An effective putaway process is a critical component of warehouse management as it ensures inventory is well-organized, making products easily accessible and reducing picking time. Conversely, poor putaway practices can disrupt operations, waste time, and pose safety hazards to your team.
Inefficiencies in this process can significantly affect overall warehouse productivity. Implementing a well-structured putaway system is crucial to avoid backorders and stock shortages and ensure employee safety. This is especially important for achieving success in Singapore’s highly competitive business environment.
This article will explore various putaway methods and their benefits, review different strategies, and highlight how Warehouse Management Software (WMS) can optimize your putaway operations.
Table of Content
Content Lists
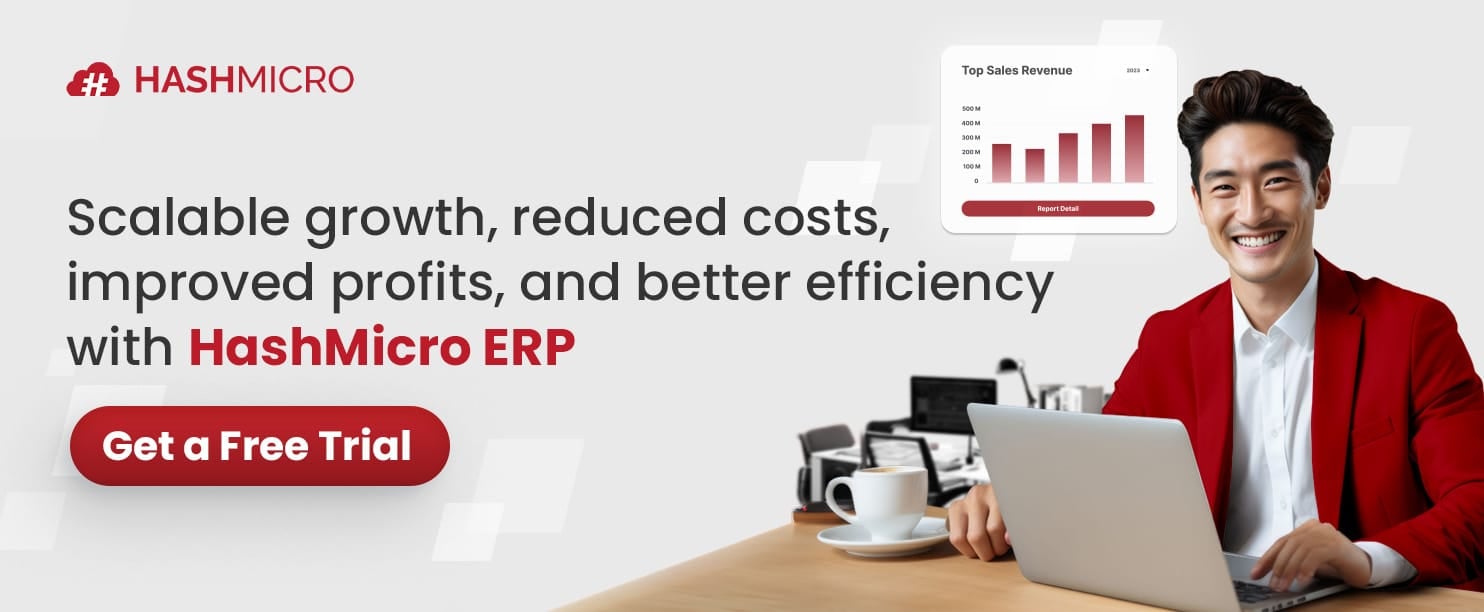
Key Takeaways
|
What is Putaway?
Putaway is a key process in warehouse operations that involves moving items from the receiving area to their designated storage locations. It marks the beginning of the inventory management cycle ensuring that products are stored in an organized and systematic manner.
The putaway process helps optimize warehouse space and streamline future operations by placing goods in specific locations based on their characteristics, such as size, weight, and demand patterns.
This careful organization improves efficiency, reduces errors, enhances safety, and lays the foundation for effective inventory control.
Major Benefits of Implementing Putaway Systems in Your Warehouse
Adopting an efficient putaway process in your warehouse provides various benefits that can transform inventory management from a challenging task into a valuable strategic asset. These advantages include:
- Maximized space utilization: Efficient warehouse putaway strategies ensure optimal use of available storage space. By organizing inventory systematically, you can increase storage capacity and eliminate unnecessary clutter.
- Enhanced inventory accuracy: Properly stored goods improve inventory tracking and management, reducing the risk of overstocking or stockouts and maintaining ideal inventory levels.
- Boosted operational efficiency: A well-executed putaway process simplifies warehouse workflows, enabling faster product retrieval, quicker order fulfillment, and improved overall efficiency.
