In the manufacturing sector, managing Work-in-Progress (WIP) inventory is essential to streamline production and prevent bottlenecks. This inventory type is a crucial bridge between raw materials and finished products, making it vital for a company’s operational flow.
However, many manufacturing companies need help managing WIP effectively, such as inaccurate tracking, excess inventory, and delays in production cycles. These issues can lead to higher costs and missed business opportunities.
In the Philippines, a study by the Philippine Institute for Development Studies highlighted that many local manufacturers struggle with WIP inefficiencies, leading to increased operational costs. For more detailed insights, visit this study.
Fortunately, solutions like ERP software can help streamline and automate WIP management, ensuring accurate inventory tracking. Continue reading this article to discover how these tools can transform your manufacturing process.
Table of Contents
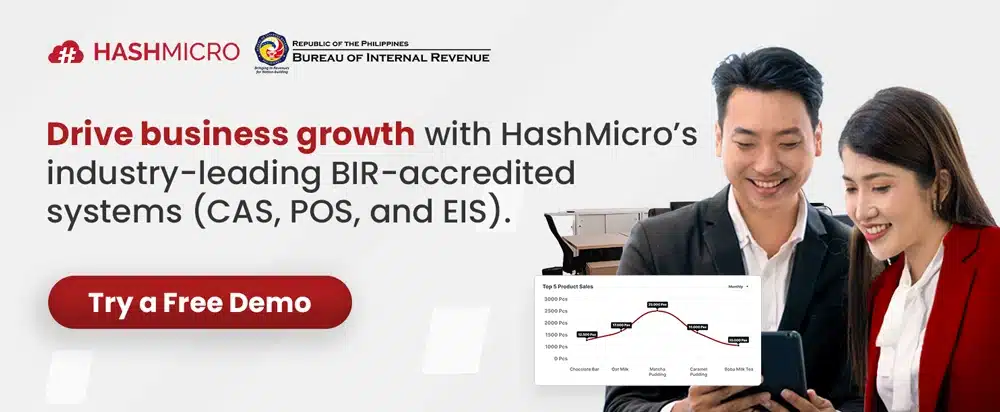
Key Takeaways
|
What is a Work in Progress?
Work in Progress (WIP) is a term used to describe goods that are being manufactured but are not yet completed. These partially finished products are at various stages of production and require further processing before they can be classified as finished goods ready for sale.
In accounting, WIP is recorded as part of a company’s manufacturing inventory and tracked to reflect the value of goods still in production. Once the product is completed and ready for distribution, this value is transferred to finished goods and ultimately to the cost of sales.
WIP is crucial for understanding production flow. It helps companies monitor the efficiency of their operations and manage the movement of goods through the manufacturing process. By tracking these intermediate goods, businesses can optimize production schedules and improve supply chain management.
Why is it Important to Track Your WIP?
Tracking your Work in Progress (WIP) is crucial as it provides detailed insights into the manufacturing process, allowing businesses to identify inefficiencies more effectively. By closely monitoring the movement of goods at various production stages, managers can quickly detect and address bottlenecks or delays that could otherwise impact overall productivity.
In addition, overhead allocations, often based on labor hours or machine usage, are essential for accurately measuring WIP. Since WIP is classified as an asset on the balance sheet, companies frequently strive to minimize its levels before reporting to simplify valuation and reduce operational complexity.
Furthermore, organizations that actively track WIP can significantly optimize inventory management by reducing unnecessary production and storage costs. This strategic approach not only frees up valuable space on the production floor but also helps mitigate waste and lowers the risk of damaged or defective goods, ensuring smoother operations.
Lastly, minimizing WIP levels before reporting also helps businesses avoid the risks of obsolescence and simplifies the estimation of completion percentages. With these improvements in place, companies can enhance efficiency, maintain cost-effectiveness, and ultimately drive long-term profitability.
Work in Progress vs. Work in Process: What’s the Difference?
“Work in Progress” (WIP) and “Work in Process” are often used interchangeably in manufacturing, but they have distinct meanings that are important for accurate accounting. WIP refers to items that are closer to completion and can be sold quickly, while “Work in Process” refers to goods that are still undergoing significant production stages and require more time to be finished.
