In today’s competitive landscape, delivering high-quality products is essential for maintaining customer trust and a strong brand reputation.
Quality control (QC) is the process of ensuring that your products meet established standards throughout production, minimizing defects and improving customer satisfaction. For businesses aiming to stay ahead, QC is more than just a regulatory requirement. It’s a key driver of efficiency, cost savings, and operational excellence.
Utilizing quality control manufacturing software can streamline this process, providing real-time insights and reducing errors across the production line.
Magpatuloy sa pagbabasa upang tuklasin kung paano maaaring paunlarin ng QC ang iyong negosyo at kung bakit mahalaga ang pag-iinvest sa tamang software para sa pangmatagalang tagumpay.
Table of Content
Content Lists
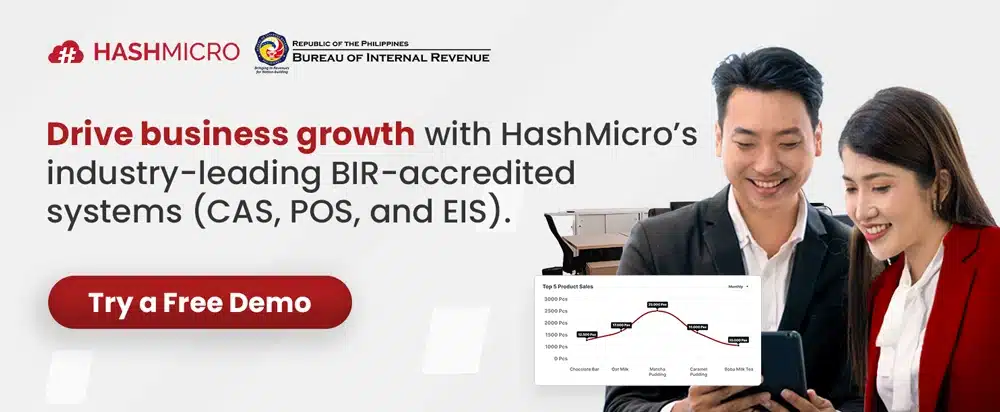
Key Takeaways
|
What is Quality Control (QC)?
Quality Control (QC) is a crucial process used by businesses to ensure that their products and services meet specific standards. It involves the systematic monitoring and evaluation of various stages of production from raw materials to finished goods to identify and correct defects or inconsistencies.
QC helps maintain consistency, reliability, and customer satisfaction by detecting issues early and preventing faulty products from reaching the market.
Quality Control is the backbone of a company’s commitment to delivering high-quality outputs and maintaining a competitive edge in the industry.
Difference between Quality Control and Quality Assurance
While both Quality Control (QC) and Quality Assurance (QA) are essential in maintaining high standards they serve different purposes within a business.
Understanding the distinction between the two can help organizations implement more effective strategies for ensuring product quality. Here’s a breakdown of the key differences between Quality Control and Quality Assurance:
Aspect |
Quality Control (QC) |
Quality Assurance (QA) |
Definition |
QC focuses on identifying defects in finished products. | QA focuses on preventing defects by improving processes. |
Objective |
Ensure the product meets quality standards and specifications. | Ensure that the production process itself is efficient and capable of producing quality products. |
Approach |
Reactive – Identifying and correcting issues after they occur. | Proactive – Implementing processes and guidelines to prevent issues before they happen. |
Scope |
Focuses on the final product or output. | Focuses on the entire production process and system. |
Methods |
Inspection, testing, and sampling of the product. | Audits, reviews, and process evaluations. |
Timing |
Happens after the product is produced. | Occurs during the development or production process. |
Responsibility |
Often performed by dedicated QC inspectors or teams. | Often involves everyone in the organization, particularly process managers. |
What Is Quality Control Management?
Quality Control Management refers to the process of overseeing and ensuring that products or services meet specific quality standards throughout production. It involves a systematic approach to monitoring, inspecting, and testing at various stages to identify and correct any defects or issues.
It aims to maintain consistency, improve reliability, and ensure that the end result meets or exceeds customer expectations.
By implementing effective practices, companies can reduce waste, lower costs, and increase customer satisfaction which ultimately contributes to overall business success.
The Importance of Quality Control for Companies
Quality control is essential for ensuring that a company’s products or services meet consistent standards and customer expectations. By identifying issues early in the production process, businesses can reduce defects, minimize costly errors, and improve efficiency.
Effective quality control also builds customer trust, as it ensures reliable, high-quality products are delivered. In today’s competitive market, quality control not only helps companies maintain a strong reputation but also provides a strategic advantage, leading to greater customer satisfaction and long-term success.
