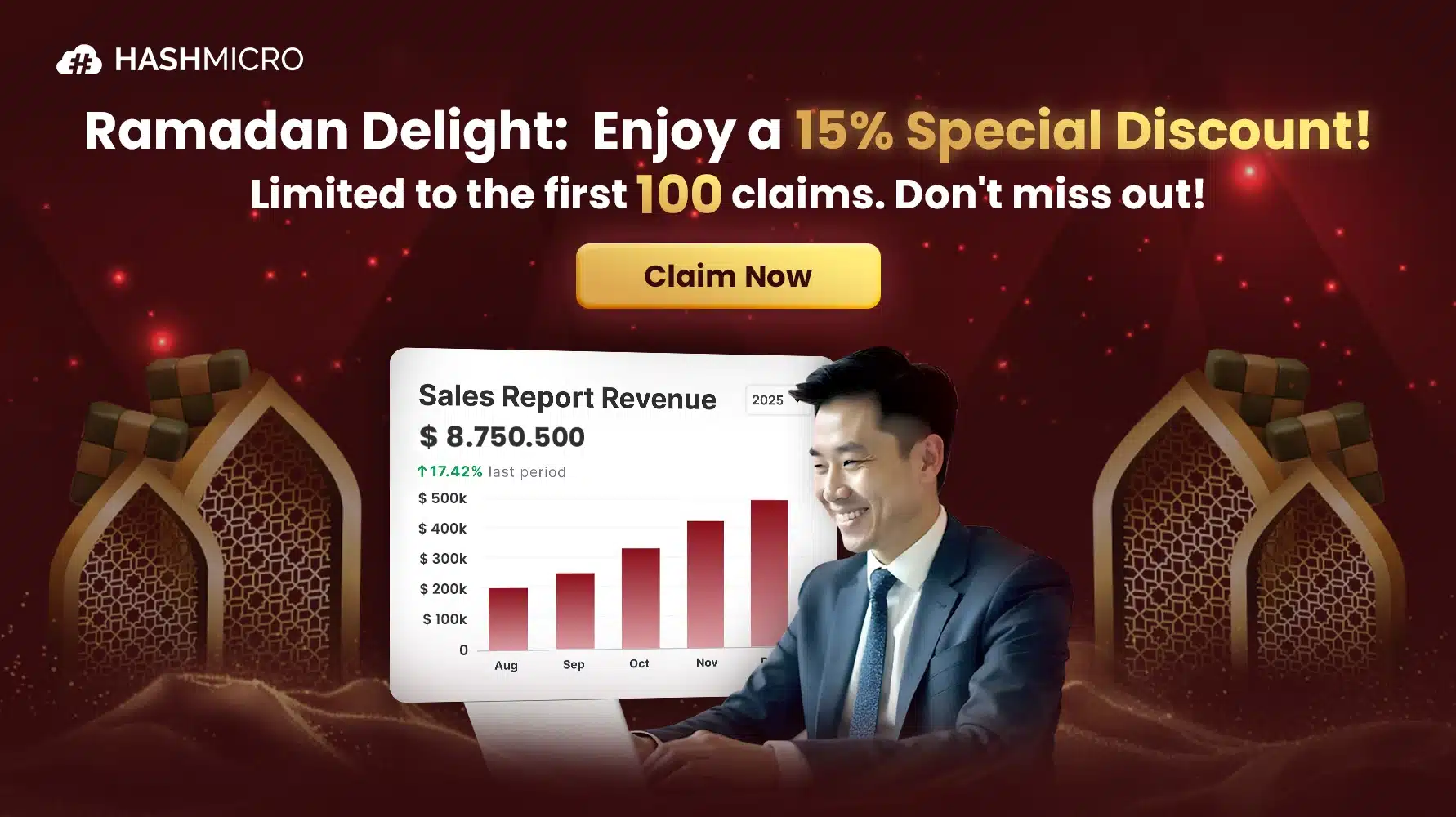
Key Takeaways
|
What is Warehouse Clustering?
