The printing industry covers a wide range of services, from tarpaulins to customized prints, so smooth operations are essential to keep up with the demands. Therefore, ang ERP software para sa printing ay tumutulong sa pag-aayos ng workflows at pag-iwas sa errors.
ERP (Enterprise Resource Planning) is a set of software that makes every business process from getting a quote to delivering services smoother and hassle-free. It cuts down wasted time, boosts profits, and keeps everything organized so work gets done faster and more accurately.
However, is that all an enterprise software can do? Of course not, as there are a lot more that it’s capable of. Hence, in this article, you will learn why ERP for the printing industry is important and how it can improve the printing and packing industry’s workflows.
Key Takeaways
|
Table of Contents
What is ERP for the Printing Industry?
ERP for the printing industry is a complete software that helps businesses run more efficiently. It connects different processes, so teams can process orders, oversee production, and coordinate deliveries in one system.
This system helps by keeping inventory levels accurate, making sure raw materials don’t run out in the middle of a job. It also calculates costs properly, so businesses know exactly how much each print run will cost.
For example, when a customer orders 10,000 brochures, the ERP automatically checks if there’s enough paper and ink. If not, it alerts the team to restock before production even starts. It also calculates costs down to the last cent, so there are no pricing mistakes.
When it’s time to print, the system schedules jobs efficiently, preventing machines from sitting idle or getting overloaded.
Benefits of ERP for Printing Sector
- Manage the entire production process: Handle everything from quote requests to job completion, delivery, invoicing, and performance analysis in one system.
- Ensure accurate financial tracking: Use a comprehensive accounting system with full general ledger support to maintain financial accuracy and compliance.
- Seamlessly integrate with JDF-enabled systems: Connect with all JDF-compatible machines and software to streamline production workflows.
- Reduce costs and increase business value: Improve efficiency and profitability with built-in innovations designed to optimize printing operations.
These are just several of many benefits of ERP for the printing industry. However, there are way more benefits that a business can gain by implementing this system, as ERP modules and their benefits offer different functionalities based on the area it covers.
Key Features of ERP for Printing and Packaging Industry
ERP software includes various features that can support printing businesses. Below are the key features that are essential to the printing industry:
- Order Processing and Management: Captures job details, customer specifications, and deadlines while updating the order status at every stage until completion.
- Inventory Management: Monitors stock levels for paper, ink, and consumables, updating quantities in real time and triggering restock requests when supplies run low.
- Scheduling and Job Planning: Allocates tasks based on machine availability, job complexity, and production deadlines while maintaining a structured workflow.
- Shop Floor Management: Displays real-time production data, tracks machine performance and operator assignments, and updates job progress throughout the process.
- Job Costing: Calculates total expenses by analyzing resource consumption, machine runtime, and labor hours, providing a detailed cost breakdown for each print job.
- Purchasing and Invoicing: Generates purchase orders based on material requirements and processes invoices for completed jobs while maintaining accurate transaction records.
- Complete Financial Management: Logs all financial transactions, including accounts payable, accounts receivable, and general ledger entries, while maintaining accurate documentation.
- Analysis and Reporting: Compiles operational data, produces reports on production efficiency and material consumption, and tracks financial performance based on key metrics.
- Web-to-Print Integration: Connects online ordering platforms with the internal system to process customer orders directly within production workflows.
- JDF Integration: Standardizes job data exchange between machines and software to maintain consistency in job specifications throughout production.
Example of a Digital Printing Order Process in an ERP
A digital printing ERP connects every step of the order process, from customer requests to final delivery. Below are the example of how an order is processed using ERP software:
1. Online Ordering Platform
A company integrates its ERP with an online ordering platform, allowing customers to place printing orders directly through a dedicated website. Customers upload design files (PDF, AI, PSD, etc.), which are automatically linked to the ERP system.
