The alcohol manufacturing industry in the Philippines faces growing challenges in production, inventory, and regulatory compliance. ERP for alcohol manufacturing helps businesses streamline operations, reduce costs, and improve efficiency.
By implementing the right ERP system, alcohol manufacturers can boost productivity, enhance accuracy, and ensure compliance with government regulations. This guide will explore the benefits, challenges, and must-have features of ERP solutions tailored for the alcohol industry in the Philippines, equipping business owners with the knowledge to make informed and strategic decisions.
Kaya tara, alamin natin kung paano makakatulong ang ERP sa negosyo mo!
Key Takeaways
|
Table of Contents
What Is ERP for Alcohol Manufacturing Industry?
Enterprise Resource Planning is an advanced software solution designed to help businesses integrate and automate their core operations. In the alcohol manufacturing industry, ERP plays a crucial role in streamlining production, inventory management, sales, and compliance tracking. By bringing all essential business functions into a single system, ERP eliminates inefficiencies and improves overall productivity.
For alcohol manufacturers in the Philippines, ERP provides a structured approach to managing operations, ensuring accurate tracking of materials, production processes, and regulatory compliance. With a centralized database, businesses can reduce manual errors, optimize supply chain management, and meet industry standards more effectively. By adopting ERP, manufacturers can boost efficiency, cut operational costs, and focus on expanding their market presence.
Key Challenges in the Alcohol Manufacturing Industry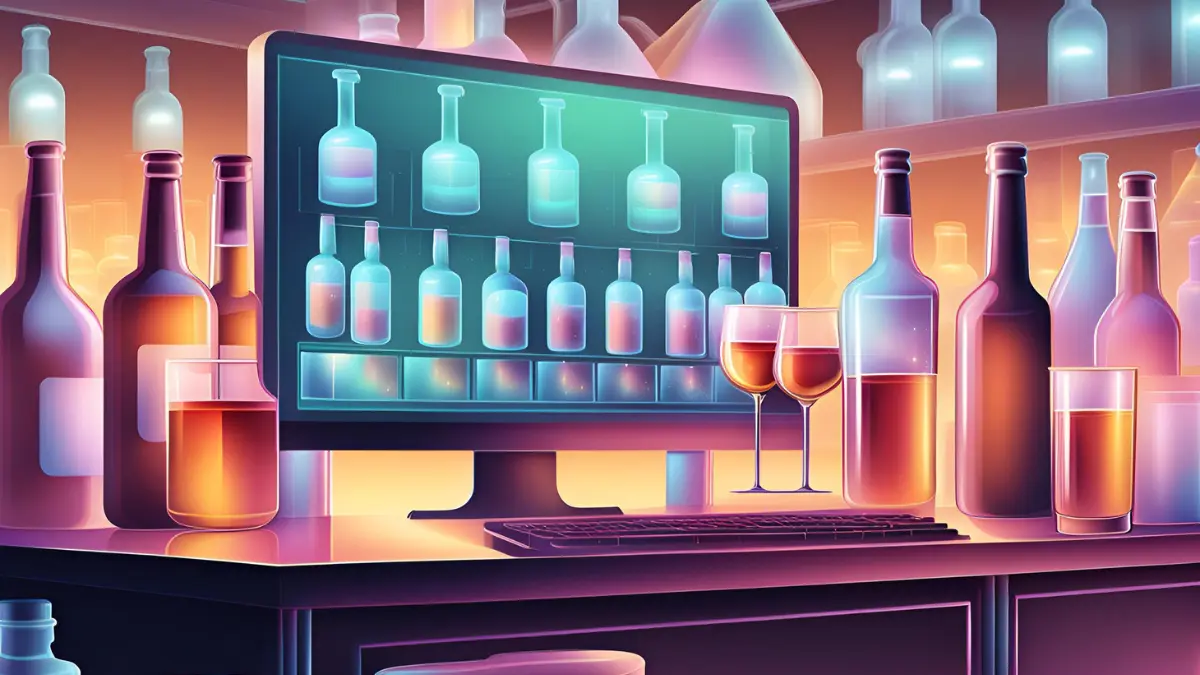
Alcohol manufacturers in the Philippines face various obstacles that can impact their efficiency, profitability, and compliance. From strict government regulations to changing consumer demands, businesses must navigate multiple challenges to stay competitive. Implementing an ERP system can help address these issues, ensuring smooth operations and sustainable growth.