- Reduced risk of damage and loss: Correct storage practices protect goods from damage during handling and storage, helping to lower associated costs.
- Improved workplace safety: Effective putaway systems and organized order picking processes create a safer work environment by reducing the risk of accidents and injuries, ensuring the well-being of employees.
Types of Putaway Methods
Various putaway methods are used based on the nature of warehouse operations, the types of products being stored, and the strategies implemented. Below is an in-depth overview of some of the most commonly used warehouse putaway methods:
1. Purchase order-based putaway
This method organizes items based on their purchase order details. It is particularly suited for warehouses that handle large but infrequent shipments. Keeping items grouped according to purchase orders simplifies cross-referencing during audits and ensures that products from the same order are stored together.
This organization makes storage and retrieval more efficient when working with order-specific information.
2. SKU based putaway
This method organizes products based on their Stock Keeping Unit (SKU), making it ideal for warehouses with large and varied inventories. By grouping items according to their SKU, warehouses can track products more accurately, manage inventory more easily, and retrieve items quickly, particularly when dealing with numerous product variations.
This method is especially beneficial for enhancing accuracy and efficiency in the picking and restocking processes.
3. Product type based putaway
Organizing items by their product type improves both storage and retrieval efficiency. In this method, products are categorized based on their characteristics, making locating and accessing similar items easier.
This approach is particularly effective for warehouses that handle a diverse range of products, as it ensures each category has its own designated storage area, simplifying sorting and picking processes.
4. Directed putaway
Directed putaway is an efficient method for transferring goods directly from the receiving area to their designated storage locations. This approach reduces handling time and accelerates placing products in their storage spots.
To implement this method effectively, real-time, accurate data is crucial to ensure items are stored in the most suitable locations based on demand and available space. Directed putaway improves operational efficiency and minimizes the risk of human errors during storage.
Common Difficulties when Managing Putaways
The following is a more in-depth explanation of the four difficulties often faced in managing unused goods in a warehouse:
1. Lack of a Standardized System
One of the primary challenges in storage management is the lack of established procedures. Without clear guidelines for storing items, different workers may adopt varying methods, resulting in confusion and inconsistency in product placement.
In the absence of specific Standard Operating Procedures (SOPs) for various products and storage areas, items may be stored randomly, making it difficult to locate them when needed. This lack of organization also complicates inventory auditing and management, increasing the likelihood of human errors, such as misplaced or incorrectly recorded items.
2. Non-optimal space utilization
Inefficient use of storage space is a common issue in many warehouses. When items are not stored according to their characteristics, such as size, weight, or product type, it often leads to wasted space.
Larger items might occupy spaces that could be better used for smaller items, or low-demand products may be placed in prime, easily accessible areas, while high-demand items are stored in harder-to-reach spots.
3. Lack of real-time monitoring
The absence of technologies like Warehouse Management Systems (WMS), RFID, or barcode tracking can result in errors when monitoring product location and status. Without real-time updates, warehouse managers may struggle to pinpoint items’ locations or accurately determine stock levels.
This can lead to issues such as overstocking, stockouts, and picking process delays. Additionally, without access to real-time data, it becomes challenging to adapt to shifts in demand or adjust the distribution of goods. The lack of inventory visibility also complicates the auditing and reporting processes.
This mismanagement of space reduces storage capacity and disrupts workflow, as employees may need to find extra space or rearrange products manually. Poor space utilization also increases the risk of stacking items too high, which can compromise safety and productivity.
4. Improper placement of goods relative to demand
One common warehouse issue is storing high-demand or frequently picked items in hard-to-reach locations. This mistake slows the picking process, particularly when quick order fulfillment is required.
If demand patterns are not properly analyzed, high-turnover items might be placed in distant warehouse areas, leading to longer picking times and higher operational costs.
Ways to Improve the Putaway Process in Your Warehouse
Improving the putaway process is essential for boosting efficiency and productivity in warehouse operations. By streamlining this process, warehouses can enhance operational flow, minimize errors, and strengthen inventory management.
Below are several strategies to optimize the putaway process in your warehouse:
1. Leverage advanced technology
Integrating a Warehouse Management System (WMS) is one of the most efficient ways to enhance putaway operations. WMS software can automate and simplify various tasks, such as determining optimal storage locations based on real-time data, product attributes, and demand patterns.
One example of a robust WMS solution is HashMicro, which offers a wide range of features, including product dimension tracking, putaway strategy configuration, and warehouse pallet racking—interested in exploring the HashMicro system? You can try their free demo by clicking here.
2. Standardize putaway procedures
Establishing standardized operating procedures (SOPs) for the putaway process ensures that all warehouse staff follow consistent, optimized methods when handling and storing inventory.
These SOPs should include clear, detailed guidelines on handling different product types, the best storage techniques for maximizing space, and specific safety protocols to prevent damage or accidents.
