Imagine a business that consistently meets customer demands without holding excess stock. This ideal situation is achievable through effective inventory optimization, which aligns stock levels with market needs.
Despite its advantages, managers face hurdles like fluctuating market demands, inaccurate inventory data, and supply chain uncertainties. Such challenges can result in either surplus stock or shortages, both detrimental to business success.
Research on Cornerstone International Philippines’ warehouse inventory system underscores the significance of robust inventory practices. Implementing structured inventory systems can substantially improve efficiency and cost savings.
As you continue reading, we’ll explore the intricacies of inventory optimization, its myriad benefits, and the techniques to implement it effectively. We’ll also highlight software solutions that can assist in refining your inventory management processes.
Table of Contents
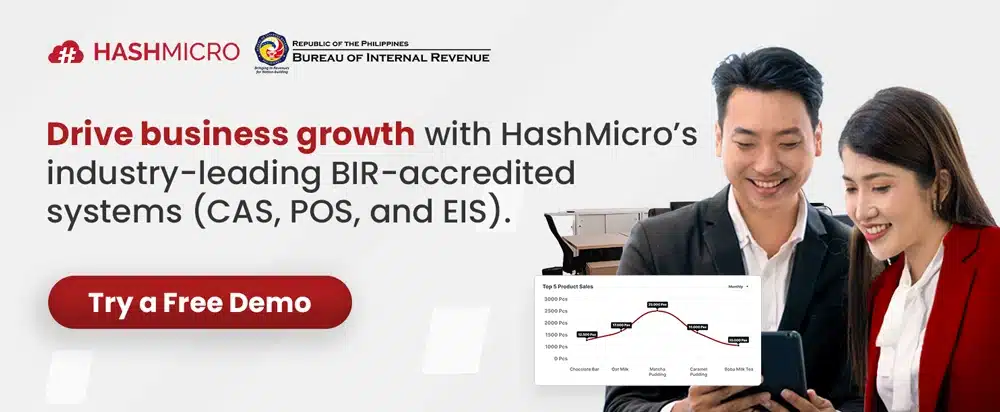
Key Takeaways
|
What is Inventory Optimization?
Inventory optimization is the process of maintaining the right inventory levels to meet customer demand while minimizing costs. It helps businesses avoid common issues like stockouts, overstocking, and backorders, ensuring that the right products are available when and where needed.
To optimize inventory effectively, businesses rely on various inventory techniques and tools that track stock in real time and accurately forecast demand. Key optimization techniques include demand forecasting, which uses historical data and market trends to predict future needs, and safety stock management to cushion against unexpected demand spikes or supply chain disruptions.
Additionally, calculating reorder points and monitoring inventory turnover is crucial for efficient inventory optimization. Reorder point calculations help determine the best time to restock, minimizing carrying costs and preventing excess inventory. Monitoring turnover rates provides insights into sales performance, assisting businesses to adjust stock levels accordingly.
Goals of Inventory Optimization
The primary goal of inventory optimization is balancing stock levels efficiently to support business growth and customer satisfaction. By implementing effective inventory techniques, companies can transform inventory management from a logistical challenge into a strategic advantage.
- Balance supply and demand: The key goal of inventory optimization is to balance supply with market demand, ensuring enough stock to meet customer needs without overstocking. This is achieved through accurate demand forecasting, analyzing historical sales data, and using predictive analytics to anticipate future trends.
- Minimize costs while maximizing service levels: Optimizing inventory helps reduce holding costs and excess stock while maintaining high service levels for customer satisfaction. Technologies like AI-driven analytics and cloud-based inventory systems improve demand forecasting, streamline supply chains, and enhance stock availability.
- Reduce waste and obsolescence: Inventory optimization techniques help identify slow-moving products early, enabling strategic decisions like markdowns to liquidate unsold stock. This approach reduces storage costs, minimizes waste, and prevents losses from obsolete products, especially in fast-evolving industries like electronics.
- Improve inventory turnover rates: By optimizing inventory, businesses can improve turnover rates, ensuring products move quickly through the supply chain. Higher turnover reduces the time goods spend in storage, lowering holding costs and freeing up capital for other business priorities.
- Enhance supply chain efficiency: Effective inventory optimization techniques streamline operations by maintaining optimal stock levels and reducing bottlenecks. This ensures timely product availability, improves order fulfillment rates, and supports smoother business processes.
Inventory Optimization Techniques
Inventory optimization techniques help businesses maintain the right inventory levels, reducing costs while meeting customer demand. By applying strategic methods, companies can optimize inventory efficiently and improve supply chain performance.
1. Demand forecasting
Demand forecasting uses historical sales data, market trends, and advanced analytics to predict future product demand. It helps businesses make informed decisions about inventory levels, production schedules, and supply chain needs.
