Managing production costs effectively is one of the most challenging tasks for any business leader. Absorption costing offers a comprehensive way to allocate costs, but implementing it efficiently can be complex.
Many managers struggle with distorted profitability metrics, which are caused by unsold inventory that adds fixed costs forward. These challenges often make it difficult to assess true production efficiency and set accurate pricing strategies.
According to a study by BusinessWorld Philippines, 60% of small enterprises in the Philippines face difficulties in implementing effective cost allocation systems. This challenge often leads to inaccurate financial reporting and hinders their ability to make informed business decisions.
In this article, we’ll explore the fundamentals of absorption costing, common challenges, and practical tips to optimize its application. Discover how advanced software solutions can simplify absorption costing for your business.
Table of Contents
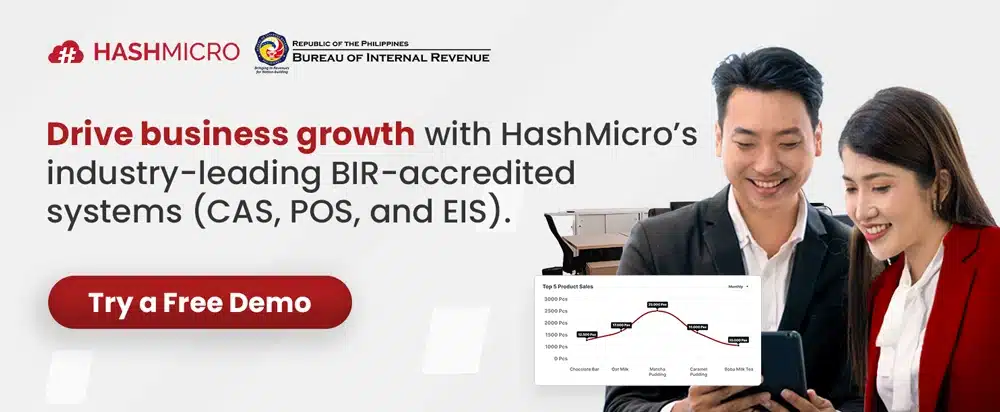
Key Takeaways
|
What is Absorption Costing?
Absorption costing, or “full costing,” is a managerial accounting method that captures all costs involved in manufacturing a product. It includes direct costs, like materials and labor, and indirect costs, such as rent and insurance, ensuring a comprehensive calculation for each product.
Unlike variable costing, full costing assigns all expenses, including fixed overhead costs, to the product’s cost base, regardless of whether the products are sold by the period’s end. This method provides businesses with a detailed view of total production costs, offering a clearer picture of profitability by accounting for expenses like wages and utilities.
Understanding absorption costing is crucial for accurate financial planning and decision-making. By incorporating all production costs into the income statement, this method helps businesses analyze profitability and make informed operational decisions.
Absorption Costing Formula
The absorption costing formula is a straightforward way to determine the cost of a single inventory unit by dividing total production costs by the number of units produced. Specifically, it combines direct labor costs, direct material costs, variable manufacturing overhead, and fixed manufacturing overhead, ensuring all cost components are accurately captured.
The formula looks like this:
Absorption cost per unit = (Direct labor + Direct materials + Variable overhead + Fixed overhead) / Units produced
To determine the inventory value for the balance sheet, this cost is multiplied by the number of unsold units. To illustrate absorption in practice, imagine applying this formula to track costs for unsold products at the end of a reporting period.
Breaking down the formula, each cost component requires precise costing computation. For instance, direct labor costs might include hourly wages, overtime, and benefits, while overhead costs account for utilities, factory rent, and machinery depreciation.
Understanding the absorption rate for each element is key to achieving an accurate costing computation, especially in industries with diverse product lines. In contrast to variable costing, which excludes fixed overhead, absorption costing allocates all costs to products, whether sold or unsold.
This comprehensive approach impacts the full costing income statement, where unsold inventory retains its cost value. For businesses managing multiple products, such as an apparel company producing scarves and dresses, the absorption method ensures each item’s cost is proportionally and fairly represented.
How Absorption Costing Works
Absorption costing is an accounting method that allocates all production costs, both direct and indirect, to individual products. This method ensures that each product carries its fair share of manufacturing expenses, providing a comprehensive view of production costs.
Here’s how it works:
- Incorporates all cost components: Absorption costing includes all direct costs (e.g., labor and materials) and indirect costs (e.g., factory rent and utilities). This ensures a thorough costing computation, capturing every expense involved in manufacturing.
- Allocates fixed overhead costs: Unlike variable costing, this method spreads fixed overhead costs across all units produced, regardless of sales. This distinction between variable costing and absorption costing is crucial for preparing an accurate income statement.
- Uses the absorption costing formula: This formula calculates unit costs by dividing total production costs (direct labor, direct materials, variable, and fixed overhead) by the number of units produced. This allows businesses to track costs effectively and plan pricing strategies.
- Provides comprehensive financial reporting: Absorption costing ensures a detailed financial overview by incorporating fixed costs into product pricing. This method is particularly beneficial for businesses dealing with long production cycles or fluctuating sales.
