Managing finished goods inventory is crucial to maintaining smooth operations and driving profitability in the dynamic business world. As businesses grow, optimizing how finished goods are tracked and managed becomes a top priority for inventory managers, ensuring they can effectively meet customer demands.
One of the biggest challenges in inventory is maintaining accuracy and ensuring seamless integration across systems, such as production, sales, and distribution. Without efficient management, companies face risks of overstocking, stockouts, and delays in fulfilling customer orders, which can severely impact business performance.
A recent study in Singapore showed how improved production planning helped reduce inventory levels for a leading company, significantly lowering storage costs and improving overall efficiency. This approach not only streamlined inventory management but also enabled better resource allocation, allowing the company to meet demand fluctuations with greater agility.
If you want better production planning, you can use the right software solution to support your business needs. Check out this article to see how innovative cloud inventory software can streamline the management of finished goods, supporting greater efficiency and business growth.
Table of Contents
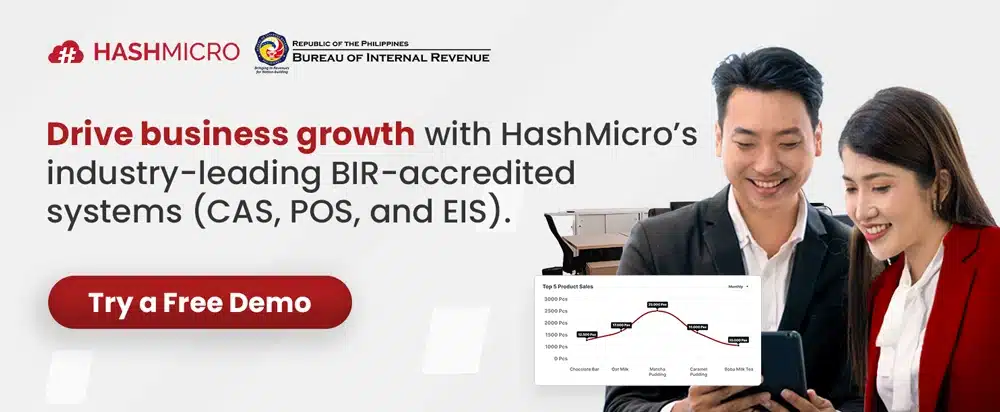
Key Takeaways
|
What is the Finished Goods Inventory?
Finished goods inventory refers to the stock of products that are entirely manufactured and ready to be sold to customers without requiring further processing or assembly. These products have completed the manufacturing cycle, transitioning from raw materials to finished products, and are now stored as inventory until purchased.
For example, if you own a clothing store, you might need an ERP system for the finished goods includes ready-to-wear apparel, such as shirts and dresses, ready for sale. However, in their raw material inventory stage, items like fabric rolls or thread do not qualify as finished goods since they require further work to become sellable products.
To effectively manage inventory, businesses must track the flow of products from when they are completed to when they are sold. Implementing a finished goods inventory formula and using advanced inventory management software can help businesses maintain optimal stock levels, reducing the risk of overproduction or stockouts while improving overall operational efficiency.
Why Is Finished Goods Inventory Important?
A clear understanding of finished goods inventory is essential for operational efficiency and financial accuracy in managing a business’s inventory. The finished goods formula is a powerful tool that helps businesses track their stock of goods, manage production, and maintain a healthy balance of raw materials to finished products.
This formula allows companies to optimize inventory management, minimize waste, and prevent stockouts. Below are several key reasons why managing stock of goods is critical for any successful business operation.
1. Improves financial budgeting
Accurately tracking finished goods inventory helps businesses improve financial budgeting by providing precise balance sheets and income statement data. Knowing the value of your stock of goods allows you to plan operating budgets more effectively for current operations and future projections.
This ensures better cash flow management and reduces financial risks. By leveraging the finished goods formula, companies can create more accurate financial reports that enhance strategic planning.
2. Records the number of current assets
Finished goods is crucial in maintaining accurate accounting records, especially regarding current assets. By using the finished goods formula, businesses can effortlessly track items across various stages of production, from raw materials to finished products.
This helps avoid costly accounting errors and ensures compliance with financial regulations. Accurate inventory records also safeguard businesses from potential audits or financial discrepancies.
