Running a construction business isn’t easy, right? Construction equipment, big or small, is often overlooked, with many contractors focusing only on projects and labor. However, effective equipment management is key to long-term success and, sadly, often goes unnoticed.
Poorly managed equipment can lead to unexpected costs, downtime, and project delays, which impact both profitability and reputation. That’s a tough pill to swallow—ang hirap kaya!
The good news is, that with the right strategies, you can gain full control over your equipment, improve visibility, and boost profitability. In this article, we’ll dive into effective practices you can apply to your construction tools management process, helping your business grow and succeed from the ground up.
Key Takeaways
|
Table of Contents
Why Good Construction Equipment Management Matters
Construction equipment management involves key aspects like cost, maintenance, and usage. Effective management ensures projects are completed safely, on schedule, and within budget. With proper equipment management, teams can:
- Extend equipment lifespan
- Lower safety hazards
- Minimize unexpected and extra costs
- Prevent delays in project timelines
- Reduce the risk of avoidable injuries
The success of a construction project is closely linked to well-organized equipment management. Managers who prioritize this know which equipment is used most or least, when maintenance is due, and what requires repairs or replacements.
8 Tips to Manage Construction Equipment Effectively
Effectively managing construction asset equipment is essential to keeping projects on time and within budget. The right strategies help prevent costly delays and extend the life of your assets. Here are eight tips to streamline equipment management and improve project success.
1. Implement a Centralized Equipment Management System
A centralized asset management software is essential for effective equipment management. Investing in fleet management software and training staff to update data accurately ensures that equipment details are always accessible and up-to-date.
Key Benefits:
- Real-Time Tracking: Monitor the location, usage, and condition of each piece of equipment.
- Inventory Control: Maintain a complete inventory, tracking availability and condition.
- Data Integration: Merge data from various sources to create a holistic view of equipment performance and maintenance.
2. Manage Equipment Requests, Allocation & Costs Centrally
When you have multiple worksites, managing requests and allocations centrally helps keep everything organized. A construction project management software lets you track availability, process requests, and monitor delivery times. You can also adjust equipment costs based on the needs of each project or location.
Benefits:
- Centralized Requests: A centralized system helps track equipment availability, manage requests, and allocate resources as needed.
- Cost Allocation: Adjust equipment rates for different job sites based on factors like location, project density, or usage duration.
3. Set Clear Protocols and Provide Training for Equipment Usage
Clear guidelines and proper training help prevent misuse and ensure safe equipment operation. Establishing detailed usage instructions, restricting access to authorized users, and assigning responsibility to operators helps keep equipment safe and efficient.
Key Components:
- Usage Guidelines: Develop procedures for safe operation and clear guidelines for each equipment type.
- Access Control: Restrict equipment use to authorized, trained personnel.
- Accountability: Assign responsibility to operators or teams to ensure accountability.
4. Conduct Routine Inspections and Schedule Maintenance Regularly
Regular inspections and scheduled maintenance prevent breakdowns and keep equipment in good shape. Using asset management software to log inspections and schedule maintenance helps you address issues early and maintain a record of all upkeep activities.
Inspection & Maintenance Approaches:
- Regular Inspections: Inspect equipment during pickup and return, identifying any wear or damage early.
- Preventive & Predictive Maintenance: Schedule regular maintenance based on usage and use predictive analytics to preemptively address issues.
5. Optimize Equipment Utilization and Track ROI
Using your equipment wisely and tracking its ROI is the key to getting the most bang for your buck! By diving into usage data, you can spot which tools bring the biggest returns and adjust your buying strategy to focus on what’s used the most. Sayang naman if equipment just sits around collecting dust, right?
Utilization Tips:
- Equipment Allocation: Match equipment to project needs to keep everything active and avoid downtime.
- ROI Calculation: Monitor equipment usage to see which tools are hitting targets and which aren’t pulling their weight.
6. Leverage Telematics and IoT for Real-Time Monitoring
Telematics and IoT allow you to monitor equipment performance and construction asset management in real-time. Adding IoT sensors to equipment and using a centralized system to analyze this data helps you make maintenance decisions before issues arise.
Key Benefits:
- Real-Time Data: Access up-to-the-minute data on equipment status, location, and performance.
- Predictive Analytics: Use predictive insights to anticipate maintenance needs, reducing unexpected breakdowns.