- Supports strategic pricing models: Tools like freight absorption pricing and monitoring the absorption rate help businesses manage transportation costs and overall profitability. These insights aid in setting competitive prices while maintaining healthy margins.
This method offers a balanced approach to tracking production costs and pricing, making it a valuable tool for businesses aiming for sustainability and growth.
Advantages of Absorption Costing
Absorption costing is a widely used accounting method that offers several distinct advantages for businesses. By incorporating all production costs, this method ensures accurate financial reporting and better decision-making. Below is a list of its primary benefits:
- Compliance with GAAP standards: Absorption costing is mandatory for external reporting under Generally Accepted Accounting Principles (GAAP). Unlike other methods, it provides consistency and compliance, ensuring a more reliable absorption costing income statement.
- Accurately reflects profit: This method matches expenses with revenues in the same reporting period, yielding a precise net profit forecast. In the debate between variable costing and absorption costing, this is a key advantage that supports better financial analysis.
- Simplifies costing computation: Since fixed and variable manufacturing overheads do not need separate treatment, the absorption method simplifies the costing computation process. This ease of calculation saves time and minimizes errors.
- Supports strategic pricing: It ensure all costs, including fixed overheads, are factored into product pricing. This approach helps decision-makers establish accurate selling prices and even aids in special strategies like freight absorption pricing.
- Improves net income reporting: One notable benefit is that a portion of fixed overhead costs tied to unsold inventory is carried forward as assets on the balance sheet. This results in a higher reported income, providing an example of absorption advantages for businesses seeking to optimize financial outcomes.
With these advantages, absorption costing remains a crucial tool for businesses aiming to enhance financial accuracy, comply with regulations, and improve strategic decision-making.
To further streamline your financial processes, consider leveraging accounting software to automate cost calculations and ensure accuracy. Click the banner below to explore how HashMicro’s solutions can help your business and get a customized pricing estimate today!
Disadvantages of Absorption Costing
While absorption costing provides a comprehensive view of production costs, it also has certain limitations that can affect internal decision-making. These drawbacks highlight why some businesses may prefer variable costing vs absorption costing for specific analyses.
Here are the key disadvantages:
- Distorts net income reporting: Absorption costing can inflate net income when unsold inventory carries fixed manufacturing costs forward to the balance sheet. This delay in expensing costs may skew the absorption costing income statement, making profitability appear higher than it actually is.
- Inaccurate cost analysis for internal decisions: When analyzing production volume, costing computation under absorption costing can be misleading. Increased production reduces unit costs, but this doesn’t reflect actual profitability if goods remain unsold, making it less effective for internal evaluations like volume or efficiency analysis.
- Skewed profitability analysis: The inclusion of fixed overhead costs in unit pricing can misrepresent profitability, particularly for businesses planning to scale production. A method like variable costing may offer better insights for such scenarios, avoiding distortions caused by the absorption rate.
- Does not align with variable costing for operational analysis: Fixed costs, such as rent and machinery expenses, remain constant regardless of production levels. This characteristic of the absorption method can make it less useful for operational decisions compared to a variable costing approach, which better reflects the impact of production changes.
- Limited flexibility in pricing strategies: Absorption costing may hinder strategies like freight absorption pricing or dynamic pricing models due to its focus on allocating fixed costs. Businesses seeking agile pricing strategies often prefer alternatives that allow for greater flexibility.
Understanding these limitations helps businesses choose the appropriate costing method for their specific needs. Comparing absorption and variable costing is essential for internal analyses and operational decisions to ensure accurate insights and effective strategies.
Component of Absorption Costing
Absorption costing involves accounting for all production-related costs, ensuring a comprehensive allocation to each unit produced. This method provides a detailed breakdown of costs, creating an accurate basis for pricing and financial reporting.
Below are the essential components of absorption costing:
- Direct materials: The cost of raw materials used directly in manufacturing a product is a primary component. For instance, in an example of absorption, this would include fabric in garment production or steel in car manufacturing.
- Direct labor: Labor costs for employees actively involved in the production process are included. This ensures precise costing computation, capturing all expenses tied to producing each unit.
- Variable manufacturing overhead: These are costs that fluctuate with production levels, such as electricity and machine maintenance. Unlike variable costing vs absorption costing, this method includes these variable overheads in unit costs.
- Fixed manufacturing overhead: Fixed costs, like factory rent and equipment depreciation, are distributed across all units produced. This allocation, a hallmark of the absorption method, ensures an accurate reflection of total production costs.
- Freight and logistics costs: Transportation expenses, including freight absorption pricing, are factored into product costs. This component is vital for businesses managing extensive distribution networks.
By encompassing these components, absorption costing provides a robust framework for creating an accurate income statement. This comprehensive approach distinguishes it from other methods, such as absorption and variable costing, and supports strategic financial management.
Example of Absorption Costing
Let’s consider ABC Company, which manufactures widgets using the absorption method. In January, the company produced 10,000 widgets, each with a direct cost of ₱5 for labor and materials. To account for fixed overhead costs totalling ₱20,000, the company allocates ₱2 per widget based on the absorption costing formula of dividing total overhead by units produced.
