Managing a warehouse isn’t easy, especially when orders pile up and pickers waste time navigating messy workflows. Without a structured picking method like wave picking, the warehouse risks so many things, from a messy warehouse, lost items, to missing deadlines.
This is where wave picking makes a difference. Instead of relying on random order flows, this method organizes picking tasks into structured waves based on shared factors like shipping deadlines, product type, or warehouse zone.
However, as there are so many order picking systems a warehouse can implement, you need to determine whether wave picking is the right one for you or not. Thus, this article will give you a rundown on what wave picking is, the benefits and challenges, and tips to utilize it for your business.
Key Takeaways
|
Table of Content
Content Lists
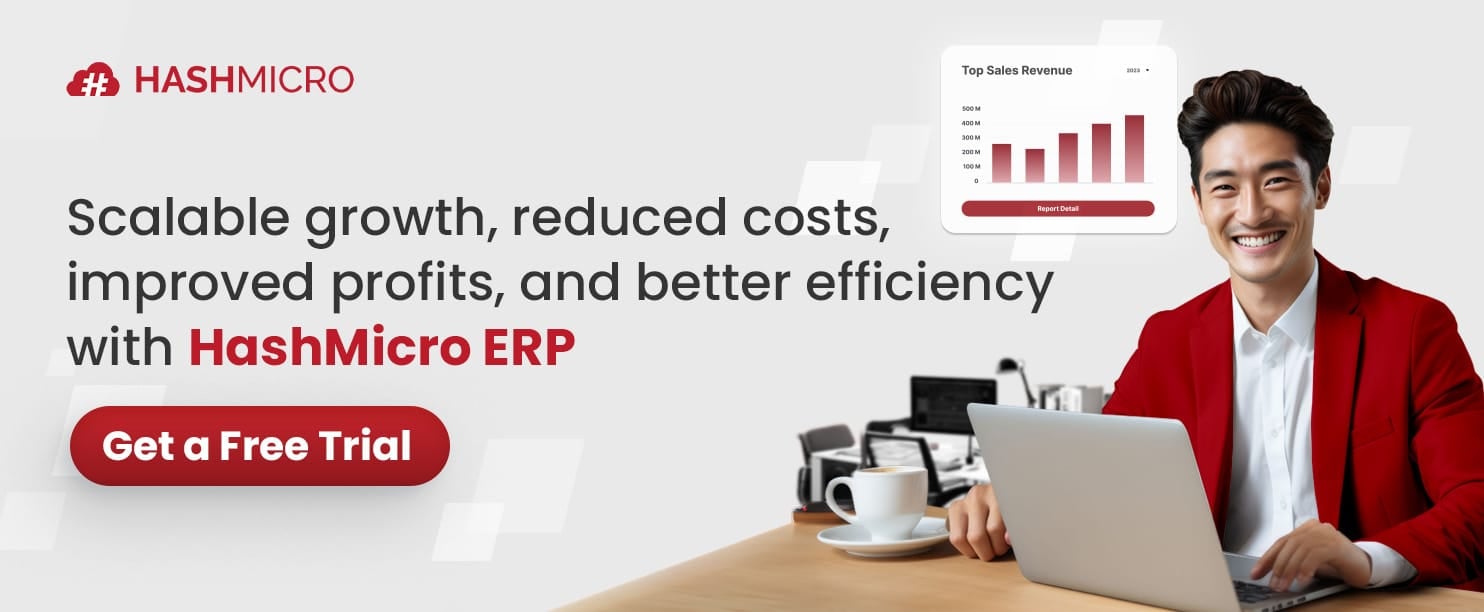
What is Wave Picking?
Wave picking, also called cluster picking, is a warehouse order picking method designed to enhance efficiency. It involves releasing orders for fulfillment based on shared factors like shipping date, item type, or warehouse zone.
Instead of assigning pickers per shift and relying on a steady order flow, wave picking ensures teams meet specific goals, such as completing a set number of orders per shift or hitting shipping deadlines.
This method prioritizes when orders are picked. Management schedules short picking intervals, or waves, that align with key warehouse operations like transportation plans or departure schedules.