By providing staff with structured workflows, you can create a more organized and efficient warehouse environment where tasks are carried out uniformly.
3. Invest in staff training
A skilled workforce is crucial for successfully implementing an optimized putaway process. Employees should receive regular training on the latest warehouse techniques, technologies, and safety protocols.
Ongoing training sharpens their abilities in managing the putaway process and improves their adaptability to new systems and technologies, like WMS.
By ensuring that staff are knowledgeable about the most current practices and tools, you can guarantee that the putaway process is carried out efficiently and with minimal errors.
4. Utilize cross docking when applicable
Cross-docking is an effective strategy for enhancing warehouse efficiency, particularly for time-sensitive or high-demand products. This approach involves moving items directly from the receiving dock to the shipping dock, skipping the usual storage phase.
Cross-docking is especially beneficial for goods that need to be shipped quickly. When used appropriately, it can free up valuable warehouse space and speed up the entire supply chain process by reducing handling time, labor, and storage costs.
Implementation of HashMicro Warehouse System for More Efficient Putaway Management
HashMicro Warehouse Management Software (WMS) provides an effective solution that simplifies and enhances the complexity of the putaway process. In addition to offering features tailored to putaway management, the system boasts a user-friendly interface, ensuring a smooth and quick implementation.
Moreover, this system can be seamlessly integrated with other platforms such as accounting, procurement, HRIS, and more. With this easy integration, you’ll be able to manage data from various departments on a single platform.
Here’s how HashMicro WMS can optimize your warehouse’s putaway operations:
- Automated data entry: HashMicro WMS utilizes barcode scanning and RFID technology to automate data entry, significantly reducing the time and errors associated with manual processes.
- Real time inventory tracking: With HashMicro WMS, you gain real-time insights into inventory levels and storage locations. This up-to-date visibility ensures goods are stored in optimal locations, streamlining the putaway process and boosting efficiency.
- Optimized storage recommendations: The system intelligently recommends ideal storage spots based on factors like product type, size, and frequency of access. This feature maximizes warehouse space utilization and speeds up retrieval times.
- Seamless integration with other systems: HashMicro WMS easily integrates with purchasing and supply chain platforms, providing a unified approach to inventory management. This alignment ensures that the putaway process is smoothly coordinated with overall warehouse and supply chain operations, enhancing efficiency across the board.
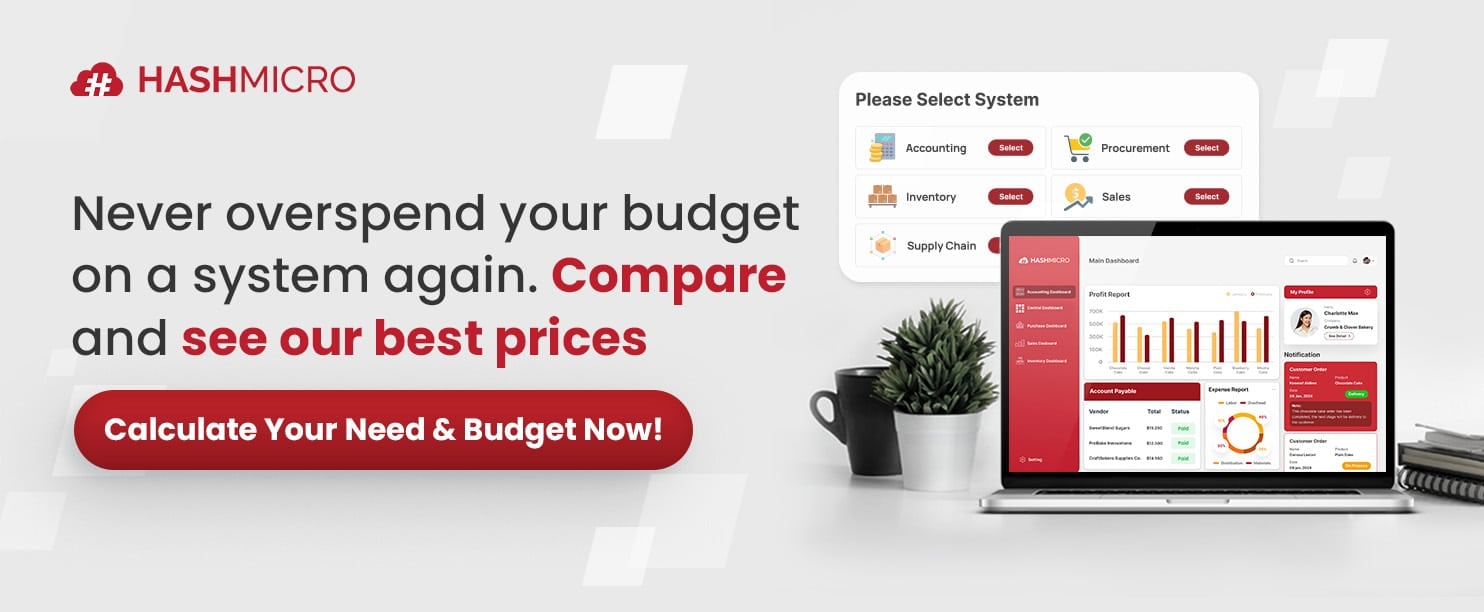
Conclusion
Integrating an effective putaway process with the advanced capabilities of HashMicro’s Warehouse Management System (WMS) in Malaysia can revolutionize how businesses manage their warehouses.
