Efficient work order management is the backbone of successful manufacturing operations, ensuring tasks are executed promptly and in accordance with established protocols. Without a robust system, companies risk operational disruptions and inefficiencies.
Managers often face hurdles such as miscommunication between departments, leading to misaligned priorities, and the manual handling of work orders, which is prone to errors and time-consuming. These challenges can result in delayed repairs and dissatisfied customers.
Research focusing on the University of Baguio’s Requisition, Procurement, and Inventory System demonstrated that implementing automated solutions streamlines operations, improving overall service delivery.
Explore this article further to uncover strategies and software solutions designed to enhance your work order processes and elevate your manufacturing efficiency.
Table of Contents
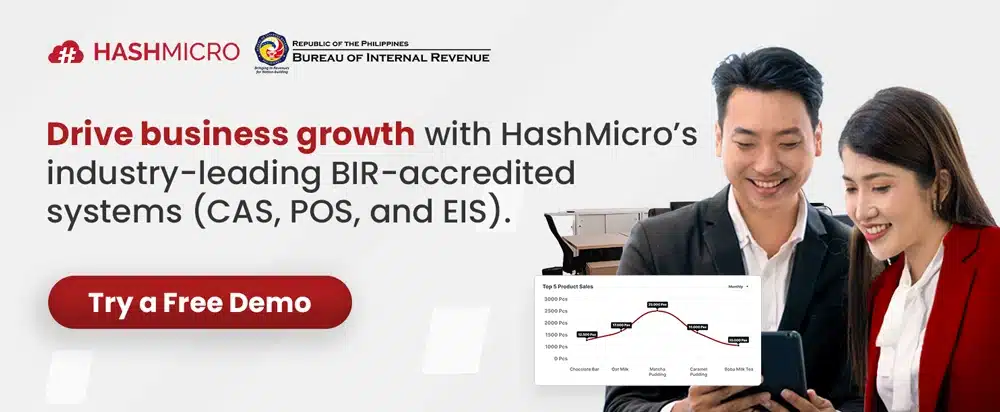
Key Takeaways
|
What Is a Work Order?
A work order is a formal document that outlines specific tasks to be completed, whether for internal operations or external service providers. It typically includes task descriptions, assigned personnel, required materials, estimated costs, and deadlines.
This document is essential for tracking inspections, equipment repairs, and material requests in maintenance and manufacturing. It can also include preventive tasks to address potential issues or urgent requests for immediate repairs before they escalate.
Companies may issue service requests for third-party contractors when internal teams lack the expertise or resources. A clear task description should define the scope, priority level, and expected completion timeline.
By using workflow automation software, businesses can streamline task assignments, track progress in real-time, and improve overall efficiency, ultimately boosting productivity and reducing costs.
Why Is It Important to Use Work Orders?
A work order system is essential for maintaining efficiency and ensuring tasks are completed on time. It provides a structured workflow by detailing what needs to be done, when it should be completed, and who is responsible. This level of organization reduces delays, minimizes errors, and ensures businesses operate smoothly while optimizing resource allocation.
A well-structured job request process helps companies customize and adapt workflows to meet evolving business needs. A transparent system improves productivity, whether it’s a preventive task to avoid equipment failure or an urgent repair request for unexpected issues.
Investing in automated tracking software allows businesses to streamline operations, reduce paperwork, and improve cost efficiency. By leveraging standardized templates and forms, companies can enhance consistency while maintaining flexibility.
Ultimately, a well-managed task workflow supports increased sales, reduces inefficiencies, and ensures every assignment is completed accurately and with accountability.
The Purpose of a Work Order and When to Use One
A work order system helps businesses schedule, assign, and track tasks efficiently, ensuring smooth workflow execution. Whether used in manufacturing, construction, or field services, it provides clear documentation of job details, required resources, and deadlines to maintain accountability and efficiency.
Different task categories in maintenance and repair operations serve specific purposes, such as preventive maintenance for scheduled inspections and urgent repairs for unexpected issues. A well-documented service request ensures external contractors have the necessary details to complete tasks effectively while maintaining cost control and quality standards.