Quality Control Methods and Strategies
There are several methods available for manufacturing quality control:
1. Just in Time (JIT)
Just in Time (JIT) is a strategy focused on reducing inventory waste by receiving goods only when they are needed in the production process. This method aims to improve efficiency and minimize costs by ensuring that materials and components arrive exactly when required, reducing the need for large stockpiles.
2. Workstation quality
Workstation quality refers to the practice of ensuring that each workstation in the production line is set up and maintained to meet specific quality standards. This involves organizing tools, equipment, and materials in a way that supports efficient workflows and minimizes the risk of defects.
Companies can reduce errors, improve consistency, and enhance overall productivity by focusing on workstation quality. Properly trained employees at each station are crucial, as they are responsible for monitoring and ensuring that every product meets quality requirements before it moves to the next stage.
3. Statistical quality control
Statistical Quality Control (SQC) is a method that uses statistical techniques to monitor and control the quality of a product during the manufacturing process. By analyzing data from production samples, SQC helps identify variations that may lead to defects, allowing companies to take corrective actions before problems escalate.
This approach involves tools such as control charts, process capability analysis, and regression analysis to track product quality and ensure consistency.
4. Inspection
Inspection is a key quality control method that involves carefully examining products or materials at various stages of the production process to ensure they meet specified quality standards.
This process can be done visually or with the use of specialized tools and equipment to detect defects, inconsistencies, or deviations from design specifications. Inspections can take place at multiple points, such as during raw material receipt, in-process production, or final product evaluation.
5. Total Quality Management (TQM)
Total Quality Management (TQM) is a comprehensive approach to improving the quality of products and services across all areas of an organization. It involves the continuous involvement of all employees, from top management to front-line workers, in an effort to enhance processes, reduce waste, and improve customer satisfaction.
TQM emphasizes the importance of long-term quality improvement through systematic practices such as process optimization, employee training, and data-driven decision-making.
How Can Quality Control be Enhanced in Manufacturing?
Improving quality control in manufacturing is crucial for maintaining consistent product standards, increasing customer satisfaction, and optimizing operational efficiency. Here are some key ways to enhance quality control in manufacturing:
1. Auditing processes
Auditing processes in manufacturing refers to the systematic evaluation and review of production methods, procedures, and overall operational performance. Regular audits help identify areas where processes may be failing or where improvements can be made.
These audits typically involve assessing compliance with quality standards, reviewing the efficiency of current workflows, and ensuring that equipment and materials are being used optimally.
By conducting audits, manufacturers can uncover inefficiencies, reduce errors, and ensure that all processes align with industry regulations and best practices, ultimately leading to higher-quality products and greater operational consistency.
2. Collecting data
Collecting data is a crucial step in enhancing quality control in manufacturing, as it provides valuable insights into the production process. By gathering data on various factors such as production speed, defect rates, material usage, and equipment performance, manufacturers can identify trends, pinpoint issues, and track performance over time.
This data can be used to monitor quality, make informed decisions, and implement corrective actions when necessary. Utilizing data collection tools like sensors, monitoring systems, and software analytics (all of which is available in manufacturing ERP software) allows manufacturers to take a proactive approach to quality control, ensuring continuous improvement and higher standards throughout the production cycle.
Simplify Quality Control in Manufacturing with HashMicro Software
Managing quality control in manufacturing ERP systems can be a complex process, but with the right tools, it becomes significantly more efficient and effective. HashMicro’s comprehensive resource management software offers a range of features designed to streamline and improve production workflows.
Here’s how HashMicro can simplify your processes:
- Automated quality checks: Manufacturing management software HashMicro automates routine quality inspections, minimizing human error and ensuring consistent standards. This feature enables real-time monitoring and reporting, allowing manufacturers to identify and resolve issues swiftly.
- Data-driven insights: The software’s advanced analytics provide valuable insights from collected data, helping manufacturers track trends, optimize processes, and make informed decisions.
- Integrated workflow management: HashMicro’s solution seamlessly integrates with other production systems, ensuring a cohesive workflow. This integration reduces duplication of effort and enhances coordination across teams, contributing to a more efficient process.
- Customizable reporting: With HashMicro, manufacturers can generate detailed, customizable reports that provide an in-depth overview metrics. These reports help track performance and ensure compliance with industry standards.