While different, these terms are tracked in the company’s accounting system under inventory management. WIP and work-in-process inventory include raw materials, labor costs, and overhead, which must be carefully accounted for to ensure proper financial reporting and cost control.
Understanding the difference between WIP and work in process can help managers optimize production efficiency and reduce unnecessary costs. By accurately tracking these stages in the production cycle, companies can better manage their inventory, streamline workflows, and avoid potential bottlenecks that slow down overall productivity.
Function of Work in Progress (WIP) Inventory
In manufacturing, companies typically categorize their inventory into raw materials, work in progress (WIP), and finished goods. Separating inventory into these categories also simplifies accounting, as each type of inventory—raw materials, WIP, and finished goods—has its specific value that must be tracked.
This distinction allows companies to maintain accurate financial records, ensuring that work-in-progress accounting is properly handled for effective production planning.
Today, companies can track and calculate the value of their inventory, including WIP, in real time through Manufacturing Software. This technology enables businesses to generate detailed production analysis reports with just a few clicks, helping optimize the production process and improve overall efficiency.
How do Accountants Record Work In Progress?
Accountants use various methods to handle work-in-progress (WIP) inventory, ensuring accurate financial reporting and efficient production management. Inventory is generally divided into three main categories: raw materials, work in progress (WIP), and finished goods inventory.
WIP is reported separately on the company’s balance sheet, though it often appears as a relatively small line item compared to the overall inventory. Since WIP valuation is often challenging, accountants aim to keep these levels relatively low as the reporting period approaches, frequently finalizing unfinished goods by moving them into the finished product category before closing the books.
To streamline this process, standard completion levels are typically assigned to items in progress, assuming results will average out across multiple units. However, this approach may not always reflect reality due to issues like defects, rework, or leftover materials that can skew estimates.
Accountants, therefore, rely on methods that incorporate overhead, labor, and raw material costs to arrive at a practical estimation of WIP. They recognize that while not flawless, these methods are effective for managing inventory in process.
By leveraging advanced Manufacturing Software, accountants can enhance accuracy and efficiency in this process. Click the banner below to discover how this software can simplify and improve WIP accounting for your business.
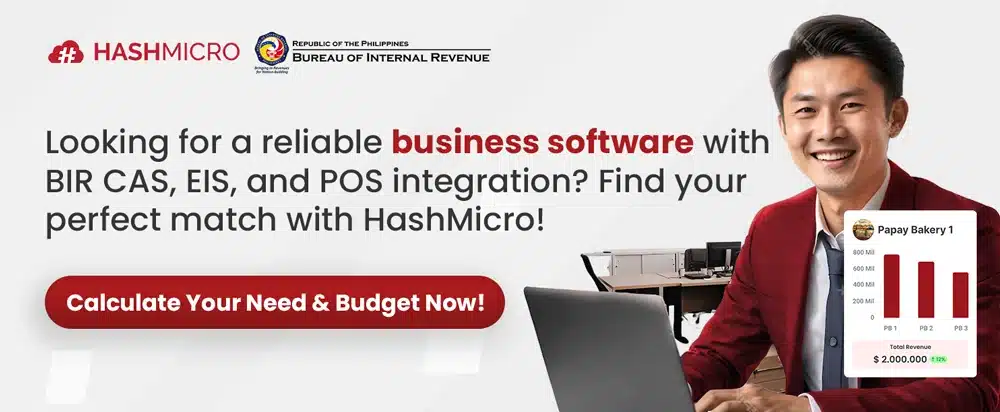
Tips for Efficiently Managing the Production Process of a Manufacturing Company
Efficiently managing the production process in a manufacturing company involves a comprehensive approach, from planning to actual production. Initially, manufacturing processes relied on manual labor, which was time-consuming and prone to errors, slowing down the business.
Relying on manual operations is no longer sustainable as competition increases. Companies can automate and streamline operations by adopting modern technologies such as Manufacturing Software, significantly enhancing productivity and reducing inefficiencies.
One of the key features of Manufacturing Software is Bill of Material (BOM) Management, which allows companies to categorize inventory like raw materials and work in progress (WIP). This feature ensures accurate, real-time calculations for finished goods, making inventory management more precise and effective.
