Imagine running a manufacturing operation where every resource is optimized, every schedule is on time, and raw materials are always ready. This is the promise of effective Production Planning and Inventory Control (PPIC) in today’s fast-paced industry.
Yet, without the right tools, PPIC managers face overwhelming challenges such as inaccurate forecasting, production delays, and high operational costs. These issues impact efficiency and profitability and affect customer satisfaction.
According to a study by the Philippine Statistics Authority (PSA), over 40% of manufacturing delays in the country stem from mismanaged inventory and production schedules. Adopting advanced solutions is critical for overcoming these setbacks.
Discover in this article how PPIC works, its benefits to your business, and how ERP software can simplify your processes. Let us guide you toward a more intelligent, more efficient manufacturing operation.
Table of Contents
Key Takeaways
|
What is PPIC (Production Planning and Inventory Control)?
Production Planning and Inventory Control (PPIC) is planning a company’s manufacturing activities and managing the raw materials needed to produce finished goods. It involves creating schedules, monitoring resources, and ensuring sufficient inventory levels meet production demands.
In most manufacturing companies, the PPIC department coordinates production with other key departments like sales, procurement, and finance. This ensures a smooth workflow and minimizes disruptions caused by inventory shortages or production bottlenecks.
The PPIC department plans production and controls inventory to align with customer demand and market trends. It is a vital link between various departments, ensuring that every stage of the production process runs seamlessly—proper PPIC management results in reduced waste, optimized resource utilization, and timely fulfilment of customer orders.
Here are some key responsibilities handled by the PPIC department:
- Planning production schedules: Create detailed schedules to ensure manufacturing processes run smoothly and meet deadlines efficiently.
- Creating and managing manufacturing orders: Organize and handle production orders to align with inventory levels and customer requirements.
- Forecasting inventory requirements: Predict inventory needs by analyzing customer demand, sales forecasts, and market trends.
- Scheduling: Plan production batches based on available raw materials, inventory levels, and estimated production times.
- Monitoring inventory levels: Track raw materials and finished goods in warehouses to ensure uninterrupted production.
- Optimizing machine productivity: Manage machinery usage to avoid overuse or underuse, ensuring efficient and balanced operations.
- Coordinating with other departments: Collaborate with sales, marketing, and procurement teams to address production-related challenges.
- Managing stock movements: Monitor incoming and outgoing goods to maintain optimal stock levels and avoid excess or shortages.
- Providing inventory data: Share accurate inventory information with the finance department to support financial planning and reporting.
- Solving production issues: Resolve production-related problems quickly through effective communication with relevant departments.
Benefits of PPIC (Production Planning and Inventory Control)
Production Planning and Inventory Control (PPIC) is vital to managing manufacturing processes effectively. Implementing an efficient PPIC system ensures streamlined operations, reduces unnecessary expenses, and boosts overall productivity.
The key benefits of adopting PPIC are explained below in detail:
1. Ensure right-sized investments in capital equipment
PPIC helps organizations determine the exact production capacity requirements to meet their business demands. It guides investment decisions by identifying the right amount of machinery, labour, and suppliers needed, ensuring budgets align with production goals.
With accurate planning, businesses can reduce waste and make confident decisions about equipment investments. This approach maximizes ROI while eliminating delays and inaccuracies in production capacity.
2. Reduce your inventory costs
An effective PPIC system minimizes unnecessary inventory handling costs by optimizing stock levels. By collaborating with the sales team, PPIC forecasts customer demand and ensures well-planned safety stocks.
This preparation allows businesses to navigate unexpected supply and demand fluctuations without panic. Moreover, it prevents expensive last-minute raw material orders, saving significant costs in the long run.
3. Reduce your labor costs
PPIC streamlines labor allocation by optimizing manufacturing processes and introducing automation where applicable. This ensures maximum productivity with minimal workforce requirements.
It helps identify the correct practices, raw materials, and technology investments, allowing businesses to accomplish more tasks with fewer employees. Automation further enhances operational speed and labor efficiency.
4. Improve your ROA (Return on Assets)
PPIC enables businesses to optimize asset utilization, from machinery to suppliers, ensuring nothing is overworked. PPIC helps improve overall performance and ROI by adopting best practices tailored to the business.
This systematic approach enhances asset efficiency while maintaining production quality, ensuring a consistent return on investment.