-
Strict Government Regulations and Compliance Requirements
The alcohol industry in the Philippines follows strict regulations set by government agencies like the Bureau of Internal Revenue (BIR) and the Food and Drug Administration (FDA). Manufacturers must comply with tax laws, product labeling, and safety standards to avoid penalties and legal issues.
An ERP system simplifies compliance by automatically tracking regulatory requirements and generating necessary reports. It ensures transparency and reduces the risk of human errors, making it easier for manufacturers to meet government standards.
-
Managing Logistics and Controlling Transportation Costs
Transporting alcohol products across the Philippines can be expensive due to high fuel costs and logistical challenges. Poor coordination can lead to delays, product damage, or increased expenses, affecting overall profitability.
With an ERP system, manufacturers can optimize delivery routes, track shipments in real time, and manage inventory levels efficiently. This reduces waste, improves supply chain visibility, and helps businesses maintain smooth operations.
-
Meeting Consumer Demand for Healthier and Organic Beverages
Consumers in the Philippines are becoming more health-conscious, increasing demand for organic, vegan, and low-calorie alcoholic drinks. Manufacturers must adjust their production strategies to meet these changing preferences.
ERP software helps businesses analyze market trends, monitor ingredient sourcing, and develop new product lines based on customer demand. By using real-time data, manufacturers can quickly respond to market changes and stay ahead of competitors.
-
Addressing Innovation Limitations and Sustainability Concerns
Innovation plays a crucial role in the alcohol industry, but many manufacturers struggle with high costs and outdated processes. Additionally, waste management and environmental concerns have become a priority for businesses and consumers alike.
ERP systems support innovation by providing accurate data on production efficiency, resource usage, and sustainability initiatives. With automation and predictive analytics, businesses can reduce waste, optimize production, and implement eco-friendly solutions.
-
Adapting to E-Commerce Growth and Digital Transformation
More Filipino consumers are purchasing alcohol online, increasing the need for digital solutions and seamless e-commerce integration. Traditional manufacturers may struggle to adapt to these changes without the right technology in place.
An ERP system connects e-commerce platforms with inventory and sales data, allowing manufacturers to manage online orders efficiently. With real-time tracking, businesses can enhance the customer experience and grow their online presence.
Key Benefits of ERP for Alcohol Manufacturing
Investing in an ERP system offers significant advantages for alcohol manufacturers in the Philippines. From improving compliance management to enhancing operational efficiency, ERP software helps businesses optimize their processes. Understanding these benefits can assist manufacturers in making informed decisions for long-term success.
-
Streamlined Compliance and Regulatory Management
ERP automates compliance tracking, making it easier to meet government regulations and avoid penalties. Businesses can generate accurate reports and maintain proper documentation effortlessly.
With a centralized system, manufacturers can ensure quality control and adhere to safety standards without delays. This builds trust with consumers and regulatory agencies alike.
-
Optimized Production and Reduced Operational Costs
ERP systems enhance production efficiency by reducing manual tasks and optimizing resource allocation. Businesses can minimize errors, reduce waste, and lower costs.
Automation also improves scheduling and production planning, allowing manufacturers to meet market demand without overproduction or shortages.
-
Improved Inventory Control and Supply Chain Efficiency
Managing raw materials and finished goods is crucial for alcohol manufacturers. ERP systems provide real-time inventory tracking, ensuring optimal stock levels.
With accurate demand forecasting, businesses can prevent shortages and overstocking, leading to better cash flow and reduced losses.