3. Reduces waste of materials
Maintaining an optimal level of finished goods prevents businesses from overstocking, which can lead to unnecessary waste of raw materials and finished products. The finished goods inventory formula helps companies balance storing the right amount of raw materials and finished products.
This reduces warehousing costs and eliminates excess inventory that may go unused or expire. Ultimately, this optimization leads to more sustainable operations and cost savings.
4. Optimizes inventory management processes
Using the finished goods formula allows businesses to refine their inventory system by providing better visibility into production costs and labour efficiency. Tracking every stage, from raw materials to finished products, helps identify areas for improvement, whether through automation or process adjustments.
This optimization leads to smoother operations, fewer bottlenecks, and better resource use, ultimately improving the supply chain.
5. Minimizes stockouts
A well-maintained finished goods prevents stockouts, ensuring customers can receive orders without delays. By accurately predicting demand and adjusting the stock of goods accordingly, businesses can minimize backorders and avoid lost sales.
Utilizing the finished goods inventory formula allows companies to balance supply with demand, ensuring they have the right inventory levels to meet customer expectations without overextending resources.
3 Steps to Becoming Finished Goods
Before a product is categorized as finished goods, it must pass through several critical stages in the manufacturing process. Each stage is vital in transforming raw materials into a fully completed product, ready for sale or distribution.
Understanding these steps helps optimise the finished goods inventory formula and clarifies how raw materials transition into valuable goods stocks.
Using practical examples, let’s explore these three essential stages—raw materials, work in progress, and finished goods.
- Raw materials: The first step in producing finished goods involves gathering raw materials essential for manufacturing. For example, a company needs to maintain a sufficient inventory of raw materials, such as wood and plastic, to ensure a smooth transition from raw materials to finished products and generate the right stock of goods.
- Work in Progress: Working in progress (WIP) refers to items currently being manufactured but not yet complete. Like a half-assembled rowboat, these products have undergone part of the production process but still require labour and additional materials before becoming finished goods ready for distribution.
- Finished goods: Once all components are assembled and the product is complete, it becomes finished goods, ready for sale or distribution. Like a fully equipped rowboat, the finished goods inventory is now part of the company’s stock, available for shipment to customers or retail outlets.
Optimizing each production stage is key to managing inventory efficiently and accurately anticipating costs. Ready to simplify these steps with a software solution tailored to your business? Click the banner below for an instant price estimate and explore a streamlined approach to managing finished goods.
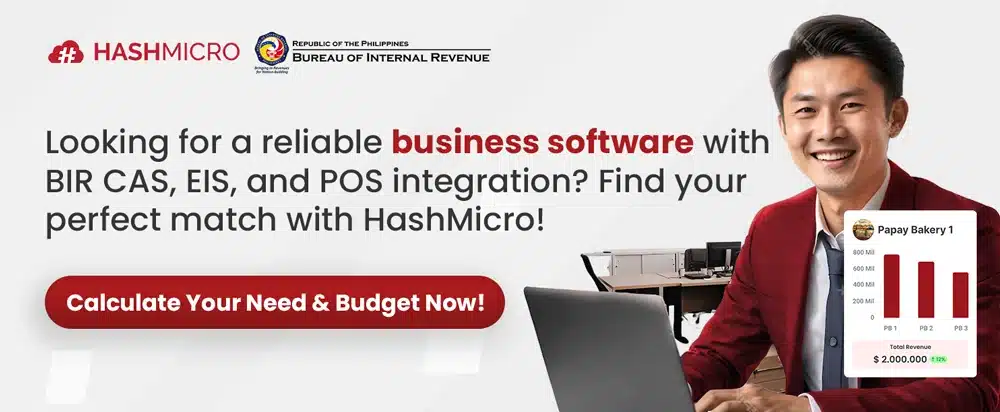
How to Calculate Finished Goods Inventory
Calculating finished goods is vital for any business to understand its stock value at the end of a fiscal period. Finished goods typically carry a higher value than items in earlier stages, like raw materials or work-in-progress, because direct labour, materials, and overhead have been added.
By using the inventory formula, businesses can accurately assess the value of their stock of goods and ensure their pricing strategy reflects the actual cost of production.
