In the fast-paced world of logistics, efficient order fulfillment is crucial for maintaining customer satisfaction and operational success. One method that has gained prominence is zone picking, a strategy designed to streamline the picking process within warehouses.
However, implementing zone-picking presents challenges such as coordinating between zones, managing inventory distribution, and ensuring timely order completion. These issues can lead to bottlenecks and inefficiencies if not properly addressed.
A study highlights the complexities involved in zone picking, emphasizing the need for effective management strategies to overcome these hurdles. Without proper coordination and automation, warehouses may face delays, increased labor costs, and order inaccuracies that affect overall efficiency.
Continue reading this article to learn more about zone picking, its challenges, and potential software solutions. We will explore how technology can enhance warehouse operations and provide practical insights for managers.
Table of Content
Content Lists
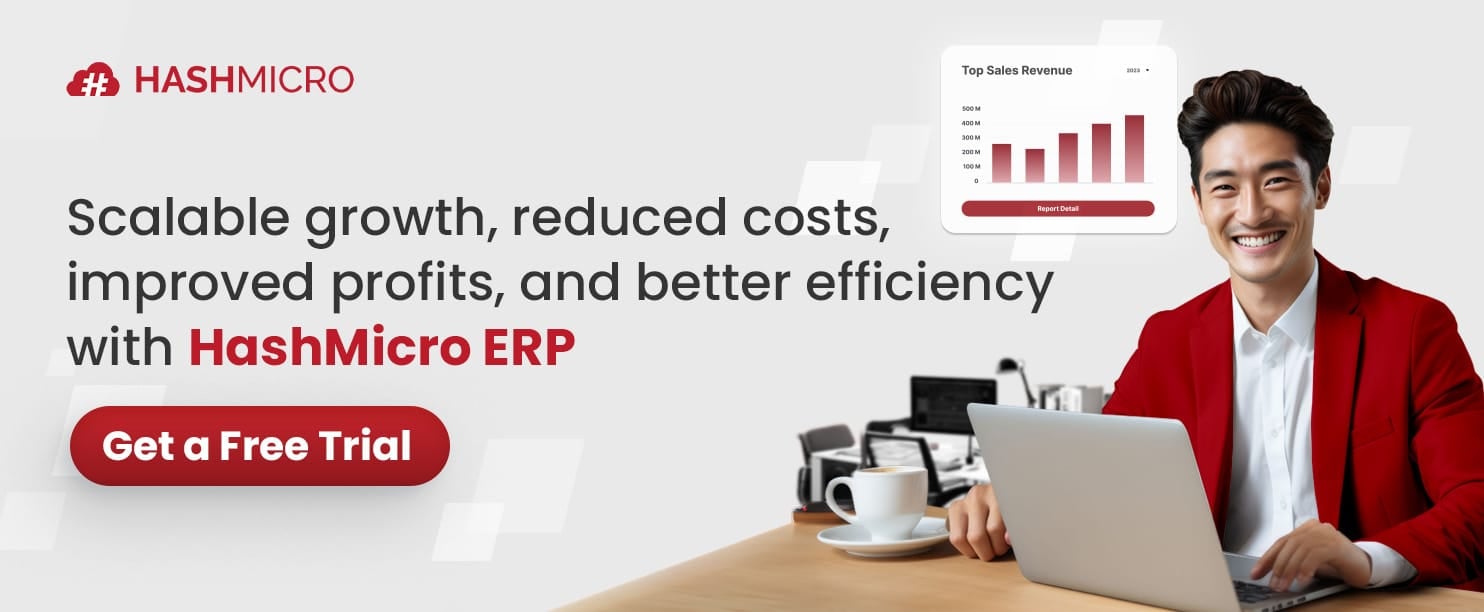
Key Takeaways
|
What is Zone Picking?
Zone picking is an efficient warehouse picking method that divides storage areas into separate zones, where designated workers pick items for order fulfillment. Instead of one picker moving across the entire warehouse, each worker is responsible for picking only from their assigned warehouse zone, improving efficiency and reducing congestion.
This process is often called pick and pass, as items move from one zone-picking station to the next until the order is complete. For example, a warehouse zone may be dedicated to fresh produce, another to frozen goods, and another to heavy items requiring forklifts, ensuring that items are packed using the most effective tools and processes.
Unlike zone picking vs wave picking, where orders are picked in batches at specific times, zone-picking in the warehouse focuses on continuous workflow, improving order accuracy and speed. By assigning pickers to particular zones, businesses follow warehouse picking best practices, reducing travel time, optimizing labor, and ensuring a smoother fulfillment process
The Benefit of Zone-Picking
A well-structured zone-picking system enhances warehouse efficiency by reducing travel time, improving inventory accuracy, and streamlining fulfillment. This method divides the warehouse zone into designated areas where pickers handle only specific sections, minimizing unnecessary movement and enhancing productivity.