-
Enhanced E-Commerce Capabilities and Digital Adaptability
ERP software integrates with online stores, allowing seamless order management and inventory updates. This improves order accuracy and customer satisfaction.
Businesses can track sales data, analyze consumer behavior, and adjust marketing strategies accordingly. A digital-ready ERP helps companies expand their online presence effortlessly.
Features in ERP for Alcohol Manufacturing Industry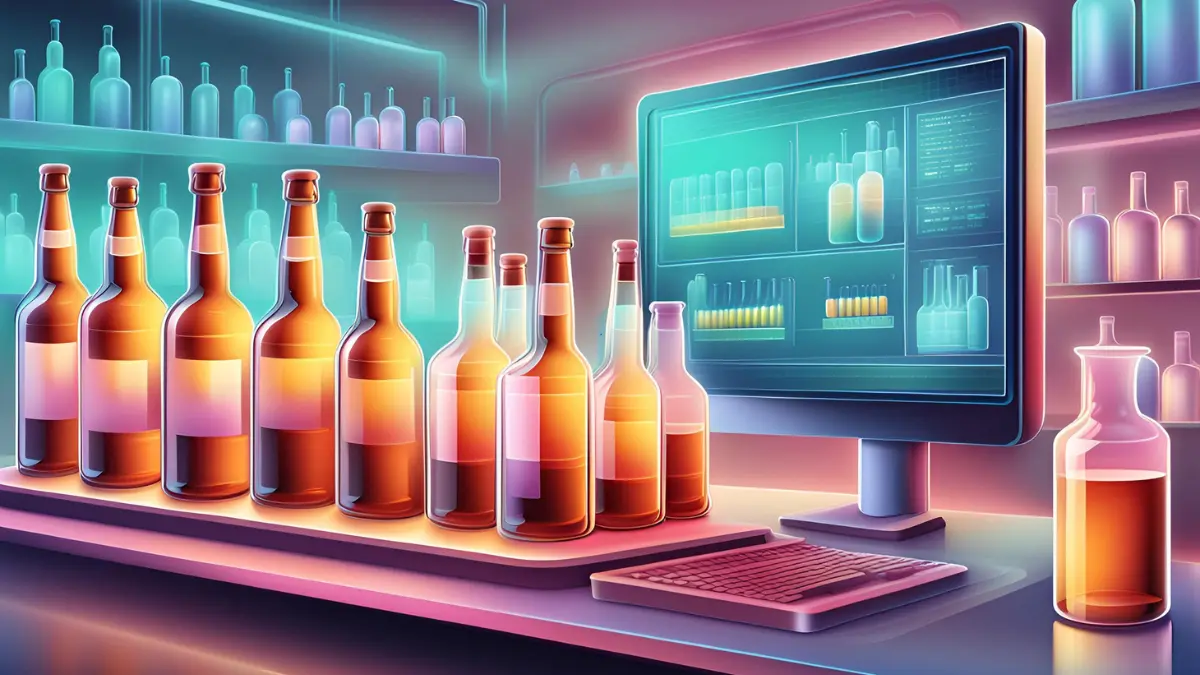
Implementing an ERP system provides alcohol manufacturers with essential tools to manage production, inventory, and compliance efficiently. The right ERP software should include specialized features tailored to the industry’s unique challenges. Here are the key features that make ERP indispensable for alcohol manufacturing businesses.
-
Multi-Level Bill of Materials (BoM) Management
Managing complex recipes and formulations is crucial for alcohol production. ERP systems provide a multi-level BoM that ensures accurate ingredient tracking and cost calculation.
With an integrated BoM system, manufacturers can monitor production stages, maintain quality control, and streamline batch processing. This leads to reduced waste and consistent product quality.
-
Material Requirements Planning (MRP) Tool
Efficient production planning is essential for meeting market demand. ERP software with an MRP tool helps businesses forecast material needs and schedule production effectively.
By optimizing resource allocation, manufacturers can prevent shortages, reduce excess inventory, and minimize production delays. This ensures smooth operations and cost efficiency.