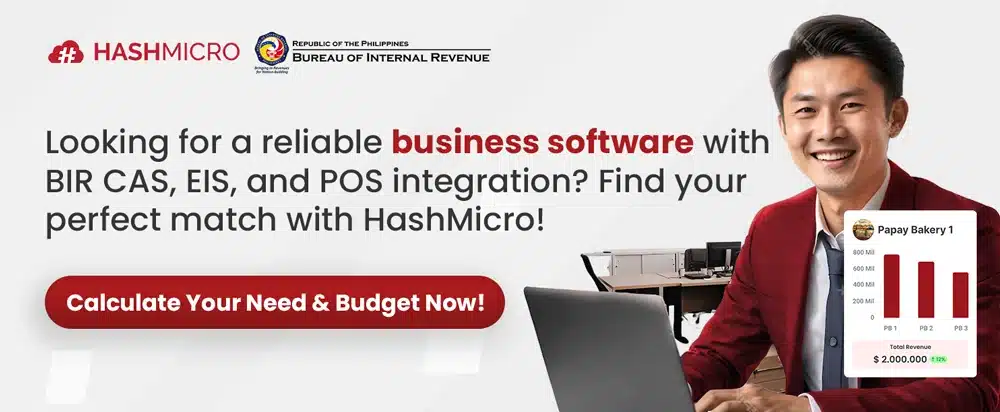
Conclusion
Understanding the significance of quality control is essential for any company aiming to achieve consistent product standards, enhance customer satisfaction, and maintain a competitive edge.
Implementing these methods robustly can streamline operations, reduce costs, and foster trust with clients. However, managing these processes efficiently requires the right tools.
HashMicro’s advanced resource management software provides a comprehensive solution for optimizing quality control procedures. By leveraging this software, companies can automate monitoring, improve accuracy, and ensure continuous improvement across all production stages.
Explore how HashMicro can elevate your quality control strategies by scheduling a free demo today.
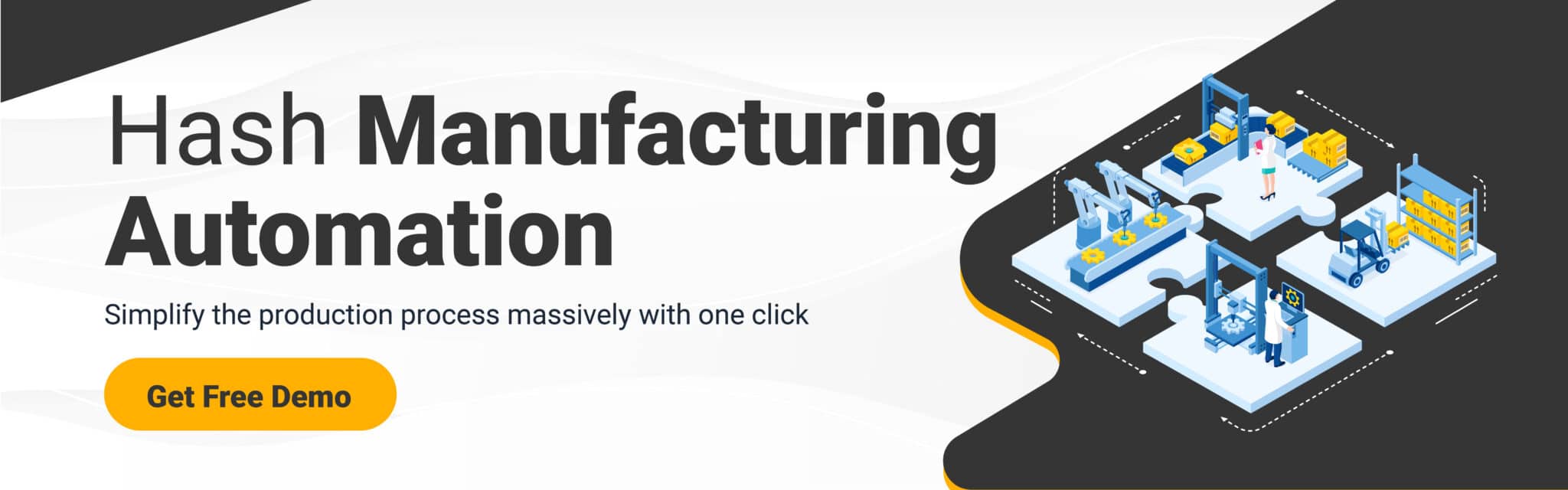
Frequently Asked Questions About Quality Control
-
What methods are commonly used?
Common methods include inspections at different production stages, statistical process control to monitor variations, and functional testing to ensure products perform as expected.
-
What are common tools used?
Common tools include detailed checklists for inspections, control charts for monitoring processes, and sampling techniques to evaluate product batches. These tools help streamline the quality assessment process.
-
Does it impact customer perception?
Yes, maintaining consistent quality directly influences customer satisfaction and loyalty