5. Enhance customer service
Effective PPIC ensures precise production schedules and on-time order delivery. This consistency strengthens customer satisfaction and builds a positive brand image. Businesses foster stronger client relationships with fewer complaints and delays, resulting in a loyal customer base.
6. Easy inventory control
A robust PPIC process provides real-time insights into inventory levels, making stock management effortless. It instantly notifies teams about stock availability or shortages, enabling proactive planning.
This efficiency saves time and energy, allowing staff to focus on other essential tasks. As a result, businesses maintain better control over inventory without unnecessary effort. If you want to learn more, try the pricing calculation by clicking the banner below!
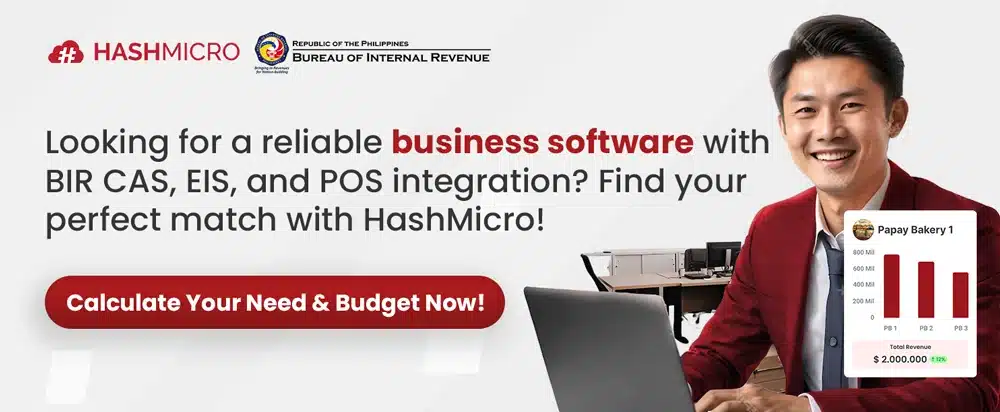
7. Improve plant morale
PPIC improves team coordination by ensuring well-planned schedules, organized inventories, and clear communication. It fosters a stress-free work environment by reducing rush orders and last-minute chaos.
Employees feel more empowered and confident in their roles, leading to higher morale and a more productive workforce.
8. Reduce idle time
Idle time due to a lack of raw materials can disrupt workflows and lower productivity. PPIC minimizes this issue by ensuring a smooth flow of materials and a well-planned production process. Businesses can maintain continuous operations and maximize efficiency across all departments by reducing delays.
Adopting an effective PPIC process is essential for businesses looking to streamline production planning software and inventory management. Whether exploring improving your production schedule or seeking better control over your resources, PPIC offers the foundation for success.
Types of Production Planning
1. Master Production Schedule
The Master Production Schedule is a comprehensive plan that specifies when production will commence for various products, detailing the timing and quantities involved. Its primary objective is to establish a practical timeline that ensures timely delivery while minimizing excess inventory.
2. Materials Requirement Planning
Materials Requirement Planning focuses on guaranteeing the availability of essential raw materials, maintaining minimal stock levels, enhancing inventory oversight, and aiding in procurement strategies.
3. Capacity Planning
Capacity Planning refers to the evaluation of the production capabilities necessary for the organization to meet customer demand and adapt to variations in product requirements. This process aims to balance costs with available resources, as well as align supply with demand.
4. Workflow Planning
Workflow Planning involves organizing the sequence of tasks executed throughout the production process. It allows for monitoring each item’s progress and clarifies who is responsible for specific tasks, thus providing visibility into the current status of production activities.
What are the stages involved in production planning and inventory control?
1. Planning
This phase outlines the production objectives, including what will be made, who will handle the tasks, and the methods to be employed. It involves collecting information from sales and engineering to develop a detailed plan for labor, equipment, and material needs, ensuring an efficient workflow.
2. Routing
Routing determines how raw materials move through the production facility, detailing their conversion into finished products. This step coordinates all production stages, specifying the required materials and resources while optimizing operational efficiency.
3. Scheduling
Scheduling is concerned with timing, focusing on when each operation will be completed to make the best use of available time. Various schedule types, such as Master and Daily Schedules, are utilized to effectively manage timelines.
