Downtime is expensive, frustrating, and often avoidable, yet nearly every business faces this challenge regularly. In fact, unplanned downtime costs industries billions annually, often resulting directly from poor or inadequate maintenance scheduling.
To avoid becoming part of these costly statistics, implementing an effective maintenance scheduling strategy is essential. Properly scheduled inspections and servicing help your equipment stay reliable, productive, and operational when you need it most.
Here’s a practical guide to mastering maintenance scheduling, so your company can avoid downtime and keep operations running at peak performance.
Key Takeaways
|
Table of Contents
What is Maintenance Scheduling?
Maintenance scheduling is strategically planning tasks by clearly defining who will do them, what exactly needs to be done, when they’ll take place, and where they’re required. It focuses on efficiently managing and performing activities like equipment checks, preventive care, and corrective repairs.
Through scheduled maintenance, you can optimally allocate available working hours according to your resources. Typically, tasks are prioritized, with the most critical work orders addressed first.
The main goal of maintenance scheduling is to reduce downtime while optimizing equipment performance and longevity.
Benefits of Maintenance Scheduling
Maintenance scheduling and maintenance planning are closely connected processes. When both are utilized correctly and completely, maintenance scheduling offers numerous advantages:
- Higher productivity: Tasks become clearly organized. As a result, workers can complete more work in less time.
- Increased efficiency: Resources are allocated effectively. Consequently, operations require less effort and generate less waste.
- Decrease in spare parts: Proper scheduling reduces equipment breakdowns. Therefore, fewer spare parts are necessary.
- Improved overall workflows: Maintenance tasks are well-organized. Thus, the overall operational process runs more smoothly.
- Fewer injuries and less stress: Planned maintenance reduces hazards. This makes the workplace safer and less stressful.
- Reduced downtime: Scheduled tasks prevent unexpected breakdowns. As a result, equipment stays operational longer.
- Less resource movement: Efficient scheduling reduces unnecessary movement of tools, equipment, and staff. Hence, productivity increases.
- Fewer and lower costs: Proper planning decreases operational costs. This happens because it prevents emergency repairs and excess inventory.
Therefore, it is essential that planners schedule tasks accurately. They must rely on precise data to make effective decisions.
The Process of Maintenance Scheduling
Maintenance scheduling is usually handled by maintenance supervisors and maintenance planners. In large-scale operations with complex maintenance requirements, dedicated schedulers are often necessary. In smaller operations, individual supervisors or planners may take on this responsibility.
When planning maintenance work, teams must consider several factors to ensure everything is accounted for. Following these steps helps keep the process organized:
- Review the work order and confirm details with the maintenance planner.
- Gather all required resources, including tools, personnel, supplies, spare parts, and safety equipment.
- Verify that the asset is available and prepared for maintenance.
- Assign the task to a technician for execution.
- Monitor progress and implement improvements as needed.
Some maintenance tasks need to be scheduled on a recurring basis. In such cases, the scheduler must confirm that each work order is completed consistently and on time.
How to Make Maintenance Scheduling
Effective maintenance scheduling requires careful planning, collaboration, and the right approach to keep operations running smoothly. Below are key steps to help you create a well-structured and efficient maintenance schedule.
1. Get Organizational Buy-in
Before moving forward, secure support from your organization. Present your plan by highlighting how it reduces costs, increases return on investment, improves efficiency and productivity, and identifies weaknesses that need attention.
2. Assess the Current Situation
Gather representatives from all relevant departments, including technicians, crew leaders, supervisors, and key stakeholders. A collective discussion will provide a clearer understanding of the organization’s current maintenance challenges.
Use this information to outline the existing situation and develop a schedule that addresses these issues effectively.
3. Prepare the Necessary Resources
The maintenance planner must collaborate closely with the team to document processes, define roles, and establish responsibilities. Updating asset management software is crucial at this stage to reflect any changes.
A modern system ensures that updates are synchronized across all users, preventing miscommunication. Additionally, implement training sessions for any newly defined roles to ensure smooth execution.
4. Implement the Schedule
The objective is to integrate maintenance scheduling into the team’s routine. While it may take a few months for everyone to fully adapt, consistent coaching will help the team adjust.
It’s important to ensure that the maintenance planner focuses solely on scheduling while the rest of the team handles other responsibilities.
5. Establish a Review Process
Once the schedule is in place, regular evaluations are necessary to maintain its effectiveness. Acknowledge the efforts of your team and celebrate milestones to keep morale high. Gather feedback through surveys or discussions to identify areas for improvement.