Warehouse clustering is a strategy in which multiple warehouses are grouped to improve logistics efficiency, reduce costs, and enhance supply chain performance. It allows businesses to leverage shared resources and optimize their logistics operations.
This approach is widely used across various industries. Here are the different sectors that implemented warehouse clustering.
- E-commerce and retail businesses rely on warehouse clustering to increase order fulfillment and maintain stock availability.
- Manufacturing companies use it to store raw materials and finished goods efficiently.
- Clustered warehouses benefit fast-moving consumer goods (FMCG) brands by ensuring steady product distribution to supermarkets and retailers.
- Pharmaceutical and healthcare providers utilize warehouse clusters to store and distribute medicines quickly, ensuring a reliable supply for hospitals and pharmacies.
- Logistics and third-party warehousing (3PL) companies optimize their last-mile delivery using this strategy.
- Agriculture and food supply chains use cold storage clusters near major ports like Port Klang to preserve perishable goods and facilitate smoother import-export processes.
Types of Warehouse Clustering
Warehouse clustering can be categorized into different types based on industry needs, warehouse functions, geographic locations, and ownership structures. Below are the key types of warehouse clustering and how they contribute to optimizing logistics and distribution.
1. Industry-specific clustering
Industry-specific clustering involves grouping warehouses based on the sector they serve. Different industries have unique warehousing requirements, such as temperature-controlled storage for food supply chains or high-volume fulfillment centers for e-commerce, which can be further optimized with e-commerce fulfillment software to enhance efficiency and accuracy.
For example, cold storage clusters are essential for perishable goods like seafood, dairy, and frozen foods, ensuring proper preservation and minimizing spoilage. This type of clustering enhances efficiency by placing warehouses closer to manufacturing plants or distribution points.
2. Functional clustering
Functional clustering categorizes warehouses based on their roles within the supply chain. Organizing warehouses based on function allows businesses to streamline operations and optimize logistics flows. Here are several examples of functional clustering.
- Bonded warehouses. Bonded warehouse stores imported goods without immediate duty payments, helping businesses manage customs clearance efficiently.
- Fulfillment centers, commonly used in e-commerce, focus on rapid order processing and last-mile delivery.
- Distribution centers store large inventories for bulk shipments to retailers.
Container warehouses handle shipping containers before further distribution.
3. Geographic clustering
Geographic clustering involves placing warehouses in strategic locations to enhance transportation efficiency. Logistics hubs near major highways, ports, and urban centers reduce transit times and lower distribution costs.
For instance, warehouse clusters near Port Klang in Malaysia facilitate smooth import-export processes, enabling businesses to move goods efficiently. This clustering helps companies optimize delivery routes, minimize transportation expenses, and ensure faster market access.
4. Ownership-based clustering
Ownership-based clustering classifies warehouses based on who owns and operates them. There are two examples of ownership-based clustering.
- Private clusters consist of warehouses owned by a single company for its internal logistics needs, allowing full control over operations.
- Third-party logistics (3PL) clusters are managed by providers serving multiple businesses, offering shared storage, transportation, and distribution. It is ideal for companies aiming to lower warehousing costs while gaining specialized logistics expertise.
Benefits Of Warehouse Clustering in Logistics
Warehouse clustering offers numerous advantages that enhance logistics efficiency and cost-effectiveness. Below are the benefits of implementing warehouse clustering.