For example, an outdoor apparel brand may analyze seasonal trends, weather forecasts, and past promotions to plan jacket production. This optimization technique minimizes stockouts, reduces excess inventory, and aligns resources with customer needs.
2. Inventory turnover ratio
The inventory turnover ratio measures how often inventory is sold and replenished over a specific period. It’s calculated by dividing the cost of goods sold (COGS) by the average inventory value, indicating inventory efficiency.
A high turnover ratio suggests strong sales but could risk stockouts, while a low ratio may signal overstock or declining demand. By analyzing turnover rates, companies can adjust pricing strategies, production plans, and supplier relationships to optimize inventory.
3. Safety stock calculation
Safety stock is a buffer to prevent stockouts during unexpected demand surges or supply chain disruptions. Companies calculate safety stock by multiplying daily sales by the desired buffer days, ensuring continuous product availability.
For example, if a business sells 200 units daily and wants a seven-day safety stock, it needs 1,400 extra units. This technique balances the risk of lost sales with the cost of carrying additional inventory, helping to optimize inventory levels.
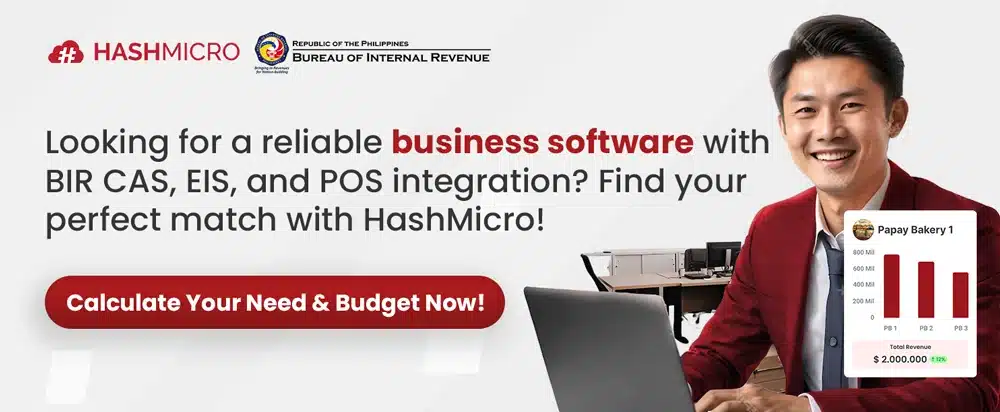
Advantages of Inventory Optimization
Inventory optimization provides key advantages that enhance business efficiency, reduce costs, and improve customer satisfaction. Here are some of the main benefits:
1. Reduced holding costs
Holding costs include storage, insurance, utilities, and financing for unsold inventory. Inventory optimization minimizes these costs by maintaining optimal stock levels, minimizing excess inventory, and freeing up storage space.
Accurate demand forecasting reduces the risk of obsolescence, especially for perishable or seasonal products. This ensures companies invest more in high-margin items and less in stagnant stock.
2. Improved cash flow
Optimizing inventory improves cash flow by reducing the capital in unsold stock and accelerating inventory turnover. Businesses can reallocate resources effectively when inventory levels are closely aligned with actual demand.
Just-in-time (JIT) inventory techniques and real-time tracking systems enhance financial flexibility by minimizing waste and maximizing liquidity. This enables companies to invest more in growth opportunities and strategic initiatives.
3. Enhanced customer satisfaction
Inventory optimization helps businesses meet customer demands promptly, reducing the chances of stockouts or backorders. Accurate demand forecasting ensures popular products are available when and where customers need them.
This reliability boosts customer satisfaction, fosters loyalty, and enhances the company’s reputation for dependability. Faster delivery times and improved service quality further boost the customer experience.
4. Increased productivity
Inventory optimization improves productivity by enabling better planning and resource allocation based on demand patterns. Companies can predict raw material needs accurately, reducing production delays due to stock shortages.
Automation of inventory techniques, like stock tracking and order generation, reduces manual errors and administrative workload. This results in smoother operations and more efficient use of workforce and resources.
5. Minimized risks of overstock or stockouts
Using optimization techniques, businesses can balance inventory levels to prevent both overstock and stockouts. Regularly reviewing sales trends and market demands helps align stock with actual needs.
Advanced inventory optimization tools automate replenishment when levels drop to critical thresholds. This proactive approach ensures continuous product availability while minimizing excess inventory.
6. Improved Supplier Relationships
Inventory optimization fosters stronger supplier relationships through consistent and accurate ordering patterns. Accurate forecasts allow businesses to place timely orders, reducing last-minute requests that strain supplier operations.