4. Loading
Loading evaluates the workload assigned to machines and workers by balancing new tasks with those already scheduled. It identifies both underutilization and overloading issues, proposing solutions like adding shifts or overtime to prevent delays.
5. Dispatching
Dispatching involves issuing orders and instructions based on routing and scheduling plans. This step ensures that all necessary materials are prepared for production and maintains comprehensive records throughout the process.
6. Follow-up
Often referred to as monitoring, this step identifies problems in the production process by comparing actual performance with expected outcomes. It addresses issues such as missed deadlines and may require adjustments to targets or schedules to improve overall efficiency.
How ERP Software Optimizes PPIC
Amid rapid technological advancements, manufacturers have become increasingly inefficient in relying on manual processes to manage PPIC. Manual operations often result in human errors, data inaccuracies, and delays, leading to consistency in production.
To overcome these challenges, implementing PPIC software is essential to simplify production planning and enhance manufacturing management. With ERP software, manufacturers can automate and streamline their business operations seamlessly.
An ERP system allows quicker, more accurate process management by integrating them into a centralized platform. This eliminates the need to use separate systems for different tasks, enabling businesses to operate more efficiently and precisely.
Here are some key benefits of using ERP software to optimize your PPIC:
- Automated production scheduling for better planning
- Efficient BoM (Bill of Materials) and routing preparation
- Early warnings for low inventory levels to avoid disruptions
- Automated scheduling of equipment and machine maintenance
- Simplified purchase processes through automation
- Real-time monitoring of raw materials, WIP (Work in Process), and finished goods
- Accurate inventory data for better forecasting of demand and stock requirements
- Comprehensive analysis of reports on inventory, production, and expenses
HashMicro’s ERP manufacturing software offers modules to optimize all aspects of a manufacturing business, including HR, customer, production, inventory, asset, and financial management. This cloud-based solution enhances your PPIC processes and transforms your entire manufacturing operation.
Streamline Your PPIC Management with HashMicro’s Manufacturing Software
HashMicro’s Manufacturing ERP Software is an all-in-one solution designed to optimize overall manufacturing operations for businesses in the Philippines. By automating processes and providing real-time data, this software helps manufacturers streamline production workflows, reduce inefficiencies, and ensure compliance with industry standards.
To help businesses explore its features, HashMicro offers free demo access for its Manufacturing ERP Software. This lets companies experience its capabilities firsthand, including automated scheduling, inventory tracking, and enhanced operational efficiency.
The following are some of the key features provided by HashMicro’s Manufacturing ERP Software to help companies optimize their manufacturing processes:
- Manufacturing Production Scheduling: This feature allows manufacturers to forecast production needs based on demand history, ensuring better planning. With graphical tools, businesses can analyze and control the Master Production Schedule (MPS) for informed decision-making and improved efficiency.
- Manufacturing Requisition Planning: By aligning raw material requisitions with production schedules, this feature prevents inventory shortages and production delays. It ensures materials are requested at the right time, supporting a seamless manufacturing workflow.
- BoM Cost Forecast: This feature helps businesses predict the costs associated with the Bill of Materials (BoM) for production planning. It enables manufacturers to allocate budgets accurately, reducing financial inefficiencies.
- Multi-Level BoM: With multi-level BoM, manufacturers can create detailed breakdowns of components and materials required for production. This improves resource management and ensures precise planning at every stage.
- Stock Requisition Based on Planned Production: This feature automates inventory requests by analyzing planned production needs. It eliminates overstocking and ensures the availability of raw materials for uninterrupted operations.
- Manufacturing Gantt Chart Schedule Management: This tool provides a visual timeline to manage production tasks effectively and track progress. It ensures deadlines are met, improving overall production efficiency and accountability.
- Real-Time Stock Input and Output for Production: With real-time tracking, manufacturers can monitor raw materials used and finished goods produced. This enhances inventory accuracy and reduces manual errors in stock management.
- Finished Goods Production Simulation: This feature allows businesses to simulate production processes, ensuring proper resource allocation and planning. It minimizes risks by identifying potential bottlenecks before actual production begins.
- Manufacturing Quality Control: This tool ensures production quality meets standards, reducing waste and rework. It helps maintain consistency in outputs, enhancing customer satisfaction and brand reliability.
- In-depth reporting on Time Spent, Materials Used, and Finished Goods Produced: Detailed reporting provides insights into production performance, helping manufacturers optimize processes. This feature supports better decision-making and enhances overall operational efficiency.