From a financial perspective, work order software helps businesses track labor, materials, and operational costs to stay within budget and improve resource allocation. Whether in print or digital format, a work order form ensures transparency by recording job specifics, including assigned personnel, location, and expected completion dates.
Types of Work Orders
Understanding different task categories is essential for maintaining efficiency and handling assignments appropriately. Each job request serves a unique purpose, whether for routine maintenance, urgent repairs, or long-term improvements.
- Corrective maintenance: Issued when an inspection identifies issues requiring repairs or part replacements. Unlike urgent repairs, this type allows for scheduled fixes before complete equipment failure.
- Electrical maintenance: Covers the repair, servicing, or installation of electrical systems such as wiring, power supplies, and lighting. This ensures safety, compliance, and uninterrupted operation within a facility.
- Emergency repairs: Used when critical equipment fails, posing risks to safety or productivity. It requires immediate attention and is classified as the highest priority to minimize downtime.
- General maintenance: A broad request covering non-urgent tasks such as painting, pest control, or facility upkeep. It ensures that minor but necessary work is scheduled without disrupting operations.
- Inspections: Issued for asset evaluations to detect risks, anomalies, or performance issues proactively. Commonly used in preventive care to maintain equipment reliability and regulatory compliance.
- Preventive maintenance: Scheduled servicing to extend the lifespan of assets and reduce costly repairs. Identifying potential failures early helps businesses maintain efficiency and avoid unexpected downtime.
- Safety compliance: Created to address hazards such as chemical spills or structural damage. These tasks ensure workplace safety regulations are met while minimizing risks.
- Special projects: Used for facility upgrades, equipment modernization, or process improvements. These initiatives help businesses increase productivity, adopt new technologies, and enhance efficiency.
By leveraging task management software, businesses can streamline these processes, ensuring assignments are documented, tracked, and completed effectively. A well-structured workflow template provides clarity and organization, improving maintenance management.
Benefits of Using Work Order Software
Implementing work order software enhances efficiency, accuracy, and productivity in managing maintenance tasks. Whether handling preventive maintenance or emergency work orders, businesses benefit from automation, improved data tracking, and streamlined workflows.
Below are the key advantages of using a work order system.
1. Reduced operational costs
A work order system eliminates the need for manual paperwork and spreadsheets, significantly cutting administrative expenses. Businesses save time and minimize planning efforts by automating work order creation, tracking, and service requests.
Additionally, storing digital data reduces costs associated with document storage and retrieval. With optimized resource allocation, companies can focus on proactive work order maintenance instead of reactive repairs.
2. Improved data access and real-time updates
With cloud-based work order software, teams can access maintenance data anytime, anywhere. Managers can track work order descriptions, assigned personnel, and task status in real-time, ensuring better coordination.
Mobile integration allows maintenance teams to receive instant updates, edit tasks, and submit reports. This accessibility enhances efficiency and keeps everyone informed about ongoing service work orders.
3. Enhanced data visibility and reporting
A well-structured work order template includes detailed job tracking, allowing businesses to analyze trends and forecast future maintenance needs. Customizable reports help identify performance gaps, optimize work order types, and improve asset management.
By leveraging historical data and case examples, companies can develop more effective preventive maintenance strategies. This data-driven approach enhances operational reliability and extends equipment lifespan.
By integrating work order software, organizations gain better control over maintenance tasks, reducing downtime and improving workflow efficiency. Whether managing routine maintenance, urgent repairs, or service requests, a digital work order sample ensures smooth operations and cost-effective decision-making.
Lifecycle of a Work Order
A work order follows a structured lifecycle to ensure tasks are completed efficiently and documented properly. Each phase in the work order system plays a critical role in organizing, assigning, and analyzing maintenance work.
1. Task identification
The first step in the work order lifecycle is recognizing the need for maintenance or repairs. Whether it’s a preventive maintenance work order scheduled in advance or an emergency work order requiring urgent action, identifying the task ensures the right solution is implemented.
2. Work request submission
Once an issue is identified, a work order form with relevant details such as task description, urgency level, and required resources is submitted. This step helps maintenance teams prioritize work, whether a service work order for external contractors or an internal repair request.