Predictable demand helps suppliers plan their inventory and production more efficiently. This collaboration builds trust, improves reliability, and may lead to better pricing or priority service during high-demand periods.
Inventory Optimization Challenges
While inventory optimization offers numerous benefits, businesses face several challenges that can complicate the process. Recognizing these challenges helps companies develop strategies to optimize inventory effectively.
-
Fluctuating market demands
Rapid shifts in customer preferences, seasonal changes, and economic fluctuations can create unpredictable demand patterns. For example, an economic downturn may reduce demand for luxury items, leading to excess inventory and reduced turnover.
To manage this volatility, businesses should adopt agile inventory techniques like just-in-time (JIT) practices and invest in advanced data analytics to identify emerging trends. Regularly updating inventory strategies based on real-time market data helps maintain optimal inventory levels despite fluctuating demands.
-
Supply chain disruptions
Supply chain disruptions caused by natural disasters, geopolitical issues, or pandemics can lead to delays and inventory shortages. These disruptions make it challenging to maintain steady inventory levels, affecting both supply and demand forecasts.
Companies can mitigate risks by diversifying suppliers, maintaining buffer stock for critical items, and investing in flexible supply chain management systems. Adopting these optimization techniques ensures businesses can respond quickly and efficiently to unexpected supply chain challenges.
-
Technological challenges
Outdated inventory management systems and manual processes hinder effective inventory optimization. A lack of system integration can result in inaccurate demand forecasts and inefficient stock levels, especially if inventory systems are not connected to sales or forecasting platforms.
To overcome this, businesses should invest in the best inventory management software, which facilitates real-time tracking and seamless integration across departments. Implementing advanced technology not only optimizes inventory but also improves overall operational efficiency.
Inventory Optimization Best Practices
Implementing best practices in inventory optimization is essential for businesses aiming to maintain efficiency and adapt to changing demands. Here are three key practices to optimize inventory effectively.
1. Lean inventory management
Lean inventory management focuses on maintaining only the inventory levels necessary to meet customer demand. This approach reduces storage costs, minimizes waste, and improves cash flow by eliminating excess stock.
For example, car manufacturers use just-in-time (JIT) inventory techniques to receive parts only when needed, optimizing production efficiency. Regular analysis of sales patterns and demand helps companies adapt quickly to market changes, ensuring inventory levels align with actual needs.
2. Strategic supplier relationships
Building strong relationships with suppliers enhances inventory optimization through better communication and collaboration. Reliable suppliers provide timely information on product availability, lead times, and potential disruptions, allowing for more accurate inventory planning.
Companies can negotiate flexible order quantities and faster deliveries, reducing the risk of stockouts or overstock situations. Strong partnerships also support joint forecasting and planning efforts, aligning inventory techniques with market demands.
3. Continuous improvement and adaptation
Inventory optimization is an ongoing process that requires continuous evaluation and adaptation. Businesses should regularly analyze key performance indicators, such as sales trends and supply chain efficiency, to identify areas for improvement.
Integrating advanced technologies like AI-driven forecasting tools can enhance decision-making and optimize inventory levels. This commitment to continuous improvement ensures businesses remain agile, responsive, and competitive in evolving markets.
How Hashmicro Optimizes Your Inventory Management System
HashMicro offers a robust Inventory Management System designed to enhance efficiency and accuracy in inventory optimization processes. One key feature is automated inventory tracking and demand forecasting, which are seamlessly integrated into our IMS solution for real-time inventory optimization.
Experience the capabilities of HashMicro’s IMS Solution through a free demo. Explore how automation optimizes inventory management, reduces stock discrepancies, and improves inventory accuracy, ensuring better stock control and faster replenishment.
Why choose HashMicro? Our IMS software automates critical tasks like inventory monitoring, stock level optimization, and demand forecasting, minimizing manual errors and increasing operational productivity. Its seamless integration with other business modules provides a comprehensive solution for inventory management.
It helps businesses improve inventory management best practices while optimizing stock levels and resource efficiency. Below are some of the key features of HashMicro’s IMS Solution:
- RFID Warehouse Rack Stock In-Out Automation: This feature automates inventory movements using RFID tags, enabling real-time tracking of stock entering and leaving warehouse racks. It improves accuracy by reducing manual errors and speeding up stock audits.
- Fast-Moving & Slow-Moving Stocks Analysis: It identifies which products sell quickly and which stay in inventory longer through data analysis. This helps businesses optimize stock levels by focusing on high-demand items and minimizing overstock.
- OCR for Efficient Receiving Processes: OCR technology automatically scans and extracts data from incoming shipment documents. This reduces manual data entry, ensuring faster and more accurate receiving processes.