2. Document Validation
After placing an order, the ERP’s validation module reviews the uploaded files to check compliance with printing specifications, such as resolution, color mode (CMYK), and margins.
If any issues are detected, the system notifies the customer through the online platform for necessary corrections. If required, a secondary validation can be performed by the prepress team.
3. Order Processing
Once the files pass validation, the ERP automatically forwards the order to the production team. The system generates work orders containing printing details, deadlines, and material requirements to guide the production process.
4. Data Transfer to Production
The validated files move from the ERP to the RIP (Raster Image Processor) for final adjustments before printing. RIP converts design files into pixel-based data, optimizing them for printing machines to ensure accurate reproduction.
5. Production
The optimized files stored in the RIP are used to print orders using the company’s digital printing machines. These machines support various page description languages, such as PostScript and PCL, to ensure precise and high-quality output. The ERP continuously monitors production progress and inventory levels in real time.
6. Shipping and Billing
After printing is complete, the ERP automatically generates delivery notes and corresponding invoices. Orders are shipped with all necessary documents, and shipping details are updated in the ERP. The system also sends invoices to customers and tracks payment status.
Best 5 ERP Software for Printing Companies
Knowing which is the best printing ERP software will make it easier for you to use it to its full potential for your business. Heto ang 5 top ERP software providers na dapat mong i-consider. (Here are the 5 top ERP software providers you should consider.)
1. HashMicro ERP for the Printing Industry
HashMicro’s ERP software makes printing business management simpler, faster, and more efficient. It brings all your operations into one system, so you can handle everything from orders to production without the hassle.
With fully customizable modules, the system adapts to your unique workflow. Whether it’s tracking inventory, managing costs, or automating WIP calculations, every feature is built to keep things running smoothly.
Furthermore, the user-friendly interface makes it easy to navigate, and expert consultants are always ready to help with setup and support.
You also get unlimited user access, real-time reporting, and seamless IoT integration—all at a competitive price that works for businesses of any size.
Curious to see how it works? Try the free demo and experience how HashMicro’s ERP can transform your printing business.
2. WinMan ERP Software
WinMan ERP offers a complete system for the printing and packaging industry. It provides tools to manage production, track costs, and define print specifications.
The software integrates CRM, production control, job tracking, reporting, and accounting into one platform. This structure allows teams to monitor job progress, verify expenses, and maintain order accuracy without switching between multiple systems.
With real-time data access, businesses track material usage, control expenses, and adjust production schedules. This setup improves cost efficiency, minimizes waste, and keeps deliveries on time.
3. Printify Printing Software
Printify uses competition among print providers to lower printing costs while maintaining product quality.
The system adjusts to demand, allowing companies to process bulk orders without delays, especially during peak seasons. Automated order routing assigns print jobs to the best available provider, avoiding production bottlenecks.
A large partner network ensures a steady supply chain, preventing order disruptions. This structure allows businesses to focus on customer satisfaction and business expansion.
4. Eresource ERP Software
Eresource ERP is an enterprise resource planning system designed for multiple industries, including manufacturing, construction, pharmaceuticals, and logistics.
The software includes modules for finance, sales, purchasing, inventory, production, and quality control. It connects business processes in a single system, allowing companies to track operations and access real-time data.
With a flexible and scalable structure, Eresource ERP adapts to businesses of all sizes, providing tools to manage resources effectively and improve workflow efficiency.
5. Printlogic ERP System
Printlogic ERP is a specialized software for the printing industry, covering every stage of print management. It supports estimating, quoting, production planning, inventory tracking, and invoicing in a single platform.
The system provides tools to oversee printing operations, monitor material usage, and maintain cost accuracy. By centralizing print-related tasks, Printlogic simplifies job coordination and order processing.
With an intuitive interface and advanced features, Printlogic offers a structured approach to managing print production while maintaining quality and workflow efficiency.