The finished goods formula is: Beginning finished goods inventory + Cost of Goods Manufactured (COGM) – Cost of Goods Sold (COGS) = Ending finished goods inventory.
To apply this formula, determine the value of your beginning finished goods from the previous period, add the COGM for the current period, and subtract the COGS. This provides the ending value of your finished goods, which is essential for financial reporting and determining whether stock levels are appropriate based on sales performance.
For example, if a company begins the quarter with $100,000 in finished goods, produces $90,000 worth of new products (COGM), and sells $70,000 of stock (COGS), the ending inventory value would be $120,000.
This finished goods inventory example shows how tracking the value from raw materials to finished products can help businesses maintain an optimal balance between production, inventory management, and sales growth. Implementing a barcode inventory system can improve this process by ensuring accurate inventory updates.
Managing Finished Goods With HashMicro’s Inventory Management Software
HashMicro’s Inventory Management Software is a comprehensive solution designed to help businesses efficiently manage their finished goods. With advanced features for tracking stock of goods, from raw materials to finished products, it streamlines operations and provides real-time insights into your inventory.
If you want to learn more about how HashMicro’s inventory management software can optimize your business operations, you can try a free demo today. This will give you a hands-on understanding of its capabilities and how it can improve your inventory management.
Some key features of HashMicro’s Inventory Management Software such as:
- RFID Warehouse Rack Stock In/Out Automation: RFID technology, integrated within warehouse management software, automates inventory tracking as it moves in and out of warehouse racks, providing instant updates on product location. This feature reduces manual handling and errors, ensuring accurate, real-time visibility of finished goods.
- Stock Forecasting: Stock forecasting analyzes sales trends and predicts future inventory needs, ensuring that finished goods meet customer demand without surplus or shortage. This feature helps optimize stock levels, minimize costs and enhance inventory efficiency.
- Quality Control Management: Quality control management enforces standards by checking to ensure each product meets specific criteria before entering finished goods inventory. This process helps maintain product quality, boosts customer satisfaction, and reduces returns.
- Pick, Pack, Delivery 3-Step Route Warehousing: This system streamlines order fulfilment with a structured picking, packing, and delivery route, making the dispatch of finished goods efficient and accurate. The organized workflow reduces delays and errors, supporting fast and precise order completion.
- FEFO (First Expiry First Out): FEFO prioritizes products with the earliest expiration dates, essential for industries handling perishable finished goods. This approach helps prevent waste by ensuring that older items are sold before they expire.
- Lot & Serial Number Management: Lot and serial number management tracks individual products, enabling accurate tracing and detailed inventory control. This feature supports quality assurance and compliance by recording product information at every stage.
- Return Management: Return management streamlines the handling of returned goods, performing quality checks before reintegrating items into the finished goods. This system maintains inventory accuracy and enables effective return processing.
- Stock Aging Report: The report provides data on when finished goods remain in stock, helping identify slow-moving inventory for timely management. This feature allows businesses to adjust stock levels based on demand trends and inventory age.
- Stock Reservations & Reporting: This feature allows businesses to reserve stock of goods for specific orders or clients, improving order fulfilment accuracy. Comprehensive reporting enhances inventory planning and ensures availability for high-priority demands.
- Integrated Barcode & QR Code Scanning: Barcode and QR code scanning improves tracking accuracy, enabling rapid and precise inventory updates for finished goods. This feature reduces manual entry errors and speeds up inventory management processes.
It also includes tools to implement the inventory formula, allowing businesses to quickly calculate and monitor their stock levels.
In addition to these features, HashMicro offers integration capabilities with third-party systems, ensuring seamless data flow across platforms. The software is also highly customizable, enabling companies to tailor its features to meet their business needs, whether managing raw material inventory or transitioning from raw materials to stock of goods.
Conclusion
Finished goods inventory represents the final products ready for sale, and its efficient management is crucial for ensuring smooth business operations. To achieve this, companies must invest in the right inventory management software that streamlines the tracking, reporting, and handling of finished goods, reducing inefficiencies and improving overall productivity.
One of the best solutions for handling the complexities of finished goods management is HashMicro’s Inventory Management System. HashMicro offers comprehensive tools to optimize inventory, automate processes, and ensure real-time visibility, making it the ideal choice for businesses looking to enhance their finished goods management.