Regular check-ins with the crew will help address any issues and ensure that the schedule continues to function efficiently.
6. Keep the System Evolving
Even after successfully implementing the schedule, ongoing improvements are essential. Regularly review performance metrics in meetings to ensure maintenance targets are being met. Adapt and refine processes as needed to maintain long-term efficiency and effectiveness.
Challenges of Maintenance Scheduling
Despite careful planning, maintenance scheduling comes with its own set of challenges that can disrupt workflows. Below are three challenges that the team often finds when they try to schedule maintenance:
1. Managing Unplanned Work vs Scheduled Tasks
Challenge:
Maintenance and asset managers often face disruptions from unplanned maintenance tasks that interfere with existing weekly schedules.
- Unplanned tasks are frequently (and incorrectly) prioritized over scheduled activities.
- Deciding whether unplanned work should supersede scheduled tasks can be difficult, especially when schedules are already finalized.
- Allowing unplanned tasks to take precedence reduces weekly compliance, increases maintenance backlog, and may lead to critical scheduled tasks being overlooked.
2. Overlooking Preventive Maintenance
Challenge:
Preventive maintenance is frequently neglected, as many maintenance programs become reactive over time, focusing primarily on breakdowns and emergencies.
- Technicians often operate in “firefighting” mode, causing planned preventive maintenance to be delayed or skipped.
- Neglecting preventive maintenance increases the likelihood of unexpected breakdowns, emergency repairs, and downtime.
- Prioritizing short-term production demands over preventive measures creates a false economy, negatively impacting long-term equipment reliability and uptime.
3. Accurately Estimating Maintenance Task Durations
Challenge:
Accurately estimating how long maintenance activities take is crucial yet often problematic. Initial time estimates from the project phase often become outdated, and CMMS data may not reflect realistic durations over the asset’s lifespan.
- Inaccurate estimates in CMMS result in ineffective scheduling, resource misallocation, and increased backlog.
- Overestimating task duration can inflate labor requirements, which leads to inefficiencies, idle resources, and excessive spare parts inventory.
- Underestimating duration can lead to unrealistic plans and affects morale, safety, and inventory management.
- Budget overruns in one area often require adjustments in other scheduled tasks, so resource imbalances and poor overall plan execution may occur.
- Financial consequences include increased operational expenses, reduced equipment availability, and potentially lower profitability.
Examples of Maintenance Scheduling
A maintenance schedule can be customized in countless ways to suit specific needs. However, to provide a general idea, here are some common elements typically included in maintenance schedules.
1. Public Transportation Maintenance Schedule:
- Agency/Organization: The entity responsible for managing and maintaining the equipment.
- Equipment Code: A unique identifier assigned to each piece of equipment.
- Equipment Description: A brief overview of what the equipment is and its function.
- Condition: The current state of the equipment, such as operational, requires repair, or near replacement.
- Age: The number of years the equipment has been in use.
- Remaining Useful Life: An estimate of how much longer the equipment can function effectively.
- Replacement Cost: The projected expense for replacing the equipment when necessary.
Although this example applies to public transportation, a similar structure can be adapted to various industries. For a more detailed approach, machinery maintenance schedules often include additional parameters.
2. Machinery Maintenance Schedule:
- Machine Name: The specific name or type of machinery being maintained.
- Condition: An assessment of the machine’s current operational state.
- Location: The physical placement of the equipment within the facility.
- Assigned To: The individual or team responsible for overseeing maintenance.
- Last Maintenance Date: The most recent date when maintenance was performed.
- Maintenance Frequency: The regular interval (in days) at which maintenance is scheduled.
- Next Maintenance Date: The planned date for the next maintenance session.
- Notes: Additional remarks or observations regarding the machine’s condition or any specific issues.
3. Refrigeration Maintenance Schedule
Below is an example of a structured refrigeration maintenance schedule tailored for large-scale operations:
Core Maintenance Tasks:
- Condenser Maintenance: Perform high-pressure cleaning of all air-cooled condenser coils to maintain efficiency.
- Evaporator Inspection: Conduct a thorough check of evaporators for signs of damage, ice buildup, or inefficiency.
- Drain Maintenance: Perform pressure cleaning of all drains to prevent blockages and water accumulation.
- Fan System Inspection: Assess all fan motors and blades for wear, alignment, and operational integrity.
- Temperature Calibration: Verify that refrigeration units maintain optimal temperatures within set tolerances.