3. Work request evaluation
The maintenance team reviews the work order request to assess feasibility, required materials, and personnel availability. If approved, the request is converted into a work order sample, ensuring clarity on task execution and resource allocation.
4. Work order creation
The maintenance supervisor finalizes the work order description at this stage, assigning necessary staff and tools. A clear work order definition includes deadlines, estimated costs, and a checklist of tasks to be completed.
5. Work order distribution and completion
The assigned technician receives the work order example and follows the outlined tasks to ensure completion within the given timeframe. If a company uses work order software, the system automatically updates progress, allowing real-time tracking and accountability.
6. Work order documentation and closure
Once the task is completed, technicians document time spent, materials used, and any additional observations. A well-documented work order maintenance record helps track efficiency, cost, and potential areas for improvement.
7. Work order review and analysis
The work order system is reviewed post-completion to identify trends, bottlenecks, or missed tasks. This ongoing evaluation ensures better work order management, improving efficiency and reducing downtime for future maintenance needs.
By following a structured work order lifecycle, businesses can streamline operations, reduce costs, and improve task accountability. Utilizing work order software further enhances efficiency by automating assignments, tracking progress, and generating insightful reports.
What Should a Work Order Include?
A work order is a structured document that ensures maintenance, repairs, or service requests are properly tracked and executed. To maximize efficiency, a work order system must include essential details that provide clarity, accountability, and proper documentation.
Below are the key components that every work order example should include:
1. Contact and internal information
Every task request form should start with basic details like the company name, address, and contact information to ensure clear communication. A unique tracking number is assigned to monitor progress and retrieve records efficiently within the management system.
Additionally, the document should specify issue dates, start and completion dates, and priority levels to streamline scheduling. If applicable, it should also identify the requester, department, or assigned technician handling the work order maintenance.
2. Job description
A well-defined work order description outlines the scope of work, including the tasks to be completed, estimated labor hours, and assigned personnel. The document should specify whether the request is a routine maintenance task, a preventive maintenance work order, or an emergency work order requiring immediate action.
Billing details should also be included, ensuring transparency on service costs, labor rates, and additional fees. If external services or parts are involved, the service work order may sometimes have a designated shipping address.
3. Required materials
The document should include a list of materials, tools, or spare parts required to complete the job efficiently. This section outlines item descriptions, quantity, unit price, and total cost, ensuring accurate budgeting and inventory tracking.
Any applicable taxes, additional charges, or special service costs should be documented to provide a comprehensive cost overview. Lastly, manufacturing software may include a section for extra notes, ensuring all relevant details are captured before final approval and execution.
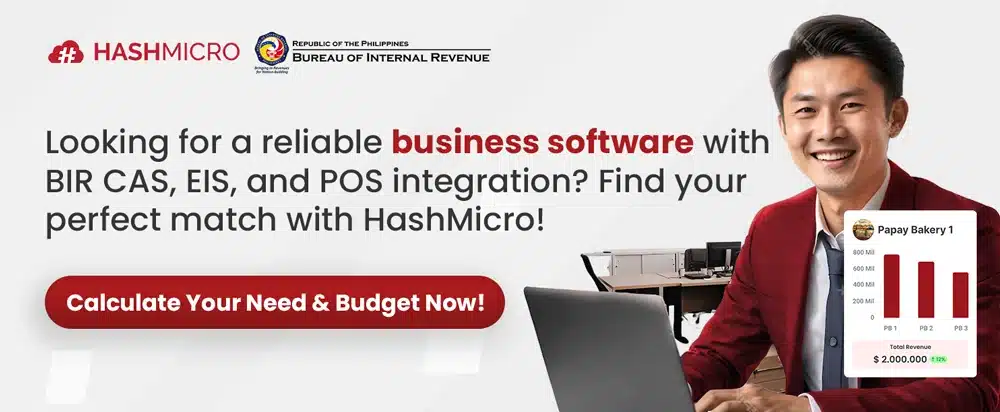
By incorporating these essential elements, a work order system helps businesses improve efficiency, reduce errors, and maintain better control over maintenance and service operations. Implementing structured work order software further streamlines the process, ensuring tasks are well-managed and completed on time.