Orders are grouped and picked at specific times, minimizing idle time for pickers. By waiting until all orders meet a set deadline before scheduling a wave, pickers avoid unnecessary downtime.
Wave Picking vs. Zone Picking
Wave picking differs from zone picking, which is based on where items are picked. However, the two methods can be combined in some warehouses. The way zones are structured depends on the warehouse size and product mix, with common setups including:
- Product type: Separating non-perishables from fresh produce.
- Risk factors: Keeping controlled substances in a secure zone.
- Packing needs: Grouping hazardous materials separately.
- Sales volume: Placing fast-moving items in one area and slower sellers in another.
Regardless of the setup, pickers are assigned to a specific zone and only retrieve SKUs from that area. This setup helps reduce worker travel time and prevents congestion.
How Does Wave Picking Work?
While wave picking is simple in concept, executing it can be complex since it requires coordination among multiple teams, including receiving, shipping, and freight carriers. To maximize efficiency, wave picking is typically broken down into three steps:
1. Pre-Wave Picking
This step involves scheduling waves based on key variables. Orders must be grouped and timed strategically, such as aligning with shipping deadlines. For example, if orders are grouped by shipping time, picking must allow enough lead time for packing before the carrier’s departure.
A warehouse management system (WMS) simplifies this process by automating scheduling, which would otherwise be time-consuming and difficult to manage manually.
2. Performing Wave Picking
This is the actual picking process, which is optimized using hand-held scanners that provide digital pick lists and direct pickers to product locations. These devices, when integrated with a WMS, help plan the most efficient pick routes while tracking progress.
Typically, wave picking follows these steps:
- A picker receives a pick list with 4-12 orders per wave.
- A multi-tote cart is used to keep orders separate.
- The picker follows an optimized route, retrieving items based on instructions from a mobile device.
- Each picked item is scanned for confirmation and placed in the correct tote.
- The process continues until all orders in the wave are completed.
3. Post-Wave Picking
Once picking is complete, orders need to be sorted and packed before shipping. If items were kept separate during picking, mobile scanners and tote systems make this step easier. If not, additional sorting time must be factored into the wave schedule.
The final step is loading and shipping the completed orders.
How are Waves Grouped?
How a company organizes waves depends on various factors and can change daily. This flexibility is a key advantage of wave order picking. Here are common ways waves can be grouped:
- Similar Products: The most common approach is grouping items of the same type, usually stored together in the warehouse.
- Shipping Schedules: Orders can be grouped by shipping method (e.g., ground, express, next-day) to ensure they are packed and ready for carrier pickup on time.
- Carriers: Since different carriers have unique pickup times, costs, and rules, grouping orders by carrier can save time and reduce shipping expenses.
- Replenishment Picking: High-demand SKUs stored off-site or in reserve areas need replenishment before picking begins. Scheduling these waves first prevents idle time.
- Shift Changes & Workforce Availability: Waves can be planned to match peak staffing hours or ensure completion before shift changes, reducing errors caused by handovers.
- Product Location & Type: Grouping orders by storage area or product similarity (e.g., bulky items, hazardous materials) can improve efficiency, especially with zone picking.
- Warehouse Priorities: Businesses may prioritize waves based on urgent orders, key customers, or perishable goods to meet specific needs.
These methods aren’t exclusive; companies can mix and adjust them as needed throughout the day. The key is to organize waves in the most logical way to maintain efficiency.
Wave Picking Methods
There are three types of wave picking in warehousing, each designed to optimize different workflows based on operational needs:
1. Bulk Pick
Bulk picking allows multiple orders to be picked at once based on product type rather than individual orders. This is useful for items in hard-to-reach areas or requiring equipment like forklifts. In this process, picking and packing are combined.
Once the picked quantity is confirmed in the system, the order status updates to “Packed.” A new product label and barcode can be printed, and the items are then moved to the dock or delivery truck for sorting.
2. Split Pick and Pack
This method is similar to bulk picking but separates the picking and packing processes. Items from multiple orders are picked together, but packing is done separately; either by the same user later or by a different team at a packing station.