This robust system enhances efficiency, minimizes errors, and optimizes space utilization, ensuring your business stays ahead in a competitive market. A well-designed putaway process—whether organized by purchase orders, SKUs, product types, or direct placement—is essential for maintaining an efficient and organized warehouse.
When paired with HashMicro’s warehouse management system, these processes are further streamlined with features such as real-time tracking, reduced manual errors, and increased productivity.
To learn more about this cutting-edge warehouse management system in Malaysia, click the banner below!
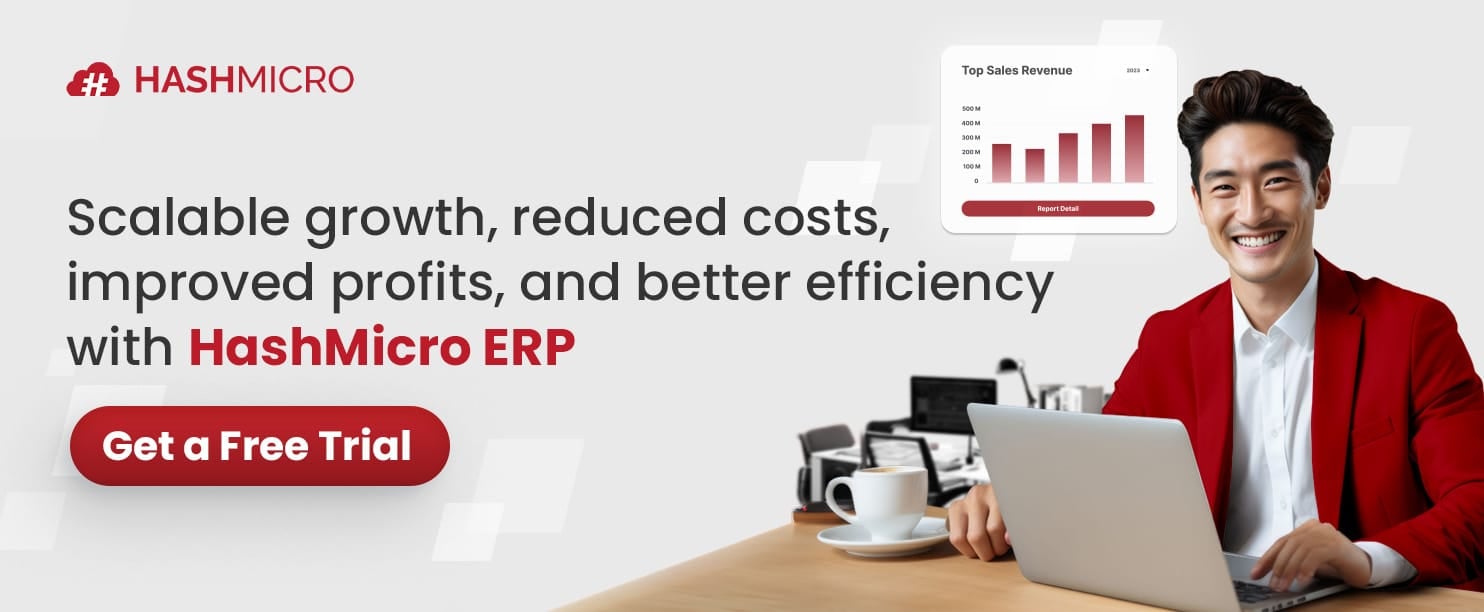
FAQ Warehouse Putaway
-
What are the activities of putaway?
What is Putaway Process in Warehouse? The putaway process in a warehouse refers to the activity of moving items from the receiving area to the storage area.
-
What is the receiving and putaway process?
Receiving and putaway processes go hand in hand in warehouse operations. As goods arrive, they must reach the receiving area and promptly move into their designated storage locations. Organization during this stage is vital to ensure products reach the right areas.
-
What is the major challenge during putaway?
If goods are stored in non-optimal locations, travel time during picking increases, delaying order fulfillment. Furthermore, improperly stored cargo can compromise the security of the products and pose safety risks for employees.