As your business grows, optimizing your warehouse layout can become increasingly challenging.
Narrow aisles, disorganized storage, and inefficient workflows can lead to wasted time, higher labor costs, and delivery delays, all of which directly affect your bottom line. This is why a well-planned warehouse layout is crucial.
By optimizing your space, reducing unnecessary handling, and improving the flow of operations, you can maximize productivity and reduce costs. Focusing on key areas such as storage, picking, and dispatch ensures that your warehouse runs smoothly, helping you meet customer demands faster and more efficiently.
In this article, we’ll explore the critical elements of designing an effective warehouse layout and how it can boost your business’s efficiency and profitability.
Key Takeaways
|
Table of Contents
What is A Warehouse Layout?
A warehouse layout shows how space is arranged in a facility, affecting how materials, workers, and equipment move around. When designing the layout, it’s important to think about areas for storage, picking, shipping, and offices, as well as the size and shape of items and any obstacles that may be in the way.
A well-designed layout improves how goods are stored, moved, and retrieved, which boosts overall efficiency. The way the facility is arranged plays a key role in maximizing space and ensuring smooth production and distribution. Ang tamang pagkakaayos ng kagamitan ay mahalaga para sa madaling pag-access at mas mahusay na produktibidad.
A good layout not only makes workflows smoother but also reduces the time and effort needed to retrieve and organize inventory. A smart warehouse layout allows materials and products to move freely, which helps minimize bottlenecks and delays.
This efficiency speeds up operations, increases productivity, and ensures that deliveries reach customers on time. Grouping similar items together also optimizes storage and cuts down on unnecessary movement. In short, a well-planned warehouse layout is essential for an organized and efficient facility.
Furthermore, using advanced warehouse management systems (WMS) can further improve warehouse layouts. WMS automates inventory management, optimizes picking routes, and provides real-time visibility. This leads to greater efficiency, accuracy, and cost savings.
How Important is Warehouse Layout?
The layout of a warehouse is essential for optimizing efficiency and productivity in daily operations. A thoughtfully designed space offers a variety of benefits that can enhance both everyday functions and long-term success. Here’s why having a smart warehouse layout matters:
-
Enhances Efficiency and Productivity
A well-planned warehouse layout significantly impacts how effectively a facility operates. When the design is streamlined, employees can store, retrieve, and move goods quickly and efficiently. This helps reduce wasted time and effort, allowing team members to concentrate on more important tasks.
For example, an organized layout decreases the time spent searching for misplaced items or fixing errors. As a result, order fulfillment becomes faster, lead times shorten, and overall productivity and customer satisfaction increase.
-
Promotes Safety
Safety is a top priority in any warehouse. A smart layout uses ergonomic principles and establishes clear pathways for both pedestrians and vehicles. By placing frequently used items within easy reach and designating specific areas for hazardous materials, businesses can minimize the risk of accidents and injuries.
Additionally, in sensitive industries like food storage, preventing cross-contamination is vital. Proper space allocation helps avoid pest-related issues and maintains product quality, ensuring safety for both employees and customers.
-
Reduces Costs
An efficient warehouse layout can lead to significant cost savings. By minimizing the distances employees travel for picking, packing, and shipping, companies can enhance labor efficiency and increase throughput.
Furthermore, a well-optimized layout maximizes space utilization, allowing for effective inventory storage without unnecessary expansion. This reduction in holding costs, along with improved labor efficiency, ultimately boosts the overall profitability of the business.
What Are the Components Of A Warehouse?
An efficient warehouse relies on several key components, each designed to streamline operations and boost productivity. When these areas are strategically placed and thoughtfully organized, they significantly enhance the overall functionality of the facility. Here’s a closer look at the essential components of a warehouse:
-
Receiving Area
The receiving area is the first stop for incoming shipments. Here, goods are unloaded, checked for accuracy, and sorted. This space is crucial for ensuring that everything arrives in good condition and is properly accounted for.
Ideally, it should be located near a dedicated receiving bay, allowing easy access for trucks and transport vehicles. By positioning the receiving area close to the storage section, businesses can facilitate quick movement of products into inventory, setting a smooth workflow in motion.
-
Storage Area
The storage area serves as the heart of the warehouse, housing inventory until it is needed for orders. A well-organized storage section is essential for maximizing space and ensuring easy access to products.