-
Warehouse Stock Capacity Monitoring
Proper inventory management prevents overstocking and supply shortages. ERP systems offer real-time warehouse stock monitoring to maintain optimal inventory levels.
With automated stock tracking, businesses can improve order fulfillment, reduce storage costs, and enhance overall supply chain efficiency.
-
ERP Integration with IoT and Smart Manufacturing
Modern alcohol manufacturers benefit from integrating ERP with IoT devices and smart manufacturing technologies. This enables real-time monitoring of equipment performance and production data.
With IoT-enabled ERP, businesses can enhance process automation, reduce downtime, and improve overall operational efficiency.
How to Choose the Right ERP for Alcohol Manufacturing Industry
Selecting the best ERP system requires careful planning and evaluation. With numerous options available, manufacturers must ensure the software aligns with their specific needs. By considering factors like compliance, scalability, and integration capabilities, businesses can find an ERP solution that enhances productivity and profitability.
-
Identify Business Requirements and Essential ERP Features
Before selecting an ERP, manufacturers should assess their business needs and list essential features. Different companies require different functionalities, such as inventory tracking, compliance management, and production planning.
Choosing an ERP tailored to the alcohol industry ensures maximum efficiency and better ROI. Businesses should look for solutions that align with their operations and long-term goals.
-
Ensure Compliance with Regulatory and Safety Standards
Regulatory compliance is a major concern for alcohol manufacturers in the Philippines. Failing to meet requirements can result in heavy fines, product recalls, or business shutdowns.
ERP systems automate compliance tracking, ensuring businesses meet local regulations without manual errors. This reduces risks and simplifies reporting processes, helping companies stay legally compliant.
-
Evaluate ERP Scalability Based on Company Size and Growth
Small businesses may require a basic ERP system, while large enterprises need more advanced features. Choosing scalable software ensures that the ERP can grow alongside the company’s expansion.
Scalability also prevents unnecessary costs, allowing businesses to upgrade features as needed. Investing in a flexible ERP system supports long-term success without frequent system replacements.
-
Consider Mobility and E-Commerce Integration
Modern businesses require remote access and e-commerce compatibility. An ERP system with mobile support allows manufacturers to manage operations from anywhere, improving efficiency and decision-making.
E-commerce integration ensures seamless order processing and inventory updates, reducing errors and enhancing customer satisfaction. A digital-friendly ERP helps businesses stay competitive in today’s market.
-
Compare Pricing Structures and Long-Term Investment Value
ERP solutions come at different price points, and businesses should evaluate costs based on features and benefits. Some software providers offer subscription-based pricing, while others charge a one-time fee.
A cost-effective ERP system delivers long-term value by reducing manual work, improving efficiency, and increasing profitability. Comparing pricing structures helps businesses find a solution that fits their budget and needs.
-
Select an ERP Provider with Experience in the Beverage Sector
An experienced ERP provider understands the unique challenges of alcohol manufacturing. Choosing a vendor with industry expertise ensures smoother implementation and better support.
Manufacturers should research vendors, read reviews, and request product demos before making a decision. Working with a trusted provider guarantees reliable software and ongoing assistance.
How ERP Software Integrates with Other Systems in Alcohol Manufacturing Industry
For alcohol manufacturers, seamless integration between ERP and other business systems is crucial for efficiency and accuracy. Modern ERP solutions connect with accounting software, supply chain management, and customer relationship management (CRM) systems. This allows businesses to automate processes, synchronize data, and enhance decision-making.
By integrating with accounting tools, ERP automates financial transactions, ensures tax compliance, and generates reports accurately. Supply chain integration streamlines inventory management, shipment tracking, and logistics coordination, reducing delays and errors.
Additionally, ERP connects with CRM platforms to enhance customer interactions, improve order management, and boost sales forecasting. With IoT integration, manufacturers can monitor production in real time, optimize machine performance, and reduce downtime. These seamless integrations create a connected ecosystem that enhances efficiency and business growth.