Managing WIP efficiently is crucial, as excessive WIP can lead to increased expenses and potential losses. With the right software, companies can avoid inventory pile-ups and reduce production costs, ensuring smoother operations and faster revenue realization.
Best Practices in Managing WIP Inventory
Effectively managing Work in Progress (WIP) inventory is essential for maintaining efficient production cycles and reducing waste. By closely monitoring and controlling WIP, businesses can minimize unnecessary costs and optimize manufacturing operations.
This requires careful planning, collaboration, and the correct practices to ensure that resources are used productively. Here are several best practices to effectively manage your WIP inventory:
-
Identify bottlenecks in your processes
Recognizing bottlenecks in your production line is crucial for maintaining smooth operations. By identifying the root cause of delays, you can target solutions that reduce production time, allow for faster turnover of work in progress, and increase efficiency.
-
Explore various methods of managing inventory
Finding the right inventory management system is vital. Consider using techniques like Just-in-Time (JIT), which minimizes waste and ensures that products are made only when needed, reducing the amount of WIP inventory at any given time.
-
Optimize manufacturing processes
Streamlining production processes by setting clear guidelines for where and how items should be placed during production can significantly reduce transition times between tasks. This allows for a smoother flow and ensures that products move efficiently through each stage of the production process.
-
Digitize the way you work
Adopting a digital platform like HashMicro can automate tasks, track issues, and streamline reporting and training. With digital tools, your team can access real-time data, helping to manage WIP inventory more effectively and maintain a smooth production flow.
-
Provide adequate employee training
Ensuring that your team is well-trained is key to achieving high productivity levels. Offering training through in-person sessions or digital tools helps employees stay updated on best practices, improving their speed and the quality of their work.
-
Upgrade equipment and machinery
Outdated equipment can lead to production delays and inefficiencies. Investing in modern machinery can help your team work faster and more effectively, directly impacting WIP levels and overall production output.
By integrating these best practices into your operations, you can keep WIP inventory levels under control, reduce costs, and increase overall efficiency in your manufacturing process. Additionally, maintaining a well-organized inventory list ensures accurate material tracking, enabling better oversight of WIP inventory and minimizing errors in production management.
Optimize Work in Progress Management with HashMicro’s Advanced Manufacturing Software
HashMicro’s Manufacturing Software is a leading provider of solutions designed to optimize Work-in-progress (WIP) management and enhance manufacturing efficiency. With its innovative technology and trusted reputation, it empowers businesses to automate WIP tracking, streamline production planning, and ensure seamless inventory management.
If you want to learn more about how HashMicro’s Manufacturing Software can revolutionize your WIP management, you can try the free demo provided by this vendor. Discover how this solution simplifies inventory tracking, reduces production delays, and supports your company in achieving operational excellence.
Why we recommend it: HashMicro’s Manufacturing Software offers advanced tools for WIP management, such as real-time inventory tracking, automated production scheduling, and in-depth reporting. These features enable businesses to tackle production challenges effectively, ensuring smoother workflows and optimized resource utilization.
HashMicro’s Manufacturing Software provides exceptional features tailored to meet WIP management needs, making it ideal for companies looking to enhance production efficiency and inventory control.
Here are some key features offered:
- Real-Time Stock Input and Output for Production: Track raw material usage and finished goods production in real-time to maintain accurate inventory records. This feature reduces manual errors and improves visibility into WIP processes.
- Finished Goods Production Simulation: Simulate production processes to identify potential bottlenecks and optimize WIP management. This proactive approach helps businesses refine production plans and minimize risks.
- Manufacturing Production Scheduling: Forecast production needs based on demand history to ensure resources are allocated efficiently. Use graphical tools to analyze and control schedules, empowering better decision-making in production processes.
- Manufacturing Requisition Planning: Align raw material requisitions with production schedules to prevent inventory shortages and delays. This ensures a smooth workflow, keeps production on track, and avoids costly disruptions.
- BoM Cost Forecast: Predict production costs by analyzing the Bill of Materials, enabling accurate financial planning. This feature helps businesses allocate budgets effectively while minimizing waste and inefficiencies.
- Multi-Level BoM: Manage a detailed breakdown of materials and components to improve production planning. This ensures precise resource allocation, reduces delays, and enhances workflow efficiency.