Typically featuring pallet racks and shelving units, this area should accommodate various types of goods. Effective storage management minimizes the time employees spend searching for items and improves the accuracy of order picking, which ultimately leads to better inventory control.
-
Packing Area
Once items are picked, they move to the packing area, where orders are prepared for shipping. This space should be designed for efficiency, enabling quick and accurate packaging.
By being strategically connected to both the storage and shipping areas, the packing section allows for seamless movement of goods. The layout should prioritize worker comfort and safety while ensuring that packaging processes are executed swiftly to meet shipping deadlines.
-
Shipping Area
The shipping area is responsible for preparing outgoing orders for distribution, acting as the counterpart to the receiving area. It should be conveniently located for easy access to both the packing area and a dedicated shipping bay.
Sufficient space must be allocated for wrapping pallets and using equipment like pallet jacks and forklifts. Additionally, incorporating a staging area within the shipping zone helps organize completed orders before they are loaded onto trucks, ensuring timely deliveries.
-
Service Areas
Service areas, such as restrooms, employee break rooms, and management offices, play a vital role in supporting daily warehouse operations.
Restrooms should be easily accessible, and office spaces should be strategically placed near the receiving or shipping zones to facilitate communication between management, suppliers, and logistics partners. These areas contribute to a comfortable and productive working environment.
-
Additional Specialized Areas
Depending on specific business needs, warehouses may also feature additional spaces like staging zones, quality control sections, or areas for specialized handling.
For instance, a high-volume warehouse might include a staging area to unbox shipments, conduct quality checks, or prepare materials for storage. These specialized zones accommodate unique operational requirements, further enhancing overall warehouse efficiency.
By thoughtfully planning and organizing these components, businesses can create a well-structured warehouse that promotes efficiency, safety, and productivity. Each component plays a vital role in facilitating the smooth flow of goods, ultimately contributing to the success of warehouse operations for all companies.
What Warehouse Layout That Needs to Be Considered?
Creating an effective warehouse layout is crucial for enhancing efficiency and productivity, no matter the size or type of your business. Let’s explore some friendly tips that can help you design a layout tailored to your needs:
-
Understanding the Operations of Your Warehouse Layout
First and foremost, think about how your business operates. If you’re in manufacturing, placing storage areas close to the production floor will give you quick access to raw materials. Meanwhile, distribution centers thrive when storage is near packing stations, speeding up order fulfillment. By recognizing your operational flow, you can create a layout that works like a charm!
-
Considering Your Products
Next, consider the types of products you store. If you handle perishables, you’ll want designated spaces for cold storage alongside dry goods. If your focus is on non-perishable items, a straightforward layout might do the trick. Understanding your products’ needs helps you select the right storage solutions that keep everything organized and easily accessible.
-
Maximizing Available Space
When working with existing facilities, make every square foot count! Take a good look at the size and shape of your building and think about how to best utilize the available space. This will guide your choice of storage systems—whether it’s shelving, racking, or even automated solutions—ensuring everything fits perfectly.
-
Choosing the Right Equipment
Don’t forget about the equipment! Selecting the right racking and shelving systems is key to maximizing storage capacity. Think about your material handling needs, like forklifts and conveyor systems, based on the types of goods you manage. By integrating the right tools into your layout, you can improve workflow efficiency and make life easier for your team.
-
Enhancing Workflow
A well-planned layout should support a smooth workflow, reducing unnecessary movement and potential bottlenecks. Aim for a design that allows for seamless transitions between receiving, storing, picking, and shipping. Depending on your operation and products, consider different picking methods, like zone picking or wave picking, to further boost productivity.
-
Ensure Your Warehouse Design Meets Standards
Safety should always come first! Make sure your warehouse design adheres to safety regulations. This includes clear exit routes, proper signage, and designated areas for hazardous materials. Adding safety features like good lighting and spacious aisles will create a comfortable and secure environment for everyone.
-
Balancing Costs
Lastly, keep an eye on costs while designing your layout. It’s essential to explore different options to find the sweet spot between achieving your operational goals and sticking to your budget. A thoughtfully designed warehouse can significantly cut operational costs by streamlining processes and enhancing overall efficiency.
What are the Different Types of Warehouse Layouts?