To explore how HashMicro can benefit your business, you can try a free system trial and consult our professional team for personalized guidance.
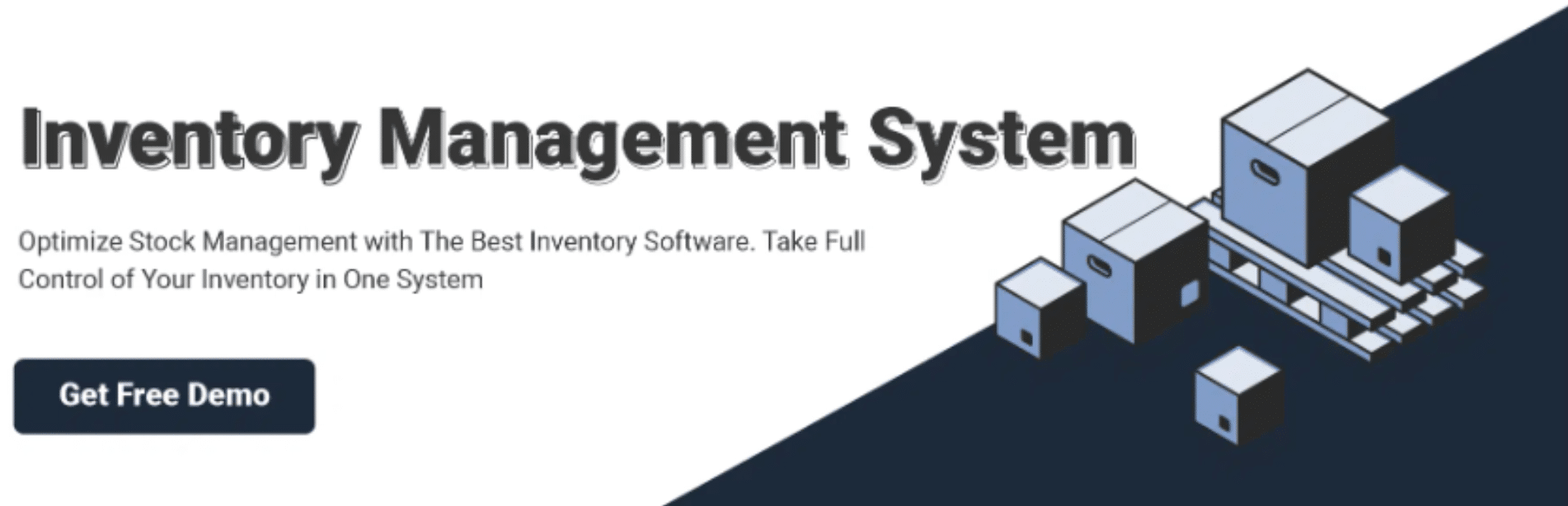
FAQ About Finished Goods Inventory
-
How do you record finished goods inventory?
Add the beginning finished goods inventory to the cost of goods manufactured. Subtract the cost of goods sold (COGS) during the accounting period. The resulting value is the ending finished goods inventory, which should be recorded in the balance sheet as a current asset.
-
What are examples of finished goods?
Some common examples of finished products include apparel that has completed its design process, food that has been cooked and is ready to be served at a restaurant, and computers that have completed production and can be sent to an electronics retailer.
-
What is the difference between WIP inventory and finished goods?
WIP Inventory: These products are currently at some phase of the manufacturing process. They’re in an unfinished state, and, therefore, you cannot sell them. Once a raw material meets human labor, you should consider it a work in process. Finished Goods: These are your final assembled products ready for sale.
-
What type of account is finished goods inventory?
Finished goods inventory is a current asset account. It represents the fully manufactured products that are ready for sale but not yet sold. These goods are listed on the balance sheet under current assets because they are expected to be sold within the normal operating cycle, which provides liquidity for the business.
-
How are finished goods valued?
Finished goods are typically valued using the cost accounting method which includes all costs incurred to produce the goods, such as direct materials, direct labor, and manufacturing overhead.
The commonly used methods for valuation are First-In, First-Out (FIFO), Last-In, First-Out (LIFO), or weighted average cost, depending on the inventory management approach of the business. This valuation reflects the total cost of goods manufactured and impacts both the balance sheet and income statement.