7. Foster Effective Communication and Collaboration
Clear communication among teams helps keep everyone informed about equipment status and needs. Using digital tools and apps, teams can quickly report issues, share updates, and collaborate effectively.
Communication Tools:
- Digital Platforms: Use mobile apps for real-time updates on equipment status and issues.
- Reporting Systems: Implement an easy-to-use reporting system for tracking equipment issues.
- Collaborative Tools: Encourage team collaboration through shared platforms, enabling team members to exchange updates and tips.
8. Conduct Regular Audits and Assessments
Routine audits are important for ensuring compliance and improving processes. Regularly inspecting equipment and reviewing management practices help maintain safety and identify ways to enhance efficiency.
Audit Components:
- Equipment Inspections: Ensure each piece is in optimal condition and meets safety standards.
- Process Reviews: Regularly assess equipment management processes to find inefficiencies.
- Compliance Checks: Verify adherence to safety and regulatory standards.
How to Choose the Right Construction Equipment
Another key factor in construction equipment management is selecting the right machinery for each project. Different projects and job sites have unique requirements that demand specific equipment. Here are some strategies for choosing the most suitable construction equipment for your project.
- Identify Project Requirements: Begin by assessing what each project needs to be completed efficiently, on time, and within budget. While every project has unique demands, reviewing similar past projects can serve as a helpful reference.
- Analyze Site Conditions: Consider the location and conditions of the job site, including terrain, climate, available space, and other factors that might affect equipment needs.
- Set a Budget: Budget constraints will play a major role in determining which equipment is feasible. Depending on the project’s budget, you may need to prioritize certain types of equipment.
- Research Suppliers: Find reputable suppliers nearby who can provide the required equipment on schedule.
- Make the Final Choice: Before finalizing equipment selection, carefully review warranties and complete the necessary contracts.
This approach helps you get the perfect equipment match for each project’s unique needs! Imagine having the right tools lined up, ready to go, without the hassle of last-minute adjustments; astig, di ba?
When to Retire and Replace Equipment
While maintenance is essential, knowing when it’s no longer worthwhile is equally important. Several factors can influence the decision to replace or retire a piece of equipment. Here are key considerations:
- Age and Usage: Manufacturer guidelines often specify the expected lifespan of equipment with regular use. However, you’ll need to assess your actual usage, which may be higher or lower than the typical threshold.
- Repair Costs: If repair expenses begin to exceed the value you’re getting from the equipment, it may be time to phase it out. Likewise, if you’re investing heavily in maintaining a piece that soon requires replacement, it might be more cost-effective to replace it now.
- Technological Advances: Equipment that still functions well can become outdated if newer technology offers greater efficiency and productivity. In such cases, upgrading to modern equipment may be beneficial.
- Project Needs: Construction project requirements evolve, and equipment that was essential at the start may become redundant later. Effective equipment management involves consistently evaluating project needs and adjusting accordingly, including selling or returning unneeded equipment.
- Safety Compliance: Older equipment may fail to meet current safety or environmental standards, which can pose risks. When equipment no longer aligns with these standards, it’s time to consider replacement.
These factors help ensure that equipment management supports project goals, cost-effectiveness, and safety.
Manage Construction Effectively with Construction Equipment Management Software
Managing construction equipment doesn’t have to be a guessing game. Imagine having instant access to the location, condition, and maintenance status of every piece of machinery on your sites—all from one platform.
HashMicro Asset Management Software brings this vision to life, making it easy to oversee equipment, cut down on unexpected costs, and keep your projects moving smoothly. With real-time data and automated insights, you’re equipped to make confident decisions that keep every job on schedule and within budget.
Below is the list of features that help the companies manage their equipment:
- Preventive Maintenance Scheduling: This feature is essential for construction equipment, as scheduled maintenance helps prevent unexpected breakdowns, ensuring equipment remains operational and extending its lifespan.
- Asset GPS Tracking: Knowing the precise location of equipment on various job sites is crucial in construction. GPS tracking provides real-time visibility, helping managers locate and deploy equipment efficiently.
- Asset Comprehensive Cost Reporting: Detailed cost reporting on maintenance provides valuable insights into the expenses associated with each piece of equipment. This data helps managers plan future maintenance budgets and optimize resource allocation.
- Asset Maintenance Budget: Tracking and managing the maintenance budget for each piece of equipment helps avoid unexpected costs and ensures compliance with allocated budgets, a key aspect of construction accounting to keep projects financially on track.