By implementing warehouse-picking best practices, businesses can optimize workflows, ensure inventory security, and maintain product quality.
1. Organizing warehouse space
Dividing a warehouse zone based on product characteristics, such as size, demand, or security requirements, helps improve organization and retrieval speed. Pick zones can be structured for fast-moving vs. slow-moving SKUs, hazardous materials, or temperature-sensitive goods, ensuring efficient storage.
This segmentation allows each zone to have its storage strategy, picking equipment and technology suited to the items stored. As a result, zone picking in warehouse operations becomes smoother, reducing misplaced inventory and fulfillment delays.
2. Improving efficiency
By assigning pickers to specific warehouse zones, zone-picking reduces travel time and ensures a continuous workflow. Unlike traditional picking methods, where workers move across the warehouse, pickers stay within their designated zones, leading to faster and more accurate order fulfillment.
This method also supports conveyor-based or robotic-assisted transport, further streamlining picking operations. Compared to zone picking vs. wave picking, this system minimizes downtime by ensuring each order progresses seamlessly from one zone to another.
3. Enhancing safety and security
A well-zoned warehouse prevents safety risks by storing hazardous or high-value items separately in controlled environments. For example, corrosive materials or flammable liquids can be placed in specialized warehouse zones with necessary safety measures, reducing the risk of accidents.
High-security SKUs, such as electronics or luxury items, can be placed in restricted-access areas with advanced monitoring systems. These security measures align with warehouse-picking best practices, ensuring product integrity and compliance with industry regulations.
4. Reducing product spoilage
Proper zoning helps businesses maintain separate storage areas for items that require specific environmental conditions. Perishable goods can be stored in refrigerated zones, while dry storage areas prevent moisture damage, extending product shelf life.
This structured approach ensures inventory control, minimizes spoilage, and prevents financial losses. By maintaining optimal storage conditions, zone picking helps businesses achieve better stock rotation and reduce waste.
5. Supporting scalability and flexibility
One of the most significant advantages of zone-picking is its ability to scale with business growth and adapt to changing demands. Large warehouses handling thousands of SKUs can implement hybrid picking methods, such as zone-wave or zone-batch picking, to enhance efficiency.
Pickers become more familiar with their assigned zones, improving accuracy and speed while reducing operational bottlenecks. Whether combined with automation or manual processes, zone-picking in warehouse settings provides flexibility to meet diverse business needs.
How does Zone Picking Work?
Zone picking is a structured warehouse picking best practice where pickers are assigned to specific warehouse zones to optimize order fulfillment. Depending on the method, orders can be processed sequentially or simultaneously, ensuring faster and more accurate picking.
Below are the two main types of zone-picking in warehouse operations and how they function.
1. Sequential zone picking (pick and pass method)
In sequential zone-picking, each picker retrieves items only from their assigned warehouse zone before passing the order to the next area. For example, a picker in Zone One gathers pasta and canned tomatoes, then places the bin on a conveyor or hands it off to another worker.
The bin moves through different zones, where additional items—such as pet food in Zone Two and headphones in Zone Three—are added before reaching the packing station. This method ensures a structured workflow but can take longer if multiple zones are involved.
2. Simultaneous zone picking (pick and merge method)
In simultaneous zone-picking, all pickers collect the required items from their designated warehouse zones simultaneously. Unlike sequential picking, they do not pass the bin from one zone to another; instead, they bring their items directly to the parking area.
For instance, while the grocery zone picker collects pasta and tomatoes, the pet supplies picker grabs cat food, and the electronics picker retrieves Bluetooth headphones simultaneously. This approach speeds up the process compared to zone picking vs. wave picking, making it ideal for high-volume warehouses.