- Reduced transportation costs
Minimizing distances between clustered warehouses lowers transportation costs by reducing fuel and logistics expenses. Shorter routes improve delivery efficiency, cutting transportation time. Additionally, less fuel use decreases carbon emissions, promoting sustainable logistics. - Improved supply chain efficiency
Improved supply chain efficiency speeds up goods movement, reducing delays and enhancing fulfillment. Shorter lead times allow businesses to meet customer demands quickly. This streamlined process prevents disruptions and boosts overall performance. - Better inventory management
Consolidating warehouses and improving stock visibility enhances inventory management. Businesses can track levels accurately, preventing stockouts and excess storage. Better stock rotation optimizes product distribution, reducing waste and inefficiencies. - Shared resources and cost savings
Warehouses sharing labor, equipment, and facilities reduce operational expenses and enhance resource flexibility, improving distribution efficiency. Businesses enjoy lower infrastructure costs while maintaining high efficiency. - Enhanced customer satisfaction
Faster delivery times and consistent product availability enhance customer satisfaction. Well-organized warehouse clustering reduces delays, ensuring timely order fulfillment. Customers receive their products on time, improving reliability and strengthening brand reputation.
Strategies of Warehouse Clustering
Efficient warehouse clustering requires strategic planning to optimize logistics operations and reduce costs. Implementing the right strategy ensures smoother supply chain operations and better resource utilization. Below are the methods of warehouse clustering.
- Cross-docking strategy
Cross-docking reduces storage time by transferring goods directly from inbound to outbound shipments. This method lowers warehousing costs and speeds delivery for perishable or fast-moving products, making it popular in e-commerce, retail, and food supply chains. - Consolidation centers
Consolidation centers enhance supply chain warehouse consolidation by merging small shipments from various suppliers into larger ones, lowering distribution costs and trips. This method benefits businesses by improving bulk shipment coordination. - Hub-and-spoke model
The hub-and-spoke model uses a central warehouse to distribute goods to regional warehouses, optimizing inventory and reducing delivery times. This approach enhances distribution efficiency and customer service in e-commerce, retail, and manufacturing.
How Warehouse Clustering Improves Supply Chain Efficiency
Efficient warehouse clustering uses strategic logistics planning and advanced technologies to optimize supply chain operations. Below are the ways warehouse clustering improves supply chain efficiency.
- Optimizing transportation routes
Warehouse clustering reduces transit distances by locating warehouses near suppliers and markets, leading to lower fuel use, transportation costs, and quicker deliveries. Minimizing travel helps streamline logistics and improve supply chain efficiency. - Enhancing inventory distribution
Warehouses help businesses manage inventory efficiently, avoiding stockouts in high-demand areas and overstock in low-demand ones. Warehouse network optimization ensures balanced distribution, enabling faster replenishment and better order accuracy. - Leveraging warehouse management systems (WMS) and automation
Advanced WMS and automation improve warehouse coordination through real-time inventory tracking and automated workflows. They enhance picking, sorting, and packing efficiency, reduce errors, and ensure smooth operations and better supply chain visibility. - Improving collaboration between warehouses
Warehouse clustering enables businesses to share resources, reducing costs and enhancing scalability. This approach helps manage seasonal demand fluctuations and boosts overall productivity.
Warehouse clustering requires effective strategies and technologies for efficiency and cost savings. Companies should invest in solutions for smooth transitions. Download our pricing scheme for tools that enhance warehouse clustering and supply chain efficiency.