- Advanced Stock Forecasting: This feature uses historical sales data and market trends to predict future inventory needs. It helps maintain optimal stock levels and reduces the risk of stockouts or overstocking.
- Run Rate Reordering Rules: It automates reordering based on consumption rates, triggering restock orders when inventory reaches predefined thresholds. This ensures continuous stock availability without over-purchasing.
- Racking Capacity Management with Putaway Strategy: The system optimizes storage by calculating racking capacity and suggesting the best putaway locations. This improves space utilization and reduces the time spent locating items.
- Stock Reservations & Real-Time Reporting: Businesses can reserve stock for specific orders while monitoring real-time inventory updates through the inventory report. This ensures priority items are always available and improves stock visibility.
- Quality Control Management: This feature tracks product quality checks at various supply chain stages. It helps identify defects early, reducing the risk of distributing substandard products.
- Lot & Serial Number Management: It assigns unique lot and serial numbers to products, enabling detailed tracking throughout the inventory lifecycle. This enhances traceability and simplifies recalls if needed.
- Pick, Pack, and Delivery 3-Step Route Warehousing: The system streamlines warehouse operations into picking, packing, and delivery steps. This structured workflow improves order accuracy and speeds up fulfillment processes.
These capabilities enhance stock visibility, reduce operational costs, and improve inventory accuracy. With HashMicro’s IMS Solution, businesses can optimize inventory, maximize productivity, and achieve long-term operational efficiency.
Conclusion
Inventory optimization is crucial for businesses aiming to maintain efficiency, reduce costs, and improve stock management. The right inventory management software helps businesses streamline operations, reduce manual errors, and achieve real-time inventory visibility, leading to improved decision-making and resource allocation.
HashMicro’s Inventory Management System is one of the best solutions for businesses in the Philippines. It offers comprehensive features like automated stock tracking, advanced forecasting, and real-time reporting, designed to meet the unique needs of the Philippines businesses and support their growth.
Ready to experience the benefits firsthand? Sign up for a free demo of HashMicro’s IMS Solution today and discover how it can transform your inventory management processes for greater efficiency and productivity.
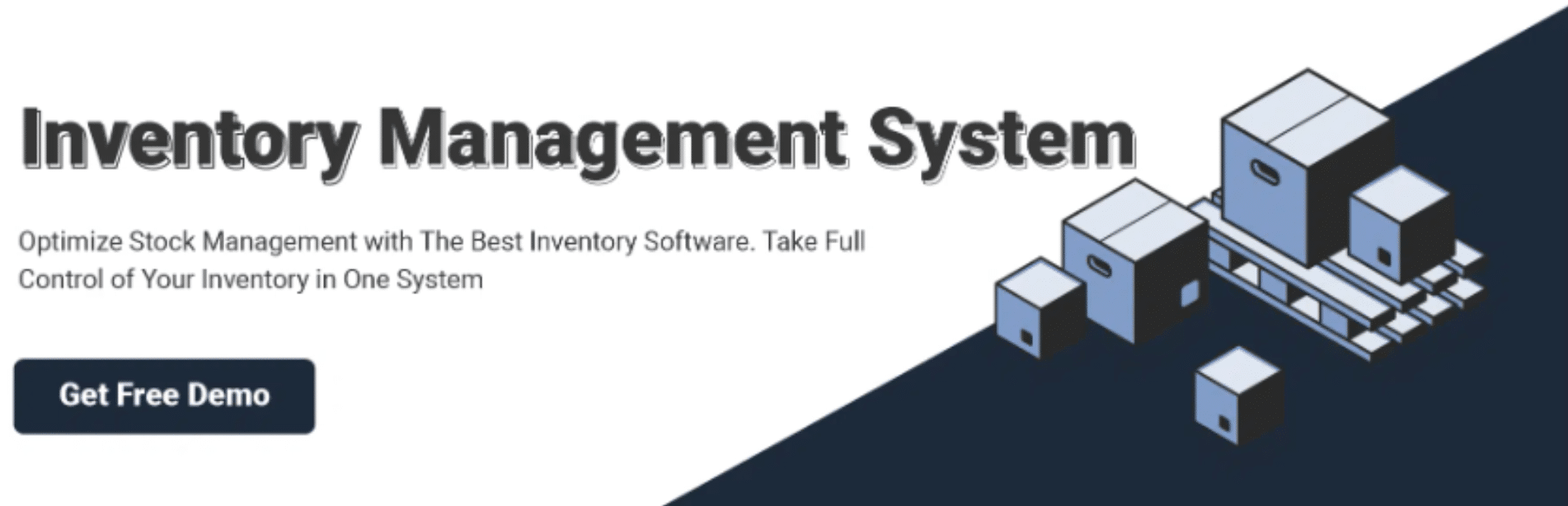