The Work Order Process
A task management system follows a structured process to ensure maintenance activities are efficiently handled and completed. Whether it’s preventive upkeep or an urgent repair request, each step ensures proper tracking, resource allocation, and execution.
Below are the three essential steps in the workflow process:
1. Create a work request
A work order begins with a work request submitted when a maintenance issue is identified. This request can come from various sources, such as customer service inquiries, safety inspections, preventive maintenance audits, or internal department needs.
The work order form captures key details, including task descriptions, priority levels, and requested completion dates. Businesses can ensure that maintenance needs are addressed promptly and organized by adequately documenting requests.
2. Evaluate the work request
Once submitted, the maintenance manager reviews the work order request or supervisor to determine feasibility. This evaluation includes assessing whether the task is routine maintenance, a service work order for external contractors, or an emergency requiring immediate action.
The manager also considers resource availability, ensuring that materials, equipment, and personnel are allocated effectively. Only after approval is the work request converted into a work order sample for execution.
3. Create a work order
After final approval, the task details are finalized, outlining the job scope, assigned personnel, deadlines, and material requirements. A well-documented task order ensures that all involved parties have clear instructions and expectations for execution.
Businesses can automate this process using maintenance software, enabling real-time tracking and minimizing errors. A structured task management system enhances efficiency, communication, and accountability across departments.
By following these steps, businesses can streamline their work order maintenance process, ensuring tasks are completed efficiently, and resources are used effectively. Implementing a work order system helps organizations stay proactive, reducing downtime and improving overall operational performance.
How Does CMMS Work Order Software Work?
A CMMS system automates task management, enabling businesses to efficiently create, track, and complete maintenance activities. This software helps organizations process requests, assign responsibilities, and manage resources while reducing downtime and improving workflow.
A web-based platform allows companies to handle various maintenance tasks, including preventive, emergency, and service-related activities. Additionally, it offers essential features like inventory tracking, warranty management, and compliance monitoring, helping businesses optimize asset performance and ensure regulatory adherence.
Furthermore, a CMMS solution includes downtime tracking and data analysis tools, supporting informed maintenance decisions. With an automated request system and structured documentation, businesses can minimize errors, improve task execution, and enhance efficiency across operations.
Simplify Work Order Management with HashMicro’s Manufacturing Software
HashMicro offers a powerful manufacturing software solution to help businesses streamline work order management, improve production efficiency, and optimize resource utilization. With automated work order creation, material tracking, and real-time reporting, manufacturers can ensure seamless operations while minimising errors.
Experience the benefits of automated work order processing with HashMicro’s manufacturing software. This system simplifies production planning, work order execution, and inventory management, ensuring accurate data and improved operational performance.
Why Choose HashMicro’s Manufacturing Software? HashMicro’s solution automates maintenance, machine scheduling, and raw material management, reducing manual workload. With seamless integration across production, inventory, and financial tracking, manufacturers can minimize production delays and enhance cost control for a more streamlined workflow.
This system helps businesses manage work orders efficiently, ensuring smooth operations while reducing waste and production bottlenecks. Below are some of the key features of HashMicro’s manufacturing software:
- Automated Work Order Management: The system automates work order creation, tracking, and scheduling, ensuring efficient task execution. It provides real-time updates on job progress and resource allocation, reducing delays and improving workflow.
- Multi-Level Bill of Materials (BoM): The software compiles detailed cost data for components, spare parts, and raw materials in a structured format. This allows businesses to plan production budgets and optimize material usage accurately.
- Material Requirements Planning (MRP): The system integrates production planning, inventory control, and work order execution in a single platform. It ensures materials are available when needed, reducing stock shortages and preventing overproduction.
- Real-Time Stock Monitoring: The software tracks inventory in real time, ensuring FIFO (First-In-First-Out) stock management is properly implemented. This helps prevent dead stock and optimizes warehouse space for better efficiency.