HashMicro’s Hash Manufacturing Automation ERP for Alcohol Manufacturing Industry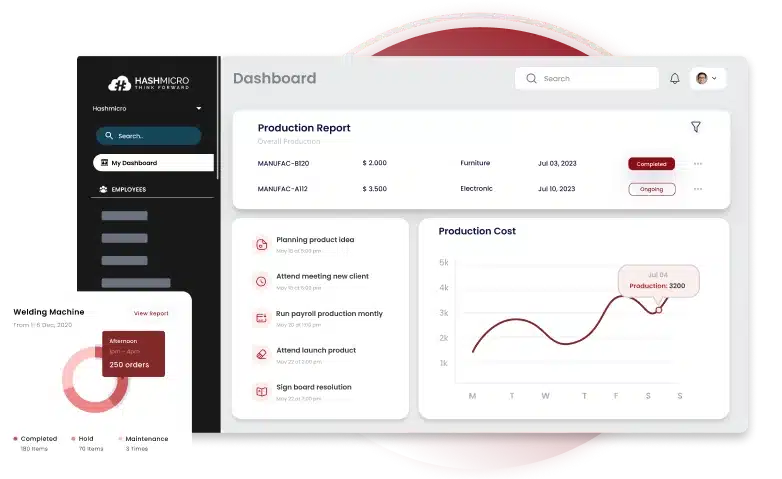
HashMicro’s ERP is a powerful software solution designed to streamline and automate operations in alcohol manufacturing. It integrates production, inventory, compliance, and sales tracking into one system, ensuring better efficiency and accuracy. By eliminating manual errors and optimizing processes, HashMicro ERP helps businesses improve productivity and reduce operational costs.
With HashMicro ERP, alcohol manufacturers in the Philippines can simplify compliance, enhance inventory management, and adapt to market changes seamlessly. Real-time data and automation empower businesses to make informed decisions and maintain a competitive edge. Take the next step towards efficiency, schedule a free demo today and see how HashMicro can transform your operations!
Conclusion
ERP is a game-changer for the alcohol manufacturing industry in the Philippines. It helps businesses improve compliance, streamline operations, and boost profitability.
By choosing the right ERP system like HashMicro, manufacturers can overcome industry challenges and achieve long-term success. Investing in ERP is a smart move for companies aiming for growth and efficiency.
For alcohol manufacturers in the Philippines, investing in ERP software means long-term growth, improved productivity, and a seamless operation. By choosing a system tailored to their needs, businesses can overcome challenges and maximize profitability.
FAQ About ERP for Alcohol Manufacturing Industry
-
Why business needs ERP?
ERP can reduce risk. It helps companies manage daily operations by preventing data duplication and inaccuracies and maximizing overall efficiency. Another benefit is improved efficiency, as ERP automates business processes across departments, eliminating costly and unnecessary repetitions.
-
What are the four types of ERP?
The four types of ERP are on-premise, cloud-based, hybrid, and open-source. On-premise ERP is installed on company servers and offers full control over data but requires high maintenance. Cloud-based ERP is hosted online, providing accessibility, scalability, and lower upfront costs. Hybrid ERP combines both, allowing businesses to store sensitive data on-premise while using cloud features. Open-source ERP offers customization and flexibility but requires technical expertise for implementation and maintenance.
-
What is the purpose of using ERP?
ERP is designed to integrate and automate business processes, improving efficiency, accuracy, and decision-making. It centralizes data from different departments, reducing manual work and eliminating silos. By streamlining operations like inventory, production, finance, and compliance, ERP helps businesses reduce costs, boost productivity, and scale effectively in a competitive market.
-
What is ERP used for in manufacturing?
In manufacturing, ERP is used to automate production, track inventory, and manage compliance requirements. It optimizes supply chain operations, ensuring raw materials are available when needed. It also improves demand forecasting, reduces waste, and enhances production scheduling. With real-time data, manufacturers can make informed decisions, minimize downtime, and maximize profitability.