Choosing the right warehouse layout is essential for boosting efficiency and ensuring smooth operations. Each design caters to specific business needs, making it easier to handle your products. Let’s dive into some popular layouts that can help you optimize your warehouse space:
-
U-Shaped Warehouse Layout
The U-shaped layout brings the receiving and shipping areas close together, creating a friendly flow of goods. This design minimizes the distance your team needs to travel, making it easier to access different sections of the warehouse. It’s perfect for businesses aiming to keep inbound and outbound traffic organized, which helps reduce congestion and keeps everything running smoothly.
-
L-Shaped Warehouse Layout
In an L-shaped layout, you’ll find separate areas for receiving and dispatching goods. This setup promotes organized movement and provides a clear path for materials, allowing for efficient transitions from receiving to storage and then to shipping. If your business needs to quickly transfer items between trucks, this layout is an excellent choice, facilitating fast cross-docking while keeping things orderly.
-
I-Shaped Warehouse Layout
The I-shaped layout offers a straightforward design, with receiving and shipping areas located at opposite ends of the warehouse. This configuration provides a direct route for goods to flow, making it ideal for high-volume operations. By reducing travel time, it helps your team work more efficiently, ensuring that products move quickly through the warehouse.
Each of these layouts has its own strengths, so take the time to consider your available space, product flow, and operational needs when making your selection. By choosing the right warehouse layout, you can optimize your storage and streamline shipping processes, leading to greater productivity and a smoother overall operation. Let’s get your warehouse working smarter!
What are The Tips on Critical Aspects of Logistics and Warehouse Functions?
Optimizing logistics and warehouse operations is essential for any business aiming to boost efficiency and create a smooth supply chain experience. Here are some friendly yet professional tips to help you enhance these important functions:
-
Accurate Inventory Management
Keeping an eye on your inventory in real-time is a game changer! It helps you avoid stockouts and excess inventory. By utilizing inventory management software, you can easily track your products, set reorder points, and automate restocking. This ensures you meet customer needs while keeping costs in check.
-
Evaluate Throughput
Regularly taking a closer look at your warehouse’s throughput can reveal valuable insights. By analyzing how materials flow, you can spot any bottlenecks or inefficiencies. This understanding empowers you to implement effective strategies that streamline the movement of goods, making your operations smoother and more efficient.
-
Choose the Right Warehouse Layout Design
A well-organized warehouse layout can work wonders! Whether you prefer a U-shaped, L-shaped, or I-shaped design, pick a layout that fits your needs. Be sure to place frequently accessed items within easy reach to save time and enhance productivity.
-
Invest in Effective Storage Layout Solutions
Selecting the right storage systems can make all the difference. Whether you choose selective pallet racking or automated solutions, the right choice will help you make the most of your space while ensuring efficient material handling.
-
Leverage Technology and Automation For Warehouse Layout
Embracing technology is key to modern operations. Incorporate tools like barcode scanning and warehouse management systems (WMS) to streamline your processes. Automation speeds up picking, packing, and shipping, reducing errors and boosting overall efficiency.
-
Focus on Employee Training
Your team is your greatest asset, so invest in their growth! Regular training on new technologies and best practices not only empowers employees but also fosters a positive work environment. When your team is well-equipped, productivity naturally flourishes.
-
Prioritize Safety and Compliance
Safety should always be at the forefront. Conduct regular safety audits and ensure your team has the necessary training and equipment. A safe workspace not only protects your employees but also enhances overall efficiency by reducing accidents and downtime.
-
Monitor Key Performance Metrics
Keeping track of key performance indicators like order accuracy and inventory turnover is essential. By analyzing these metrics, you can pinpoint areas for improvement and make informed changes that boost efficiency.
-
Foster Strong Supplier Relationships
Building solid relationships with your suppliers leads to better communication and reliability. Collaborating with them can result in improved pricing, faster response times, and valuable market insights that benefit your operations.
-
Adapt to Market Changes
Flexibility is key in today’s fast-paced market. Regularly assess your operations and be open to new technologies or practices that can help you stay competitive and responsive to customer demands.
-
Consider Demand Forecasting
Understanding future demand patterns is crucial for effective warehouse optimization. By analyzing historical data and market trends, you can anticipate customer needs and adjust your resources, accordingly, ensuring you’re always prepared.
-
Engage with Experts to Understand More on Warehouse Layout
Don’t hesitate to collaborate with industry experts! Their insights can provide valuable recommendations for optimizing your logistics and warehouse functions. Their experience can help you make informed decisions and implement best practices that keep you ahead of the competition.