This setup is ideal for warehouses where picking and packing take place in different areas or are handled by separate teams.
3. Combination Wave Pick
Combination wave scheduling groups multiple sales orders for the same customer or delivery run to be picked together. This ensures that all related orders are picked and packed at the same time for streamlined dispatch.
A 3PL (third-party logistics) provider, for example, might assign wave picks to different users, which allows them to pick and pack orders while moving through the warehouse so that they are completed together.
Benefits of Wave Picking
Wave picking is widely used because it offers several advantages over traditional single-order picking:
- On-time shipping: By considering orders, resources, and shipping schedules, wave picking ensures orders are picked and completed before shipping deadlines.
- Fewer bottlenecks: Unlike single-order picking, which can cause aisle congestion, wave picking schedules workers and equipment at different times, improving productivity.
- Faster picking: Planning waves based on multiple factors allows pickers to retrieve larger quantities of the same SKU or multiple SKUs in one location, reducing travel time.
- Increased accuracy: Sorting and packing teams can double-check SKU counts after picking, ensuring orders are correctly fulfilled.
- Improved tracking: A structured schedule and handheld scanning devices linked to a WMS provide real-time progress updates for better management.
- Better for high-value or perishable goods: Just-in-time picking reduces the risk of damage, theft, or spoilage by minimizing idle time before shipment.
Challenges of Wave Picking
While wave picking has many benefits, it also comes with some challenges:
- Potential downtime: Poorly planned waves or uneven labor distribution can create bottlenecks, causing some pickers to wait while others struggle with heavy workloads.
- Delays for urgent orders: Since wave picking follows strict schedules, last-minute priority orders can either disrupt the workflow or be delayed, requiring management to make tough decisions.
- Extra processing step: If items aren’t picked directly into shipping cartons, they must go through sorting and packing, which can add time and increase the chance of errors.
- Warehouse congestion: More pickers working at the same time can lead to traffic and confusion if a warehouse management system (WMS) isn’t in place to coordinate movements.
How to Optimize Wave Picking
To make the most of wave picking, follow these steps:
- Analyze order details: Look at factors like size, weight, and priority to organize orders efficiently and avoid delays.
- Group similar orders: Pick from the same zone whenever possible to cut down travel time and speed up fulfillment.
- Use automation tools: Conveyor belts, robotic pickers, and barcode scanners improve accuracy and reduce manual effort.
- Integrate with a WMS: A warehouse management system (WMS) provides real-time tracking, analytics, and seamless coordination for multi-wave picking.
- Ensure proper training and ease of use: Regular training and user-friendly systems help teams work efficiently and maximize the benefits of this picking.
With the right tools and strategy, wave picking becomes a powerful way to streamline warehouse operations and boost productivity.
Simplify Wave Picking Processes Through HashMicro
When fine-tuning your warehouse operations, choosing the right picking method makes all the difference. Wave picking is a great option, but it’s important to see if it aligns with your workflow. With HashMicro’s Warehouse Management System, you get a solution designed to optimize wave picking based on your needs.
This method works best in a well-organized space where products are grouped by zones to minimize unnecessary movement. If your warehouse is set up this way, HashMicro’s WMS can make wave picking more efficient.
HashMicro has these features to help:
- Inventory Tracking and Management: Monitors stock levels and updates inventory in real time.
- Barcode and RFID Scanning: Captures product data using barcode or RFID scanners during receiving, picking, and shipping.
- Order Management: Processes sales and purchase orders automatically.
- Warehouse Layout Optimization: Organizes storage locations and assigns space for efficient item retrieval.
- Multi-Warehouse Management: Syncs inventory data across multiple warehouse locations.
- Advanced Reporting and Analytics: Generates reports on stock movements, order status, and warehouse performance.
- Integration with Other Systems: Connects with ERP, CRM, and accounting systems for centralized data management.
- Mobile Access: Allows warehouse staff to use the system on mobile devices for on-the-go operations.
Conclusion
Wave picking is a warehouse order fulfillment method that organizes picking tasks into scheduled waves based on shared factors. The warehouse teams can group waves in different ways, such as by product type, shipping schedule, or workforce availability.