Aside from these five recommendations, there are also plenty of ERP software in the market, each catering to different companies with varying needs. So, if you’re curious about other solutions, read our comprehensive review about the best ERP system software in the Philippines.
Conclusion
ERP software for the printing industry makes managing orders, production, and inventory easier and more efficient. With real-time tracking and automation, businesses can control costs, prevent material shortages, and meet tight deadlines without hassle.
HashMicro’s ERP helps printing businesses work smarter by putting everything in one system, wala nang kalat-kalat na spreadsheets! (no more cluttered spreadsheets) With easy-to-use features and expert support, it simplifies job tracking, cost calculation, and production scheduling.
Want to see how it can help your business? Try the free demo and experience how HashMicro’s ERP can take your printing business to the next level!
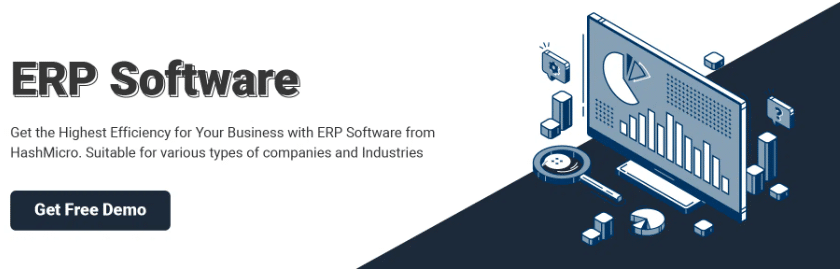
Frequently Asked Questions on ERP for the Printing Industry
-
How does an ERP system enhance quality control in printing operations?
ERP systems improve quality control by tracking production processes in real time. They also detect defects early, ensure compliance with industry standards, and help businesses improve their operations continuously.
-
Can ERP software integrate with existing Customer Relationship Management (CRM) tools in a printing business?
Most ERP systems allow integration with CRM tools to connect sales, customer service, and production teams. This integration improves communication, ensures accurate data sharing, and enhances customer relationships.
-
How does ERP software support financial management in the printing industry?
ERP software automates accounting tasks and generates real-time financial reports. It also manages budgets, tracks expenses, and provides insights to help businesses make informed financial decisions.
-
What role does ERP play in managing supply chain logistics for printing companies?
ERP systems help businesses optimize procurement, monitor inventory levels, and coordinate with suppliers. They also ensure on-time material delivery, keeping production schedules smooth and efficient.
{
“@context”: “https://schema.org”,
“@type”: “FAQPage”,
“mainEntity”: [{
“@type”: “Question”,
“name”: “How does an ERP system enhance quality control in printing operations?”,
“acceptedAnswer”: {
“@type”: “Answer”,
“text”: “ERP systems improve quality control by tracking production processes in real time. They also detect defects early, ensure compliance with industry standards, and help businesses improve their operations continuously.”
}
},{
“@type”: “Question”,
“name”: “Can ERP software integrate with existing Customer Relationship Management (CRM) tools in a printing business?”,
“acceptedAnswer”: {
“@type”: “Answer”,
“text”: “Most ERP systems allow integration with CRM tools to connect sales, customer service, and production teams. This integration improves communication, ensures accurate data sharing, and enhances customer relationships.”
}
},{
“@type”: “Question”,
“name”: “What role does ERP play in managing supply chain logistics for printing companies?”,
“acceptedAnswer”: {
“@type”: “Answer”,
“text”: “ERP systems help businesses optimize procurement, monitor inventory levels, and coordinate with suppliers. They also ensure on-time material delivery, keeping production schedules smooth and efficient.”
}
},{
“@type”: “Question”,
“name”: “How does ERP software support financial management in the printing industry?”,
“acceptedAnswer”: {
“@type”: “Answer”,
“text”: “ERP software automates accounting tasks and generates real-time financial reports. It also manages budgets, tracks expenses, and provides insights to help businesses make informed financial decisions.”
}
}]
}