- Stock Requisition Based on Planned Production: Automate material requests by analyzing planned production needs, ensuring raw materials are always available. This feature eliminates overstocking and avoids costly last-minute purchases.
- Manufacturing Gantt Chart Schedule Management: Visualize production timelines and progress with an intuitive Gantt chart. This tool ensures tasks are completed on schedule, improving accountability and overall efficiency.
- Manufacturing Quality Control: Monitor quality at every production stage to ensure consistent standards and minimize rework. This feature enhances product reliability while reducing waste and operational delays.
- In-depth reporting on Time Spent, Materials Used, and Finished Goods Produced: Generate detailed reports to analyze WIP performance and identify areas for improvement. These insights enable better decision-making, fostering continuous growth and operational excellence.
In addition, HashMicro’s Manufacturing Software integrates seamlessly with other modules, such as procurement and finance systems, ensuring smooth and efficient manufacturing operations. Its customizable and user-friendly interface adapts to your business requirements, empowering you to focus on growth while keeping WIP inventory under control.
Conclusion
Work in Progress (WIP) refers to inventory items in the production process, and managing them efficiently is crucial for manufacturing companies. Using integrated manufacturing software, managers can streamline inventory calculations and reduce time-consuming manual processes, leading to greater operational efficiency.
HashMicro’s Manufacturing Software offers a comprehensive solution for seamlessly managing WIP inventory and other operations. With features like real-time stock tracking, production planning, and quality control, this software helps companies reduce waste, optimize workflows, and improve overall productivity.
To experience the benefits of automating your manufacturing processes, try HashMicro’s software with a free demo today. Click the banner below to schedule your demo and explore how our solution can help you enhance your business operations.
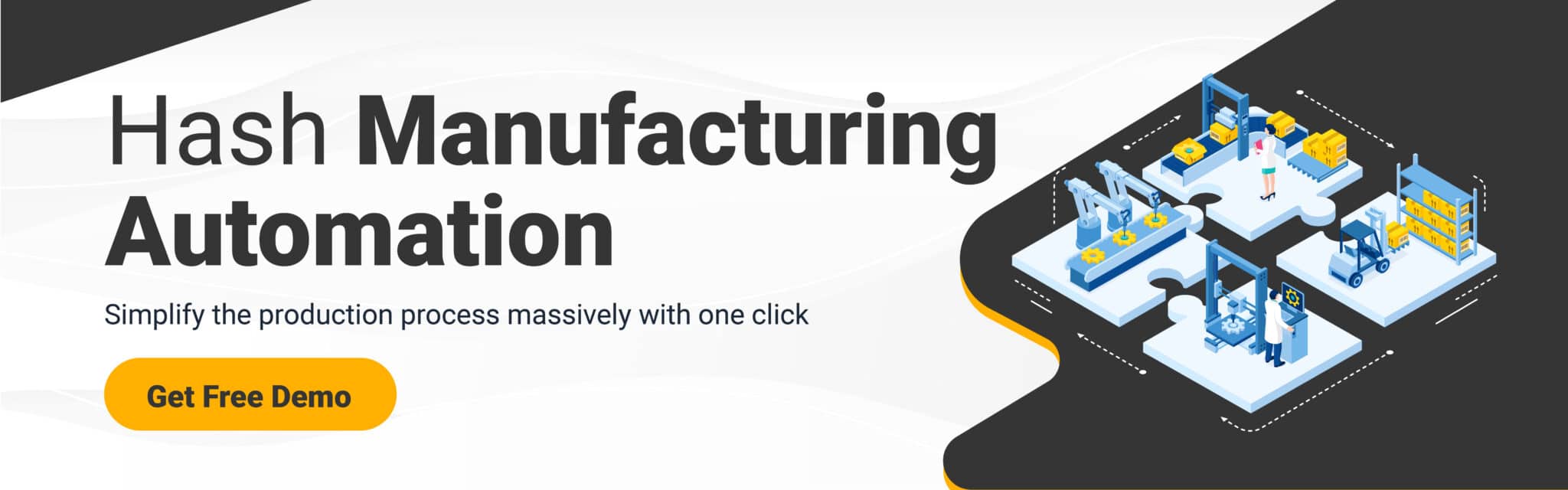