- Production Cost Tracking with Accounting Integration: The system records material and operational expenses in real-time. This provides accurate financial insights, ensuring businesses can control production costs effectively.
- Human Resource Management: The software automates payroll, insurance, and leave management, reducing administrative workload. It ensures accurate employee compensation tracking and enhances workforce productivity.
- IoT Integration for Production Monitoring: With the Internet of Things (IoT) capabilities, the system monitors machine performance and production capacity in real-time. This allows businesses to identify inefficiencies early and optimize resource utilization.
- Comprehensive Reporting & Analytics: The system generates real-time production reports, comparing planned vs. actual performance. This enables data-driven decision-making, improving productivity and strategic planning.
With HashMicro’s manufacturing software, businesses in Malaysia can simplify work order management, enhance productivity, and achieve long-term growth. Optimize your production workflow today with an integrated, automated system designed for maximum efficiency and precision.
Conclusion
A work order is a structured document used to manage and track specific tasks such as spare part inspections and production scheduling in manufacturing. It plays a crucial role in organizing workflows, planning resources, and providing detailed cost information, ensuring every task is executed efficiently and accurately.
To enhance work order efficiency, manufacturers can leverage Hash Manufacturing Automation Software, which streamlines production planning, work order creation, and real-time tracking. This system automates task assignments, cost calculations, and material management, allowing businesses to operate more effectively with improved accuracy and speed.
Optimize your work order management with Hash Manufacturing Automation Software and experience automated, precise, and hassle-free production processes. Schedule a free demo today to see how our solution can transform your manufacturing operations.
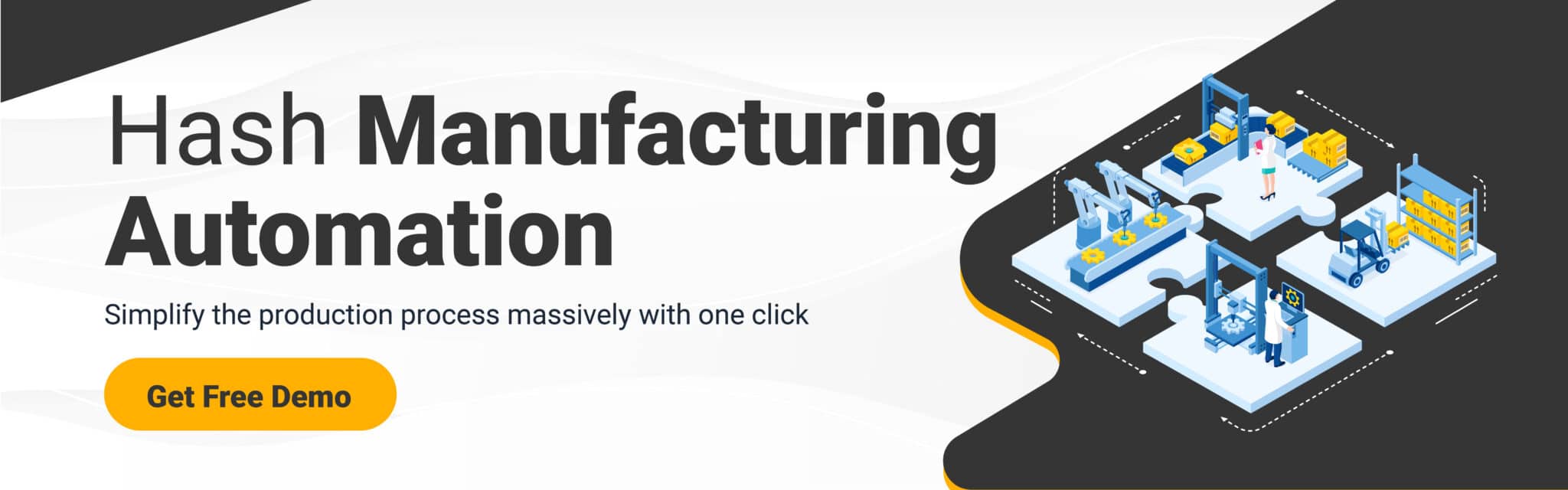