To get the most out of wave picking, you need a smart warehouse management system (WMS) that keeps everything in sync. HashMicro’s WMS does the heavy lifting by automating wave scheduling, tracking inventory in real time, and organizing warehouse layouts for faster picking.
Whether you’re handling bulk orders or rushing urgent shipments, HashMicro makes wave picking faster, smarter, and hassle-free. So, if you’re interested in making your picking process more efficient, try the free demo now!
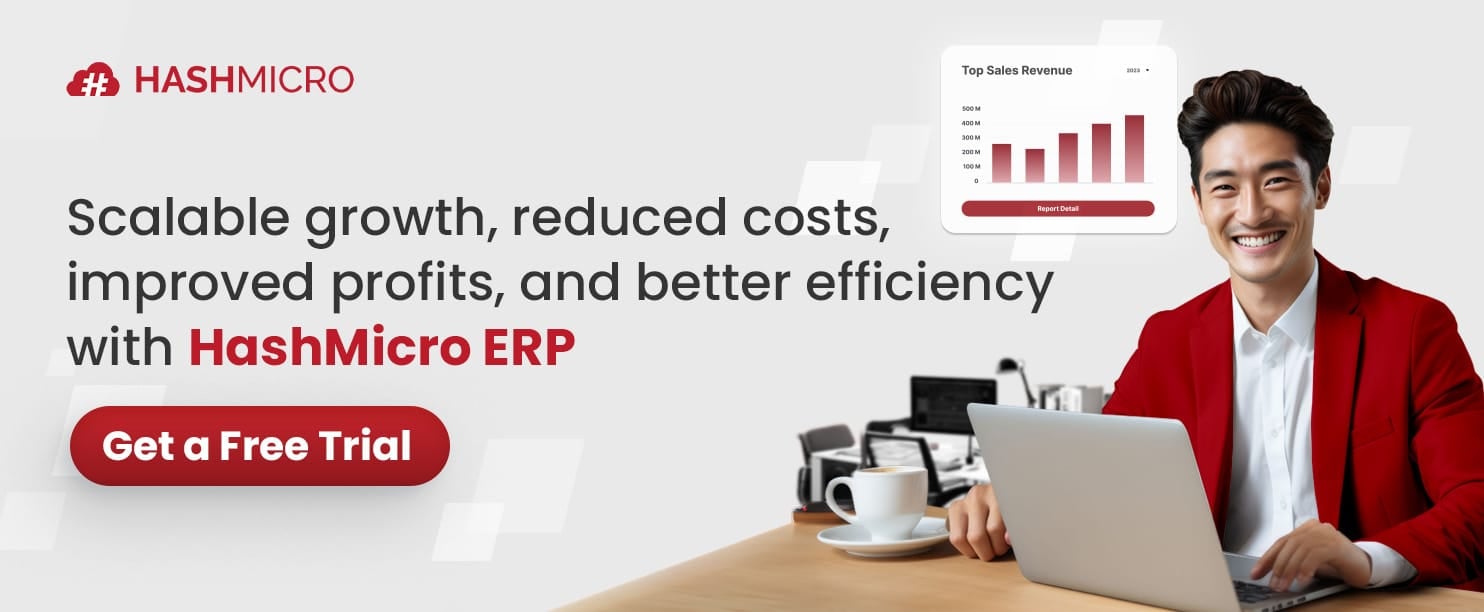
FAQ on Wave Picking
-
How does scheduled order picking differ from batch picking?
While both methods involve picking multiple orders simultaneously, wave picking releases groups of orders at scheduled times, whereas batch picking focuses on picking similar orders together without a set schedule.
-
What types of warehouses benefit most from structured order fulfillment?
Warehouses with high order volumes and a large variety of SKUs benefit from this method, as it enhances efficiency by grouping orders based on shared factors.
-
What is dynamic wave picking?
Dynamic cluster picking creates waves in real-time based on current order requirements, allowing for a more flexible and responsive picking process.
-
Can grouped picking be combined with other picking methods?
Yes, this approach can be integrated with methods like zone picking or batch picking to optimize warehouse operations.