This results in a total absorption cost of ₱7 per unit (₱5 direct costs + ₱2 fixed overhead). If 8,000 widgets are sold during the month, the absorption costing income statement will reflect a cost of goods sold (COGS) of ₱56,000 (₱7 × 8,000 units sold).
This provides a clear example of how absorption and variable costing differ, as variable costing excludes fixed overhead from unit costs.
The total value of the remaining 2,000 units in inventory is carried forward at ₱14,000 (₱7 × 2,000 units). This demonstrates how absorption costing can impact both COGS and inventory valuation, highlighting its usefulness in cost computation and external reporting.
Absorption vs. Variable Costing
Absorption costing and variable costing are two methods used to calculate product costs. They differ primarily in how they treat fixed overhead costs. The absorption method includes both direct and indirect costs, ensuring every unit produced reflects a share of fixed overhead.
In contrast, variable costing considers only direct costs in the cost of a product, treating fixed overhead as a period expense recorded in the income statement. This approach provides clearer insights into incremental costs, making it more suitable for internal decision-making and analysis of variable costing vs absorption costing scenarios.
Full costing allocates fixed overhead across both sold goods and inventory, impacting profitability and inventory valuation. On the other hand, variable costing presents fixed overhead as a single lump-sum expense, simplifying the costing computation for management while providing a sharper focus on production efficiency.
Achieve Absorption Costing Efficiency with HashMicro Accounting Software
HashMicro’s Accounting Software is a robust solution designed to enhance business processes, including absorption costing and financial reporting. By automating cost allocation, tracking production expenses, and complying with regulations such as CAS (Computerized Accounting System) requirements by the BIR, companies can achieve more accurate cost computations and streamlined operations.
To give businesses a firsthand experience, HashMicro offers free demo access to its accounting software. This allows potential users to explore its advanced features, which ensures that they make well-informed decisions for their overall financial management.
Bakit namin ito inirerekomenda: HashMicro’s accounting software simplifies absorption costing by automating complex processes, such as cost computation and inventory valuation. It also provides real-time insights, helping businesses meet compliance standards like BIR CAS and make accurate, data-driven decisions.
Below are some key features of HashMicro’s accounting software, such as:
- Multi-Level Analytical Reporting: This feature allows managers to compare financial statements across projects, branches, or departments. By analyzing cost allocation at multiple levels, businesses can identify inefficiencies and optimize absorption costing computations.
- Profit & Loss vs Budget & Forecast: The software automatically compares actual profit and loss data with budgeted and forecasted figures. This helps businesses assess if production costs and revenue align with financial goals under the costing method.
- Financial Statement with Budget Comparison: It generates financial statements that include side-by-side budget comparisons for better clarity. This ensures accurate reporting of absorbed costs and supports strategic decision-making.
- Landed Costs Management: This feature tracks and allocates additional expenses like shipping and customs directly to products. Businesses can calculate accurate product costs, ensuring compliance with the absorption costing formula.
- Forecast Budget: The system helps businesses forecast production budgets based on historical and projected data. Managers can plan for fixed and variable costs, ensuring accurate cost allocation.
- Complete FS with Period Comparison: Users can generate financial statements that compare performance across multiple periods. This feature highlights cost trends and helps refine absorption rate calculations for improved accuracy.
- Cashflow Reports: The software tracks cash flow related to production costs, including direct and indirect expenses. This helps businesses maintain operational efficiency while ensuring cost alignment with budgets.
- Multi-Company with Inter-Company Transactions: This feature consolidates financial data across multiple entities and manages inter-company transactions. It simplifies absorption costing for businesses operating in diverse locations or subsidiaries.
- Chart of Accounts Hierarchy: The system organizes accounts into a clear hierarchy, making it easier to allocate costs accurately. Businesses can trace expenses back to specific categories, improving cost transparency.
- Budget & Realization Tracking: Managers can track actual expenses against budgets in real-time to ensure proper cost allocation. This feature helps businesses spot discrepancies and refine absorption costing processes efficiently.
Additionally, the software supports unlimited users, offers flexible customization options, and integrates seamlessly with third-party applications. Its adaptability and integration make it ideal for businesses looking to optimize full costing processes and ensure compliance with local financial regulations.
Conclusion
Absorption costing is a critical method for accurately allocating production costs, but it often presents challenges for managers, such as tracking fixed overhead and ensuring accurate inventory valuation. The right tools can manage these complexities efficiently, enabling businesses to streamline cost computations and improve decision-making processes.
For companies in the Philippines, HashMicro’s Accounting Software provides an ideal solution for effectively implementing absorption costing. With features designed to comply with BIR CAS requirements, the software ensures accurate financial reporting while automating cost tracking and allocation for greater efficiency.
To experience the benefits firsthand, we invite you to try HashMicro’s free demo. Explore how this powerful accounting tool can simplify absorption costing for your business and help you achieve accurate, compliant financial management.