- Cycle Performance Check: Analyze unit cycling patterns to detect any irregularities that may indicate performance issues.
- Refrigerant Level Assessment: Measure and record refrigerant levels to prevent inefficiencies or leaks.
Structural and Component Inspections:
- Door and Seal Integrity: Examine door gaskets and seals to prevent air leaks and ensure proper insulation.
- Hardware Maintenance: Inspect hinges and automatic door closers for wear and alignment.
- Lubrication: Apply oil to motors and bearings where oil ports are available to reduce friction and extend lifespan.
- Thermostat Accuracy Check: Test unit thermostats to confirm temperature readings are precise.
- Insulation Inspection: Evaluate insulation conditions to prevent temperature fluctuations and energy loss.
Electrical and Operational Verifications:
- Wiring Inspection: Conduct a full electrical assessment to check for loose connections, frayed wires, or potential hazards.
- Defrost System Validation: Verify defrost clock settings and ensure proper defrost cycle operation to prevent ice buildup.
- Compressor Examination: Assess unit compressors for performance efficiency and detect early signs of failure.
Final Review and Documentation:
- Compliance and Reporting: Maintain logs of all inspections and maintenance activities to comply with safety regulations and operational standards.
- Recommendations and Notes: Document any additional findings, recommend necessary repairs or upgrades, and establish follow-up actions.
Every organization requires a maintenance schedule tailored to its specific needs. It should be as detailed as possible to ensure that no critical tasks are overlooked by the team.
Best Practices for Maintenance Scheduling
Maximize the benefits of scheduled maintenance by implementing these essential best practices:
1. Conduct Regular Equipment Inspections
Perform regular inspections to identify potential issues early and prevent unexpected breakdowns. Use structured and detailed checklists during every inspection to ensure thoroughness.
Set inspection frequency based on equipment importance to your operations and manufacturer guidelines.
2. Implement Preventive Maintenance
Schedule preventive maintenance proactively to address issues before they become critical. Follow manufacturer maintenance guidelines closely, and maintain detailed records of all maintenance activities and inspection outcomes.
Keep documentation accurate to foster accountability, drive continuous improvement, and inform future maintenance strategies.
3. Monitor Equipment Continuously
Track equipment performance consistently using advanced sensors and monitoring systems. Analyze data regularly to identify performance trends and respond swiftly to changes.
4. Train and Communicate Effectively
Provide comprehensive training to equip maintenance staff with the skills required for routine tasks, troubleshooting, and emergency responses. Maintain open communication channels among the maintenance team, operations staff, and management. Regularly share valuable insights and encourage feedback to foster innovation and strengthen your maintenance strategy.
5. Commit to Continuous Improvement
Regularly review and update your maintenance procedures, schedules, and outcomes. Actively seek feedback from both maintenance staff and equipment operators. Embrace new technologies and innovative techniques to enhance efficiency and improve equipment performance continually.
6. Leverage Maintenance Scheduling Software
Adopt advanced maintenance scheduling software, such as a Computerized Maintenance Management System (CMMS), to simplify and automate scheduling processes.
Integrate your CMMS with other organizational systems, such as inventory, asset management software, or operational monitoring, to achieve a holistic view of your maintenance needs.
Level Up Your Manufacturing with HashMicro Manufacturing Software
Now that we’ve mastered maintenance scheduling, you’re already halfway to a leaner, smoother manufacturing process. But why stop there?
Imagine if you could extend the clarity and control you have over your maintenance schedules into every aspect of your manufacturing operations. In fact, you can do that with HashMicro Manufacturing Software.
Forget juggling spreadsheets, endless phone calls, or frustrating miscommunications. HashMicro brings all your processes together in one intuitive, powerful platform—connecting maintenance schedules to inventory control, real-time production planning, and resource allocation.
It’s designed to help your teams communicate effortlessly, act confidently, and adapt quickly. How does it do that? Simple, as the software has these features:
- Integrated Real-time Stock Management: Provides continuous, real-time tracking of raw materials, work-in-progress, and finished goods through an integrated inventory system.
- Multi-Level Bill of Material (BoM): Defines complex product structures with multiple hierarchical levels of components and sub-components used in manufacturing.
- Comprehensive Production Cost Tracking (Materials, Overhead, Labor, Subcontracting): Tracks actual costs associated with materials, labor, overhead expenses, and subcontracting throughout the production process.
- Master Production Schedule based on Forecasted Demand: Generates production schedules by aligning manufacturing activities with forecasted customer demand data.