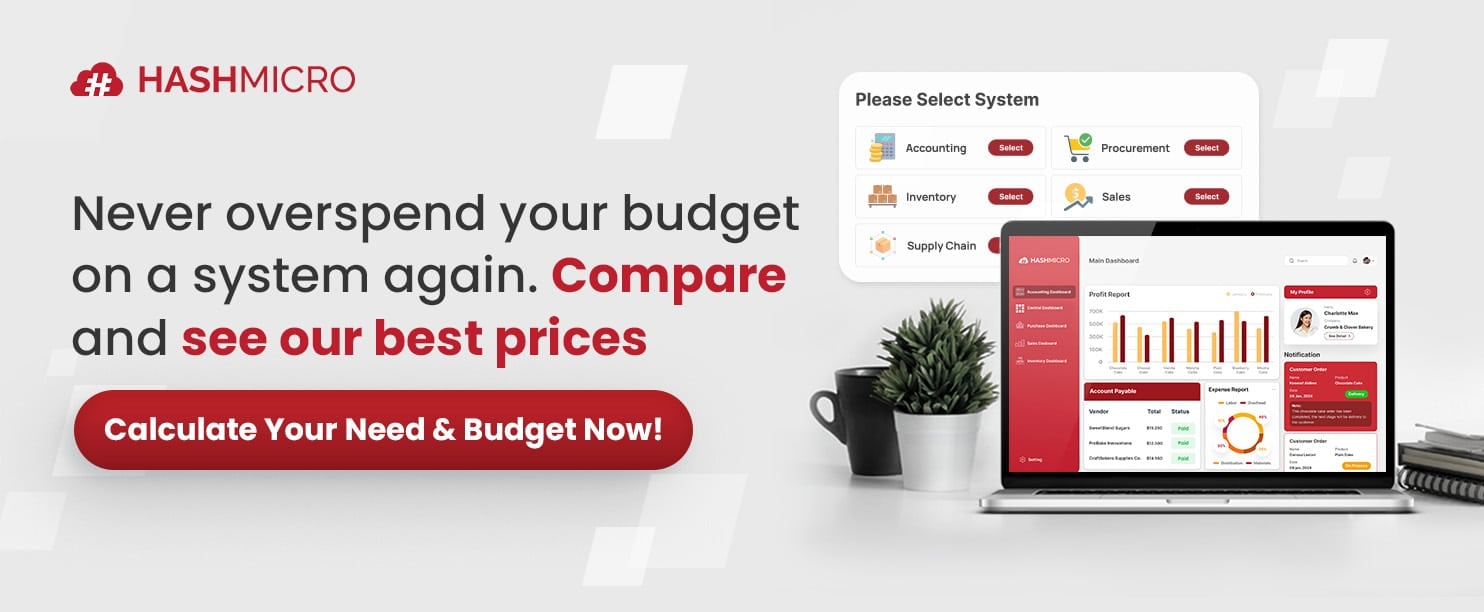
Both zone-picking methods improve efficiency by reducing unnecessary movement and allowing workers to specialize in their zones. Choosing between them depends on warehouse size, order volume, and operational requirements, ensuring flexibility in warehouse zone management.
Wave Picking vs. Zone Picking
While zone picking assigns pickers to specific warehouse zones, wave picking groups similar orders into batches and picks them within a scheduled timeframe. This scheduling ensures that all items are ready for processing before key logistics activities, such as shipping deadlines or carrier pickups, improving overall efficiency.
In zone-picking in warehouse operations, workers stay in designated areas and select only the SKUs within their zones, reducing travel time and improving accuracy. Meanwhile, wave picking optimizes labor by allowing workers to pick multiple orders simultaneously, ensuring that bulk orders are processed efficiently and shipped on time.
When comparing zone and wave picking, the proper method depends on warehouse size, order volume, and fulfillment priorities. Businesses handling a wide variety of SKUs benefit from zone picking, while high-order volumes requiring strict scheduling may find wave picking more effective in managing fulfillment speed.
Examples of Zone-Picking
Zone picking is essential for wholesale distributors handling large, multi-item orders efficiently. A company like Convenient divides its warehouse zone into sections—such as kitchen supplies and cleaning products—so pickers stay in designated areas, reducing travel time.
This warehouse-picking best practice improves order accuracy and speeds up fulfillment. Pickers place selected items in totes, which are then moved along conveyors or manually transported to the next zone.
Unlike zone picking vs wave picking, which follows a set schedule, zone-picking in the warehouse enables continuous workflow. This approach allows distributors to process high volumes faster, minimize errors, and meet demand efficiently.
Zone Picking Best Practices
Implementing zone-picking in warehouse operations effectively requires strategic planning and organization. Below are key warehouse-picking best practices that enhance efficiency, reduce errors, and improve overall productivity.
- Minimize handling to reduce errors: Reducing unnecessary handling lowers the risk, dropped items, and breakage. The fewer times an item is touched, the faster and more accurate the zone-picking process becomes.
- Store fast-moving products near shipping areas: Placing high-demand SKUs close to the shipping area minimizes travel time and speeds up fulfillment. This approach optimizes zone picking vs wave picking by ensuring frequently picked items are always within easy reach.