In addition to these features, the software supports unlimited users, offers flexible customization options, and integrates seamlessly with other modules or third-party applications such as inventory management software from HashMicro Inventory Management System. These qualities make it a powerful solution for businesses looking to enhance efficiency and productivity across their manufacturing operations.
Conclusion
PPIC is crucial for smooth production and inventory management in manufacturing. Without proper planning and control, businesses face delays and inefficiencies. Leveraging the right tools helps streamline workflows, meet customer demand, and improve operational performance effectively.
Modern ERP software, like HashMicro’s Manufacturing ERP, simplifies PPIC with automation and real-time data accuracy. Its features, such as automated scheduling and inventory tracking, help businesses improve efficiency, reduce errors, and optimize operations seamlessly.
Take the first step toward transforming your manufacturing processes by exploring HashMicro’s Manufacturing ERP software. Schedule a free demo today and discover how it can elevate your business efficiency and performance.
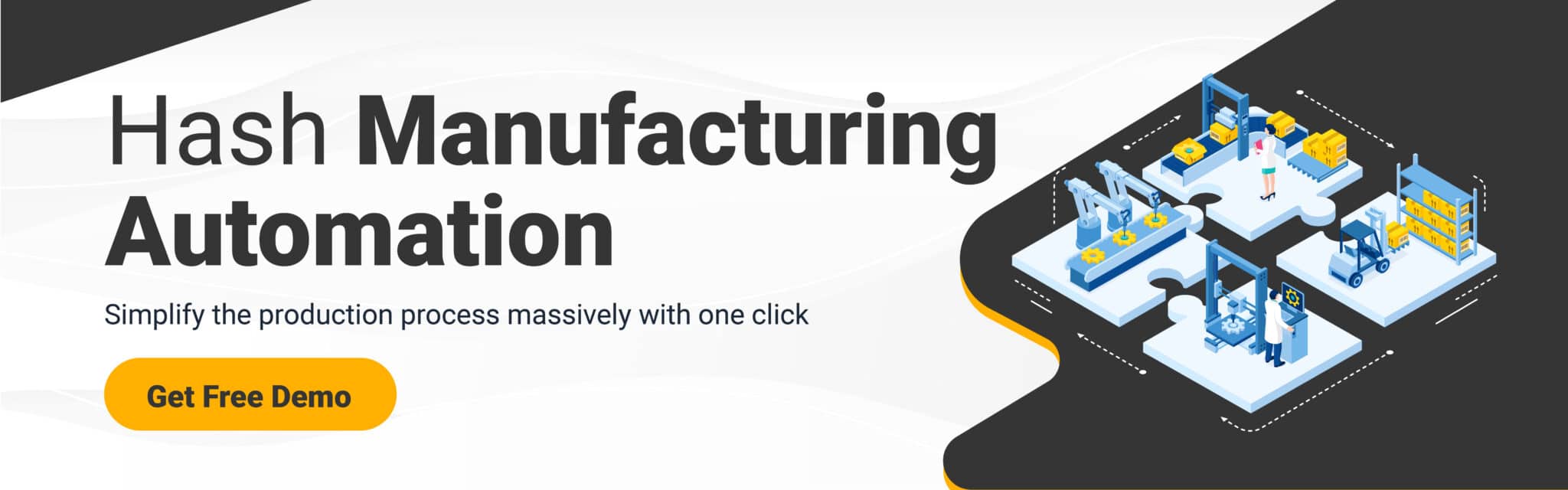
FAQ About PPIC
-
What is PPIC in supply chain?
PPIC, or Production Planning and Inventory Control, is a key function in the supply chain that ensures efficient production processes and optimal inventory management. It aligns production schedules with inventory levels to meet customer demand while minimizing waste and delays.
-
What is the purpose of PPIC?
The purpose of PPIC is to streamline manufacturing processes and manage inventory effectively. It ensures production schedules run on time, raw materials are available, and finished goods meet demand. PPIC aims to enhance efficiency, reduce costs, and improve overall operational performance.
-
What is the purpose of the inventory control system?
The purpose of an inventory control system is to maintain optimal stock levels, prevent overstocking or shortages, and ensure smooth operations. It helps monitor inventory in real time, reduce waste, improve cash flow, and ensure that production processes remain uninterrupted.