How Cloud-First and AI-Powered Warehouse Management Systems Help Optimize Warehouse Layout?
Cloud-first and AI-powered warehouse management systems (WMS) are changing the game for optimizing warehouse layouts and boosting efficiency.
By using advanced data analysis, these systems provide insights that help you make smarter decisions for your operations. One major benefit of WMS is improved stock rotation.
With real-time data, these systems can identify slow-moving inventory and suggest ways to maximize your storage space as well as reducing waste. Additionally, cloud-first and AI-driven WMS streamline material movement by optimizing pick routes and minimizing unnecessary movements.
This leads to lower operational costs and higher productivity. Using these systems also help you manage your warehouse costs efficiently. By analyzing data, you can spot inefficiencies and implement changes to save on labor and energy.
Conclusion
An efficient warehouse layout is essential for boosting productivity, cutting costs, and ensuring your deliveries are on time.
When you organize your storage, picking, and dispatch areas effectively, you create a smoother workflow and a safer environment that helps your business scale. By using HashMicro’s Warehouse Management System Philippines makes this process easier and more enjoyable!
With features like RFID technology, you can track your stock in real time, so you always know where everything is. The system also includes a 3D digital model of your warehouse, allowing you to visualize your layout and plan effectively.
Plus, with Optical Character Recognition (OCR), turning paper documents into digital records is a breeze, keeping your inventory data accurate and up to date. HashMicro’s stock forecasting tools analyze demand patterns, helping you avoid overstocking or running out of items, which saves costs and keeps your customers happy.
So why not take the first step toward smoother operations today? Start your free demo and discover how HashMicro can enhance your efficiency, accuracy, and profitability. We’re excited to partner with you on this journey!
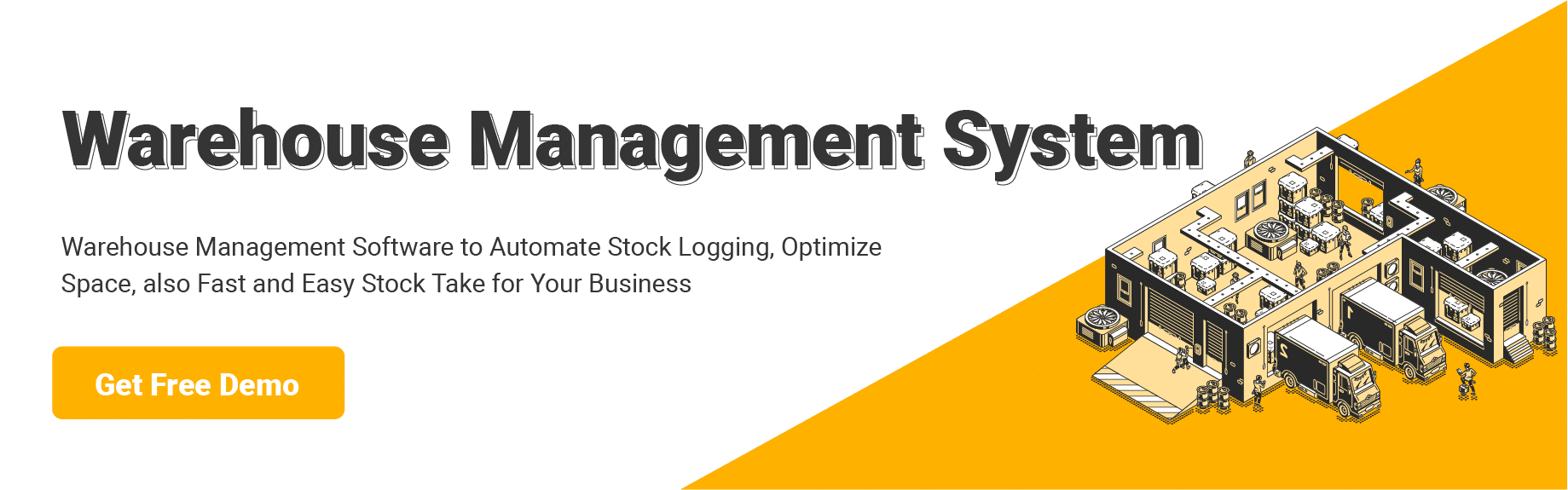