- QR Code Scanning for Facilities Request: Quick and efficient reporting of issues using QR codes allows employees to request repairs or maintenance instantly. This feature facilitates immediate responses to equipment issues to avoid delays.
Conclusion
Effectively managing construction equipment means planning ahead, maintaining regularly, and keeping a close eye on costs. By following best practices, construction managers can avoid costly breakdowns, reduce downtime, and keep every project moving smoothly. Walang aberya!
HashMicro’s Asset Management Software is the ultimate tool for construction companies looking to level up equipment management. With real-time tracking, preventive maintenance, and detailed cost reports, it has everything managers need to stay organized and proactive.
Give your team the power of HashMicro’s user-friendly software, and watch productivity soar across every job site. Say goodbye to hidden costs and hello to a smarter way of managing equipment.
Try the free demo today and see for yourself!
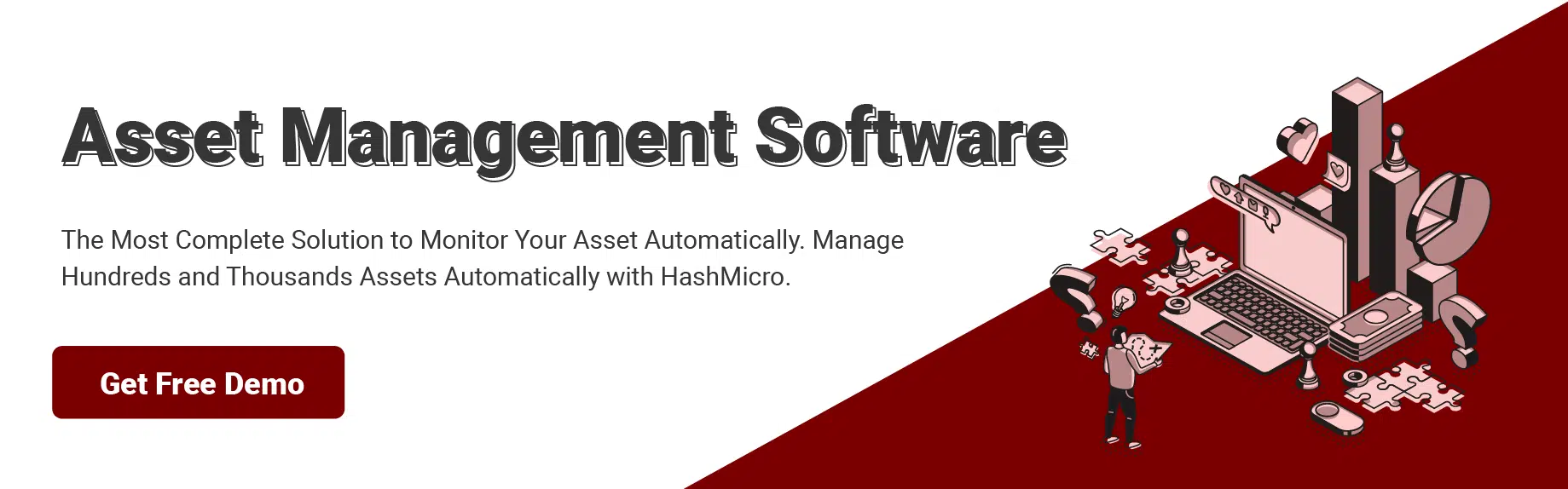
FAQ About Construction Equipment
-
What are the different types of construction equipment?
Construction equipment encompasses a wide range of machinery, including excavators, bulldozers, cranes, loaders, backhoes, and concrete mixers. Each type serves specific functions, such as earthmoving, material handling, and concrete mixing, essential for various construction tasks.
-
How do you determine the right size of equipment for a construction project?
Selecting the appropriate equipment size depends on factors like project scale, site conditions, material volume, and task complexity. Assessing these elements ensures optimal performance, efficiency, and safety on the job site.
-
What is the difference between renting and purchasing construction equipment?
Renting equipment offers flexibility and lower upfront costs, making it suitable for short-term projects or specialized tasks. Purchasing equipment involves higher initial investment but can be cost-effective for long-term use, providing ownership benefits and potential tax advantages.
-
What are the safety considerations when operating construction equipment?
Safety considerations include ensuring operators are properly trained and certified, conducting regular equipment inspections, adhering to manufacturer guidelines, and implementing site-specific safety protocols. These measures help prevent accidents and maintain a safe working environment.