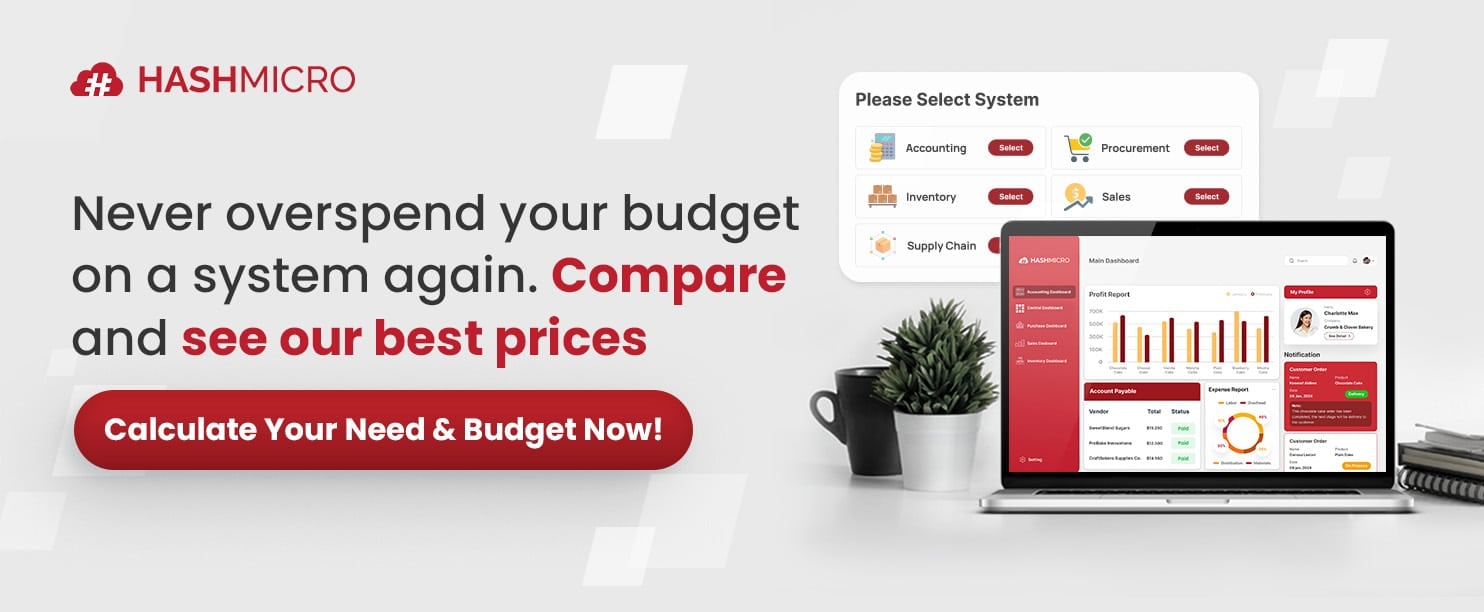
Best Practices for Implementing Warehouse Clustering
Businesses must adopt strategic warehouse clustering to maximize efficiency and cost-effectiveness in supply chain management. Here are ten best practices to successfully implement warehouse clustering.
1. Define clear objectives
Before clustering warehouses, set clear goals like improving delivery speed, lowering costs, or enhancing inventory management. These objectives ensure clustering strategies align with business needs and customer expectations, offering measurable benefits.
2. Analyze demand patterns
Understanding customer demand by region is crucial for effective clustering. Analyzing sales data helps businesses identify high-demand areas, optimize warehouse placement, reduce stockouts, and enhance order fulfillment.
3. Utilize data-driven approaches
Using data analytics and AI, businesses can make informed decisions about warehouse clustering. By grouping warehouses by geographic proximity, order frequency, and shipping costs, companies improve efficiency and reduce waste.
4. Optimize warehouse locations
Strategically placing warehouses near key markets, suppliers, and transportation hubs reduces logistics costs and delivery times. Proper location planning ensures inventory is stored close to demand centers, improving responsiveness and customer satisfaction.
5. Implement an efficient inventory allocation strategy
Distributing inventory across warehouses balances stock and prevents shortages or overstock. Companies enhance supply chain efficiency and reduce costs by placing high-demand items in multiple locations and consolidating slow-moving products.
6. Improve technology integration
Investing in WMS and ERP enhances visibility, automation, and coordination, improving inventory tracking, order processing, and logistics for smoother operations and better decisions.
7. Enhance transportation and logistics coordination
Optimizing transport routes and logistics reduces transit times and fuel costs. Centralized planning tools and real-time tracking enhance last-mile delivery efficiency and decrease shipping expenses.