- Prioritize worker safety: Proper equipment, such as pallet jacks and ergonomic support, prevents injuries and improves efficiency. A safer warehouse zone reduces errors and ensures employees sustain productivity throughout their shifts.
- Track and optimize Key Performance Indicators (KPIs): Monitoring metrics like order accuracy and picking speed helps identify areas for improvement. Setting benchmarks encourages workers to refine their zone-picking accuracy and maintain high fulfillment standards.
- Keep zones clean and organized: A well-maintained warehouse zone prevents congestion and ensures easy item location. Clear aisles improve workflow and enhance overall warehouse picking best practices for seamless operations.
How to Organize a Warehouse for Zone Picking
Effectively setting up a warehouse zone for zone picking requires strategic planning and the right technology. Below are key steps to optimize zone picking in warehouse operations and improve efficiency.
- Choose between a WMS or a ZPS: A warehouse management system (WMS) helps manage all warehouse operations by analyzing labor and product flow, including zone picking. Meanwhile, a zone picking system (ZPS) is more specialized, guiding totes through pick-and-pass zones using conveyors for seamless order fulfillment.
- Implement a warehouse organization strategy: Dividing warehouse space based on factors like sales volume, packaging needs, or temperature control improves zone picking definition and efficiency. Ensuring sufficient space for receiving, picking, and shipping operations prevents congestion and enhances workflow.
- Select the right equipment for zone picking: Zone-picking equipment ranges from simple pushcarts and totes to automated goods-to-picker systems with robotics and conveyors. The best option depends on warehouse size, order volume, and a cost-benefit analysis of automation vs. manual processes.
By following these warehouse-picking best practices, businesses can streamline zone-picking vs. wave-picking operations and maximize productivity. Proper planning ensures faster fulfillment, reduced errors, and a more organized warehouse zone for long-term success.
Optimize Zone Picking Using HashMicro’s WMS Solution
HashMicro offers a powerful Warehouse Management System (WMS) designed to enhance efficiency and accuracy in zone-picking operations. One key feature is automated zone assignment and order tracking, which are seamlessly integrated into our WMS solution for real-time warehouse optimization.
Experience the capabilities of HashMicro’s WMS Solution through a free demo. Explore how automation streamlines warehouse zone-picking, reduces travel time, and improves order accuracy, ensuring faster fulfillment and better inventory control.
Why choose HashMicro? Our WMS software automates critical tasks like zone allocation, picking route optimization, and inventory tracking, minimizing manual errors and increasing warehouse productivity. Its seamless integration with other logistics modules provides a comprehensive solution for warehouse zone management.
It helps businesses improve warehouse picking best practices while optimizing space and labor efficiency. Below are some of the key features of HashMicro’s WMS Solution:
- Product Dimension Tracking: Improve zone-picking efficiency by tracking item dimensions, ensuring optimal storage allocation that minimizes congestion and speeds up retrieval.
- Location Dimension Management: Automatically calculate and assign storage locations based on item size, reducing misplacements and improving picking accuracy in warehouse zones.
- Putaway Strategy Settings: Define smart storage strategies to place new inventory in the most efficient zones, reducing picker travel time and enhancing order fulfillment speed.
- Putaway Capacity Checking: Prevent overstocking by verifying storage capacity before placing items, ensuring a balanced distribution across warehouse zones for smoother picking.
- Warehouse Pallet Racking: Organize shelves strategically to categorize items by type and function, speeding up zone-picking and reducing search time for warehouse staff.
- Warehouse In-Depth Reporting: Generate real-time reports to track zone-picking performance, identify inefficiencies, and refine warehouse strategies for maximum productivity.
These capabilities enhance order fulfillment speed, reduce operational costs, and improve warehouse organization. With HashMicro’s WMS Solution, businesses can efficiently manage zone picking, maximize productivity, and achieve long-term warehouse efficiency.
Conclusion
Zone picking is a highly efficient warehouse picking best practice that reduces travel time, improves accuracy, and streamlines order fulfillment. Businesses can optimize labor and inventory management by assigning pickers to specific warehouse zones.
Implementing a Warehouse Management System (WMS) further enhances this process by automating zone allocation, order tracking, and picking routes, ensuring smooth operations and increased productivity.
HashMicro’s WMS Solution is one of the best warehouse management systems in Malaysia, designed to optimize zone picking in warehouse operations. With advanced automation features, it helps businesses efficiently manage inventory, reduce manual errors, and improve overall warehouse efficiency.
Ready to transform your warehouse operations? Try a free demo of HashMicro’s WMS Solution today and discover how automation can improve zone picking, streamline order fulfillment, and drive greater efficiency in your supply chain.