- Manufacturing Gantt Chart Schedule Management: Visually represents production timelines, sequences, and dependencies through an interactive Gantt chart scheduling interface.
- Comprehensive Quality Checks (Material, WIP, Finished Goods): Facilitates systematic qualitative and quantitative inspections at different stages of production, including raw materials, work-in-progress, and finished products.
- Comprehensive Overall Equipment Effectiveness (OEE) Reporting: Measures and reports equipment performance by tracking availability, performance, and quality rates across production lines.
Conclusion
A well-structured maintenance schedule keeps your equipment running smoothly, reduces downtime, and improves overall efficiency. By prioritizing planned maintenance, your business can prevent unexpected breakdowns and optimize resources effectively.
To take efficiency even further, you need a system that connects maintenance with every aspect of your operations. HashMicro Manufacturing Software streamlines production, inventory, and resource management into one seamless platform, giving you full visibility and control.
Hindi mo na kailangan mag-manual track ng maintenance schedules at mag-alala sa unexpected downtime; lahat ay automated at naka-integrate sa isang system. With HashMicro, you gain automation, real-time insights, and precision in every process.
So if you are interested, try the free demo now!
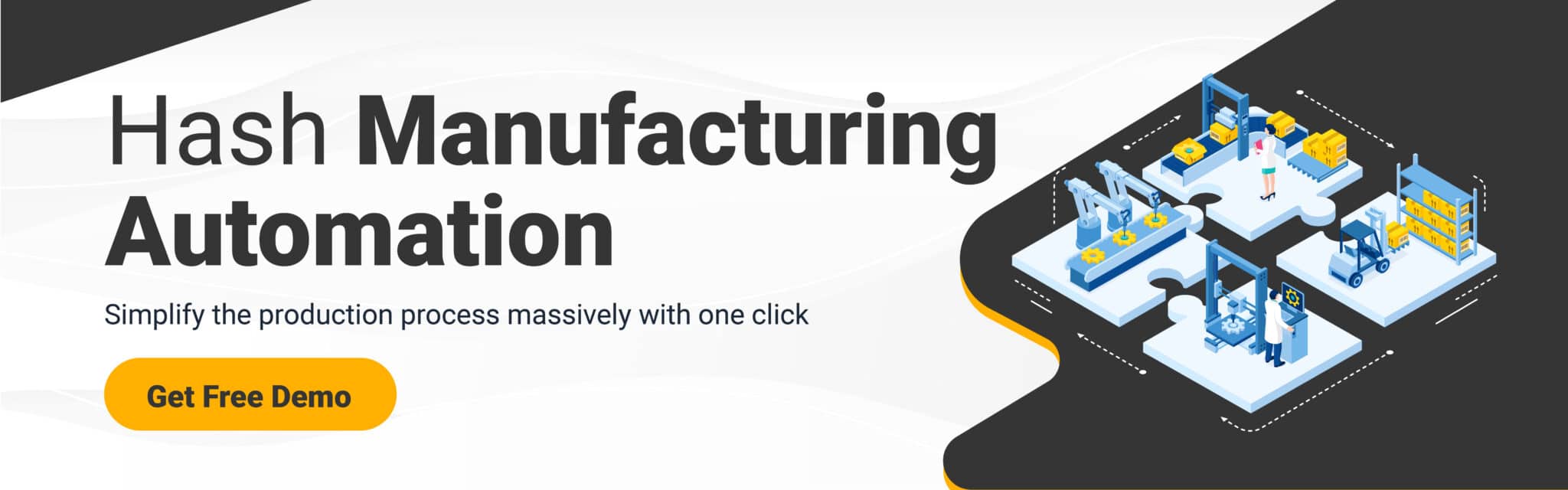
Frequently Asked Questions on Maintenance Scheduling
-
What’s the difference between maintenance planning and scheduling?
Maintenance planning focuses on identifying what tasks need to be done and how to perform them, while maintenance scheduling determines when and by whom these tasks will be executed.
-
How does predictive maintenance fit into maintenance scheduling?
Predictive maintenance uses real-time data to anticipate equipment failures, allowing maintenance to be scheduled proactively before issues arise.
-
Why is it important to consider technician skill sets when scheduling maintenance?
Aligning maintenance tasks with technicians’ specific skills ensures higher quality work and boosts overall team productivity.
-
What role does a Computerized Maintenance Management System (CMMS) play in scheduling?
A CMMS automates the scheduling process by organizing maintenance tasks, tracking equipment history, and managing resources efficiently.