8. Foster collaboration between warehouses
Facilitating communication and data sharing between warehouses improves resource use. Cross-warehouse fulfillment, stock transfers, and coordinated replenishment enhance flexibility and minimize supply chain disruptions.
9. Conduct regular performance evaluations
Monitoring KPIs like order fulfillment, storage efficiency, and transportation costs identifies areas for improvement. Regular audits and data analysis help businesses refine clustering strategies and adapt to market changes.
10. Adapt to market changes
Warehouse clustering must be flexible and responsive to economic shifts, customer behavior, and technological advancements. Companies that regularly review and adjust their strategies can remain competitive and maintain long-term efficiency and profitability.
Utilizing Technology for Effective Warehouse Clustering
Technology is vital in optimizing warehouse clustering by improving efficiency, reducing costs, and enhancing decision-making. Below are the ways technology is used for effective warehouse clustering.
- Warehouse management systems (WMS)
A warehouse management system enhances clustering, optimizes inventory tracking, and improves order fulfillment. It also enables an efficient stock management in a multi-warehouse distribution system, monitors shipments, reduces errors, and improves supply chain coordination. - Automation
Automation enhances warehouse management by reducing manual labor and boosting efficiency. Robotics and automated systems accelerate processes while minimizing errors. Automating picking, packing, and storage raises throughput and lowers labor costs. - Data analytics
Data analytics improves warehouse clustering with real-time insights for informed decisions. Predictive analytics forecasts demand, optimizes inventory, and cuts holding costs. Identifying bottlenecks refines layouts and boosts logistics efficiency.
Enhancing Warehouse Clustering through Hashmicro’s Warehouse Management System
Optimizing warehouse clustering is crucial for efficient storage and distribution as businesses grow. HashMicro’s Warehouse Management System boosts efficiency by automating workflows, enhancing inventory accuracy, and streamlining order fulfillment across locations.
Here are the key features that make HashMicro’s WMS a powerful solution for warehouse clustering:
- Product dimension tracking: Monitor each item’s height, width, and weight to determine the best storage location and maximize space utilization.
- Location dimension management: Automatically calculate warehouse space availability and adjust storage based on product size and capacity.
- Putaway strategy settings: Set optimized storage strategies to ensure newly received inventory is placed in the most efficient locations for faster retrieval.
- Putaway capacity checking: Track and manage warehouse capacity in real time, ensuring products are assigned to the most suitable storage bins.
- Warehouse pallet racking: Organize shelving efficiently by categorizing racks based on product type and function, improving warehouse navigation and accessibility.
- Warehouse in-depth reporting: Access comprehensive analytics and reports to evaluate warehouse performance and improve operational efficiency.
Conclusion
Warehouse clustering enhances logistics efficiency by strategically grouping warehouses to reduce costs and optimize supply chain operations. This approach enables businesses to improve inventory management and streamline distribution, making it a crucial strategy for competitive growth.
Implementing an advanced warehouse management system (WMS) is essential to maximizing the benefits of warehouse clustering. HashMicro WMS offers comprehensive solutions for inventory tracking and warehouse automation, ensuring seamless operations and improved efficiency.
Sign up for a free demo to explore how it can enhance your supply chain performance and drive business success. Take the first step toward smarter warehouse management now!
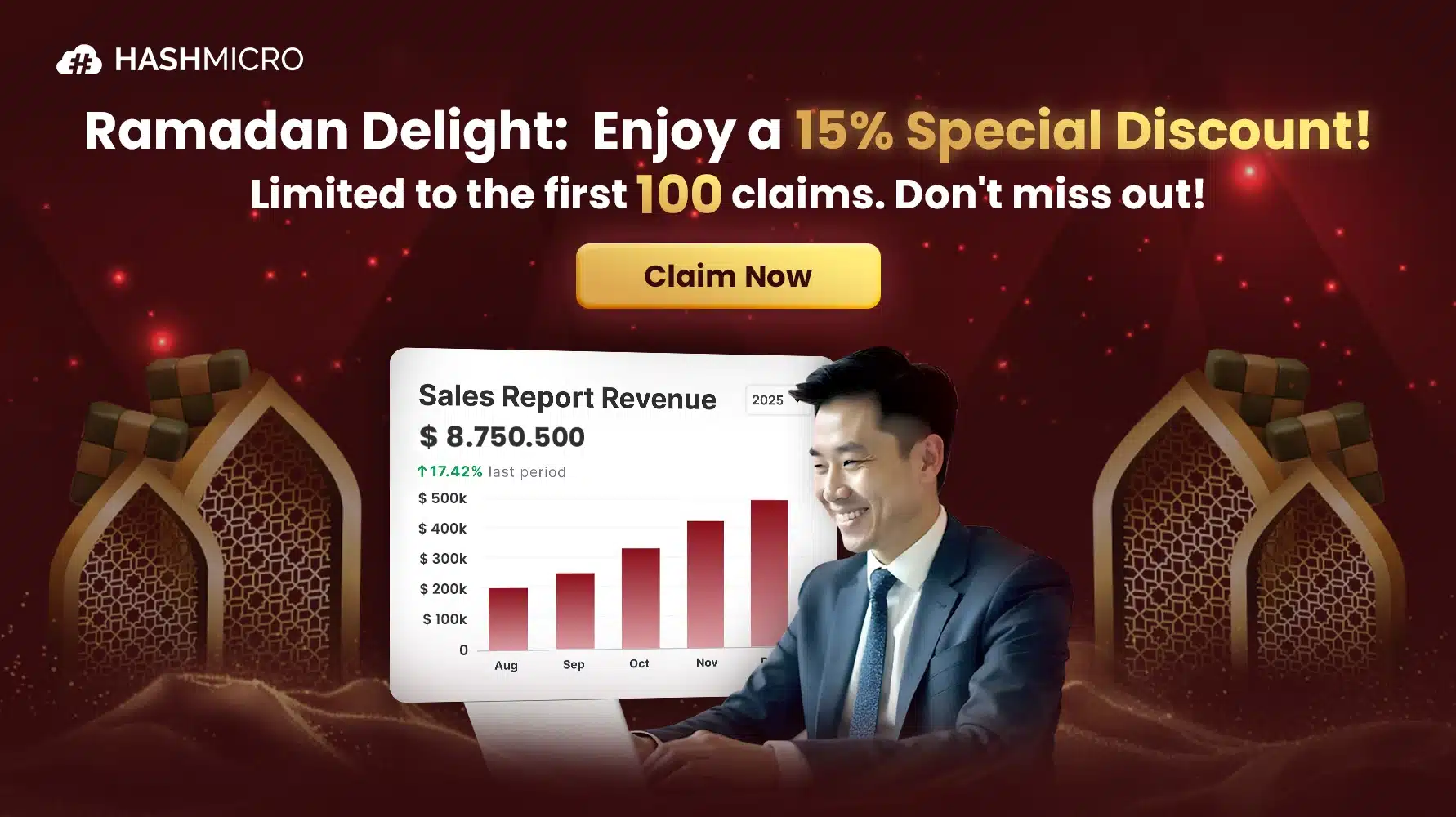
Frequently Asked Questions About Warehouse Clustering
-
What is clustering in a warehouse?
Clustering is one of the few warehousing strategies that consider the relationships between goods. These relationships should be prioritized over stock or product expiration dates.
-
What is a multi-cluster warehouse?
A multi-cluster warehouse enables more users to connect to the same-sized warehouse. It also eliminates the need to resize the warehouse or start and stop additional warehouses to handle fluctuating workloads.
-
What is a cluster system in the data warehouse?
Cluster analysis, also known as clustering, is a data mining method that groups similar data points. The goal of cluster analysis is to divide a dataset into groups (or clusters) such that the data points within each group are more similar than data points.